Green Manufacturing Practices in America Can Help Profits, Will Help Planet
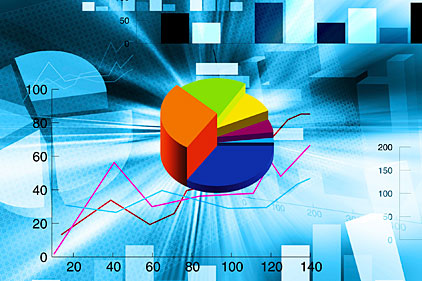
It’s quite apparent that more and more manufacturers understand the value of sustainability initiatives.
It’s a perfect storm – but a positive one. Two strong forces today are converging in the U.S. manufacturing sector that can deliver a whirlwind of benefits for those companies – and the environment. First, at long last, American industrial executives are recognizing the importance of preserving and enhancing the use of our precious natural resources through green energy practices in a vast array of manufacturing applications. Second, it’s now apparent to most manufacturers that this altruistic perspective, unlike many, can positively impact bottom lines and deliver cost-saving benefits short term and long term.
A new study of manufacturing professionals confirms this perspective. When asked by IFS North America what’s driving their companies to adopt and implement green initiatives, “it’s a management directive” shared top billing, cited by 54 percent of respondents. “It’s a social responsibility” also was cited by 54 percent of the manufacturers, followed closely by “customers are demanding it” (50 percent).
In addition, a 2011 study by the Material Handling Industry of America (MHIA) revealed a whopping nine in 10 executives surveyed say their companies believe that sustainable initiatives have the potential to both save money and resources.
The U.S. manufacturing sector can play a significant role in meeting the energy demand challenge. According to The Manufacturing Institute and the U.S. Department of Labor, the industrial sector accounts for nearly one-third (31 percent) of total end-user consumption in the United States, even surpassing transportation (28 percent). Residential (22 percent) and commercial (19 percent) rank third and fourth. Thus, green practices employed by manufacturers will impact a large percentage of energy use.
Greener, more energy-efficient manufacturing environments represent the ultimate win-win. A recent study by Aberdeen Group on sustainability initiatives conducted by more than 200 companies, many of them in manufacturing, illustrates the benefits of green manufacturing practices. Those deemed “best in class” achieved an impressive 9 percent reduction in carbon footprint while cutting energy costs 6 percent, facilities costs by 7 percent, paper costs by 10 percent and transportation/logistics costs by 7 percent.
And, this movement transcends politics. Both sides of the political spectrum have addressed the energy challenges the United States and the world face. As noted in his new book, Make It in America, Andrew Liveris, chairman and CEO of Dow Chemical, writes, “Energy, clearly, is one of the megatrends defining this century. It is only going to grow in importance as global demand increases.”
Admittedly, China is not a democracy and can mandate initiatives America likely would not. Yet, it’s difficult to dispute that China has made the greatest strides globally in instituting renewable, environmentally friendly energy initiatives.
Perhaps a more “apples to apples” example is Germany, a mature western European economy. Initially fueled in part by passage of its Renewable Energies Act in 2000, which paid any company or individual who sold back renewable energy to the grid, Germany quickly achieved rather ambitious goals. In 2000, the government set an objective to generate 12.5 percent of its electricity from renewable sources by 2012; it attained that level five years early. A new goal to achieve a 20 percent level by 2020 likely will be achieved in 2011, according to Liveris. In addition, the surging number of Germans employed in the renewable energy sector would make other countries green with envy.
New Government Programs Are Green Catalysts
Countries such as China and Germany have achieved such dramatic success in the industrial green arena due, in great part, to the substantial national programs that make energy efficiency commitments easier and financially rewarding within their borders. Many U.S. pundits voice frustration with America’s lack of any comparable national policies. That issue will not be debated here.
But what can be stated with certainty is the existence of a number of new “assistance” programs established by government agencies to help manufacturers create sustainable programs. One growing in popularity is the Green Suppliers Network established by the U.S. Environmental Protection Agency (EPA) in collaboration with the U.S. Department of Commerce. Its mission is to help small and medium-sized manufacturers stay competitive and profitable while reducing their impact on the environment.
