Weathering Testing: Real-Time Temperature Measurement of Coatings
Researchers have used instrument-provided black panel temperatures to estimate the temperatures of coatings of real interest. However, such estimates are error-prone for a number of reasons. Recently, new technology has been developed to measure and provide the specific sample surface temperature of materials under test, thereby providing more accurate and reliable weathering test results.

Weathering is caused by environmental stresses that create generally unfavorable chemical and physical changes in any exposed organic material. The main weathering stresses are light and moisture in any of its forms. However, heat also is extremely important since any reaction initiated by light is driven kinetically and therefore tends to increase significantly with temperature.1
The importance of the coating temperature is suggested by the “rule of thumb” that states that reaction rates double for every 18°F (10°C) increase. Fischer, et. al., found factors ranging from 1.2 to 1.8 per 18°F increase, depending on the material tested.1
Most laboratory weathering devices used for temperature characterization are equipped with a “black panel” that usually complies to either of the designs generically described by ASTM G 151.2 During the course of a weathering test, the black panel is intended to provide an estimate of the worst-case sample surface temperature. This test assumes that the panel, primarily because it is coated with an efficient, black solar absorber, will record a higher surface temperature than most, if not all, other “real” coatings.
Researchers have used the instrument-provided black panel temperature to estimate temperatures of the coatings of real interest.1 However, such estimates are error-prone for three main reasons: 1) operational variability among different designs of black panel is well documented;3 2) the properties of black panel coatings change during the course of their service life, effectively creating a moving baseline; and 3) changes in coatings being tested cannot be expected to parallel changes occurring in black panels.
In short, the critical coating temperature parameter is unknown in today’s laboratory weathering tests. Additionally, there are no current reliable means to estimate these temperatures.
The need to know the temperatures of specific materials while under test has been expressed repeatedly throughout various literature,4 but until now, presumably because of the inherent challenges, laboratory instrumentation has been incapable of providing this information.

The infrared (IR) sensor was chosen to respond in a spectral range exclusive of the xenon output wavelength range to make it insensitive to light. The device has a facility to keep the non-contact IR sensor head free of any condensation for proper performance. The unit’s operating air temperature range of 32 to 185°F (0 to 85°C) and relative humidity range of 0 to 100% encompass all known weathering test methods. The system incorporates a small-volume sensor so that it is minimally obtrusive to test specimens, and its spot size and response time are appropriate to obtain adequate signal response from rotating specimens.
The device was successfully tested in an Atlas MTT Ci4000 WeatherOmeter® for the following performance criteria:
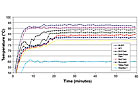
Tests with various materials were conducted with preselected emissivity settings of 0.85, 0.90 and 0.95, while all other test conditions were kept constant (black panel temperature [BPT] at 140°F/60°C, chamber temperature [CHT] at 100°F/38°C, and relative humidity [RH] at 50%). Minimal temperature differences were observed between the various emissivity settings. These results suggest that a single, nominal emissivity setting is sufficient to provide acceptable accuracy on a wide variety of materials.


The averages and standard deviations were plotted for the two measurement methods. The data for the SAE J1885 test method shown in Figure 3 was representative of all the test methods. Generally, there was good agreement between the average temperatures as measured by both techniques, while the measurements obtained with the new technology were more repeatable, as indicated by lower standard deviations.
Figure 4 compares the average temperature readings for all test methods referenced earlier. The near 45 degree “line of equality” illustrates good agreement between the specific sample surface temperature measurement method and the established 3M, fixed thermocouple technique under the very different conditions embodied in the test methods.
By providing the capability to record in situ coating surface temperatures in real time, the new specific sample surface temperature measurement technology can redefine how weathering tests are conducted. The system makes it possible for researchers to conduct investigations in materials durability testing that were either very difficult or impossible before, thereby providing more accurate and reliable test results.
*The technology is commercially available as S3T™ or S3T™ through Atlas Material Testing Technology LLC, Chicago, IL For more information, visit www.atlas-mts.com

Weathering is caused by environmental stresses that create generally unfavorable chemical and physical changes in any exposed organic material. The main weathering stresses are light and moisture in any of its forms. However, heat also is extremely important since any reaction initiated by light is driven kinetically and therefore tends to increase significantly with temperature.1
The importance of the coating temperature is suggested by the “rule of thumb” that states that reaction rates double for every 18°F (10°C) increase. Fischer, et. al., found factors ranging from 1.2 to 1.8 per 18°F increase, depending on the material tested.1
Most laboratory weathering devices used for temperature characterization are equipped with a “black panel” that usually complies to either of the designs generically described by ASTM G 151.2 During the course of a weathering test, the black panel is intended to provide an estimate of the worst-case sample surface temperature. This test assumes that the panel, primarily because it is coated with an efficient, black solar absorber, will record a higher surface temperature than most, if not all, other “real” coatings.
Researchers have used the instrument-provided black panel temperature to estimate temperatures of the coatings of real interest.1 However, such estimates are error-prone for three main reasons: 1) operational variability among different designs of black panel is well documented;3 2) the properties of black panel coatings change during the course of their service life, effectively creating a moving baseline; and 3) changes in coatings being tested cannot be expected to parallel changes occurring in black panels.
In short, the critical coating temperature parameter is unknown in today’s laboratory weathering tests. Additionally, there are no current reliable means to estimate these temperatures.
The need to know the temperatures of specific materials while under test has been expressed repeatedly throughout various literature,4 but until now, presumably because of the inherent challenges, laboratory instrumentation has been incapable of providing this information.

