Understanding Benzoin in Powder Coatings
Use of powder coatings is growing rapidly. However, surface defects such as orange peel and pinholing prevent the expansion of powder coatings into some markets. For the prevention of pinholes due to degassing, benzoin has been the favorite material because of its high efficiency and low cost. In fact, benzoin is used in virtually all powder coating systems worldwide. The prospect of developing an improved air-release agent has stimulated research on benzoin's role in degassing in powder coatings. In some cases, alternative air-release agents have been developed, but these alternatives generally fall short either in performance or in terms of economics.

Background
Over the years, a number of patent applications on benzoin substitutes have been filed. For example, an application filed in 1976 by Jiro Yoshikawa at Nippon Paint Co. claims a number of compounds, including bisphenol A, phenyl acetylsalicylate and benzoin, that prevent foaming in epoxy-based powder coatings (2).In 1992, Jan Schippers at DSM filed a patent application claiming that crystalline waxes could be used to prevent pinholes without yellowing in Primid-based systems (3). This application claims that some crystalline waxes will prevent pinholes while avoiding the yellowing seen during curing in Primid systems with benzoin, especially under overbake conditions. Also in 1992, a patent by Stanislaw Skora claims a bisphenoxy propanol compound that can completely prevent pinholes in thermosetting powders when used at levels of 0.5 to 3% by weight (4). In a paper presented at the Waterborne, Higher-Solids and Powder Coating Symposium in 1993, William Arendt of Velsicol claims that 1,4-cyclohexane dimethanol dibenzoate (CHDM Dibenzoate) gave excellent coatings with less yellowing at levels three to nine times higher than that of benzoin in epoxy-hybrid systems (5). In a European patent application filed in 1993, Wilkinson and Phillips claim a solid thermoplastic polymer can be used in place of benzoin in Primid-based powder coatings to give superior color. The use of these solid thermoplastic degassing agents in other powder systems is mentioned with statement to the effect that differences in color are noted in other systems. This application is the first to attempt to explain how degassing or air-release agents work. The authors claim degassing agents have a surface tension effect that "holds the surface open" during cure (6). However, no data is offered to support the claim.
In the past decade, there have been several studies to learn the mechanism of air release. For example, Randoux, et.al., showed that benzoin and benzil, a bright yellow oxidation product of benzoin, are evolved from the coating during cure in a variety of powder coating systems (7). Uhlmann reported that benzoin reduces wetting tension in epoxy systems while having a slight effect on melt viscosity and Tg (8). Uhlmann also reports that a high MW butyl acrylate flow modifier is more efficient than benzoin in reducing wetting tension. Furthermore, benzoin provided no additional reduction of wetting tension when used with a flow modifier. The fact that benzoin does not add to the effect of the flow modifier on wetting tension suggests that wetting tension is not a major factor in air release. The presence of benzil as an impurity in benzoin is often cited as the source of the yellowness found in powders formulated with benzoin. Uhlmann suggests that the amount of benzil in benzoin is important because benzil has a significant influence on the effect of benzoin during film formation. He also states that it is important for manufacturers to realize that storage conditions for benzoin may affect the benzil content and thus affect the air-releasing properties of the benzoin. It is also stated that the quality of the coating is dependent on the fact that benzil can leave the coating while benzoin remains in it. This statement contradicts the work of Randoux cited above.
While significant attempts had been made to determine how benzoin promotes gas release and prevents pinhole formation during powder coating curing, no clear picture emerges as to why benzoin is so effective. In addition, no cost-effective replacements for benzoin have been forthcoming in the last 25 years of powder coating development. Clearly, a better understanding of how benzoin works might help to develop a new generation of gas-release agents that do not yellow during cure. This paper describes our work to develop such an understanding.

The Experiment
Initially, the work focused on the effect of benzoin on the rheology and cure profile of the coating. A clear epoxy system was selected as a good model for these studies (Table I). Samples containing varying amounts of benzoin were subjected to dynamic mechanical analysis (DMA), gel-time determination, inclined plate flow, TGA, photoacoustic IR, attenuated total reflectance (ATR) IR and headspace GC analysis.
The gel-time test was repeated in an epoxy-hybrid system (Table 1) and a polyester/blocked-isocyanate system to determine if the effects seen in the epoxy system were reproduced in other cure systems.
