PFAS Replacement in Polish Systems
Silicone Wetting Agents vs. PFAS

VCT hospital floor. Image courtesy of Indspyre.
Perfluoroalkyl substances (PFAS) are found in multiple industries despite their negative human health effects being known for decades. Due to their unique performance properties, it is challenging to replace PFAS or formulate them out of products. In coating systems, they aid in chemical resistance as well as dynamic surface wetting and flow. They work at very low levels with high efficiency, thus minimizing the possibility of defects such as haziness or migration to the coating.
In 2021, the state of Maine initiated efforts to ban products containing intentionally added PFAS, and required companies to list the type and quantity in their formulated products. Other states followed suit (Figure 1), and a Minnesota law has critically shortened the timeframe companies have to develop replacements. This law bans the sale of many consumer materials containing intentionally added PFAS starting Jan. 1, 2025. While there was time to act in 2021, many industries have failed to remove PFAS from their formulations.
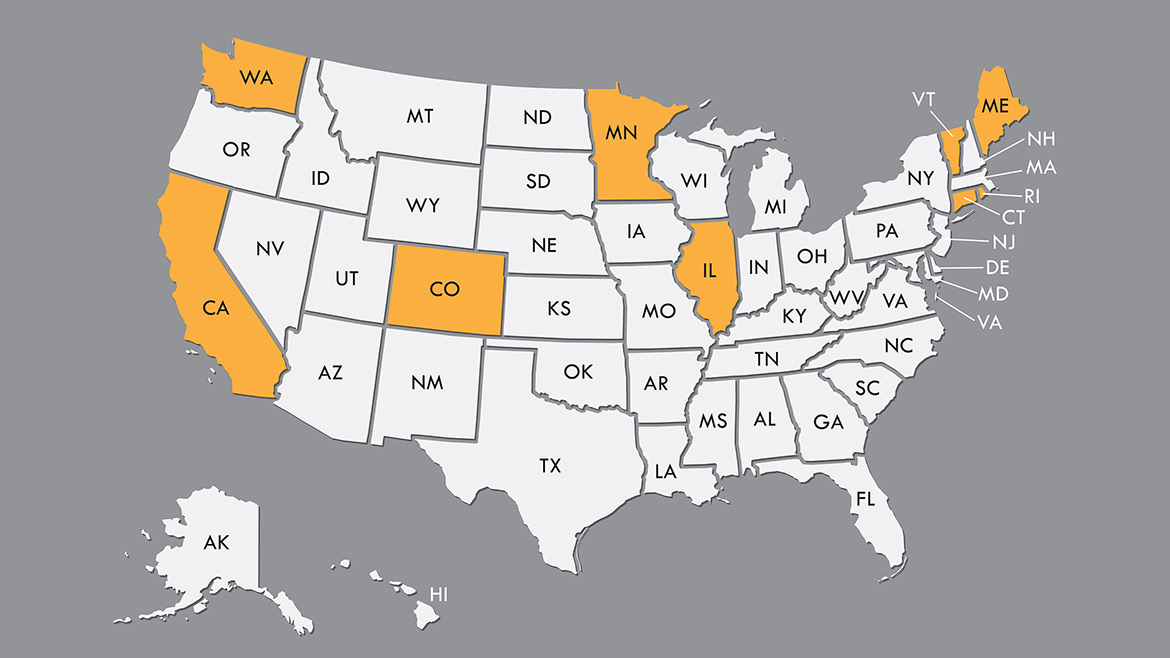
For example, the flooring industry has rigorous demands on performance and maintenance. Coatings must work on various substrates, which poses an added challenge. Wood flooring, such as in gymnasiums, has different demands from resilient flooring, such as vinyl composite tiles (VCTs) used in hospitals. Maintenance of these various flooring types ranges greatly as well. Gymnasium floors must be coated multiple times with sealers, game lines and graphics while delivering scuff, abrasion and chemical-resistant properties. Resilient flooring is mopped onto the VCT and must flow and level well in a short period, with up to 10 coats of acrylic polish applied to build a very high gloss. Both systems must maintain greater than 90-degree gloss and minimal haziness. The historical use of PFAS in floor applications has provided an easy route to achieving the performance and maintenance required.