This is accomplished via the network’s “Lean and Clean Advantage.” The program works with large manufacturers to engage their suppliers in low-cost technical reviews to identity strategies to improve process lines, use materials more efficiently and eliminate the root causes of waste.
Of course, there is a host of U.S. Department of Energy (DOE) initiatives. For example, the department offers the Industrial Technologies Program Save Energy Now that aims to drive a reduction of 25 percent or more in industrial energy intensity in 10 years. And, let’s not forget the very prominent Leadership in Energy and Environmental Design (LEED®) rating program. Created by the U.S. Green Building Council, LEED awards projects based on their use of sustainable materials and highly efficient equipment.
The newest program is the Economy, Energy and Environment Initiative, known as E3, a coordinated federal and local technical assistance program to provide manufacturers with customized, hands-on assessments of production processes and assist with the implementation of energy-saving projects. In October 2010, the DOE, EPA, U.S. Department of Commerce, U.S, Small Business Administration and U.S. Department of Labor signed a memorandum to support this worthy initiative.
One example of how this works in real life is Milwaukee’s new ME3 program that will invite local manufacturers to participate in a new sustainability program to drive down waste in their production processes and cut costs. Federal agencies and local partners, such as universities and the state’s focus on energy program, will provide technical assistance.
Academia Joins the Movement
Yet another reason to view America’s growing focus on the greening of manufacturing operations with hope is the surge in partnerships between academia and industry.
One program growing in prominence is Western Michigan University’s Green Manufacturing Initiative, which in late 2010 received a $1 million grant from the DOE. The goal: Establish a consortium between the school and industry partners to solve “green” related issues and assess what projects they should tackle to reduce the environmental and energy impact of their designs, materials, processes and facilities.
The school’s program, launched in early 2010, already has produced numerous real-life results. One example: Two students reviewed a local company’s overhead doors and the efficiency of door heaters. They provided design solutions that involved differential steam control valves and proximity sensors to automatically operate the doors. An initial investment of $5,100 now generates annual energy savings of $28,400.
A different emphasis that enhances green industrial development is the new partnership between Rochester Institute of Technology and Caterpillar, Inc. A $650,000 gift from the company will fund the Caterpillar Professorship in Remanufacturing that will focus on promoting research, education and outreach in remanufacturing, the technical process through which components and parts are restored to “like new” condition and reused.
Multiply the inspiring work of just these two schools to the many other U.S. universities tackling the green manufacturing issue and one begins to feel quite upbeat about how America’s young people are responding to the challenge.
Manufacturing Associations Carrying the Green Banner
It is not surprising that America’s manufacturing trade groups have made sustainability initiatives a priority. In this case, America takes a back seat to no other country.
This is exemplified by programming at the most recent FABTECH tradeshow, cosponsored by five leading manufacturing associations, including Fabricators & Manufacturers Association, International (FMA). “Make Green by Going Green” headlined the keynote presentation and discussion led by Kristin Pierre, the Green Supplier Network manager from the EPA; panelists from companies implementing successful sustainable practices related their experiences to attendees. Many other seminars addressed the issue, covering topics such as “the lean and green audit,” “how to be lean and green with your finishing system,” and “converting factory lighting.” Similar subjects are planned for the FABTECH 2011 event.
And, let’s look at just one four-month period on a green manufacturing events calendar. To list only a few, there’s the FMA’s “Zero-Waste-to-Landfill Workshop;” the “Sustainability in Business Conference,” presented by the Paul Merage School of Business University of California-Irvine; the Association of Energy Engineers Globalcon 2011 conference; and the Engineering Sustainability 2011 conference.
Thanks to our high-tech era, individuals can attend educational sessions from their desks via webinars. Here, too, the industry offers numerous opportunities to gain knowledge. One example of many is the recent, “The Business Case for Green Manufacturing” webinar, sponsored by the Green Manufacturer Network.
Trade Editorial Media Vigorously Showcases Solutions
Complementing the work conducted by government, academia and industry is the surge in press coverage devoted to green practices. One striking example is the one-year-old Green Manufacturer magazine. Even in a turbulent economy, the publishers felt they should take a risk and launch a title devoted to this business-critical subject matter.
