Novel Hybrid Technology Accelerates VOC Release from Wood Coatings
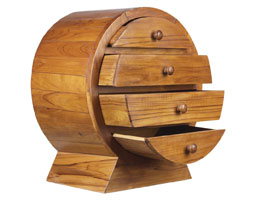
As an example, the current dominant technologies used in North America are solventborne nitrocellulose lacquers for wood furniture, and acid-catalyzed alkyd-aminoplast conversion varnishes for kitchen and bath cabinets.(1) Reformulation of these solventborne coatings to lower VOC and HAPs levels has allowed their continued use in those markets, but the use of even lower VOC technologies should be expected to grow in the future. In particular, UV-cure technology has grown significantly in the kitchen cabinet market, where flat stock can be finished before assembly.(1) Waterborne technologies are also available, and waterborne systems based on acrylic latex, polyurethane dispersions and other polymer technologies have been increasingly utilized as regulatory pressures lead coating manufacturers and wood finishers to look for more environmentally advanced coatings.
Wood coatings end users such as furniture and cabinet manufacturers are also looking for solutions to regulations and specifications that limit emissions of chemical species from finished products. Regulatory pressure is partly the result of consumer demand for living and working space with better air quality, and partly based on the knowledge that building materials and products such as finished wood can affect indoor air quality by emitting volatile components long after their manufacture.
Examples include limits on individual species such as formaldehyde or certain other aldehydes, as well as on total VOC (TVOC), an estimation of the total volatile organic content that is emitted from a wooden coated part after it has been dried for a certain amount of time and is then packaged for shipment. Manufacturers don’t want consumers to be exposed to volatile emissions when items are unpacked, or for their products to be emitting VOCs during use and contributing to poor indoor air quality. There are several certification and specification programs underway that limit volatile emissions, such as those from Greenguard(2) and BIFMA (Business and Institutional Furniture Manufacturers Association).(3) Both the Greenguard and BIFMA standards measure volatile emissions using a dynamic chamber method designed to simulate emissions occurring in a model environment, such as a business office or residential bedroom.(3,4)
The purpose of this article is to describe a new waterborne technology for wood coatings that will impact both the VOC content and rate of emission from finished wood products. A unique combination of acrylic latex and polyurethane dispersion (PUD) polymers leads to a coating that has lower VOC demand and offers a mechanism for the accelerated release of coalescing solvents compared to a waterborne acrylic by itself. Performance improvements in hardness development are significant, as well as in properties that are related to hardness such as block, print, scratch and mar resistance. The effect of the technology on the measurement of volatile emissions will be described. A comparison of the new acrylic/PUD blends with waterborne acrylics and commercial waterborne and solventborne wood coating systems will be made using test protocols designed for wood furniture and kitchen cabinet applications.
![]() |
Table 1 Click to enlarge |
Experimental
The acrylic/polyurethane binder based on the new technology that was used in the evaluations is designated as PUA-1. It is a blend of a hard acrylic latex and a soft polyurethane dispersion, and contains self-crosslinking functionality that cures by oxidative and photolytic mechanisms at ambient temperatures. PUA-1 was prepared at 39.0% weight solids and pH 7.6, and has a minimum film formation temperature (MFFT) of less than 0 °C. PUA-1 contains some solvent (dipropylene glycol dimethyl ether, DMM), which comes from the manufacturing process of the PUD. PUA-1 contains approximately 2.9% DMM on total, and has a calculated VOC content of approximately 84 g/L. DMM does act as a coalescent and aids in film formation for the acrylic/urethane blends.
![]() |
Table 2 Click to enlarge |
Commercial coating systems designed for use in wood furniture and cabinet applications were obtained from their manufacturers and are described briefly in Table 3. The systems consisted of both a sealer and topcoat. The commercial waterborne system (COM-1) consisted of sealer (WB-1) and acrylic topcoat (WB-2) formulations. The binder chemistry is not disclosed for WB-1, but is assumed to be acrylic latex. Solventborne system COM-2 consisted of a fast-drying, vinyl-modified nitrocellulose sealer (SB-1) and a cellulose acetate butyrate (CAB)/acrylic topcoat (SB-2). The second solventborne system (COM-3) uses both sanding sealer and lacquer based on nitrocellulose technology. Sealer and topcoat combinations were chosen based on manufacturer system recommendations.
