You Can’t Omit Emissions When It Comes to VOC Testing
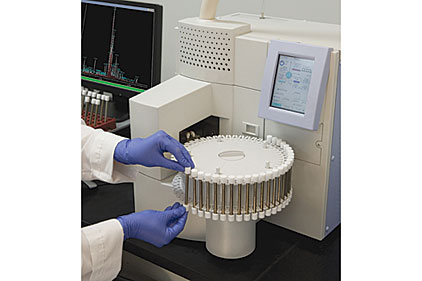
Manufacturers are accustomed to operating in this environment. The latest in a long line of new requirements is product emission testing. With people spending upwards of 90% of their time indoors, there is increasing concern for the quality of the air we breathe in the places where we live, work, learn and play. Sustainable building programs, and even building codes regulated by state and local authorities are increasingly demanding products that support good indoor air quality (IAQ). One of the most popular: the U.S. Green Building Council’s LEED Program (Leadership in Energy and Environmental Design), is currently undergoing final review, and an updated standard is slated for release in 2012.
A part of the proposed updated requirements in LEED 2012 is a shift from VOC content testing only, to additional VOC emissions testing for good IAQ. This is not the only standard: additional codes and international regulations are requiring VOC emission testing. All of this means that product emission testing is relevant to coatings manufacturers, and manufacturers are adopting this testing as a necessary product-development step in meeting verification requirements.
The Growing Green Landscape
Green Outlook 2011: Green Trends Driving Growth, a report by McGraw Hill Construction, estimates the value of green building construction to be between $43 billion and $54 billion in 2010 and projects that number will triple or quadruple to between $120 billion and $145 billion by 2015. Awareness of indoor air quality among the green building community and occupants alike is growing. Key green building programs such as LEED 2012, the International Green Construction Code (IGCC) and the National Home Builders Association’s (NAHB) Green Standard all include criteria for measuring chemical emissions from products inside a building. Programs certifying products with environmental attributes and regulatory programs requiring product emission testing internationally continue to increase, making VOC emissions a requirement for acceptability in the marketplace.
The bottom line for coatings manufacturers is that there will be growing demand for low-emitting coatings and also an increasing number of mandates requiring emission testing. The burden of proof will rest upon manufacturers, and they must find the most cost-effective, efficient way to incorporate product emission testing into the product engineering process.
VOC Content Does Not Equal VOC Emissions
Manufacturers have long been familiar with VOC content testing as specified by the U.S. EPA Test Method 24. This method is generally not sensitive or reproducible for content levels less than 0.1 to 1%. Consequently, it is common to find VOC emissions from a product even though it has been reported to have no VOC content based on Method 24. Some VOCs, such as formaldehyde, may be generated as byproducts or by chemical reactions during coating application; these VOCs cannot be measured in the content analysis.
In 2011, UL Air Quality Sciences, a product emissions testing laboratory, conducted a study to compare VOC content and emissions.1 In this study, IAQ scientists tested 26 untinted paint products applied to gypsum board. These paints had a range of stated VOC content levels from 0 to 150 g/L, with all paints conforming to the LEED New Construction low-emitting credit criteria for coatings. The products were analyzed for VOC emission using gas chromatography/mass spectrometry(GC/MS) and for low-molecular-weight aldehydes using high-performance liquid chromatography(HPLC), following the state of California’s (CDPH/EHLB/Standard Method V1.1), “Standard Method for the Testing and Evaluation of Volatile Organic Chemical Emissions from Indoor Sources Using Environmental Chambers.”
Measurable levels of formaldehyde and ethylene glycol were in the emissions from almost half of the paint samples. Seven samples had formaldehyde levels exceeding the California Chronic Reference Exposure Limit (CA CREL) of 9 µg/m3, and two samples had ethylene glycol emissions above the ½ CA CREL limit (200 µg/m3).
The study results clearly demonstrate that paint VOC content should not be used as a proxy for paint VOC emissions into indoor air. Low total VOC content is not necessarily indicative of acceptable VOC emissions for specific compounds with known health impacts. Thus, building designers, owners and operators, or occupants may be provided a false sense of security regarding the quality of the indoor air.
Table 1 includes a list of VOCs commonly emitted from latex and oil-based or alkyd paints. In high concentrations, these chemicals can have a negative impact on health.
What Manufacturers Can Do
Understanding that VOC emissions are of increasing concern to the building community and consumers alike, many manufacturers are at a loss regarding initial steps to begin the process of having their products’ emission tested. It may seem like a daunting task, but with the right partner, it need not be any more overwhelming than conducting VOC content testing. The initial step for manufacturers is simply recognizing the importance of product emissions as yet another product performance requirement. With a little insight and some planning, product emission testing can be conducted cost effectively and offer coatings manufacturers an opportunity to differentiate their products and reach new markets. Here are some tips:
Be prepared to share formulations − While content does not equal emissions, understanding the chemicals used in formulation can help experienced chemists predict if there are specific VOCs that are likely to be emitted based on individual volatility or combinations of chemicals in the content. By having the formulation documented and readily available to share, it is also easier for chemists to identify the components that may be producing irritating odors and irritation.
Conduct baseline testing – For manufacturers new to product emission testing, it makes sense to test to a standard that provides a comprehensive result, both in terms of emissions measured and time tested, so that the results can be used to model data to meet other requirements. California Specification 01350 offers a good example of a test that provides for a maximum curing time and analyzes for all VOCs.
Work to categorize – In an effort to avoid the expense of testing every single SKU, it is a good idea to organize products under categories that encompass similar formulations. This makes testing easier and more streamlined, enabling the testing of one product to provide results for a cluster of products. Indoor air quality scientists can assist with this process.
Certify products – For manufacturers that have conducted product emission testing and their products offer great IAQ performance, they may consider having those products certified by one or more voluntary IAQ certification programs. These certifications are often known by building professionals, consumers or relevant markets and could offer a point of differentiation from competitors.
Select a knowledgeable partner – With environmental codes and standards changing every day around the world, it requires a dedicated resource to keep up with the latest standards. An experienced IAQ partner will be fully aware of all of the latest changes and standards related to product emission testing.
Making Green Sense
Not only does product emission testing provide valuable information about a product’s environmental performance, but it also makes sense from a financial standpoint. The ROI on product emission testing can be a result of increased revenues based on the ability to sell to new green building markets demanding low-emitting products. In other cases, it is simply a requirement to sell a product in EU countries, many of whom are requiring product emission testing. Earning an environmental label such as GREENGUARD or Blue Angel may also help differentiate products from the competition, earning a premium price or simply increasing product desirability. Manufacturers that conduct product emission testing can also resolve odor complaints, getting to the source of the problem quickly. Most importantly, supporting human health is simply the right thing to do. Moving forward, coatings manufacturers should note that you cannot omit product emission testing when it comes to VOC determinations.
References
1 Mason, S.; and Ceragioli. Paint Volatile Organic Compound Emissions and VOC Content Comparison Study, Proceedings of Indoor Air 2011, Austin, Texas, 2011.
For more information, e-mail mblack@aqs.com, or visit http://www.aqs.com.
Looking for a reprint of this article?
From high-res PDFs to custom plaques, order your copy today!