Resins and Curatives: The Binder System for Thermosetting Powder Coatings
Ideally, appearance and other properties of a powder coating should be equivalent to those of a liquid coating of the same thickness. However, the unique requirements of a thermosetting powder coating impose restrictions on the binder system (the resins and curatives), making this difficult to achieve.
While liquid paint and powder coatings are similar in many respects, the technology used to prepare them is markedly different:
- Liquid paints are prepared by dispersion of the solids in a resin solution in a mill. Powder coatings are prepared by dispersion of the solid ingredients in a molten resin in an extruder.
- Paint dispersions must be stabilized to prevent pigment agglomeration and settling. Flooding, floating and pigment agglomeration are not problems in powder coatings.
- Powders have only a short time after melting to coalesce and flow before cross-linking starts. Therefore, the melt viscosity, functionality and reaction rate of powder coatings must be carefully controlled.
Glass Transition Temperature
One of the most important characteristics of a powder coating is its glass transition temperature (Tg). In simple terms, this is the temperature at which solid polymeric materials start to soften and flow.A simple test to evaluate the sintering resistance of a powder is to immerse samples in a small container, place in an oven or waterbath at 45 to 60ºC for at least 24 hours and observe the degree of powder mobility after removal and cooling to room temperature. (See, for example, Recommended Procedure #1, "Accelerated Stability Test," published by The Powder Coating Institute.) Some powders will remain completely free-flowing, while others will sinter into a solid lump. Powders with a low Tg can also cause problems with "impact fusion," the buildup of solid deposits in powder delivery lines and venturis of the spray equipment.
The Tg of a powder coating is affected by all the resinous and polymeric ingredients present. In a TGIC-cured powder coating, for example, the Tg of the resin is depressed about 1ºC for each percent of TGIC present in the formulation. Therefore, in a typical powder coating with a resin that contains a TGIC ratio of 93:7, the Tg of the mixture will be reduced by about 7ºC, compared to the resin itself. This is the reason most resins have a higher Tg than absolutely necessary to prevent resin sintering and clumping.
It is generally agreed that the Tg of the binder resins used in thermosetting powders should be at least 50ºC, preferably higher. The Tg must be high enough to resist sintering and agglomeration during storage and shipping of the powder, but to promote maximum flow and leveling, the Tg and molecular weight of the binder system should be low. In solventborne coatings, on the other hand, the binder system often has a Tg below room temperature and is a liquid in some cases.
The formulator must be
aware of the Tg of additives and curatives and their effect on the Tg
of the total system. The necessity of maintaining an adequate Tg for
the formulated powder places constraints on both the resin manufacturer and the
formulator. The Tg of a powder coating can be easily measured by
differential scanning calorimeter (DSC) techniques.

Molecular Weight of the Binder Resins
The resins used in the preparation of powder coatings are comprised of a mixture of polymers of varying molecular weights. The molecular weight is usually measured by gel permeation chromatography (GPC), which involves the use of a thin metal column packed with a special gel having a specified volume and distribution of pore sizes. The resin is injected as a solvent solution and diffuses through the column. Larger and smaller molecules diffuse at different rates and are measured by special detectors (Figure 1). The numerical results are reported as Mn (number average), Mw (weight average) and Mz (z-average). Mw is indicative of the average molecular weight and is usually the value given when the molecular weight of a resin is reported. For powder coating resins, this is usually in the range of 1,500 to 15,000. Mechanical properties of the coating, such as flexibility and impact strength, are mostly dependent on the number average molecular weight, while viscosity is a function of the weight average molecular weight. The molecular-weight distribution, or polydispersity (Pd), is the ratio of the weight average and number average molecular weight:To maximize the physical properties and retain a low melt viscosity, the polydispersity should approach unity. Unfortunately, this is difficult to achieve. Present-day polyester resins, for example, have a polydispersity of about 2 (1).
The Tg of a
polymer rises with increasing molecular weight, leveling off at a high
molecular-weight value. Because of the relatively low molecular weight of
thermo-setting powder coating resins, the Tg is in a range that
changes rapidly with alterations in molecular weight. This means that a change
in the molecular weight of the resin can have a considerable influence on the Tg.
This is another reason to maintain as low a level of polydispersity as possible,
since the low-molecular-weight fraction depresses the Tg of the resin
and the higher-molecular-weight fraction results in high resin viscosity and
reduced flow of the coating.

