11 Tips for Buying a Used Rectifier
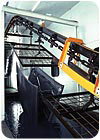
Rectifers are used to provide power for electrocoating and numerous other finishing applications. Photo courtesy of PPG.
Rectifiers - electrical devices that convert alternating current (AC) power to direct current (DC) - are used to provide power for a number of finishing applications. There are many reasons that a coater may wish to purchase a used rectifier, including lower cost, an immediate need or the desire to have a spare unit. Although the initial advantages may make this approach attractive, it is important to use the same care in purchasing a used rectifier as with a new one. Key considerations include the manufacturer, control type, size, input and output amperage and voltage, cooling method, efficiency, ripple, age and condition, warranty, and price.
1. Manufacturer. Is the manufacturer still in business? Is the manufacturer located conveniently so that replacement parts and schematics are easily available? Is the brand of rectifier the same as other units you have in your shop so that parts and circuit boards are compatible? What is the reputation of the manufacturer within the industry?
2. Control. What type of control does the used rectifier have? Is it tapswitch, powerstat, saturable core or SCR? Do you need to have either constant current or constant voltage for your process? If so, will you be able to use a rectifier that cannot provide this capability? Do you control your rectifiers with a PLC? If so, you might not be able to control your rectifier unless it has the proper type of control for the voltage and amperage output.
3. Size. What kind of footprint does the rectifier have? Will it fit in the space you have available, or will you have to locate it farther from the line? If it has to be relocated, will the existing buswork fit or will new bussing be required? Will there be a voltage drop if the bussing is extended, and will that affect the process?
4. Input Voltage and Amperage. Does the used rectifier have the same voltage requirements as those available in your facility? If not, are you willing to install a step-up or step-down transformer to provide the proper voltage? Will it draw more amperage than your wiring will accommodate? If so, are you willing to add larger feed lines, fuses, and disconnects to accommodate the used rectifier?
5. Output Voltage and Amperage. Does the unit have sufficient voltage for the process? If you are using it as a spare, can it operate in different applications? If the maximum output voltage is too high, will it operate efficiently or without excessive ripple at lower voltages? Does the used rectifier have sufficient amperage for your application? Can it operate at full output without overheating? If the used unit puts out more amperage, can the existing buswork accommodate it?
6. Cooling. Do you prefer air-cooled or water-cooled in your shop? Can you accommodate the heated water generated in a water-cooled rectifier in your process, or will you have to send it to a sewer and pay waste treatment fees? Using an air-cooled rectifier in a location with high humidity and a chemical atmosphere can compromise its reliability.
7. Efficiency. Is the used rectifier as efficient as the unit it is replacing? If not, it might draw more amperage to do the same amount of work and might overload your existing wiring.
8. Ripple. Does the used rectifier have higher ripple than your process can accommodate? If so, are you willing to buy a choke? How will the additional price of a choke affect what the rectifier is worth to you?
9. Age and Condition. Although age and condition are intertwined, you are primarily interested in the condition of the rectifier. A unit that has been kept in a clean environment and well maintained might be in better condition than one that is not as old but has not been well taken care of. Pay particular attention to the major components, including the main transformer, SCR stacks, diode stacks, tapswitches, powerstats and contactors. The ancillary components, including meters, relays, pots, stepdown transformers, and even firing boards, can be replaced or repaired. If the wiring is in a tangle, troubleshooting can be time-consuming and expensive. If possible, examine the unit in person. If that isn’t possible, have the dealer send digital photos and nameplate data so you can confirm its age and condition.
10. Warranty. What sort of warranty is provided for the used rectifier? Does it include both parts and labor? Will the unit have to be sent back to the provider for warranty service, or will the provider send a technician to perform the work? Will you be responsible for travel costs? Is the unit completely rebuilt, which involves more removal and replacement of components than if it is reconditioned? Or is the unit merely sold in “as-is” condition, which means that you will assume more of the risk if the unit fails? Is the dealer someone you have done business with before, and is he or she reputable?
11. Price. What you are really looking for is value. Are you paying too much for the type, make and condition of the rectifier you are buying? If you are buying for bottom dollar, you may be willing to take a unit that will require some work to recondition it if the major components are in good condition. If you need a unit that works perfectly as soon as you apply power and hit the “start” button, you might need to pay a little extra.
Some coaters buy used rectifiers without due consideration and wind up with more grief than relief if they need them to replace a line unit that fails. Just as with the purchase of any other major piece of hardware in your operation, some initial foresight and effort can save you a lot of headaches in the long run.
For more information about rectifiers, contact JP Tech, Inc. at 262.642.7671 or customerservice@jptechinc.com, or visit www.drrectifier.com.
Looking for a reprint of this article?
From high-res PDFs to custom plaques, order your copy today!