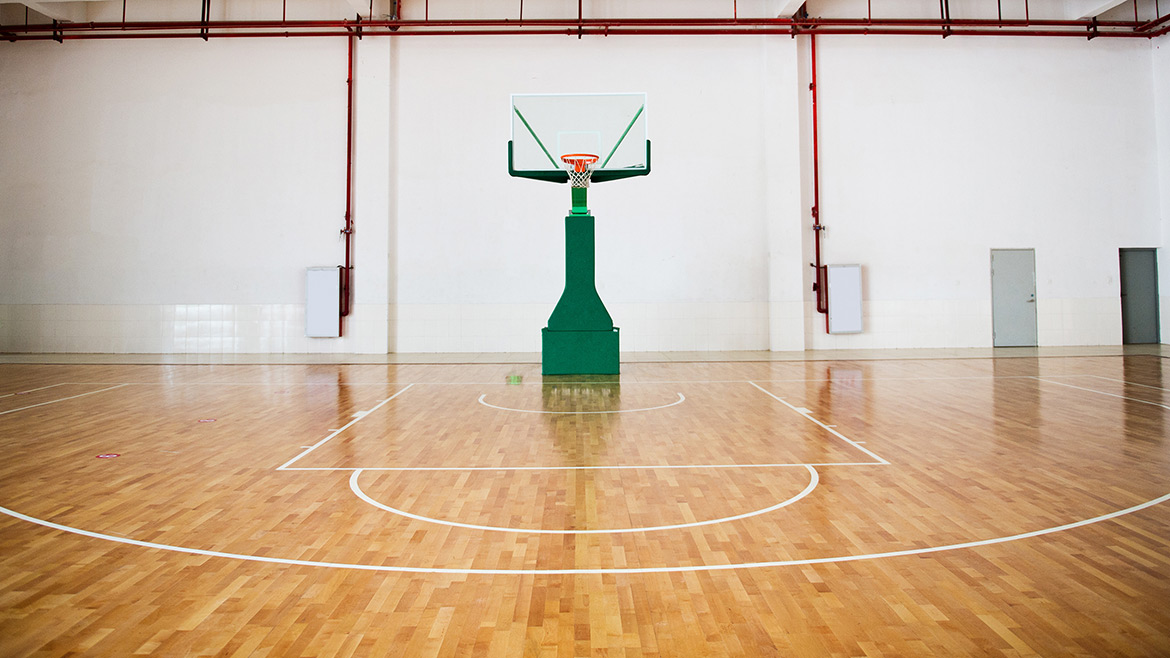
When developing polish systems, application on a single VCT panel must be tested and surface tension checked before moving on to larger surfaces, such as an 8-by-8-foot test floor. PFAS chemistry acts as a surface wetter, emulsifier and leveling agent all in one product. Many of the silicone or hydrocarbon surfactants have a slightly higher surface tension and require a higher loading level in the formulation to achieve the same performance attributes. We can measure these by application as well as contact angle and dynamic surface wetting (Figure 2).
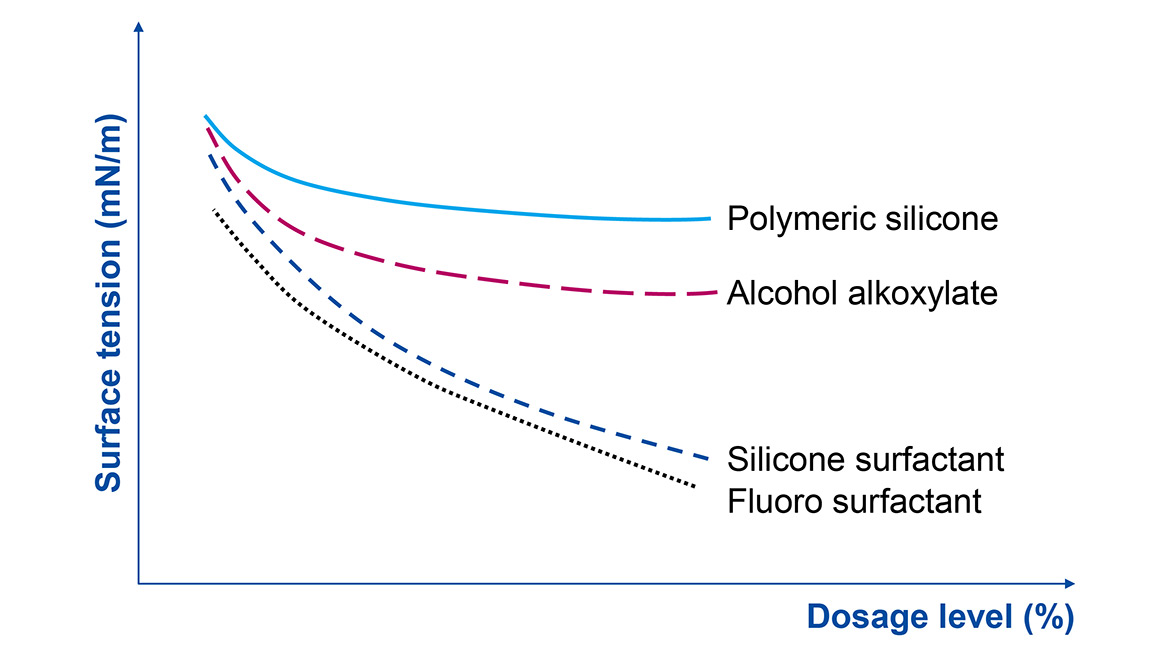
When formulating, there are other components that contribute to surface wetting and leveling, such as glycol ethers, waxes, plasticizers, and of course, resin selection. Table 1 shows a typical polish formulation.
