Cost-Effective Conductivity
New coatings based on a conductive polymer known as soluble doped polyaniline can offer a significant improvement in functionality and ease of application over current capacitor coating technologies. The new coatings provide the same benefits as traditional conductive polymer-based coatings but with significantly less manufacturing time, as well as other enhanced attributes.

Capacitors are essential to the functionality of electronic products. From automobiles to wireless phones, laptops and GPS devices, all electronics need capacitors to function. Using conductive polymer coatings as cathodes in solid electrolytic capacitors is equally vital to the electronics manufacturing industry, as this type of coating provides several key benefits.
Conductive polymer cathodes generally increase the speed at which a capacitor can release its charge - a critical feature for today’s high-speed electronics. They also lower the equivalent series resistance (ESR), which helps reduce energy requirements on circuit boards. Additionally, conductive polymer cathodes allow higher capacitance per unit, which means that more energy can be created in a smaller area, supporting the drive for device miniaturization.
Additionally, current conductive polymer coatings are negatively affected by the moisture and humidity to which capacitors are exposed naturally in manufacturing and in practical field use. This weakness decreases the charge storage capability of a capacitor, rendering it less effective.
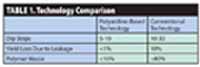
The new coatings are true film formers that provide uniform coverage on the entire part, including corners. They are also thermally stable at and above 392°F (200°C). In fact, tests have shown that the conductivity of the coatings increases by 21% after cast films are exposed to 212°F (100°C) for 100 hours. In the capacitor manufacturing process, this benefit translates to durability as anodes are exposed to heat. The coatings are not brittle; they easily conform to the thermal expansions of other layers of material in the capacitors.
Another critical property of the new technology is its inherent hydrophobicity, a characteristic that is not available in current conductive polymer-based coating chemistries. Moisture and humidity, to which capacitors are exposed during manufacturing and in practical use in the field, bear little to no effect on the conductivity of the new coatings. Accelerated aging tests on thin film samples showed that the polyaniline-based coatings consistently outperformed the current leading coating. After 100 hours of continuous exposure to 85% relative humidity and 185°F (85°C), two different grades of polyaniline coatings with two different starting conductivities experienced little to no change in conductivity (see Figure 1).

A beneficial quality of the new coatings is their tunable work function, which makes the coatings more compatible with a variety of metals (see Figure 2). Although metals have a fixed work function, the work function of polyaniline used in the new coatings can be tuned using a proprietary doping process, in which the charge density along the polymer backbone is controlled. This means that the coatings can be adjusted according to the needs of individual capacitor manufacturers. Because of their tunable work function, the coatings form a self-healing structure that tends to oxidize any defects in the metal oxide structure.
The coating materials also have a high band gap (3 eV). This characteristic implies that when de-doped, the polymer forms a good dielectric insulator that will protect the capacitor during a short-circuit event. This property adds an important safety feature for capacitor users.
Reduced Production Time. The solubilizing dopant in the new coatings not only converts the polyaniline from an insulator to a conductor, but it also facilitates the formation of a processable coating material. Because of the way the coatings are formulated, they require no chemical polymerization on the capacitor. Additionally, when a capacitor anode is dipped in the polyaniline-based system, it is coated with uniform, core-penetrating coverage. It is this coverage that allows acceptable thicknesses to be achieved with just one to five dip steps. For capacitor manufacturers, this benefit can translate into a savings of at least 10 normal working days of production time compared to conventional conductive coatings.
Reduced Part Rejects. With many conventional coating systems, exposed corners lead to part rejects and yield loss due to capacitance leakage. Many traditional conductive polymer cathode materials have as much as 10% yield loss due to leakage. The ability of the polyaniline-based coatings to provide uniform coverage on the entire part, including corners, can reduce yield loss due to leakage to less than 1%.
The polyaniline-based coatings also do not block pores, which sometimes can happen with dispersions of other conductive polymer coating materials. Another benefit is that the new coatings reduce capacitor failures because they builds thickness and bond well to previous layers, such as dielectric oxides and other conductive polymers. Because of their excellent adhesion to other chemistries, the coatings can serve as an external sealant for manufacturers that use other coatings for initial layers.
