Corrosion Resistance for Zinc Plating
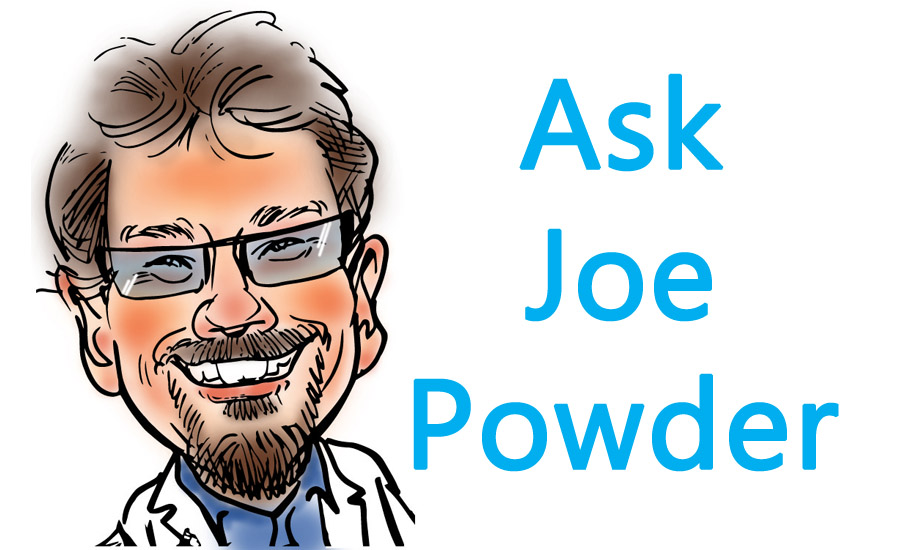
Hi Joe,
I came across your blog whilst looking for solutions to an ongoing problem I’ve had. I design and manufacture designer gates cut from 3-mm mild steel. When I get the raw steel back from laser cutting it is still covered with mill scale. I install all of my gates in a coastal region, and because my gates are bespoke boutique pieces I’d like them to last as long as possible while exposed to the elements.
I’ve been zinc plating and powder coating them with various service providers, but this is hit and miss. It’s incredibly frustrating to hear the powder coater call and say the powder has come out of the oven full of pinholes and usually they say they have no idea what happened. Worse still the zinc plater will also claim ignorance. I’ve had good results, but it’s touch and go and when things go wrong it’s very expensive to fix and I’m usually left carrying the cost. I’ve tried everything from baking before coating to cleaning the gates before with degreaser and etching solutions, leaving them for a few days to off gas. I also have some channels in the gate and where the radius is tight and the zinc doesn’t deposit too well, and often I prime it, which is time consuming and I’m never sure whether this is good to powder coat over.
I would love to be able to do the coating etc. in-house with the most affordable but lasting option. I’d like to lose the zinc plating all together because this is, in my opinion the root of all my evils. If I were to just powder coat, what in your opinion would be the best cost to quality option? I’ve been looking up thermoplastic coating with great interest. Please advise on surface preparation too. I’d like to cut out as many service providers as possible and have greater control and certainty regarding the accuracy of the coating process. Perhaps your solution may be worth spending on a small home setup if it’s affordable. I make standard size door gates, which are installed both indoors and outdoors. From indoor up to 100 km from the coast to outdoor 100 m from the sea.
Kind regards
Barry Lottering
Port Elizabeth, South Africa
Hi Barry,
Thanks for the question. I took a look at your website and, wow, you do amazing work. You turn simple gates and railings into exquisite artistry.
I think you probably already know the source of the inconsistency in your coatings, it's the zinc plating. Undoubtedly it is wise to use a two-coat process to ensure a good combination of corrosion resistance and outdoor durability. This is definitely a must for hardware that has to endure a coastal environment. But zinc plating can be inconsistent.
Here is what I recommend. Take the finishing process in-house. This will involve not only coating process, but also the metal preparation as well. Since you are laser cutting some of the ware and the parts have residual mill scale you should blast them with a decent media to lose the mill scale and clean the laser cut edges. I suggest aluminum oxide. Next step is a three-stage phosphate pretreatment. Google "metal pretreatment companies" in South Africa and ask them for recommendations. After pretreatment, thoroughly dry the parts with a convection type oven. The air movement will help to completely dry the metal surface.
The next step is to completely cover the metal with an epoxy powder coating primer. If you have tight areas inside of channels, you should pre-heat the metal and spray those areas while it is still hot. After the parts are completely coated, bake the primer for about 5-10 minutes (see the supplier's technical data sheet for the correct temperature). Make sure the coating has flowed out adequately to form a smooth surface. The 5-10 minutes should represent a deliberate underbake. This provides optimum adhesion of the next coat. After the part has cooled, lightly sand the primer with a 220 grit sandpaper. Reheat the part to about 110-125 ⁰C and then apply a polyester powder topcoat. I recommend a "superdurable" grade for good UV durability. Place the coated part in the oven for a full cure cycle.
This process and these materials will ensure an excellent coating that should provide 10 years durability with only moderate fade and chalking. And as long as the part is completely coated and has not been breached it will resist corrosion as well. Furthermore, by taking the finishing process in-house, you will have complete control of the final quality.
I hope this helps and I sure would love to visit Port Elizabeth someday. South Africa is on my bucket list and I need a good excuse/reason to visit.
Best regards.
Joe Powder
Have a question for Joe Powder? Email kevinbiller@yahoo.com. And be sure to listen to the Ask Joe Powder “Powdcast” for all the latest news, insights and technology in the powder coatings industry. Click here to listen!