Waterborne UV Technologies
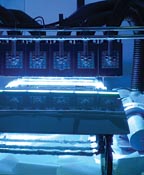
One of the environmental considerations is maximum achievable control technology (MACT), which is an EPA initiative aimed at the emission of HAPs. UV technologies are in compliance with-or technically exempt from-the MACT rules because HAPS (generally certain solvents) are not used in UV formulations, so HAPs emissions from UV formulations are zero. But there are other areas of current focus. One of these is "balance."
The U.S. government, under the current administration, is looking to balance, or rationalize, environmental regulations so that they make sense from both an environmental and an economic standpoint. This approach implies that cleanup and efficiency may be mutually exclusive.
UV technology, however, is a "pollution prevention" technology-a perfect example of how you do not have to compromise efficiency to clean up. Pollution prevention technologies actually make a process more productive, in some cases having the potential to dramatically improve the bottom line. Rather than clean up or be efficient, pollution prevention allows companies to have it both ways.
Another focus is on other types of emissions above and beyond VOC emissions. When VOC emissions are reduced through some technologies, the result may be to the neglect or actual creation of certain other emissions that have the potential to be problematic. UV technologies also score well on this front because they are basically complete low-emission packages with little to no emissions of substances such as NOx, SOx, or C02. C02, in particular, while not currently regulated, is receiving global attention, with programs in the works at the state and federal levels in the U.S. to begin at least monitoring emissions.
Other advantages
But in addition to their environmental advantages, UV coatings offer many other very practical benefits. For example, much has been written about the lack of skilled labor and the poor education and training of our workforce. In many cases, this makes UV an attractive option for firms not able to hire or train sufficient skilled help. UV coating is typically an automated process, with little or no tweaking necessary.An Internet article by Industry Week defined the characteristics of "world class" manufacturers with traits strikingly similar to the benefits that UV technology offers manufacturers:
- Use of automated processes
- Shortening of lead times
- Reduced scrap, waste and rework

Growth rates for UV technologies
During RadTech conferences, held every two years, surveys regarding usage of various product formulations are taken. Before 1999, the UV industry recorded double-digit or high single-digit growth for several years in a row. Of course, looking strictly at growth rates is partly a numbers game, because areas which had registered high growth as UV began to penetrate the industry typically experienced moderated growth as the application matured and the use of UV became more commonplace.In markets where UV is dominant, growth rates are tied to how the final product fares in the market. For example, the use of UV formulations for premium no-wax flooring is inextricably tied to consumer demand for no-wax flooring. While the diversity of the UV industry seems to assure the potential of double-digit growth in many emerging applications, these areas are typically small and don't contribute as much initially to the overall industry usage figures. Emerging applications with the potential for continued high growth include ink jet, powder, adhesives, automotive and plastics.
During the two-year period ending in 2001, many economic sectors had begun to see a downturn, leading up to September 11, when the U.S. economy fell into a full recession, with manufacturing hit particularly hard. Consistent with that trend, the UV industry moderated over the same period, with survey results showing UV- and EB-formulated product usage growing 8% overall, to just under 77,000 metric tons.
Looking ahead, RadTech survey respondents were optimistic about the next three years, with the potential for growth in new applications combined with recovery in other sectors as the driving-forces.
Wood-Wood accounts for about 20% of UV formulations by weight. In wood applications, "fillers" are the biggest areas, as UV is the technology of choice for medium density fiberboard (MDF) and particleboard processes, and account for the bulk of these operations. All areas of wood continue to grow. Clear finishes are the second-largest wood area by weight, representing nearly one-third of UV usage for wood. Though from smaller base-usage levels, stains and sealers and prefinished flooring continue to show above-average growth rates. Pigmented coatings for wood also show above-average growth.
Wood is one industry, among others, where UV is a good choice not only for production speed and environmental reasons, but because the equipment itself is generally now cost-competitive with other systems, such as waterborne coatings.