Panel Preparation
![]() |
Table 3 Click to enlarge |
For most tests, coating systems were applied to maple panels (10 cm x 30 cm) by conventional air spray. Coatings were applied at approximately 1 mil (25 mm) dry film thickness per coat, with one coat of sealer and two coats of topcoat. Maple panels were sanded with 220 grit sandpaper prior to use, with sanding dust removed by compressed air spray and wiping with a clean, lint-free cloth. For each coat applied, the coating was dried at ambient temperature for 10 min and then placed in a 60 °C oven for an additional 10 min. The sealer was sanded with 280 grit sandpaper prior to application of the topcoat. After sealer and topcoats were applied, the maple panel was placed in a constant temperature and humidity room (75 °F and 50% RH) for 2 weeks prior to testing.
For hardness, scratch/mar, and block and print resistance tests, coatings were applied by drawdown bar to a treated aluminum panel (Q Panel Type AL-412 chromate pretreated aluminum, 10 cm x 30 cm) to yield approximately 1.5 mil (40 mm) dry film thickness. Panels were placed in a constant temperature and humidity room (75 °F and 50% RH) for the amount of time listed below for each test prior to testing.
Testing Procedures
Coatings were evaluated according to the test methods for kitchen and vanity cabinet coatings outlined in the Kitchen Cabinet Manufacturers Association (KCMA) standard.(5)
A) Detergent and Water Resistance (edge soak) – For this test, all six sides of the maple panels were coated as described previously. A #8 cellulose sponge was soaked in a 0.5% Palmolive dish detergent solution, and the panel edge was placed on the sponge for 24 h. Panels were rated for delamination, swelling, color change, checking and other forms of film failure. A pass is reported for no change in the film and panel.
B) Hot and Cold Check Resistance – This test cycled the panel between hot (49 °C), ambient (25 °C) and cold (-21 °C) temperatures, and was run as described in the KCMA standard using a Thermotron environmental chamber model S-8S-SL. A pass is reported for no change in the panel or coating.
C) Shrinkage and Heat Resistance – This test placed the panel at 49 °C and 70% relative humidity for 24 h and was run using a Hotpak Environmental Chamber model 417532. A pass is reported for no change in the condition of the coating.
D) Chemical Resistance – The coating was subjected to a variety of household chemicals to determine its resistance to staining and discoloration. The chemicals include lemon, orange and grape juices, vinegar, ketchup, coffee, olive oil, 50% ethanol, 0.5% Palmolive dish detergent, and mustard. Chemicals were applied to the panel in a vertical position, and allowed to stand for 24 h before cleaning and rating of the panel. In the case of mustard, cleaning was performed after a 1 h exposure. The exposed coating was evaluated for discoloration, staining and other obvious changes, and rated on a 1 to 10 scale, with 10 equal to no change.
Other tests were run on maple substrates to evaluate the systems as viable coatings for wood furniture and general wood application. These include the following:
E) Clarity – A visual observation of the coating clarity.
F) Adhesion – an “X” scribe was cut into the coating using a razor blade. Adhesion was tested by the tape pull method (ASTM D 3359) using Permacel 99 tape. Ratings use a scale of 0A to 5A, with 5A being no adhesion loss.
G) Chemical Spot Resistance – Resistance to common chemicals was evaluated by applying spots of the chemical to the coated panel for a specified time, then cleaning the panel with clean water and a sponge, and drying prior to rating. Chemicals were applied to the surface by saturating a 2.3 cm, grade 3 Whatman filter and covering with a watchglass to prevent evaporation. One hour spot tests were done using ethanol, isopropyl alcohol, butyl acetate and acetone. Overnight exposures for 16 h were done with water, hot coffee, 50% ethanol, Formula 409 cleaner, isopropyl alcohol, 7% ammonia, Scheaffer brand red ink, and grape juice. Rating of film damage and discoloration/staining was done on a 1 to 10 scale, with 10 being no change.