Reduced Manufacturing Costs. The polyaniline-based coatings significantly reduce the production time of coating capacitor anode bodies, thereby providing capacitor manufacturers with savings on overall production costs. The key to this savings is the technology’s ability to coat anodes so effectively. The substantial number of dip steps required with conventional coatings, coupled with the limited pot life of some key raw materials, can cause nearly 80% of the polymer raw materials to be wasted over a single production cycle. In contrast, the polyaniline-based coatings are pre-polymerized and are applied directly to the substrate. As a result, only 10% or less of the solution is lost due to waste in each production cycle. This waste reduction can translate into considerable cost savings and economic benefits for the capacitor manufacturers and can give companies a significant edge over manufacturers still relying on current coating systems.<
*The new coatings are supplied by Crosslink, St. Louis, MO, under the tradename Crosslink EMPAC™. For more information, visit www.crosslinkusa.com.

Capacitors are essential to the functionality of electronic products. From automobiles to wireless phones, laptops and GPS devices, all electronics need capacitors to function. Using conductive polymer coatings as cathodes in solid electrolytic capacitors is equally vital to the electronics manufacturing industry, as this type of coating provides several key benefits.
Conductive polymer cathodes generally increase the speed at which a capacitor can release its charge - a critical feature for today’s high-speed electronics. They also lower the equivalent series resistance (ESR), which helps reduce energy requirements on circuit boards. Additionally, conductive polymer cathodes allow higher capacitance per unit, which means that more energy can be created in a smaller area, supporting the drive for device miniaturization.
The Challenge
The conductive polymers currently used to coat solid electrolyte capacitor anode bodies typically are made from polythiophene- (PEDOT) or polypyrrole- (PPY), and they require chemical polymerization on the capacitor. This polymerization is a complex process that creates unnecessary waste - sometimes in excess of 80% - and slows the manufacturing process.Additionally, current conductive polymer coatings are negatively affected by the moisture and humidity to which capacitors are exposed naturally in manufacturing and in practical field use. This weakness decreases the charge storage capability of a capacitor, rendering it less effective.
A Polyaniline-Based Solution
To combat these challenges and provide a solution that is more cost-effective and time-efficient, researchers developed a new family of conductive polymer coatings* for solid electrolytic capacitor anodes. These new coatings, which are based on a conductive polymer known as soluble doped polyaniline, can offer a significant improvement in functionality and ease of application over current capacitor coating technologies. The new coatings provide the same benefits as traditional conductive polymer-based coatings but with significantly less manufacturing time, as well as other enhanced attributes. They can be used as a final coating layer that improves electrical connection around corners, edges and defects; as a total replacement for other systems and a new solution for the electrical completion stage; or as an internal coating that supports higher capacitance per unit volume and is used during the internal cathode formation stage.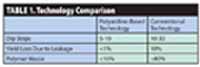
Table 1.
Performance Advantages
As with the current conductive polymer coatings, the polyaniline-based coatings are applied to capacitor anodes through a dip and dry process. However, the new coatings require only one to five steps before undergoing one final heat activation step, compared to up to 30 steps required with conventional systems (see Table 1). During the final step in the poyaniline-based technology, a proprietary process increases the conductivity and integrity of the coating. This short thermal treatment step at 302°F (150°C) crosslinks the polymer chains to strengthen inter- and intra-molecular bonding, linking one polymer chain to another and improving the coating’s performance. Specifically, this treatment step raises conductivity from ~10 siemens per centimeter (S/cm) to >100 S/cm. This step also gives the coating high levels of chemical resistance, further enhancing its compatibility and integrity when exposed to other chemistries and metals.The new coatings are true film formers that provide uniform coverage on the entire part, including corners. They are also thermally stable at and above 392°F (200°C). In fact, tests have shown that the conductivity of the coatings increases by 21% after cast films are exposed to 212°F (100°C) for 100 hours. In the capacitor manufacturing process, this benefit translates to durability as anodes are exposed to heat. The coatings are not brittle; they easily conform to the thermal expansions of other layers of material in the capacitors.
