Redox Chemistries for Use in Aqueous-Based Polymer Dispersions, Part 3

Volodymyr Konko, Creatas Video+ / Getty Images Plus, via Getty Images
Did you know there is valuable information available about the use of redox systems for effective reduction of residual monomers/VOCs after the main emulsion polymerization? EPCEd is partnering with Brüggemann for this third in a series of Did You Know columns to highlight best practices for redox application in emulsion polymers, including reaction kinetic data and guidelines for best practices. This issue focuses on preferred redox methods and optimization.
Previous articles in this series highlighted the fundamentals of redox systems typically used for the emulsion polymer chase, discussing dosage, rate of addition, rate of reduction of residual monomers, and initial screening tests for selection of the best reducing agent/oxidizer for the polymer recipe. Now that we have selected which redox pair to use, let’s optimize it to minimize residual monomers, dosage, and cycle time for the chase.
Theoretically, every radical generated by a reducing agent/oxidizer combination is capable of reacting with C=C bonds in residual monomers, converting them to dimers, oligomers, or short polymer chains. This eliminates VOCs and odor. However, the radical must find a C=C bond before it finds another radical, or other species to react with such as transition metals. Getting radicals to the C=C bonds to convert monomers instead of recombination with other radicals/termination is the challenge.
We know that continuous simultaneous dosing of the redox pair over time is more effective than feeding all of the components at once (“dumping”). Dumping creates a high radical flux in a small space, increasing the potential for recombination or termination rather than reaction with residual monomer. Below is an example showing residual monomer level (via GC) decline over time during a redox chase with continuous feed vs. a one-shot process. Redox dosages are weight percentages of each component on a solids basis vs. total latex weight.

From a previous study, we learned that rate of redox addition is related to the propensity of radicals to find residual monomers before they find another radical.
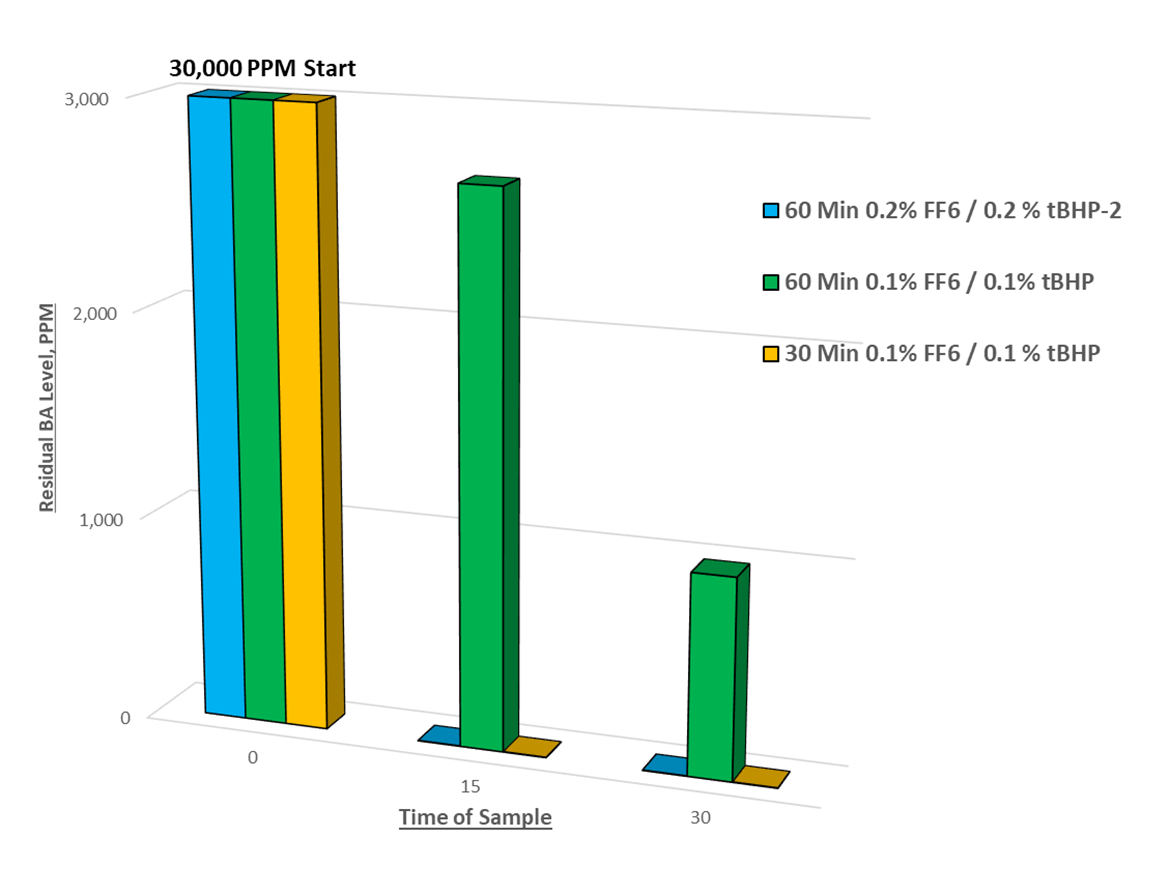
In the above example, we see three kinetic data sets of residual BA monomer levels during the chase:
- Blue: 0.2% FF6/tBHP total dosage added over 60 minutes.
- Green: 0.1% FF6/tBHP total dosage added over 60 minutes.
- Yellow: 0.1% FF6/tBHP total dosage added over 30 minutes.
Note the blue and yellow columns show undetectable BA levels after 15 minutes, which are expected since it is the same rate of redox dosage: 0.2% added over 60 minutes = 0.1% added over 30 minutes = 0.05% added over 15 minutes. This example could be further optimized to find the minimum total redox dosage and time period of addition to obtain target residual BA level.
With further optimization, we might find that BA levels could be reduced to <500 ppm in 10 minutes with 0.05% or lower total redox dosage. Adding 0.1% over 60 minutes wasted time and redox ingredients with substantially worse results; over 1,000 ppm of free monomer after the chase.
Some key takeaways for optimizing redox in an emulsion polymer chase:
- Run simple screening tests to find the best combination of reducing agent and oxidizer compounds.
- Use continuous, simultaneous dilute feed streams of reducing agent and oxidizer.
- Faster rate of redox addition will minimize redox dosage and time to reach the residual monomer target.
- One-shot “dumping” of redox ingredients all at once increases potential for radical recombination vs. reacting with C=C bonds.
As always, we invite your questions and comments by going to info@epced.com. Additionally, we invite you to go to Brüggemann’s Institute of Redox Chemistry – a collection of tutorials on redox chemistry for emulsion polymerization, providing greater detail of redox combinations and process optimization techniques. For more information, contact Brüggemann, BCUS_Sales@brueggemann.com.
The “Did You Know….?” series is a bi-monthly note from Emulsion Polymers Consulting and Education (EPCEd) that is intended to present simple questions about topics that are important to those working in the emulsion polymers area. Short and concise answers to those questions are presented to educate readers and to elicit comments and further discussion. Some readers will already know the answers and be familiar with the topic, while others, especially those newer to the field, will benefit from the answers and discussion. Experienced practitioners may also find new insights in the discussion. Paint & Coatings Industry magazine has partnered with EPCEd to share the “Did You Know” notes with our readers throughout the year.
Looking for a reprint of this article?
From high-res PDFs to custom plaques, order your copy today!