Functionality of the Coating System
To form a three-dimensional, cross-linked polymeric network, the average functionality of the reactive components must be greater than 2. If the functionality is less than 2, no cross-linking can occur. If it is equal to 2, chain extension occurs, and higher-molecular-weight linear thermo-plastic coatings are formed.The ratio of reactive groups must be accurately controlled to reach a high molecular weight. In formulating powder coatings, the average functionality of the system is generally kept above 2.2. If one of the components has a functionality of only 2 (for example, Bis A epoxy resins), the other component should have a func- tionality of at least 2.4, preferably higher. Thus, the acid functional resins used in epoxy-polyester hybrid coatings have a functionality approaching 3, while similar resins for reaction with TGIC (functionality = 3) will have a functionality closer to 2.
Functionality (Fn), number
average molecular weight (Mn) and acid value (AV) in polyester resins are
interrelated variables:
Fn | = | Mn | = | AV | x | Mn |
Eq.Wt. | 56,100 |
This means that if the AV of the polyester resin is held constant (to maintain a constant epoxy/polyester ratio, for example) to increase the degree of functionality, the molecular weight must be increased. If the AV is reduced so a higher ratio of polyester to epoxy is required, the molecular weight must be increased to maintain the same degree of functionality. This is why hybrid polyester resins designed for curing with Bis A epoxy resins at a ratio of 60/40 or 70/30 normally have a higher melt viscosity than resins used at a 50/50 ratio.
In polyester resins, however, viscosity is also a function of the degree of condensation. Resins that are highly condensed (having a low acid number) have a higher viscosity. A similar relationship holds true in the case of hydroxyl-functional polyester resins. As the hydroxy value increases, the functionality increases proportionately. At higher OH values, the molecular weight must be decreased, or gelation would occur during resin manufacturing (Figure 2).
As the average functionality of the resin/curing agent system increases, the sensitivity of reactants to the stoichiometric ratio decreases. On the other hand, the higher the functionality, the faster the viscosity of the coating will increase during curing, resulting in less time for flow out. This may result in increased level of orange peel (2).
Therefore, a high degree of functionality in the coating system leads to a fast gel time, fast cure and poor flow of the coating. Conversely, a lower level of functionality yields a powder with a longer gel time, less reactivity and higher flow. The formulator must choose the resins and curing agents according to their ability to meet the specific requirements of reactivity (cure time), physical properties, shelf stability, smoothness, flow and ease of manufacturing (sensitivity to stoichiometry).
Unfortunately, most resin
manufacturers do not publish information about the functionality of their
products. The skilled formulator must "read between the lines" to get
a better sense of the functionality of the reactants, using clues such as
recommended application, resin viscosity, residual acid number or hydroxyl
value, etc. Formulating is a series of compromises between developing a product
with ideal properties and one that is functional, producible, sellable and
profitable.
Melt Viscosity
For maximum flow of a powder coating, the melt viscosity of the system should be as low as possible and the reactivity such that there is ample time for resin fusion and flow prior to a significant increase in viscosity as a result of cross-linking. In the case of polyester-urethanes, for example, where the curative is typically blocked with caprolactam, no cross-linking can occur until the unblocking temperature is reached and the isocyanate group is activated and available to react with the hydroxyl groups of the resin.The unblocking reaction usually starts about 160ºC, so there is a long period for the powder to flow before the viscosity starts to increase. In the case of TGIC-cured polyester powders, the cross-linking reaction starts very soon after the powder particles have melted. Therefore, very smooth and "wet look" coatings are possible with urethane polyesters but are more difficult to achieve with TGIC polyester powders.
Monomer composition
significantly affects melt viscosity and Tg as well (3). In
general, aromatic or cycloaliphatic monomers lead to a higher Tg in
the polymer, and longer-chain-length aliphatic monomers lead to a lower Tg.
Most polyester resins contain significant levels of terphthalic acid and some
isophthalic acid in the backbone. Low levels of adipic or other aliphatic acids
are used to tailor resin properties such as flow and flexibility, but high
levels can result in resins with too low a Tg. While increasing the
molecular weight results in a higher Tg, melt viscosity increases as
well.

