A Brilliant Finish
A new atmospheric plasma technology has been developed to eliminate common problems and improve the quality of the finish, thereby driving down the number of rejects. The technology can produce ultrafine cleaning and high activation on a wide range of surfaces, including plastics, metal and glass; these benefits, in turn, can promote the optimum adhesion of paints and coatings.

Design elements and immaculate surfaces are assuming an increasingly greater importance in today’s highly competitive markets. Whether on automotive components, mobile phone housings, perfume bottles or numerous other products, industry is spending exponentially rising sums to improve the appearance of products through enhanced finishing processes.
A decisive factor in finishing is achieving the best possible cleaning and activation of the surfaces to be coated. Pretreatment processes range from ionization or flame treatment to wet chemical processes, power washing, the use of primers and even mechanical cleaning with ostrich feathers. Despite all the efforts being made, the proportion of rejected parts in production caused by problems such as painting over dust particles is often well above 10%. Additionally, conventional pretreatment methods often create other challenges, such as static charging of surfaces or environmental pollution.
A new atmospheric plasma technology has been developed to eliminate these problems and improve the quality of the finish, thereby driving down the number of rejects. The technology can produce ultrafine cleaning and high activation on a wide range of surfaces, including plastics, metal and glass; these benefits, in turn, can promote the optimum adhesion of paints and coatings.
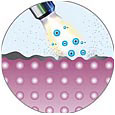
There are four commonly used plasma technologies. Vacuum plasma has generally been used for delicate applications and research, while flame treatment, corona and blown corona systems have been employed for less critical applications. All of these technologies typically have required particular conditions, including low pressure, extreme heat and/or high currents. The technology can be difficult to control precisely, and the high temperatures and voltages can be dangerous.
The new atmospheric plasma technology creates plasma in a jet through the action of a stepped, high-frequency, pulsed current that converts compressed air into a relatively low-temperature, voltage-free beam of plasma. The plasma beam is cool enough to blast a hole through a sheet of paper without catching it on fire.
In finishing applications, the plasma can be directed onto the material surface to remove static electricity and dust, as well as to vaporize contaminants, including waxes and silicone residues. Organic compounds are oxidized and turned mostly to water and carbon dioxide (see Figure 1).
The plasma also increases the surface wettability and the adhesion of coatings to the substrate being treated. How much a material attracts a liquid can be expressed in terms of surface energy (measured as dynes per cm). Water has a high surface energy of 72 dynes/cm. When a water-based coating meets a low-energy material like polypropylene (PP) that has a surface energy of below 28 dynes/cm, the coating will not wet out and adhere to the surface. When the PP is treated with the plasma technology, its energy can be increased to over 72 dynes/cm, at which point the coating will wet it completely. The surface of the material can be visualized as Velcro™ tape with closed hooks. The ions and free electrons create hooks that make the surface more attractive to liquids, and consequently easier to wet (see Figure 2). Wettable materials can be painted more easily and without using organic solvents that are damaging to the environment.
The technology operates using electricity and compressed air. No vacuum or special gases are required. Because the technology generates plasma at atmospheric pressures with low power consumption and without the need for expensive process gases, it can be used in high throughput, in-line manufacturing operations.