Several tests were performed on just the topcoat, including hardness, scratch/mar, block and print resistance, and gloss and color retention. These tests were evaluated for topcoats applied to treated aluminum panels.
H) Koenig Hardness – evaluated according to ASTM D 4366 using a TQC SP0500 Pendulum Hardness Tester, and reported in seconds. Measurements were taken at various intervals over the course of 2 weeks.
I) Block Resistance – Panels were dried for 1 or 7 days, and then two 4 cm wide strips were cut from the aluminum panel, and placed face-to-face forming a cross. A #8 rubber stopper was placed on the cross-section of the strips, and a 1 kg weight placed on top of the rubber stopper. Block resistance was rated under two conditions, 1) after 24 h at room temperature, and 2) after 30 min at 60 °C. The following 0 to 10 scale was used to rate the coatings for tack and film damage: 10, no tack/perfect; 9, trace tack/excellent; 8, slight tack/very good; 7, slight tack/good; 6, moderate tack/good; 5, moderate tack/fair; 4, severe tack, no seal/ fair; 3, 5-25% seal/ poor; 2, 25-50% seal/ poor; 1, 50-75% seal/ poor; 0, complete seal/ very poor.
J) Scratch/Mar Resistance – Scratch and mar resistance can be measured by several methods. A new method was employed in this study, which insults the film with a combination of scratch, mar and impact damage. Coatings were applied to a treated aluminum panel and dried for 12 days prior to testing. A section of the panel was placed on the bottom of a quart container with the film facing up. Various types of impact media were placed on top of the film, the container sealed and placed on a paint shaker. The container was agitated for two min, and then the sample was removed and evaluated visually. Different types of impact media can lead to different types of damage, corresponding to differing real-world insults. This study used three different sets of impact media, a) 10 smooth, spherical, 1/4 inch diameter steel shot beads, b) two 1/2 inch diameter hexagonal steel nuts, or c) one metal lid from a two ounce paint can. In general, impact media with more corners and with corners having smaller radii of curvature lead to more damage on most films. More massive media also tend to produce greater damage. The type of damage also changes with media shape – for example, ball bearings create mainly impacting-type damage, metal lids create mainly marring-type of damage, and sharper objects (such as screws) can create mainly gouging-type damage.
K) Gloss and Color Retention – Topcoats were applied in one coat at approximately 1.5 mils (40 mm) dry film thickness to the white portion of a metal Leneta chart T12-10. Panels were dried for 2 weeks prior to testing. Panels (7.5 cm x 12.5 cm) were exposed in a QUV accelerated weathering cabinet using UV-A bulbs (340 nm) and a cycle consisting of 8 h light and 4 h condensation. Gloss (20°/60°) and color (L*a*b*) were measured initially and at various time intervals during the exposure.
Results and Discussion
![]() |
Figure 1 Click to enlarge |
Once film formation has occurred, coalescents and cosolvents are no longer needed in the film, and it is desirable for them to leave the dry coating film to enhance properties such as hardness. Some slow coalescents [e.g., 2,2,4-trimethyl-1,3-pentanediol monoisobutyrate (IBT)] remain in acrylic coating films for many weeks or longer. Acrylic/urethane blends based on the new technology offer a novel mechanism for the faster release of volatiles, such as coalescents and co-solvents, from the drying film. The result is a dry film that offers faster hardness development and improvement in other film properties that rely on hardness such as block, print and mar resistance, and dirt pickup resistance. The mechanistic details of the new acrylic/urethane blend technology have been described previously,(6) but a short description will be given here to aid the reader in understanding the results of the current study.
The technology depends on the presence of two polymer phases. The major or dominant phase is a hydrophobic, hard acrylic polymer. Rapid hardness development works best with an acrylic having a glass transition temperature (Tg) greater than 25 °C. The second, minor phase is a soft polyurethane, which in the wet state is more hydrophilic than the acrylic due to its swollen, hydroplasticized state. In the wet state of the formulated hybrid polymer, the coalescent partitions mainly to the more hydrophobic acrylic phase, where it is most needed and aids in lowering the MFFT. This partitioning of coalescent has been demonstrated through computer modeling studies and experimentally using NMR techniques.(6) After coating application, water evaporates and polymer particles begin to deform as film formation proceeds (Figure 1).