In addition to reducing the degree of polydispersity of the resins, other techniques for reducing the melt viscosity of the coating system involve the use of semicrystalline resins or curing agents. In the case of polyesters, semicrystalline resins can be prepared using higher levels of even-numbered polyols and acids, such as 1,4-butanediol, 1,6-hexanediol, etc., together with terphthalic, adipic, azelaic and dodecanedioic acids. Properly designed semicrystalline resins are characterized by a sharp melting point and a very low melt viscosity. They have a heterogeneous morphology--in other words, they contain a mixture of phases and appear white in color and opaque at room temperature. They are seldom used alone but are usually combined with standard amorphous polyester resins (5). Semicrystalline resins are difficult to mix and disperse with amorphous resins because of their wide difference in melt viscosity. Special extrusion conditions are necessary to obtain a satisfactory mixture/dispersion of the two resins and even then there can be microphase heterogeneity. Other techniques for the preparation of powders based on semicrystalline resins are being investigated.
As previously noted, melt viscosity of polyester resins is influenced by the degree of polycondensation. Hydroxylterminated polyester resins used in urethane powder coatings are prepared by the polycondensation of multifunctional polyols and carboxylic acids. Because hydroxyl-functional polyesters are synthesized using an excess of hydroxyl groups, a very high percentage of carboxyl groups are consumed. In this case, the resin is almost completely hydroxyl end-capped and is referred to as a fully condensed resin. Fully condensed resins have very little unreacted acid present and are therefore characterized by a low acid number. A study carried out to determine the difference between fully condensed and less fully condensed resins (6) led to the following conclusions:
- Fully condensed resins have a higher melt viscosity.
- Fully condensed resins develop impact resistance more quickly.
- Less fully condensed resins have poor impact resistance when the sto ichiometry of the blocked-isocyanate curing agent is based only on the OH number.
- Less fully condensed resins show equivalent impact resistance compared with fully condensed resins when the stoichiometry of the curative is based on both the OH number and the acid number (the so-called reactive number).
While this study was done
on hydroxyl-functional resins, similar results would be expected for
carboxyl-functional resins. In this case, however, the degree of condensation is
more difficult to determine since both the acid number and hydroxyl number (the
total of unreacted end groups) are not reported. Other properties, such as resin
viscosity, can give an indication of the degree of condensation.

Lower viscosity and higher flow of the coating can also be influenced by the application conditions. The rate of heating has a significant influence, with faster heating rates giving a lower melt viscosity (Figure 3) (11). Note, however, that while the minimum viscosity occurs at the fastest heating rate, melt viscosity increases more rapidly after reaching the minimum. This would normally be the case for a part curing in a convection oven. The ideal situation would be to rapidly heat the substrate and melt the powder by infrared (IR) or induction heating and then complete the cure in a convection oven. IR curing of powders has come into widespread use in recent years (7).
Resin viscosity must also be taken into consideration in the melt-mixing process. A high resin viscosity at processing temperatures is necessary to promote maximum shear and optimum wetting and dispersion of the pigments, fillers and other ingredients. If the melt viscosity of the resin, as in the case of a semicrystalline resin, is too low, very little shear (dispersion) occurs in the extruder.
The importance of matching
resin viscosity with other resinous ingredients cannot be overemphasized. Poor
dispersion resulting in less than optimum development of physical properties can
easily result when using resins and curatives that differ significantly in melt
viscosity (8). Therefore, it is important that the formulator know the
relative melt viscosities of the various resinous ingredients so the proper
extrusion conditions and temperatures can be chosen.

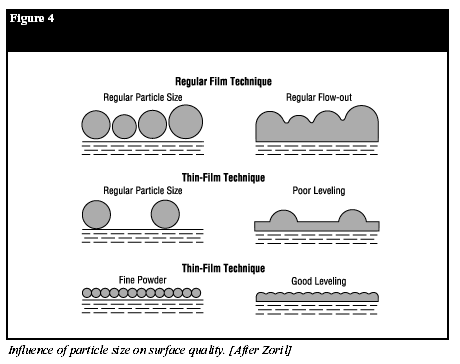
Film Formation
Film formation and leveling are fundamental aspects of the powder coating process. The major driving force causing flow and coalescence of powder particles is surface tension (9). The time required for two particles to flow together is a function of the viscosity, average radius of curvature and surface tension. Therefore, for a given surface tension, the time to flow out decreases directly with a lower melt viscosity and a smaller particle diameter (Figure 4) (10). After particle coalescence, flow/leveling is promoted by:- low melt viscosity
- high surface tension
- higher film thickness
- small wavelength of unevenness (12).