Mobile Phone Housings
The finish on mobile phone housings imposes some of the highest demands in the finishing industry. Consumers demand a painted surface that is absolutely free of defects and imperfections. Conventional pretreatment processes often create electrostatic effects that can cause nearly invisible dust particles to adhere to the surface of the housing. These dust particles create an unsightly unevenness in the finish and a high number of rejects.
When notable suppliers to the mobile phone industry in South Korea installed atmospheric plasma pretreatment units for cleaning mobile phone housings in in-line processes, they experienced significant benefits. Immediately prior to painting, several rotating plasma generators efficiently clean the plastic surfaces. The users have been able to reduce their proportion of rejects from 12% to less than 5% using the plasma technology.
Vehicle Parts
A vehicle part typically experiences many passes through the painting process. A typical plastic vehicle part will have a primer-adhesion promoter, one to eight or more layers of base coat and finally a clear coat. Most manufacturers only have only one paint line and curing oven in a facility, and ovens have limited capacity. As a result, one part often must travel though the same oven four to nine or more times. Demand for particular vehicles, in addition to requirements for multiple paint layers, causes bottlenecks in the curing ovens. Any way a manufacturer can increase capacity without a significant capital expenditure, such as additional oven capacity, can provide substantial cost savings. One fewer pass through the painting process can reduce the cost of primer, associated labor and the burden of fixed costs for the oven.
By using the plasma pretreatment technology, the primer used for adhesion to the plastic part can be eliminated, thereby saving one trip though the oven for each part. One vehicle manufacturer has experienced a decrease in oven passes by 25% for most parts, as well as a significant increase in capacity. The manufacturer had considered other pretreatment processes, including corona chambers and flaming. However, the parts are typically conductive, thus preventing the use of a blown arc corona. The open flame process can cause thermal damage to the part and give rise to safety issues - problems that do not occur with atmospheric-pressure plasma.
Automobile Interiors
Switches with laser-etched symbols, high-gloss decorative strips and covers, scratch-resistant displays and glittering fascias, ventilator grilles or glove compartments - plastic parts in the interiors of high-end automobiles are often finished with expensive coats of paint. Companies such as BMW and Rolls Royce are using the atmospheric plasma pretreatment technology to improve bonding and achieve a first-class surface finish on these and other interior components.
Perfume Bottles
A perfume often is purchased not because of its fragrance but because of its “packaging” – that is, the bottle it comes in. Producers try to outdo one another every year with extraordinary new ideas. Consumers usually do not know that the clear blue, white, lilac or matte red or even two-tone glass safeguarding the stately bouquet is not colored glass but rather glass that has been painted in a costly process. Demands for an absolutely perfect surface are a sine qua non, so the most thorough cleaning of the material prior to the painting process is an inescapable obligation.
A German perfume bottle manufacturer, supplier to many exclusive brands in the world of perfumes, discovered the merits of the atmospheric plasma pretreatment technology last year. Trials resulted in such a substantial reduction in the reject rate that the company will soon install two systems in its manufacturing operation.
Editor’s note: The atmospheric plasma pretreatment technology was developed by Plasmatreat GmbH in Germany under the tradename Openair® Plasma. For more information about the technology, visit www.plasmatreat.com.

Pretreatment of a mobile phone housing with a rotating plasma jet. Image courtesy of Plasmatreat.
Design elements and immaculate surfaces are assuming an increasingly greater importance in today’s highly competitive markets. Whether on automotive components, mobile phone housings, perfume bottles or numerous other products, industry is spending exponentially rising sums to improve the appearance of products through enhanced finishing processes.
A decisive factor in finishing is achieving the best possible cleaning and activation of the surfaces to be coated. Pretreatment processes range from ionization or flame treatment to wet chemical processes, power washing, the use of primers and even mechanical cleaning with ostrich feathers. Despite all the efforts being made, the proportion of rejected parts in production caused by problems such as painting over dust particles is often well above 10%. Additionally, conventional pretreatment methods often create other challenges, such as static charging of surfaces or environmental pollution.
A new atmospheric plasma technology has been developed to eliminate these problems and improve the quality of the finish, thereby driving down the number of rejects. The technology can produce ultrafine cleaning and high activation on a wide range of surfaces, including plastics, metal and glass; these benefits, in turn, can promote the optimum adhesion of paints and coatings.
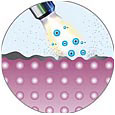
Figure 1. The ions and free electrons in the plasma beam break down contaminants. Organic compounds are oxidized and turned mostly to water and carbon dioxide. Image courtesy of Plasmatreat.
Plasma: The Fourth State of Matter
Most people are familiar with three states of matter - solid, liquid and gas. However, the most common state of matter in the universe is plasma. Plasma is a higher energy form of matter that makes up the sun and every object outside the solar system. While the energy found in solids, liquids and gases is largely carried in the form of kinetic energy or heat, the energy in plasma is also due to electrons being split from the atomic nucleus, which creates ions and free electrons. As a result, plasma can carry a lot of energy and is highly reactive.There are four commonly used plasma technologies. Vacuum plasma has generally been used for delicate applications and research, while flame treatment, corona and blown corona systems have been employed for less critical applications. All of these technologies typically have required particular conditions, including low pressure, extreme heat and/or high currents. The technology can be difficult to control precisely, and the high temperatures and voltages can be dangerous.
The new atmospheric plasma technology creates plasma in a jet through the action of a stepped, high-frequency, pulsed current that converts compressed air into a relatively low-temperature, voltage-free beam of plasma. The plasma beam is cool enough to blast a hole through a sheet of paper without catching it on fire.
In finishing applications, the plasma can be directed onto the material surface to remove static electricity and dust, as well as to vaporize contaminants, including waxes and silicone residues. Organic compounds are oxidized and turned mostly to water and carbon dioxide (see Figure 1).