In the debut issue, editor Kate Bachman explained why, stating, “With increasing frequency, we have received requests from manufacturers looking to implement sustainable practices, which convinced us that the time is right to look at manufacturing through a green filter.
“Green Manufacturer covers how to implement green manufacturing operations and facility improvements and use energy-efficient, eco-friendly equipment and products in a way that is cost-effective – and sometimes even cost reductive,” she added. Many other magazine titles now devote editorial space to such topics, indicative of the continued, growing interest of manufacturers to join the green movement.
Car Companies Commit to Renewable Energy
Energy savings have long been a mantra for the automotive industry when designing new cars. Now, this goal is a priority in the production process as well.
More than half of General Motors’ global manufacturing facilities are achieving landfill-free status. At a landfill-free plant, more than 95 percent of waste is reused or recycled. Further underscoring that green is both good for the planet and the pocketbook, GM reports it generates more than one billion dollars in revenue from recycled scrap metal alone.
At the Ford Motor Co. in Wayne, MI, solar panels are used to generate about 500 kilowatts of power to augment the conventional power sources in the plant’s electrical system. The pilot project may be extended to other Ford plants. Also, Ford will install 10 electric vehicle charging stations to charge trucks that transport parts between buildings.
Taking it one step further is Freightliner Custom Chassis Corp. (FCCC) of Gaffney, SC Once the local landfill’s best customer, FCCC, the nation’s largest producer of diesel-power chassis for vans, buses and other vehicles, dumps zero waste in any landfill. Essentially, FCCC reduced the waste with reusable packing and product redesigns and identifying recycling recipients for all of its remaining solid waste.
Lighting the Way
For many companies, changing the lighting systems in their plants represents an effective and relatively elementary method to save energy.
Aqua Lung, a Vista, CA, manufacturer of diving and snorkeling equipment, installed a “daylighting” system that harnesses natural daylight for the company’s 60,000-square-foot facility. Through the use of photocontrols and a dedicated phone line to the local utility to monitor usage, the site achieved an immediate electricity consumption reduction of 33 percent.
United Displaycraft, a Des Plaines, IL,-based manufacturer of point-of-purchase displays, turned to the sun to generate “green” electricity and take advantage of government incentives with the largest privately owned commercial photovoltage solar panel installation in Illinois. The solar system will pay for itself in four to five years.
Fabricators a Force
Manufacturers in the fabricating industry are among the leaders in aggressively implementing green tactics:
DeWys Manufacturing of Grand Rapids, MI, a precision fabricator, learned from an environmental audit that reducing wastewater was an area it should target. Through increased employee vigilance and better monitoring of equipment, the company cut its annual water usage by 58 percent.
Rapid-Line Inc., Grand Rapids, MI, a full-service fabrication and tooling shop, initially focused its green efforts on natural gas consumption. Implementing a variety of measures, such as installing insulation and industrial-grade fans to capture and redirect excess heat from its paint line ovens, Rapid-Line reduced gas consumption significantly while saving $46,000 annually.
Colson Caster Corp. of Jonesboro, AR, illustrates how manufacturers can begin efforts modestly. An analysis revealed installing a new air compressor and dryer would be an extremely effective first step. A year later, this single imitative resulted in a 25 percent annual energy savings; a savings of $2,000 per year in repair costs; a three-year ROI; a reduction in use of 700 gallons of nonbiodegradable oil per year…and even a safer working environment.
As Green Manufacturing editor Kate Bachman recently wrote, “The reality we are living and working in today is that we now compete globally with countries that are heavily subsidizing renewable-energy manufacturers and their export activities.
“We need to recognize that North American industry is not operating on its own little island anymore.”
It’s a perfect storm – but a positive one. Two strong forces today are converging in the U.S. manufacturing sector that can deliver a whirlwind of benefits for those companies – and the environment. First, at long last, American industrial executives are recognizing the importance of preserving and enhancing the use of our precious natural resources through green energy practices in a vast array of manufacturing applications. Second, it’s now apparent to most manufacturers that this altruistic perspective, unlike many, can positively impact bottom lines and deliver cost-saving benefits short term and long term.