![]() |
Figure 2 Click to enlarge |
When most of the water has left the film, the polyurethane phase changes from being hydrophilic to hydrophobic, and this shift acts as a trigger for the coalescent to diffuse from the acrylic phase to the polyurethane phase. Changes in how small molecules partition between polymer phases of different composition after film formation have been previously demonstrated in related acrylic latex systems, where the small molecules were non-volatile, low-molecular-weight acrylic oligomers.(7) In the present study, the small molecules are volatile coalescents. It is known that small molecules, such as coalescents, will diffuse more rapidly through a soft polymer phase due to the effect of greater free volume; thus the coalescent will diffuse out of the film via the soft polyurethane phase more rapidly than if the hard acrylic phase were by itself.
One requirement of the mechanism shown in Figure 1 is that the polyurethane phase must form a continuous network through which the coalescent can diffuse. The amount of polyurethane needed to form this “percolation network” depends on the relative particle sizes of the polyurethane dispersion and acrylic latex employed and the geometry of particle packing. In general a minimum of about 20 - 30% by weight of total polymer is required to be polyurethane.
The described mechanism results in faster coalescent release from a drying film, and impacts properties such as early hardness development, block and print resistance, and scratch/mar resistance. The faster coalescent release also presents the possibility for lowering the TVOC of a factory-applied wood coating. Early water resistance can be improved by removing hygroscopic materials such as hydrophilic coalescents and co-solvents from the drying film before the dry film comes into contact with water. The presence of a polyurethane phase also tends to improve toughness, as measured by pencil hardness and scratch/mar resistance, compared to an all-acrylic composition.
The improved hardness development is demonstrated in Figure 2, which plots Koenig pendulum hardness versus drying time at room temperature for acrylic/polyurethane PUA-1 and hard acrylic AC-1. For this experiment, the clear formulations were fairly simple, including only binder, water, coalescent at 20% on polymer solids, wetting aid and thickener. A single coalescent was used in each case, including the slow coalescent IBT, dipropylene glycol butyl ether (DPnB) and the fast coalescent ethylene glycol butyl ether (EB). For a particular coalescent, it is observed that PUA-1 develops Koenig hardness much more quickly. For example, Koenig hardness of the PUA-1 formula containing IBT is approximately 70 s after 7 days dry, whereas the acrylic AC-1 is only at approximately 50 s. Clearly neither has reached their ultimate hardness, which is measured after baking the panel to drive off all volatiles, and is close to 130 s. This demonstrates an important point regarding the new technology presented here.
The presence of the polyurethane polymer phase in the dry film only provides a pathway for the coalescent to diffuse from the film more rapidly than through the acrylic phase. The ultimate hardness of the system (i.e., hardness achieved after all volatile materials have been driven off) relies mainly on the hardness (and Tg) of the acrylic phase. The rate of release is also dependent on the volatility of the coalescent. Thus, when a non-volatile coalescent or plasticizer is used, such as dibutylphthalate, the polyurethane-based pathway is ineffective at improving hardness development or related properties, because the plasticizer never leaves the film. However, when a more volatile coalescent such as EB is utilized, hardness development can be greatly accelerated. In Figure 2, the PUA-1 film containing EB has reached its ultimate hardness in less than 3 days, compared to the acrylic AC-1, which is still not there after seven days. Figure 2 shows significant acceleration is also observed with a coalescent of more moderate volatility, such as DPnB.
![]() |
Table 4 Click to enlarge |
The accelerated coalescent release also improves block resistance for the acrylic/polyurethane blends compared to the hard acrylic. Table 4 shows results of block resistance testing for clear formulations based on acrylic/polyurethane PUA-1 and hard acrylic AC-1. The formulas contained only binder, water, coalescent, wetting aid and thickener. No waxes or mar/slip aids were included in order to see the polymer effect on block resistance. Coatings were coalesced with either a slow coalescent (IBT) or a fast coalescent (EB) at 20% on polymer solids. The coatings were dried at room temperature for 1 or 7 days before running both 24 h room temperature and 30 min oven (60 °C) block tests. The data shows an advantage for the acrylic/polyurethane blend technology, especially at early dry times. Block resistance is an important property for factory-applied coatings as it should develop before coated items are stacked or packaged to prevent damage to the new film.