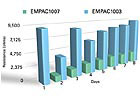
Figure 1. The above chart illustrates the stability of resistance of two different grades of polyaniline coatings when subjected to accelerated aging tests at 85% relative humidity and 185°F. Even after more than one week at these conditions, both types of polyaniline coatings showed little change in resistance.

Figure 2. The above diagram shows the relative work functions and band gaps for two different grades of doped polyaniline. While the band gap for the soluble, doped polyaniline is a constant 3.0 eV over different grades, the work function can be adjusted during manufacturing - a characteristic that allows flexibility to suit the needs of different capacitor manufacturers using different processes and materials.
Work Function
The work function of a material is defined as the energy necessary to extract an electron from a substance and move it to a zero energy state in vacuum. For metals, the work function dictates many of the properties and behaviors they exhibit. It also governs how metals interact with other materials.A beneficial quality of the new coatings is their tunable work function, which makes the coatings more compatible with a variety of metals (see Figure 2). Although metals have a fixed work function, the work function of polyaniline used in the new coatings can be tuned using a proprietary doping process, in which the charge density along the polymer backbone is controlled. This means that the coatings can be adjusted according to the needs of individual capacitor manufacturers. Because of their tunable work function, the coatings form a self-healing structure that tends to oxidize any defects in the metal oxide structure.
The coating materials also have a high band gap (3 eV). This characteristic implies that when de-doped, the polymer forms a good dielectric insulator that will protect the capacitor during a short-circuit event. This property adds an important safety feature for capacitor users.
Bottom-Line Benefits
The performance advantages of the new coatings can provide several distinct benefits to a capacitor manufacturer’s bottom line, specifically through reductions in production time, part rejects and manufacturing costs.Reduced Production Time. The solubilizing dopant in the new coatings not only converts the polyaniline from an insulator to a conductor, but it also facilitates the formation of a processable coating material. Because of the way the coatings are formulated, they require no chemical polymerization on the capacitor. Additionally, when a capacitor anode is dipped in the polyaniline-based system, it is coated with uniform, core-penetrating coverage. It is this coverage that allows acceptable thicknesses to be achieved with just one to five dip steps. For capacitor manufacturers, this benefit can translate into a savings of at least 10 normal working days of production time compared to conventional conductive coatings.
Reduced Part Rejects. With many conventional coating systems, exposed corners lead to part rejects and yield loss due to capacitance leakage. Many traditional conductive polymer cathode materials have as much as 10% yield loss due to leakage. The ability of the polyaniline-based coatings to provide uniform coverage on the entire part, including corners, can reduce yield loss due to leakage to less than 1%.
The polyaniline-based coatings also do not block pores, which sometimes can happen with dispersions of other conductive polymer coating materials. Another benefit is that the new coatings reduce capacitor failures because they builds thickness and bond well to previous layers, such as dielectric oxides and other conductive polymers. Because of their excellent adhesion to other chemistries, the coatings can serve as an external sealant for manufacturers that use other coatings for initial layers.
Reduced Manufacturing Costs. The polyaniline-based coatings significantly reduce the production time of coating capacitor anode bodies, thereby providing capacitor manufacturers with savings on overall production costs. The key to this savings is the technology’s ability to coat anodes so effectively. The substantial number of dip steps required with conventional coatings, coupled with the limited pot life of some key raw materials, can cause nearly 80% of the polymer raw materials to be wasted over a single production cycle. In contrast, the polyaniline-based coatings are pre-polymerized and are applied directly to the substrate. As a result, only 10% or less of the solution is lost due to waste in each production cycle. This waste reduction can translate into considerable cost savings and economic benefits for the capacitor manufacturers and can give companies a significant edge over manufacturers still relying on current coating systems.<
Improved Capacitor Manufacturing
The polyaniline-based conductive polymer coatings offer the potential for fundamental changes in the capacitor manufacturing process. With their improved performance characteristics, tunable work function and the ability to reduce production time and manufacturing costs, the new coatings can help capacitor manufacturers gain a competitive edge.*The new coatings are supplied by Crosslink, St. Louis, MO, under the tradename Crosslink EMPAC™. For more information, visit www.crosslinkusa.com.
Looking for a reprint of this article?
From high-res PDFs to custom plaques, order your copy today!