Figure 1. The interior of the S3T system.
Specific Sample Surface Temperatures
Recently, new technology* has been developed to measure and provide the specific sample surface temperature of materials under test (see Figure 1). The technology has been thoroughly evaluated for its ability to provide accurate surface temperature measurements for a variety of materials under a range of weathering test conditions.The infrared (IR) sensor was chosen to respond in a spectral range exclusive of the xenon output wavelength range to make it insensitive to light. The device has a facility to keep the non-contact IR sensor head free of any condensation for proper performance. The unit’s operating air temperature range of 32 to 185°F (0 to 85°C) and relative humidity range of 0 to 100% encompass all known weathering test methods. The system incorporates a small-volume sensor so that it is minimally obtrusive to test specimens, and its spot size and response time are appropriate to obtain adequate signal response from rotating specimens.
The device was successfully tested in an Atlas MTT Ci4000 WeatherOmeter® for the following performance criteria:
- Sensor sensitivity and sample tracking capability
- Performance under various test conditions
- Performance on various types of materials and different surface finishes
- Performance using different sensor configurations (exhibiting sensitivity to variations in physical setup).
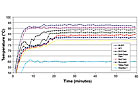
Figure 2. S3T temperature history of various colored coatings.
Preset Emissivity
A coating’s emissivity depends on its temperature, its specific material property and the wavelengths of its emmitance. Thus, a single, constant emissivity setting for IR temperature measurements of all materials is a potential source of error and is not considered ideal. Fortunately, for most frequently tested materials, the emissivity falls in the fairly narrow range of 0.85 to 0.96 for temperatures ranging from 32 to 212°F (0 to 100°C).Tests with various materials were conducted with preselected emissivity settings of 0.85, 0.90 and 0.95, while all other test conditions were kept constant (black panel temperature [BPT] at 140°F/60°C, chamber temperature [CHT] at 100°F/38°C, and relative humidity [RH] at 50%). Minimal temperature differences were observed between the various emissivity settings. These results suggest that a single, nominal emissivity setting is sufficient to provide acceptable accuracy on a wide variety of materials.

Table 1.
Sensitivity
A cross-section of typical weathering samples, including painted surfaces (coatings), textiles and polymers, was used to test the technology’s sensitivity to different materials. Due to space limitations, only the time profiles of the coated specimens are shown in Figure 2. However, the mean and standard deviations of temperature measurements for a variety of materials are summarized in Table 1. The measurements indicate that the specific sample surface temperature measurement system is usable on the wide variety of materials with different surface finishes that are typically weathered. Additionally, the low standard deviation numbers are an indication of the system’s good repeatability when performing a significant number of sequential measurements on each type of surface.
Figure 3. S3T PVC temperature measurements compared to the embedded thermocouple method.
Validation
A replicate set of the colored polyvinyl chloride (PVC) coatings on aluminum panels with embedded thermocouples, described by Fischer, et. al., in “Surface Temperatures of Materials in Exterior Exposures and Artificial Accelerated Tests,”1 was provided courtesy of 3M. The surface temperatures of these panels were measured by the new technology and simultaneously by the method using embedded thermocouples described in the paper. The comparisons were conducted under the widely disparate conditions of the test methods outlined in SAEJ1885,5 SAEJ1960,6 AATCC169-17 and GM 3414TM,8 as well as the following International Standards Organization Weathering Standards: ISO195-B02, ISO105-BO6 and ISO11341-1.
Figure 4. A comparison of temperature measurement techniques over a range of conditions.
Figure 4 compares the average temperature readings for all test methods referenced earlier. The near 45 degree “line of equality” illustrates good agreement between the specific sample surface temperature measurement method and the established 3M, fixed thermocouple technique under the very different conditions embodied in the test methods.
Redefining Weathering Testing
Manufacturers of durable products such as automobiles constantly are challenged to satisfy appearance demands, both for “showroom appeal” and for the in-service maintenance of original appearance - a challenge that is compounded by the ever-increasing array of coating materials and colors. Accurate weathering tests, with an increasing reliance on accelerated laboratory tests, are an important part of ensuring a customer’s long-term satisfaction with the finished product.By providing the capability to record in situ coating surface temperatures in real time, the new specific sample surface temperature measurement technology can redefine how weathering tests are conducted. The system makes it possible for researchers to conduct investigations in materials durability testing that were either very difficult or impossible before, thereby providing more accurate and reliable test results.
*The technology is commercially available as S3T™ or S3T™ through Atlas Material Testing Technology LLC, Chicago, IL For more information, visit www.atlas-mts.com
Looking for a reprint of this article?
From high-res PDFs to custom plaques, order your copy today!