When formulating the polish, it is typically tested on 12-by-12-inch black Armstrong tiles with 2 mL of polish per application and a gauze pad (Figure 3). To test the effectiveness of the wetting and leveling, an “X” is intentionally added in coats 5-8 on the tiles. If these flow out and the “X” becomes invisible to the naked eye, the polish can proceed to larger-scale evaluation.
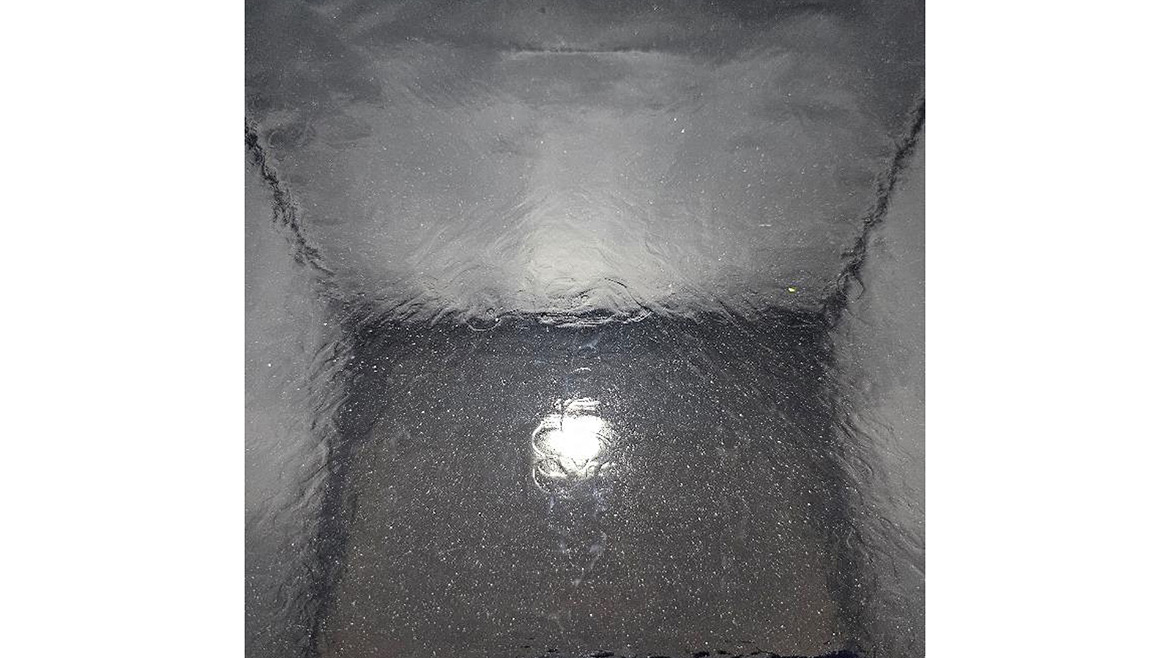
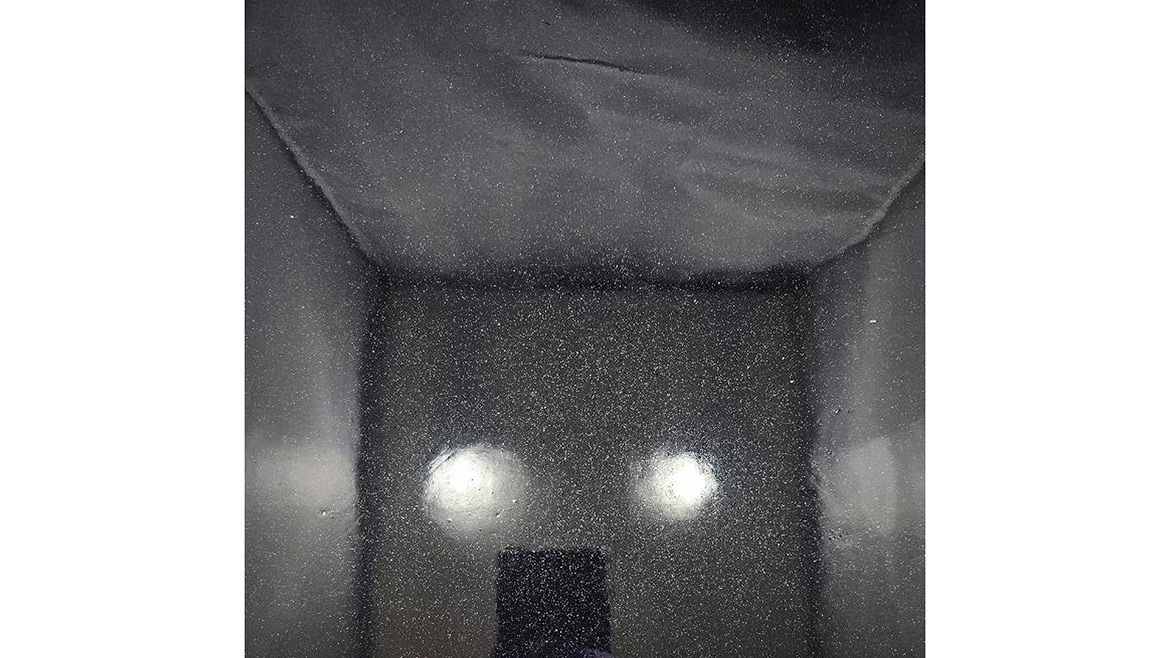
To further assist our laboratory efforts in determining proper wetting and surface tension, we use a goniometer (Figure 4). This allows us to measure the contact angle of the liquid polishes on substrates and thereby ascertain how well they wet out. We evaluate both the polish wetting out the VCT and the polish wetting itself out on a tile with several coats already applied.