Plastics-At around 10%, plastics is still a small, but fast-growing, application area for UV. Survey respondents forecast the sector as having the best possibility of being the next UV application gaining widespread use over the next five years. Currently, the biggest plastics category, however, is for vinyl flooring, where UV holds a significant share, and much of the growth depends on consumer demand rather than further penetration. Other plastics categories showing higher growth rates include automotive headlamps, interior trim and other plastic products.
Metal-Can coatings and decoration continue to be the largest metal-substrate users of UV. While still fairly small, overprint varnishes and can end varnishes showed above-average growth. Several survey respondents indicated that the use of UV for tubing and pipe was expected to grow sharply over the next few years, with growth over the survey period (again, from a relatively low base) of about 50%. Similar high growth rates, again from relatively small bases, are expected for nameplates.
Motivation for using UV technology
UV users were asked to prioritize their key motivations for using the technology. Speed is the number-one answer, cited for its contributions to improved productivity, lower costs and its ultimate effect of raising manufacturing capacity. Environmental compliance used to be the prime motivator for using the technology but, while still important, ranked lower in the most recent survey. Respondents stressed that the use of UV is based on business decisions related to profitability and value, and because in many cases it offers a performance advantage.Respondents ranked their reasons for using UV technology in the following order:
- Increased speed (improved productivity and lower costs)
- Improved properties
- Environmental compliance
- Enabling technology
- Cost effective
- Reduced space
When reviewing the most important limitations to adopting UV technology, most revolve around a basic theme: The industry still has a big job to do in educating potential customers about the technology. Overcoming these barriers requires better education about capital equipment cost justification for the process; about the need to look at applied costs rather than just cost per gallon or pound (for formulations); and about the health and safety characteristics of UV and EB, which generally compare favorably with traditional processes.
Acrylates continue to account for the bulk-about 85%-of the chemistries, with some growth in cationic, which accounts for 6 to 8% of the total. UV continues as the dominant technology, with most survey respondents indicating the distribution to be 90 to 95% UV and 5 to 10% EB. However, in contrast to past surveys, more people are indicating that the EB share is increasing. The geographic distribution of total usage in North America registered a small change, with shares by Canada and Mexico each up. Canada has an 8% market share; Mexico, 4%; and the United States, 88%.

UV chemistries
The radiation-curing process is based on two chemistries: the radical polymerization of unsaturated oligomers (mainly acrylate functionalized) and the cationic polymerization reaction of cycloaliphatic epoxides and vinyl ether. Typical liquid radiation-curing formulations are composed of oligomers, reactive diluents, photoinitiators and additives, the general performance of the final coating mainly influenced by the oligomers. The oligomers are characterized by a relatively low molecular weight (between 500 and 5,000 daltons) and are based on different types of backbones: epoxyacrylates, urethane acrylates, polyester acrylates, acrylic acrylates and cycloaliphatic epoxides. This variety of chemical structures offers a wide range of properties and applications and gives a high degree of freedom to the formulator to meet target performances.Epoxy acrylates are mainly based on bisphenol-A derivatives. They generally give a fast cure response and provide hard coatings characterized by high solvent resistance and high gloss. Recent developments mean that more-flexible products and also aliphatic versions, or nonyellowing formulations, are now available.
Urethane acrylates represent a wide range of products in terms of structures, functionality and molecular weights, mainly due to the variety of available raw materials that can be used to build them up. This results in a wide range of mechanical properties after curing, from very flexible to hard and brittle materials. They are generally considered the highest-performing oligomers.
Polyester acrylates have, like urethane acrylates, a versatile chemistry. A variety of products is therefore available, covering a wide range of functionality, molecular weights and viscosities. They are mostly used where high reactivity is required, such as for printing inks. Their performances are mostly between those of epoxy acrylates and urethane acrylates.
Acrylic acrylates are used only in very particular applications at this time, mainly for adhesion as a primer onto difficult supports. Today, only a few cycloaliphatic epoxides for cationic cure are commercially available. The main benefits of this technology are a good balance of elasticity and film hardness, plus excellent adhesion to difficult substrates, such as metal and polyolefins, and improved barrier properties.