A new study of manufacturing professionals confirms this perspective. When asked by IFS North America what’s driving their companies to adopt and implement green initiatives, “it’s a management directive” shared top billing, cited by 54 percent of respondents. “It’s a social responsibility” also was cited by 54 percent of the manufacturers, followed closely by “customers are demanding it” (50 percent).
In addition, a 2011 study by the Material Handling Industry of America (MHIA) revealed a whopping nine in 10 executives surveyed say their companies believe that sustainable initiatives have the potential to both save money and resources.
The U.S. manufacturing sector can play a significant role in meeting the energy demand challenge. According to The Manufacturing Institute and the U.S. Department of Labor, the industrial sector accounts for nearly one-third (31 percent) of total end-user consumption in the United States, even surpassing transportation (28 percent). Residential (22 percent) and commercial (19 percent) rank third and fourth. Thus, green practices employed by manufacturers will impact a large percentage of energy use.
Greener, more energy-efficient manufacturing environments represent the ultimate win-win. A recent study by Aberdeen Group on sustainability initiatives conducted by more than 200 companies, many of them in manufacturing, illustrates the benefits of green manufacturing practices. Those deemed “best in class” achieved an impressive 9 percent reduction in carbon footprint while cutting energy costs 6 percent, facilities costs by 7 percent, paper costs by 10 percent and transportation/logistics costs by 7 percent.
And, this movement transcends politics. Both sides of the political spectrum have addressed the energy challenges the United States and the world face. As noted in his new book, Make It in America, Andrew Liveris, chairman and CEO of Dow Chemical, writes, “Energy, clearly, is one of the megatrends defining this century. It is only going to grow in importance as global demand increases.”
Major "Catch-Up" Needed
Although the greening of manufacturing is starting to permeate U.S. factories, America has some major catching up to do when compared to other countries. China significantly outpaces the United States in the green manufacturing arena. In 2008, China nearly doubled the amount of installed capacity of renewable electricity when compared to the United States. According to Dow Chemical’s Liveris, in 2009 China invested $34.6 billion in the renewable energy sector, almost twice the amount than the United States spent. China also became the world’s biggest maker of wind turbines in 2009 and the largest solar panel manufacturer in 2010, accounting for one third of the world’s solar panels.Admittedly, China is not a democracy and can mandate initiatives America likely would not. Yet, it’s difficult to dispute that China has made the greatest strides globally in instituting renewable, environmentally friendly energy initiatives.
Perhaps a more “apples to apples” example is Germany, a mature western European economy. Initially fueled in part by passage of its Renewable Energies Act in 2000, which paid any company or individual who sold back renewable energy to the grid, Germany quickly achieved rather ambitious goals. In 2000, the government set an objective to generate 12.5 percent of its electricity from renewable sources by 2012; it attained that level five years early. A new goal to achieve a 20 percent level by 2020 likely will be achieved in 2011, according to Liveris. In addition, the surging number of Germans employed in the renewable energy sector would make other countries green with envy.
America's Green Glass is Half-Filled...and Rising
Despite America’s need to take longer and faster strides in this critical area, a plethora of recent developments has sparked greater participation from manufacturers in green initiatives.New Government Programs Are Green Catalysts
Countries such as China and Germany have achieved such dramatic success in the industrial green arena due, in great part, to the substantial national programs that make energy efficiency commitments easier and financially rewarding within their borders. Many U.S. pundits voice frustration with America’s lack of any comparable national policies. That issue will not be debated here.
But what can be stated with certainty is the existence of a number of new “assistance” programs established by government agencies to help manufacturers create sustainable programs. One growing in popularity is the Green Suppliers Network established by the U.S. Environmental Protection Agency (EPA) in collaboration with the U.S. Department of Commerce. Its mission is to help small and medium-sized manufacturers stay competitive and profitable while reducing their impact on the environment.
This is accomplished via the network’s “Lean and Clean Advantage.” The program works with large manufacturers to engage their suppliers in low-cost technical reviews to identity strategies to improve process lines, use materials more efficiently and eliminate the root causes of waste.