Particle Size
The importance of particle size in film formation, especially in the case of thin films, has been recognized for many years. A finer particle size is necessary to obtain thinner films. A rule of thumb is that the largest particles present in the powder should be no larger than about two times the film thickness desired. For a 25-µm (l-mil) film, the powder should contain particles no larger than 45 µm (325 mesh = 44 µm). However, greater amounts of superfine particles (those less than 8 to 10 µm) are normally generated during grinding to produce a finer-particle-size powder.Superfine particles cause many difficulties during application by electrostatic spraying and other coating methods. Most powder coating manufacturers have tried to avoid the generation of high levels of superfines by making a coarser-grind powder. But there are many applications where thinner films are required. Consider Figure 4. While this is, perhaps, an over-simplification, it illustrates the importance of a finer particle size in developing good leveling and smoothness of the powder coating. The particle shape is also important (Figure 7) (10). For thin-film application, the ideal powder should be spherical or rounded, without sharp edges, possess a fine average particle size and a narrow particle-size distribution.
The powder coating industry has matured to the point where many applicators, as well as the powder and equipment suppliers, are aware of the importance of particle size and distribution on application characteristics and the ability to provide thin coatings with superior smoothness. The Low Emissions Paint Consortium (LEPC), a joint effort by DaimlerChrysler, General Motors and Ford to develop a commercially viable powder clearcoat line for the automotive industry, has confirmed the importance of particle-size control on process uniformity and maintaining a smooth coating at a low film thickness (15). This topic has been addressed in the literature and recent technical/industrial conferences (14-18).
Several new processes are
being developed to produce finer-particle-size powders with a more narrow
particle-size distribution. Currently, however, the only commercially viable
method to accomplish this is by grinding the powder more finely and removing the
fines by air
classification.
Unfortunately, it is quite
difficult to reuse the fine powder separated by air classification, and it is
usually discarded. Air classification to obtain a narrow particle distribution
is both expensive and wasteful.

Stoichiometry
As mentioned previously, the ratio of reactive groups between resin and curative, or co-reacting resins, is important in achieving the desired molecular weight and degree of cross-link density. Physical properties, such as flexibility, tensile strength and impact strength, are largely dependent on these characteristics. In most cases, a 1:1 stoichiometric ratio between reactive groups produces a coating with optimum physical properties. In formulating powder coatings, it is best to start at a 1:1 ratio and then make changes to explore the effect of stoichiometry. In some cases, as in the example of the catalytic curing of epoxy resins with tertiary nitrogen compounds or dicyandiamide, no exact stoichiometry is involved, so the ratio of resin and curative must be determined empirically.When curing very high
hydroxyl number (>100) polyesters with a blocked isocyanate or uretdione
curative, usually only 60 to 80% of the stoichiometric level is required. The
polyester resin is so highly functional (Figure 2) that gelling occurs,
with resulting molecular immobility before all the hydroxyl groups have a chance
to react.
References
1. Maetens, D., "Influence of the Binder on Durability of Powder Coating," paper presented at Powder Coating '96 Formulation & Production Conference, 105-115, 19962. Misev, T.A. and Belder, E., Journal of Oil Colour Chemists Association, 72, (9), 1989
3. Johnson, L.K. and Sade, W.T., Journal of Coatings Technology, 65, (826), 1993
4. Chang, M.Y.H., "Polyester Resin and Powder Coatings," Paint & Coatings Industry, XV, (10), 98-108, 1999
5. O'Keeffe, L. et al, PCT WO 91/14745, 1991
6. Wu, B., Padaki, S. and Maetens, D. "The Effect of Acid Groups of Hydroxyl-Functional Resins on the Properties of Polyester-Urethane Powder Coatings," paper presented at the 26th International Waterborne, High-Solids and Powder Coatings Symposium, New Orleans, February 1999
7. Canfield, D.M., Powder Coating, 7, (7), 41, July 1996
8. Hammerton, D., "The Effect of Processing Conditions on Powder Coating Performance," paper presented at Powder Coating '96 Formulation & Production Conference, 75, The Powder Coating Institute, 1996
9. Nix, V.G. and Dodge, J.S., Journal of Paint. Technology, 45, (586), 1973
10. Zoril, U., Polymer, Paint Colour J., 179 (4241) July 12, 1989
11. Gabriel, S., Journal of Oil Colour Chemists Association, 58, 52-61, 1975
12. DeLange, P.G., Journal of Coatings Technology, 56, (717), 1984
13. Stachowiak, S.A. et al, Organic Coat. Sci. and Technol., 5, 67 Marcal Dekker Inc., 1983
14. Richart, D.S., paper presented at the Waterborne, High-Solids and Powder Coatings Symposium, New Orleans, 1995
15. Messerly, E.R. and Lis, K., Powder Coating, 6, (3), 45, June 1995
16. Lader, H.J., paper presented at Powder Coating '94, 253, Cincinnati, 1994
17. Kenney, J. C. et al, Journal of Coatings, Technology, 68, (885), 35-43, 1996
18. Horinka, P.H., Industrial Paint & Powder, 71, (12), 26-29, December 1995
Looking for a reprint of this article?
From high-res PDFs to custom plaques, order your copy today!