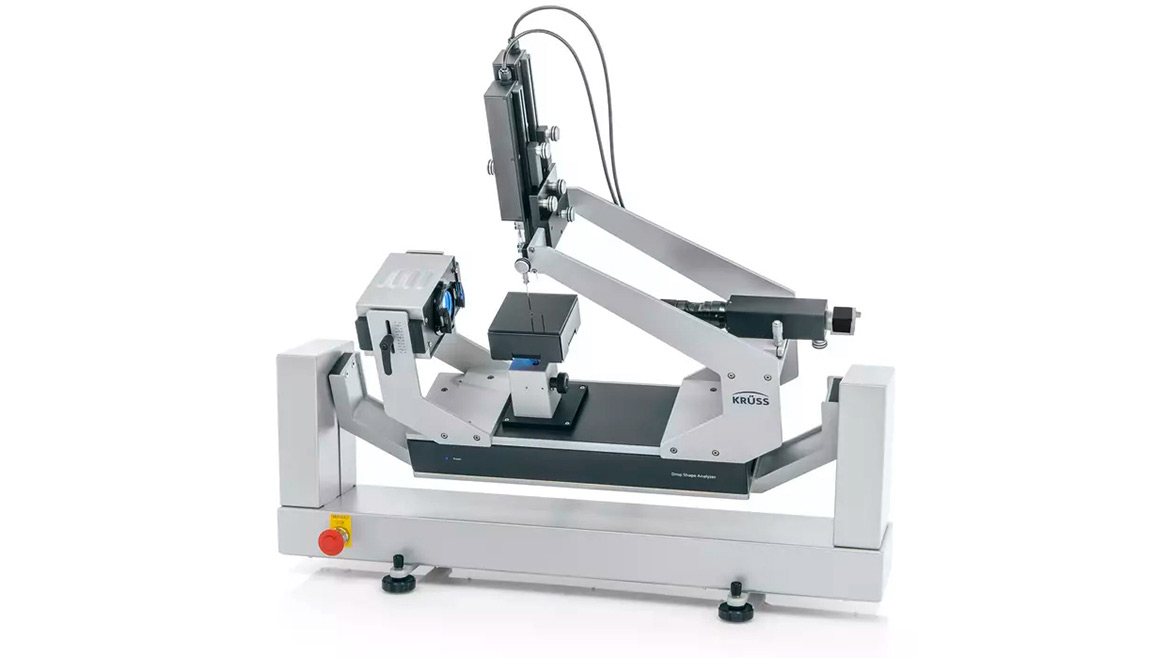
We began the process with a standard Dow starting-point formulation and substituted the fluorosurfactant with several silicone-based wetting agents from BYK. Over the course of our work, we learned that the silicone super wetters were not direct drop-in replacements and had to increase their concentration. To aid in emulsifying some of the hydrophobic components, we incorporated lauryl alcohol ethoxylate surfactants with 12 and 23 moles of ethoxylation. Test results have determined we can lower the surface tension with the silicone wetters, but not quite as low as the fluorinated wetters. In most cases, we have seen the fluorinated surfactants averaging anywhere from 4-6 mN/m lower than the silicone wetting counterparts (Figure 5).