Typical powder formulation conditions were as follows: The components were mixed on a roll mill in 0.5-gallon jars for one to two hours. The mixed components were then extruded on a Buss PCS-30 single-screw extruder at 300 rpm. The extrusion temperatures were 100ºC for the epoxy and epoxy-hybrid systems and 130ºC for the polyester/blocked-isocyanate system. The extruded samples were pulverized on a Retsch ZM-1 hammer mill to pass a 0.5-mm sieve. The ground powder was then passed through a 200-mesh screen before spraying using a Gema PG-1 corona spray gun on either Q-Panel 0.025- by 3- by 6-inch aluminum or 0.025- by 3- by 6-inch steel panels. The panels were cured for 10 to 15 minutes at 180ºC for the epoxy and epoxy-hybrid samples and for 15 minutes at 204ºC for the polyester/blocked-isocyanate system.
Results and Discussion
Rheology and Cure Rate. Benzoin is known to lower the melt viscosity and the surface tension of powder coatings (8,9). Benzoin's effect on melt viscosity was seen in our studies as well (Figure 1). However, the magnitude of the viscosity change is small and is negligible at the low concentrations of benzoin used in commercial practice. The reduction of the surface tension of the coatings alone cannot account for benzoin's effectiveness as an air release agent because other additives are more effective at reducing surface tension but are less effective as air-release agents. For example, flow modifiers are very effective at reducing surface tension but are not very effective at reducing pinholes.
Volatiles. Another possible explanation for benzoin's effectiveness is its volatility, i.e. it rapidly migrates to the surface of the coating and vaporizes carrying along other volatiles with it. Benzoin would, in effect, open a path for other volatiles, increasing the flux of gas leaving the coating. In support of this theory, it has been shown that benzoin sublimes from coatings during cure (7). However, it is not known how much of the benzoin leaves the coating or when the exodus occurs during the curing process.
To quantify the amount of benzoin that leaves the coating during cure, a series of samples containing varying amounts of benzoin were subjected to headspace gas chromatography (GC) analysis. For this test, a known quantity of clear epoxy powder was weighed into a sealed sample vial that was then heated to 180ºC for 15 minutes to simulate a cure. The headspace of the sample container was then sampled and subjected to GC/MS to determine the amount and composition of the volatiles evolved.
The results of this study are surprising. It was expected that benzoin would be seen in substantial quantities, perhaps as high as 50% of the benzoin in the coating. Instead, it was found only in a minute amount in the sample containing 5 weight-percent benzoin. Both benzaldehyde and benzoic acid were found in the headspace, but at levels that indicate that the majority of benzoin stays in the coating. There are reasons to doubt this conclusion. First, the coating in the vial is very thick for a powder coating (ca. 5 mm). As a result, diffusion of benzoin to the surface would take substantially longer than in a typical coating of 70 mm. Another reason is that the photoacoustic IR spectrum of a cured panel could not find any trace of benzoin in the coating and the TGA/MS analysis of the coatings reveals that benzoin does indeed leave the coating.
Benzoin in the Coating. Photoacoustic IR was used to scan cured panels that had been sprayed with epoxy powder paint containing 0, 0.5, 1.2 and 5 weight-percent benzoin. An authentic sample of benzoin was used for a reference spectrum. Comparison of all four samples at 200 Hz shows none of the distinct benzoin bands, even in the sample containing 5 weight-percent benzoin. There appears to be no detectable amount of benzoin in these cured panels. This result conflicts with the headspace GC results. In order to resolve this conflict, additional testing was carried out.
Dynamics of Benzoin. Thus far, the testing has primarily looked at coatings after the cure is complete. If the benzoin does sublime, oxidize or degrade, it is a dynamic process that starts as the coating melts and coalesces and ends upon complete gelation of the coating or when all of the benzoin has been consumed or vaporized. In an attempt to look at the dynamics of the curing process, panels were sprayed with the epoxy clearcoat formulation containing either 0, 0.5 or 1.0 weight-percent benzoin. These panels were then cured at two-minute intervals from two to 14 minutes at 180ºC. The resulting panels were analyzed by ATR IR (Figure 2) and Photoacoustic IR (Figure 3). The results indicate that benzoin disappears rapidly during cure. In Figure 2, a significant peak is seen at 1559 cm-1, which diminishes quickly. By eight minutes, there are no longer traces of the benzoin absorbances. A depth analysis indicates that benzoin is concentrated near the surface (Figure 3). The curve at 800 Hz is essentially on top of the curve at 400 Hz in the region of the benzoin absorbance at 1559 cm-1. While not conclusive, this work suggests that benzoin migrates to the surface and then disappears during the first six to eight minutes of cure.
