We powder coat steel tubing...
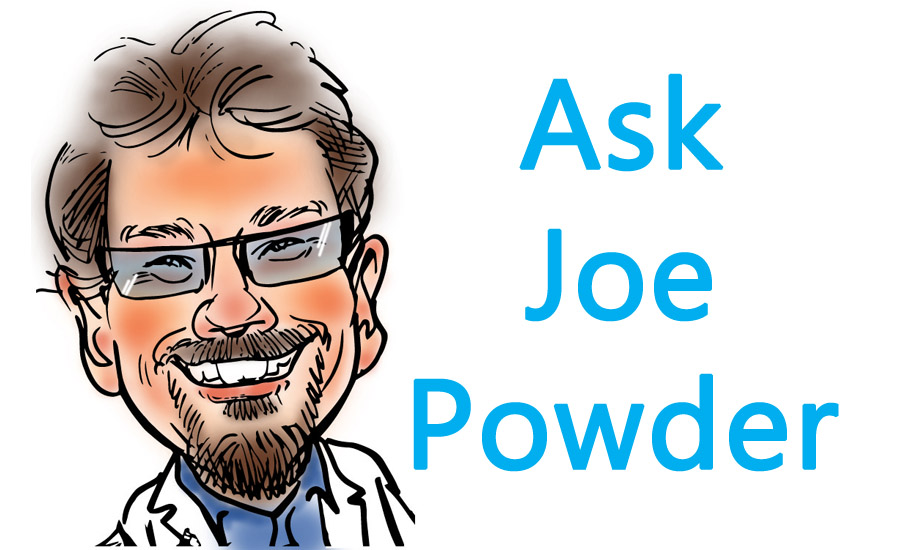
Ask Joe Powder
Joe,
We powder coat steel tubing for broom handles and paint about 1,000,000 tubes per month. We have been experiencing some contamination between color changes. We think this might have to do with our gun hoses. How often should we be replacing the hoses that go from the pump to the gun?
Hi Adam,
Excellent question. That’s a lot of broom handles. How many are for floor maintenance and how many for transport on Halloween? My thoughts on your hose situation are thus: hoses are a relatively small investment, and contaminated products and line stoppages can be costly and a pain in the neck.
I would consider having separate sets of hoses for each color. You didn’t mention how many colors you run, but if you have a large number you can consider using the same hose set for colors that are close in hue. For instance, a set for red colors, another for blacks and dark grays, etc. Hose can be purchased in bulk and the ease of color changes is enhanced with hoses dedicated to each color.
If your purchasing manager balks at the added small cost of more hose please show him or her this message.
Dear Joe,
Our current product, which is an aluminum sand casting, is powder coated to many of our customers’ color choices. We find that we have many more problems with outgassing or bubbling on colors we consider as higher gloss than other colors. This may just be a coincidence but we were wondering if the gloss levels can affect the susceptibility to outgassing because of a faster or slower set or something else we are unaware of.
Hi Cherie,
This is an interesting observation. This situation requires one to slip on their “correlation vs. causation” helmet and sort through the facts. It sounds like you have established the correlation factor here. Nice work. Root cause analysis is a mightier task, but I will provide some insight to help you in understanding the outgassing phenomenon and how it is related to powder coatings.
Fundamentally, as you know, the porosity in castings causes the expulsion of entrapped gas at elevated temperatures. Powder coatings typically require 10 to 20 minutes at 350 to 400 ⁰F to cure. These baking conditions will cause pores to expel gas. If the gas is emitted during a critical stage in the powder coating crosslinking reaction the escaping gas creates an ugly, crater-like defect.
We powder formulators have developed formulation schemes that can alleviate the formation of these kinds of defects. We basically incorporate an additive that allows the gas to pass through the film then reflow into the void created by the expulsion. Some powder suppliers call these products off-gassing resistant (OGR) or out-gassing friendly (OGF). I’m sure other monikers exist. These products work pretty well, however this formulating trick is not available in every product, hence the probable disparity in performance you are observing.
A solution to this problem could lie in a process alteration. Preheating the casting before powder coating usually eliminates the defects caused by the outgassing of castings. Perhaps you could segregate the special, high-gloss powder coating runs and preheat the parts prior to applying the powder. Alternately you could bug your powder coating supplier to modify the high-gloss products with their secret sauce. This, I’m sure, will come with a premium and possibly a time delay to get the formula modification through the lab.
Have a question for Joe Powder? Email kevinbiller@yahoo.com. And be sure to listen to the Ask Joe Powder “Powdcast” for all the latest news, insights and technology in the powder coatings industry. Click here to listen!