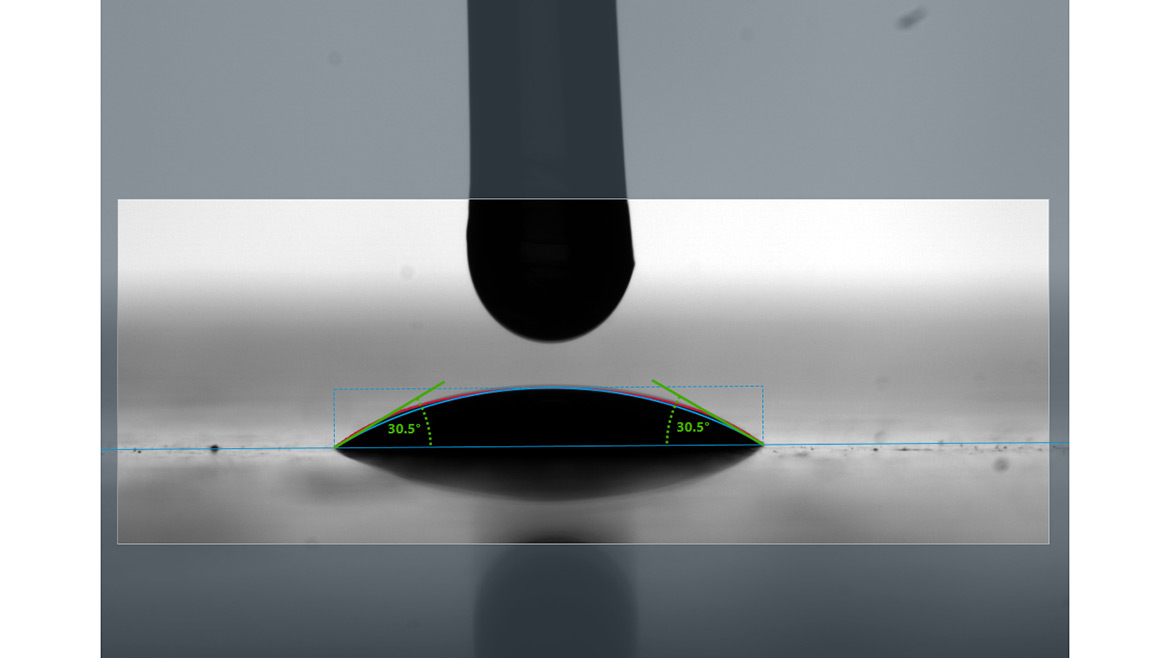
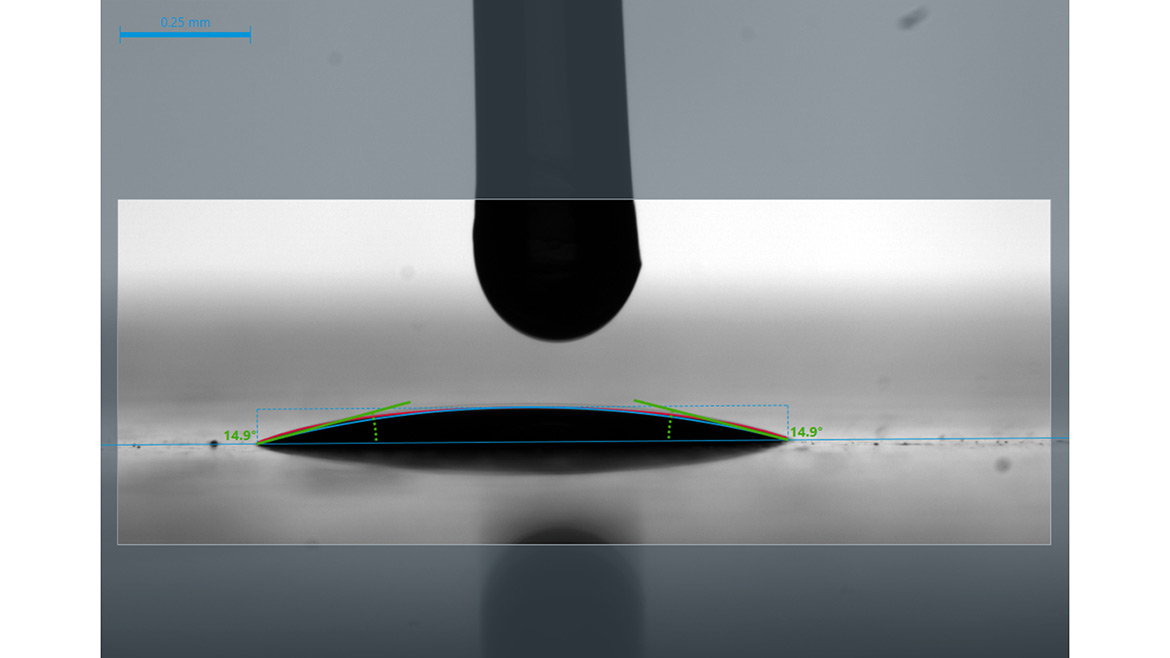
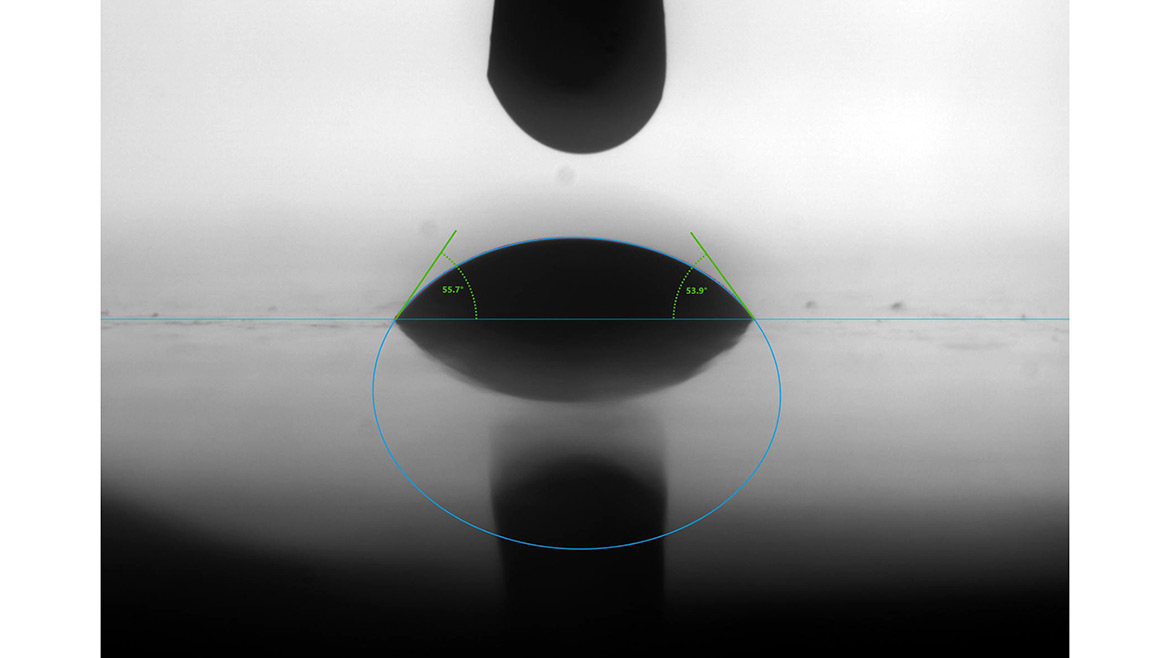
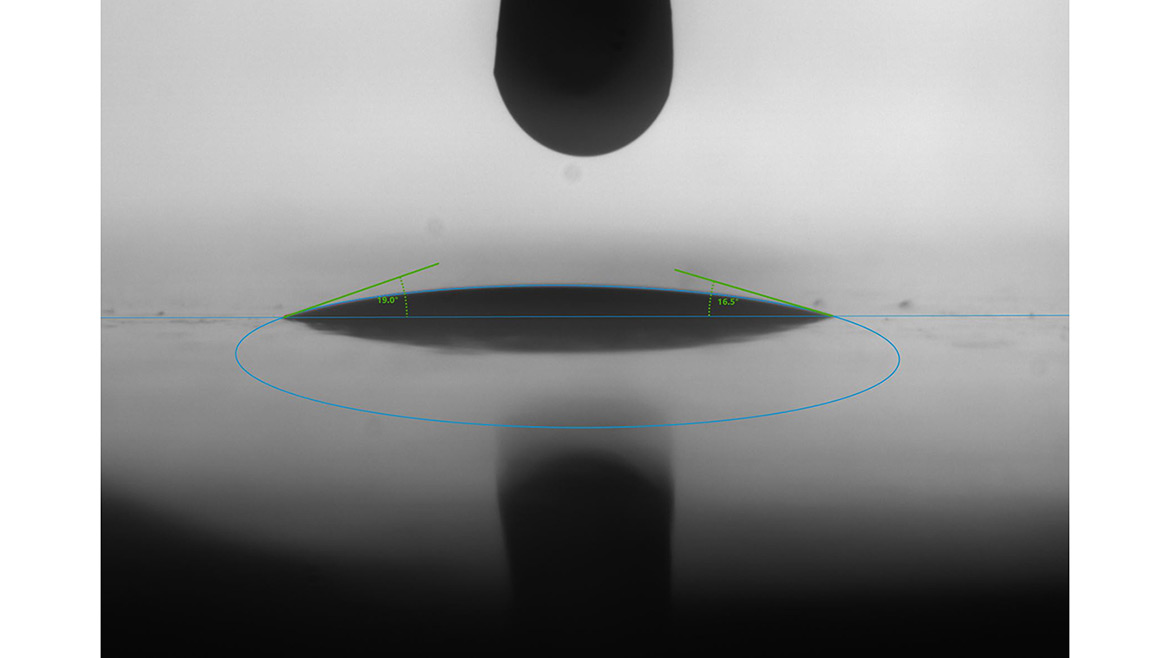