Figure 2. A plastic surface will normally repel water, but water will wet the surface evenly when it is activated with plasma. Image courtesy of Plasmatreat.
The technology operates using electricity and compressed air. No vacuum or special gases are required. Because the technology generates plasma at atmospheric pressures with low power consumption and without the need for expensive process gases, it can be used in high throughput, in-line manufacturing operations.

The electrically neutral plasma beam allows optimum cleaning, high activation and thin coating of surfaces. Image courtesy of Plasmatreat.
Applications
The atmospheric plasma pretreatment technology is finding use in a variety of industries, including electronics, automotive and packaging.Mobile Phone Housings
The finish on mobile phone housings imposes some of the highest demands in the finishing industry. Consumers demand a painted surface that is absolutely free of defects and imperfections. Conventional pretreatment processes often create electrostatic effects that can cause nearly invisible dust particles to adhere to the surface of the housing. These dust particles create an unsightly unevenness in the finish and a high number of rejects.
When notable suppliers to the mobile phone industry in South Korea installed atmospheric plasma pretreatment units for cleaning mobile phone housings in in-line processes, they experienced significant benefits. Immediately prior to painting, several rotating plasma generators efficiently clean the plastic surfaces. The users have been able to reduce their proportion of rejects from 12% to less than 5% using the plasma technology.

By using the plasma pretreatment technology, the primer used to ensure coating adhesion to automotive plastic parts can be eliminated. Image courtesy of Plasmatreat.
A vehicle part typically experiences many passes through the painting process. A typical plastic vehicle part will have a primer-adhesion promoter, one to eight or more layers of base coat and finally a clear coat. Most manufacturers only have only one paint line and curing oven in a facility, and ovens have limited capacity. As a result, one part often must travel though the same oven four to nine or more times. Demand for particular vehicles, in addition to requirements for multiple paint layers, causes bottlenecks in the curing ovens. Any way a manufacturer can increase capacity without a significant capital expenditure, such as additional oven capacity, can provide substantial cost savings. One fewer pass through the painting process can reduce the cost of primer, associated labor and the burden of fixed costs for the oven.
By using the plasma pretreatment technology, the primer used for adhesion to the plastic part can be eliminated, thereby saving one trip though the oven for each part. One vehicle manufacturer has experienced a decrease in oven passes by 25% for most parts, as well as a significant increase in capacity. The manufacturer had considered other pretreatment processes, including corona chambers and flaming. However, the parts are typically conductive, thus preventing the use of a blown arc corona. The open flame process can cause thermal damage to the part and give rise to safety issues - problems that do not occur with atmospheric-pressure plasma.
Automobile Interiors
Switches with laser-etched symbols, high-gloss decorative strips and covers, scratch-resistant displays and glittering fascias, ventilator grilles or glove compartments - plastic parts in the interiors of high-end automobiles are often finished with expensive coats of paint. Companies such as BMW and Rolls Royce are using the atmospheric plasma pretreatment technology to improve bonding and achieve a first-class surface finish on these and other interior components.
Perfume Bottles
A perfume often is purchased not because of its fragrance but because of its “packaging” – that is, the bottle it comes in. Producers try to outdo one another every year with extraordinary new ideas. Consumers usually do not know that the clear blue, white, lilac or matte red or even two-tone glass safeguarding the stately bouquet is not colored glass but rather glass that has been painted in a costly process. Demands for an absolutely perfect surface are a sine qua non, so the most thorough cleaning of the material prior to the painting process is an inescapable obligation.
A German perfume bottle manufacturer, supplier to many exclusive brands in the world of perfumes, discovered the merits of the atmospheric plasma pretreatment technology last year. Trials resulted in such a substantial reduction in the reject rate that the company will soon install two systems in its manufacturing operation.
High-Performance Finishing
To remain profitable in today’s highly competitive markets, finishing professionals must continually innovate and improve the performance of their operations by enhancing the appearance and quality of their coatings, increasing throughput, lessening environmental impact and reducing material costs. Plasma pretreatment can play a vital role in achieving these goals.Editor’s note: The atmospheric plasma pretreatment technology was developed by Plasmatreat GmbH in Germany under the tradename Openair® Plasma. For more information about the technology, visit www.plasmatreat.com.
Links
Looking for a reprint of this article?
From high-res PDFs to custom plaques, order your copy today!