Redox Chemistries for Use in Aqueous-Based Polymer Dispersions, Part II

Volodymyr Konko, Creatas Video+ / Getty Images Plus, via Getty Images
Did you know there is valuable information available about the use of redox systems for effective reduction of residual monomers/VOCs after emulsion main polymerization? EPCEd is partnering with Brüggemann for this second in a series of Did You Know columns to highlight best practices for redox application in emulsion polymers, including reaction kinetic data and guidelines for best practices. This article focuses on two of those topics.
How Much Time is Necessary to Achieve Target Residual Monomer/VOC Levels?
This depends on residual monomer level at the start of redox chase, type of redox components used, amount of redox added, rate of redox addition, temperature, pH, and type of monomer that needs to be removed. Despite the great importance of this question, there is very little available data in open scientific literature.
Brüggemann has explored the fundamental aspects of factors to optimize redox chase for decades. One example is the kinetic data shown in Figure 1 using the redox couple tBHP (tert-butyl hydroperoxide) and Bruggolite® FF6M. When the redox feed was started at 60 °C, the latex residual monomer level was ~10,000 ppm, common for starve-fed acrylic emulsion polymerizations using persulfate initiator for the main polymerization.

The traditional “hold period” offers some, but limited, reduction in monomer levels. It is vastly insufficient for current requirements of residual monomer/VOC levels in production latex recipes, often <100 ppm. After the main polymerization, periodic samples analyzed via GC during redox feed illustrate the decline of each monomer over time. This shows little monomer reduction during the “hold period” compared to dramatic reductions for each of the three monomers during the redox chase period.
There is a diffusive aspect of how radicals move through the aqueous phase of the latex and their propensity to find and react with residual monomer or another radical. There is also a chemical aspect where radicals will be donated to the most likely acceptor. For example, to avoid radical recombination or termination, a system should be optimized in order for radicals to convert residual monomers effectively. We will explore redox optimization further in our third edition of this series.
How Might One Choose the Appropriate Redox Pair for the Monomers Being Used?
This is dependent on many factors and must be evaluated for the polymer recipe. We suggest a simple screening test with different redox couples, starting at 0.2% (by weight of latex) dosage of each redox component. If no differences are observed, halve that amount and test again. In Figure 2, redox chase in an acrylic system showed little performance differences among the various redox couples in final residual monomer levels at higher dosages (e.g. 0.2%); dropping this down to 0.05% reveals which combination enables best performance.
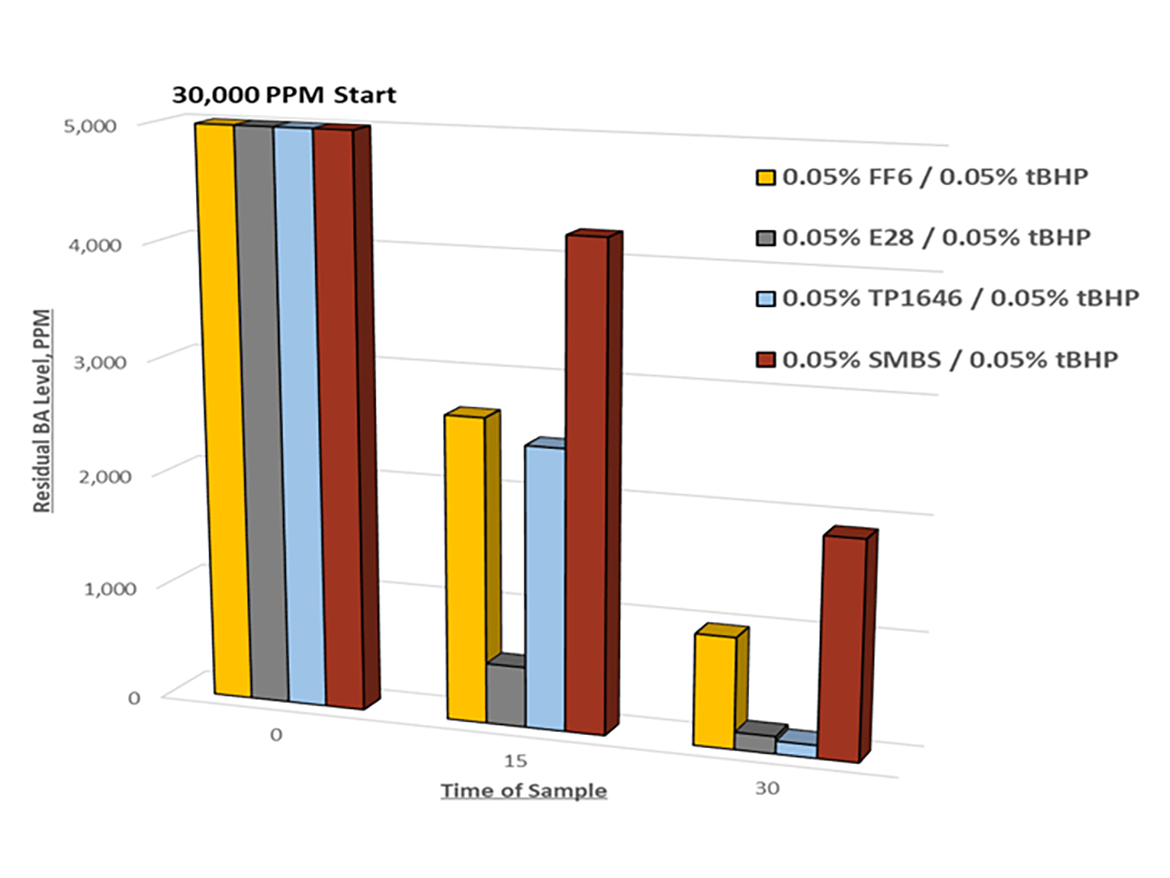
Selection of the redox pair should be the first step in optimization to minimize residual monomer level, dosage, and time. From there, other factors such as temperature, rate of addition, and pH may need to be considered.
These are complicated questions and must be tested. Process factors required to make the desired polymer in the main polymerization may influence selection of redox components for the chase. In general, lower pH and higher temperature accelerate the oxidation of a reducing agent, increasing radical flux. More-stable reducing agents will typically perform best under those harsher conditions. Conversely, a less-stable (more-reactive) reducing agent will give the best results at lower temperatures and higher pH.
As always, we invite your questions and comments by going to info@epced.com. Additionally, we invite you to go to Brüggemann’s Institute of Redox Chemistry – a collection of tutorials on redox chemistry for emulsion polymerization, providing greater detail of redox combinations and process optimization techniques. For more information, contact Brüggemann, BCUS_Sales@brueggemann.com.
The “Did You Know….?” series is a bi-monthly note from Emulsion Polymers Consulting and Education (EPCEd) that is intended to present simple questions about topics that are important to those working in the emulsion polymers area. Short and concise answers to those questions are presented to educate readers and to elicit comments and further discussion. Some readers will already know the answers and be familiar with the topic, while others, especially those newer to the field, will benefit from the answers and discussion. Experienced practitioners may also find new insights in the discussion. Paint & Coatings Industry magazine has partnered with EPCEd to share the “Did You Know” notes with our readers throughout the year.
Looking for a reprint of this article?
From high-res PDFs to custom plaques, order your copy today!