Get Reactive: Benefits of Plural-Component Coatings

Reactive-cure coatings often are used to finish heavy-duty construction equipment and other OEM products.
Industrial manufacturing OEMs often experience bottlenecks at the paint line that impact throughput times. Relatively simple process changes, coupled with the use of reactive-cure coatings, can increase manufacturing volumes from 20 to 50%. Also called plural-component or two-component coatings, reactive-cure finishes offer several production advantages to improving efficiency. But not all manufacturers take full advantage of the benefits they can provide.
Environmentally, reactive-cure coatings minimize volatile organic compounds (VOCs) and reduce energy/curing costs when compared to single-component material. Certain reactive-cure coatings can be applied in one-third of the traditional time for this type of coating, significantly enhancing production efficiency and increasing throughput.
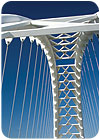
In addition to OEM products, outdoor structures such as bridges benefit from the fast cure speed and long-term durability of reactive-cure coatings.
Reactive-Cure Technology Options
With three basic product platforms available, reactive-cure coating solutions provide a substantial amount of performance flexibility. Many are capable of wet-on-wet application, so the product can move straight from priming to painting with no cure time required.Epoxy Technology. Epoxies consist of an epoxy resin with tough corrosion protection that can be sprayed wet-on-wet with a urethane or non-isocyanate (NISO) topcoat. They typically are used in primer applications and provide robust chemical resistance.
Urethane Technology.Urethanes can be used as a topcoat in direct-to-metal applications but most often are used over a primer for improved corrosion protection. At the upper end of the spectrum, they can provide a high-end quality finish comparable to the coatings used in the automotive industry, with exceptional weathering characteristics and strong chemical resistance.
NISO Technology. NISO coatings can be used either as a topcoat or a direct-to-metal primer application with comparable performance capabilities to urethane technology, yet they don’t contain isocyanates like urethane. They provide durable weathering characteristics, solid chemical resistance and a high-quality finish. With a significantly longer pot life than urethanes, they minimize material waste. This coating tends to cost more than other reactive-cure options.

Figure 1. Cure rate comparison between single-component and reactive-cure coatings.
Application Considerations
A higher-quality, more durable finish often can be achieved with reactive-cure coatings, along with significant material and productivity savings. Even with an investment in plural-component equipment, payback often is achieved within two years or less. Following are some considerations when using this type of coating.Mixing and Applying. Materials can be hand-mixed, but this process typically creates more material waste. It’s difficult to determine exactly how much coating will be required, and the pot life has to be longer - typically three to four hours - to allow adequate time to mix, prepare, apply and clean up. Any product not used within the pot life has to be disposed of, creating additional costs. An electronic proportioning system can eliminate a significant amount of labor, energy and waste from your painting process. In essence, there is no pot life because the material is mixed near the spray gun when it’s needed.
Cure Time. Two-part coatings typically cure faster than single-component materials and at lower temperatures than baking products, so they spend a shorter time in the oven or air drying (see Figure 1). They don’t have to be fully cured when removed from the drying area, so less energy is required to get top performance. When using a wet-on-wet application, one step of the curing cycle can be eliminated by going straight from the primer coat to topcoat. And if you use electronic proportioning, you can formulate the coating to cure in as little as 30 minutes.
Coverage. Reactive-cure coatings typically are applied using air spray, high-volume low-pressure (HVLP), air assisted airless or airless technology, depending on the type of finish required. With a high-performance coating, operators may only need to apply one pass rather than multiple applications, saving time and labor costs.
Standard vs. Custom Formulations
Nearly every coatings manufacturer offers custom color matching, but not all offer custom formulating of the coating itself. For example, if you purchase an off-the-shelf coating, you do not have control of the pot life or cure rate.If you want to maximize efficiency on your production line, consider a custom formulated coating that takes into consideration your production line and how you’ll be mixing, applying, and curing your painted products. You can achieve significant productivity enhancements by ensuring that you’ve selected the right formulation for your specific application needs.
In addition, when making a purchase, consider the total cost for the product. If it is premixed, it’s ready to use. If you need to add solvent, you increase your material costs and preparation time.

Steps to Maximize Cost Savings Using Reactive-Cure Coatings
Performance Based on Industry Trends
Within the coatings industry, there is a trend toward continuing to lower solvent emissions levels. In the U.S., the trend is to reduce VOCs with reactive-cure products. Two-component materials have the capability of achieving VOC levels of 2.3 to 2.8 lb/gal. In Europe, there is a growing trend toward water-based technology, and a wide range of plural-component coatings are available to meet this need.There’s also a growing global trend to focus on total cost solutions - not just on the price of paint, but on the entire paint process, from operator time to throughput efficiency. The lowest-cost coating isn’t necessarily the most cost-effective solution. Achieving a lower total cost in the manufacturing process is often possible by streamlining the production process used with reactive cure coatings.
Another industry trend is lean manufacturing, which is focused on eliminating all waste in manufacturing processes and aligning production with customer demand. Some of the steps that may be taken to improve efficiency within coating operations range from redesigning the paint line to reducing the cost of operating paint ovens by using a faster curing product.
Reactive-cure coatings offer excellent opportunities to meet goals related to lower VOC emissions, lower total cost solutions and lean manufacturing.
For more information, visit www.valsparglobal.com/corp.
Looking for a reprint of this article?
From high-res PDFs to custom plaques, order your copy today!