A common point among the different families of oligomers is the relatively high viscosity. This can be adjusted by adding reactive diluents to meet the requirements of the final application. The reactive diluents also influence, to a certain extent, the performance of the cured films, depending on their concentration, structure and functionality. They generally have a detrimental effect on the general performance of the oligomers, but they can help to control surface properties and properties such as flexibility and adhesion.
Due to the highly viscous nature of the resins, a main application method of UV liquid formulations is the roller coater. However, there is a trend toward the development of binders with lower viscosity, enabling the use of other coating techniques. This opens up the possibility of UV liquid coatings for 3-D objects.
Acrylate-based UV liquid formulations are characterized by a relatively low unsaturation equivalent weight, resulting, after cure, in a material with a high crosslinking density. This accounts for some outstanding properties, such as solvent, water and stain resistance. The main drawbacks are shrinkage and loss of flexibility and adhesion on difficult substrates.
Along with resin developments, a lot of progress has been made in the photoinitiator field and with curing equipment. The market for photoinitiators with an absorption spectrum shifted to the visible light, and the introduction of high-intensity lamps and doped lamps are two trends that have largely contributed to the use of radiation curing in pigmented systems.

Waterborne UV dispersions
Acrylics and polyurethanes are established high-performance resins, particularly in solventborne coatings. Increasing environmental pressure and the need to move to nonpolluting alternatives has led some companies to develop UV-curable waterborne dispersions.In these formulations, some of the typical advantages of radiation curing, like low energy requirements, high transformation speed and low space requirements, are lost. But the loss is balanced by a series of new, unique features, such as better film-thickness control compared to 100%-solids systems, no monomers that cause skin irritation, and a higher level of chemical resistance and physical properties than conventional and self-crosslinking water dispersions.
In these formulations, water is used to reduce the viscosity instead of reactive diluents or solvents, a strong advantage environmentally. Spray application of UV water dispersions makes it possible to apply lower coating weights. This technology allows the synthesis of high Tg oligomers, which are physically dry after water evaporation and particle coalescence. This characteristic eliminates problems encountered with tack and dust contamination on the uncured panels.
Also, the minimum film-formation temperatures of these systems are far below room temperature, this property being very peculiar for waterborne polymer dispersions that become very hard and resistant after the crosslinking process. The potential to easily dissociate the physicochemical properties before, after and during curing is particularly advantageous. For example, it is possible to have hydrophilic oligomers before crosslinking that subsequently lose any water sensitivity after curing.
Another advantage of waterborne products is that, in general, they are easy to matte. The combination of low viscosity, low gloss and high chemical or stain resistance is very difficult to obtain with 100% UV but is accessible with UV water dispersion. In addition, the polymer matrix is characterized by a lower crosslinking density (low acrylate concentration) and a higher molecular weight between crosslinks, resulting in the formation of domains of hard and soft segments.
This lower acrylate concentration makes for easier curing and makes a UV pigmented system more practical as a result. The acrylate crosslinks and the hard domains give the structure its body and hardness, while the softer domains serve as buffer zones and account for flexibility and impact resistance.
This unique combination of mechanical properties is also not currently attainable with 100%-UV systems. UV water systems are polymer dispersions with comparatively high molecular weights. This oligomer nature and the presence of water as the sole dispersing medium allow the synthesis of products without any irritant character, which is particularly valuable from a human health perspective. The most advanced products associate this property with the absence of solvents or amines (no "volatile organic content").
UV water dispersions can be of interest to all industrial coating markets where high performance is required and where the waterborne nature of the product is appreciated. Typical uses for Sherwin-Williams' Water Re-ducible Ultra-Cure are on wood office furniture, kitchen cabinets and architectural millwork. Future applications could include metal, concrete and plastics.
There is no doubt that radiation-curable water dispersions offer a unique set of possibilities associated with a very broad range of chemical structures with specific properties. Moreover, these products are at the interface between different chemistries and technologies, and are in essence excellent candidates for innovative, high-performance products with an environmentally friendly nature.
Looking for a reprint of this article?
From high-res PDFs to custom plaques, order your copy today!