Of course, there is a host of U.S. Department of Energy (DOE) initiatives. For example, the department offers the Industrial Technologies Program Save Energy Now that aims to drive a reduction of 25 percent or more in industrial energy intensity in 10 years. And, let’s not forget the very prominent Leadership in Energy and Environmental Design (LEED®) rating program. Created by the U.S. Green Building Council, LEED awards projects based on their use of sustainable materials and highly efficient equipment.
The newest program is the Economy, Energy and Environment Initiative, known as E3, a coordinated federal and local technical assistance program to provide manufacturers with customized, hands-on assessments of production processes and assist with the implementation of energy-saving projects. In October 2010, the DOE, EPA, U.S. Department of Commerce, U.S, Small Business Administration and U.S. Department of Labor signed a memorandum to support this worthy initiative.
One example of how this works in real life is Milwaukee’s new ME3 program that will invite local manufacturers to participate in a new sustainability program to drive down waste in their production processes and cut costs. Federal agencies and local partners, such as universities and the state’s focus on energy program, will provide technical assistance.
Academia Joins the Movement
Yet another reason to view America’s growing focus on the greening of manufacturing operations with hope is the surge in partnerships between academia and industry.
One program growing in prominence is Western Michigan University’s Green Manufacturing Initiative, which in late 2010 received a $1 million grant from the DOE. The goal: Establish a consortium between the school and industry partners to solve “green” related issues and assess what projects they should tackle to reduce the environmental and energy impact of their designs, materials, processes and facilities.
The school’s program, launched in early 2010, already has produced numerous real-life results. One example: Two students reviewed a local company’s overhead doors and the efficiency of door heaters. They provided design solutions that involved differential steam control valves and proximity sensors to automatically operate the doors. An initial investment of $5,100 now generates annual energy savings of $28,400.
A different emphasis that enhances green industrial development is the new partnership between Rochester Institute of Technology and Caterpillar, Inc. A $650,000 gift from the company will fund the Caterpillar Professorship in Remanufacturing that will focus on promoting research, education and outreach in remanufacturing, the technical process through which components and parts are restored to “like new” condition and reused.
Multiply the inspiring work of just these two schools to the many other U.S. universities tackling the green manufacturing issue and one begins to feel quite upbeat about how America’s young people are responding to the challenge.
Manufacturing Associations Carrying the Green Banner
It is not surprising that America’s manufacturing trade groups have made sustainability initiatives a priority. In this case, America takes a back seat to no other country.
This is exemplified by programming at the most recent FABTECH tradeshow, cosponsored by five leading manufacturing associations, including Fabricators & Manufacturers Association, International (FMA). “Make Green by Going Green” headlined the keynote presentation and discussion led by Kristin Pierre, the Green Supplier Network manager from the EPA; panelists from companies implementing successful sustainable practices related their experiences to attendees. Many other seminars addressed the issue, covering topics such as “the lean and green audit,” “how to be lean and green with your finishing system,” and “converting factory lighting.” Similar subjects are planned for the FABTECH 2011 event.
And, let’s look at just one four-month period on a green manufacturing events calendar. To list only a few, there’s the FMA’s “Zero-Waste-to-Landfill Workshop;” the “Sustainability in Business Conference,” presented by the Paul Merage School of Business University of California-Irvine; the Association of Energy Engineers Globalcon 2011 conference; and the Engineering Sustainability 2011 conference.
Thanks to our high-tech era, individuals can attend educational sessions from their desks via webinars. Here, too, the industry offers numerous opportunities to gain knowledge. One example of many is the recent, “The Business Case for Green Manufacturing” webinar, sponsored by the Green Manufacturer Network.
Trade Editorial Media Vigorously Showcases Solutions
Complementing the work conducted by government, academia and industry is the surge in press coverage devoted to green practices. One striking example is the one-year-old Green Manufacturer magazine. Even in a turbulent economy, the publishers felt they should take a risk and launch a title devoted to this business-critical subject matter.
In the debut issue, editor Kate Bachman explained why, stating, “With increasing frequency, we have received requests from manufacturers looking to implement sustainable practices, which convinced us that the time is right to look at manufacturing through a green filter.