Thermal Gravimetric Analysis/Mass Spectroscopy (TGA/MS). To quantify the amount of benzoin and other volatile components that leave the coating, TGA/MS was performed on samples containing different levels of benzoin. The TGA/MS was able to track volatiles evolving from the coating and identify them. Originally, all samples were thermally scanned from 50 to 300ºC at 20ºC per minute. By this technique, it was seen that between 150 and 250ºC, the only volatiles seen in the control containing 0% benzoin were decomposition products of the amine curing agent for the epoxy coating. In the samples containing benzoin, mass loss attributable to benzoin (mass peaks at 105 and 77) were found. Furthermore, the mass loss attributable to benzoin occurred between 180 to 250ºC, which is within the powder curing-temperature range.
In each case, it was benzil, not benzoin, that evolved from the coating. Further examination of the equipment set up suggests that the benzil results from oxidation of benzoin in the transfer tubing after it leaves the coating. This was confirmed by evaluating the volatiles from direct insertion of the coating sample into a mass spectrometer. Upon direct insertion, one sees benzoin in the volatile stream. As a result of this finding, it is not possible to determine if benzoin is oxidized to benzil in the coating.
Unfortunately, the amount of mass lost as benzoin or benzil could not be precisely measured due to the small amounts involved. In samples containing 5% benzoin, it appeared that about half of the benzoin left the coating, but this needs to be confirmed by another study.
To determine when the benzoin evolves from the coating, an isothermal experiment was conducted. A sample containing 5% benzoin was rapidly heated to 190ºC over a four-minute period and then held at 190ºC. Mass loss started as the temperature reached approximately 125ºC and proceeded rapidly. The benzil (attributed to benzoin) evolved over a six- or seven-minute period. This result agrees very well with the finding from the photoacoustic and ATR IR studies reported earlier that benzoin disappears from the coating during the first six to eight minutes of cure.
Optical Microscopy. While trying to determine what was happening to benzoin in the coating, we also wanted to find out what was happening to the coating itself. A method was developed to examine a powder coating as it cured on a hot-stage microscope. Thin glass slides were sputter-coated with a thin layer of Pd/Au metal to provide a conductive surface that was optically transparent (20-Å thick). These slides were then sprayed with a clear epoxy powder using an electrostatic spray gun. The resulting powder coated slides were inserted into a hot-stage microscope oven and heated to 200ºC as quickly as possible. The curing of the coating was recorded on videotape as a function of time. These videos dramatically show the effect of benzoin on the air, water vapor and other volatiles trapped in the melting coating. The still photos (Series 1,2,3) illustrate the important points:


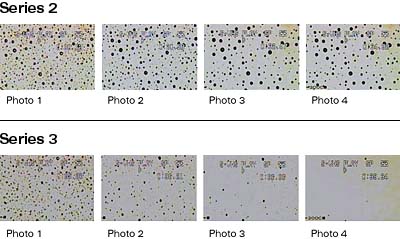
The epoxy clearcoat with 0.5% benzoin added in Series 3 shows a dramatic difference. Initially in photo 1, the scene is much the same as in Series 2. However, it is apparent in photos 2, 3 and 4 that the bubbles shrink and disappear rapidly over the course of roughly four minutes. The circles are included to help compare individual bubbles to see the shrinkage. Note that by photo 4, virtually all of the gas has escaped from the coating containing benzoin.
Conclusion
This work has clearly shown that benzoin escapes from the coating in the first six to eight minutes of cure, and during that same period of time, the gases trapped in the coating during melting and coalescence also escape. This finding, more than any other, offers the first real glimpse of benzoin's mode of action. While benzoin has been shown to affect the rheology, surface energy and cure response of powder coating systems, none of these factors alone could explain its unique effectiveness. However, the volatility of benzoin, perhaps in combination with those effects, provides the opportunity for the gases to escape. The release of the gases from the coating is a function of the coatings permeability. The bubbles do not rise to the surface and burst. Instead, they shrink as the gases inside diffuse and/or dissolve in the coating matrix. The benzoin facilitates this process by increasing the permeability of the coating. Whether benzoin increases the solubility of the gases in the coating or increases the diffusion constant of the gases through the coating or both has not been determined. However, it is believed that, due to its volatility, benzoin increases the free volume in the coating. As the benzoin leaves the coating, this free volume provides a path for the diffusion of the trapped gases through the coating. Without the benefit of benzoin, the diffusion of the gases through the coating is too slow, and the gases are trapped as the coating cures.Looking for a reprint of this article?
From high-res PDFs to custom plaques, order your copy today!