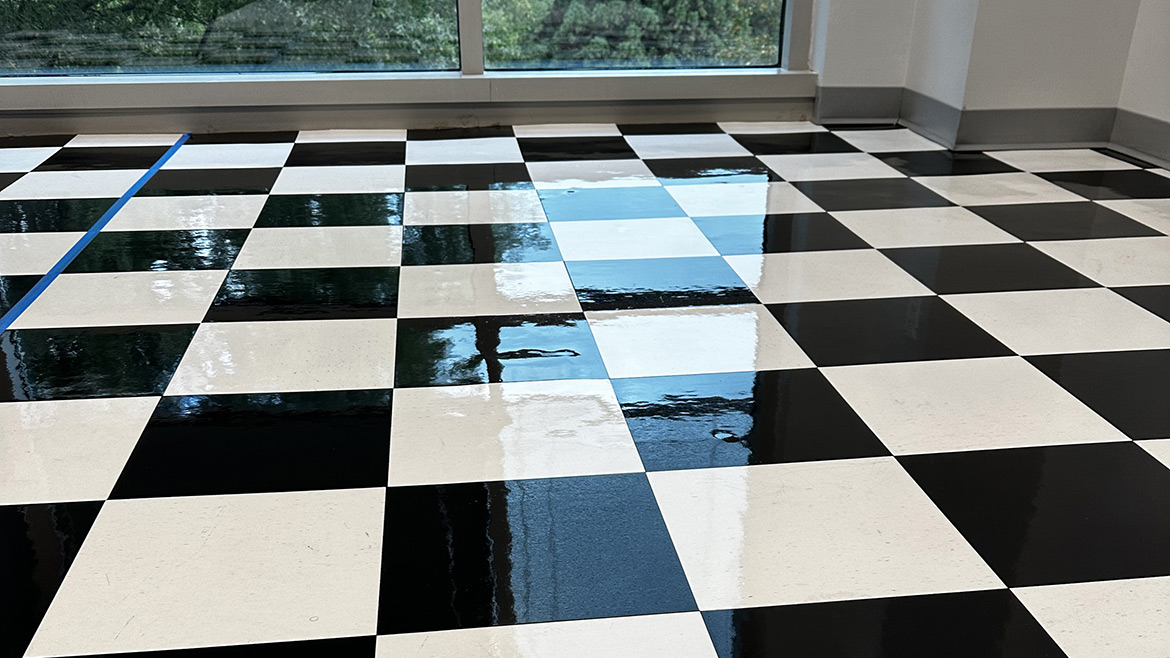
The last step before evaluating a larger floor application is to ensure the gloss and haze are acceptable. To test this, we use a Leneta card and black Carrara glass. We measure the gloss at 60 and 20 degrees and the haze on the black Carrara glass. We use a Rhopoint IQ to determine haze, gloss, and DOI of the polish on the Carrara glass.