“Green Manufacturer covers how to implement green manufacturing operations and facility improvements and use energy-efficient, eco-friendly equipment and products in a way that is cost-effective – and sometimes even cost reductive,” she added. Many other magazine titles now devote editorial space to such topics, indicative of the continued, growing interest of manufacturers to join the green movement.
Moving from Theory to Real-Life
Research, projections, initiatives and editorials are all well and helpful. What’s inspiring is how these discussions and programs are applied in real-life manufacturing situations. Here are just a few examples.Car Companies Commit to Renewable Energy
Energy savings have long been a mantra for the automotive industry when designing new cars. Now, this goal is a priority in the production process as well.
More than half of General Motors’ global manufacturing facilities are achieving landfill-free status. At a landfill-free plant, more than 95 percent of waste is reused or recycled. Further underscoring that green is both good for the planet and the pocketbook, GM reports it generates more than one billion dollars in revenue from recycled scrap metal alone.
At the Ford Motor Co. in Wayne, MI, solar panels are used to generate about 500 kilowatts of power to augment the conventional power sources in the plant’s electrical system. The pilot project may be extended to other Ford plants. Also, Ford will install 10 electric vehicle charging stations to charge trucks that transport parts between buildings.
Taking it one step further is Freightliner Custom Chassis Corp. (FCCC) of Gaffney, SC Once the local landfill’s best customer, FCCC, the nation’s largest producer of diesel-power chassis for vans, buses and other vehicles, dumps zero waste in any landfill. Essentially, FCCC reduced the waste with reusable packing and product redesigns and identifying recycling recipients for all of its remaining solid waste.
Lighting the Way
For many companies, changing the lighting systems in their plants represents an effective and relatively elementary method to save energy.
Aqua Lung, a Vista, CA, manufacturer of diving and snorkeling equipment, installed a “daylighting” system that harnesses natural daylight for the company’s 60,000-square-foot facility. Through the use of photocontrols and a dedicated phone line to the local utility to monitor usage, the site achieved an immediate electricity consumption reduction of 33 percent.
United Displaycraft, a Des Plaines, IL,-based manufacturer of point-of-purchase displays, turned to the sun to generate “green” electricity and take advantage of government incentives with the largest privately owned commercial photovoltage solar panel installation in Illinois. The solar system will pay for itself in four to five years.
Fabricators a Force
Manufacturers in the fabricating industry are among the leaders in aggressively implementing green tactics:
DeWys Manufacturing of Grand Rapids, MI, a precision fabricator, learned from an environmental audit that reducing wastewater was an area it should target. Through increased employee vigilance and better monitoring of equipment, the company cut its annual water usage by 58 percent.
Rapid-Line Inc., Grand Rapids, MI, a full-service fabrication and tooling shop, initially focused its green efforts on natural gas consumption. Implementing a variety of measures, such as installing insulation and industrial-grade fans to capture and redirect excess heat from its paint line ovens, Rapid-Line reduced gas consumption significantly while saving $46,000 annually.
Colson Caster Corp. of Jonesboro, AR, illustrates how manufacturers can begin efforts modestly. An analysis revealed installing a new air compressor and dryer would be an extremely effective first step. A year later, this single imitative resulted in a 25 percent annual energy savings; a savings of $2,000 per year in repair costs; a three-year ROI; a reduction in use of 700 gallons of nonbiodegradable oil per year…and even a safer working environment.
Competing, Cost-Containing and Caring
It’s quite apparent that more and more manufacturers understand the value of sustainability initiatives. Two aforementioned studies revealed nearly identical high numbers of executives who recognize this. Nearly nine of 10 respondents (88 percent) in the MHIA study say that sustainability initiatives will be of even greater importance over the next 14 to 18 months. Similarly, 81 percent of those surveyed by IFS expect green supply chain initiatives to become more important in the next three years. Such numbers truly are overwhelming.As Green Manufacturing editor Kate Bachman recently wrote, “The reality we are living and working in today is that we now compete globally with countries that are heavily subsidizing renewable-energy manufacturers and their export activities.
“We need to recognize that North American industry is not operating on its own little island anymore.”
Looking for a reprint of this article?
From high-res PDFs to custom plaques, order your copy today!