When we have a polish system suitable for scaling to a larger application, we apply it on our test floor for additional evaluation. We use a string mop and microfiber mop, and apply the polish with the silicone super wetter versus the fluorinated wetter in 64-square-foot sections. We apply at 1,500-2,000 square feet per gallon in each application step and look for mop lines or poor flow at each layer. The typical application is four coats on the first day and four additional coats the second day.
After evaluating a formula application on an actual floor and confirming that it flows and levels properly, we verify the static coefficient of friction is within the desired range (Figure 6). We clean the floor with a neutral cleaner to ensure there are no unusual changes in gloss, haze or slipping.
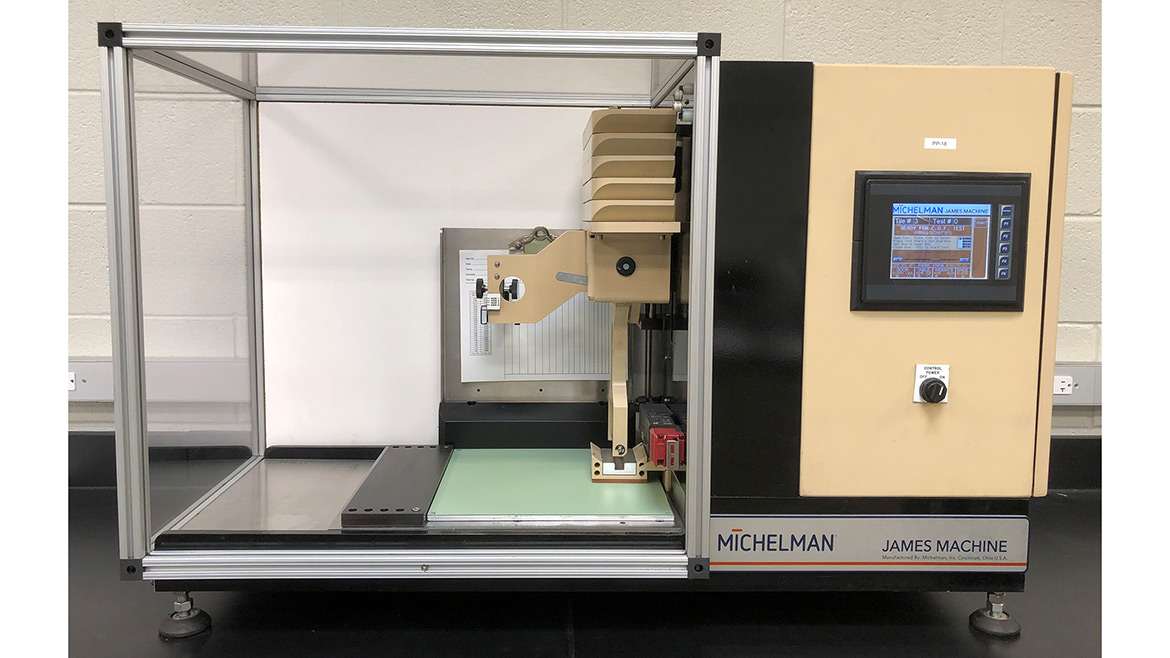
We work with one of our partners, Dow, to conduct a wear test on the prototype polish. The Accelerated Wear Tester (AWT) simulates dirt pickup, scuffing, burnishing and cleaning cycles. They conduct these tests using a rating system, evaluating the results relative to the control polish with PFAS chemistry. Through rigorous testing, IndSpyre Solutions can assist customers in developing reformulated products that retain their robust nature and performance properties.
When we have positive results from the Dow AWT evaluation, we work with our customers to communicate recommended levels of surfactants for their applications. We assist as needed to test further and scale up these products.
Conclusion
Fluorinated chemistry is difficult to replace with a safer alternative at the same percentage in formulations. This requires the formulator to work with several types of silicone surfactants and sometimes utilize other surfactants such as alcohol ethoxylates. While we have illustrated one potential pathway in formulation, there are several routes to formulate these materials out of polish.
The change to regulations is imminent, with Minnesota enforcing its PFAS statute in 2025. With the removal of perfluorinated surfactants from polish applications alone, we estimate the removal of over 40,000 pounds of these materials from the market per year.
Follow this link to view our line card of product offerings in your area. Please send all new purchase orders to indspyre.orders@indspyre.com.
Looking for a reprint of this article?
From high-res PDFs to custom plaques, order your copy today!