![]() |
Figure 3 Click to enlarge |
Scratch and mar resistance are also improved by the faster coalescent release. Figure 3 shows damage inflicted on clear coatings based on acrylic/polyurethane PUA-1 and hard acrylic AC-1 and tested according to the new method described above. The formulas in this case are those shown in Tables 1 and 2, and the test was also run for formulations without the mar aid and wax. Figure 3 demonstrates the enhanced mechanical durability of PUA-1 over AC-1 using this scratch/mar test. Using a metal lid as the impact media leads to a marring type of damage, and results in more and deeper scratches in the all-acrylic AC-1 than it does in PUA-1 (photos on left).
![]() |
Figure 4 Click to enlarge |
The formulations pictured on the left side of Figure 3 were made with no mar or slip additives to show the inherent properties of the resins. If mar and slip additives are included in the formulations they both perform much better, but PUA-1 still creates a more resilient film. Using steel hex nuts as the impact media leads to small, roughly spherical gouges, but mar and slip additives can largely mitigate these gouges. Even with mar and slip aids, however, the impact of these collisions causes flakes of film to chip off in some locations for acrylic polymer AC-1, whereas the film made from PUA-1 is free of these defects (photos on right). Similar testing was done with spherical steel shot. Steel shot leads to less visible damage, but there is still a clear advantage to using PUA-1 over AC-1.
The release of volatiles from the films was also measured using GC analysis of the headspace in a static chamber method. Aluminum panels were coated by drawdown with the same two coatings based on AC-1 and PUA-1. After drying for 7 days in an environmental chamber at 23 °C and 50% relative humidity, the panel was placed in a chamber that provided a surface area to volume ratio of 1 m2/m3. The panel sat overnight in the chamber, and the headspace was then sampled and analyzed by GC. Results are shown in Table 5. The TVOC measured for the coatings is 21 mg/m3 for the hard acrylic AC-1, and a significantly lower value of 2 mg/m3 for the acrylic/polyurethane PUA.
![]() |
Table 6 Click to enlarge |
The main benefits of the new acrylic/polyurethane blend technology are in properties related to the release of the coalescent, such as hardness, block, scratch/mar and TVOC. Other properties important for industrial wood coatings, such as chemical resistance and flexibility, remain largely unchanged by the presence of the polyurethane phase. Water resistance is generally improved by the more rapid release of coalescent from the hybrid film. Another key feature of PUA-1 is the ability to self-crosslink at ambient temperatures and still maintain true one-package stability. The functional groups present in the polymer will crosslink via both oxidative and photolytic curing mechanisms.
![]() |
Table 7 Click to enlarge |
Formulations based on the resin will begin to crosslink as soon as they are applied, and may require about 2 to 4 weeks until some properties have reached their maximum performance level. The crosslinking offers enhancements to properties such as dirt pickup resistance, chemical and solvent resistance, and durability. Because PUA-1 combines both hard acrylic and soft polyurethane phases, and the soft PUD phase contributes to lowering the MFFT of the blend, it can also be formulated at lower coalescent demand than the corresponding acrylic phase by itself. This manifests itself in the ability to formulate at lower VOC, while giving a coating that has better hardness development – a combination that is sought after in a variety of applications.
![]() |
Figure 5 Click to enlarge |
Coatings based on the acrylic/polyurethane blend technology were also evaluated over wood according to test methods used for kitchen and bath cabinets and wood furniture. Table 6 shows results of testing in self-sealed coating systems over maple according to the KCMA standards.(5) The new technology represented by PUA-1 is compared to AC-1, a commercial hard acrylic latex that exhibits excellent performance in wood coatings. The binders were formulated into the clear formulations given in Tables 1 and 2. Also included in the testing were two solventborne systems that are commercially available, based on nitrocellulose sealers, and acrylic (COM-2) or nitrocellulose (COM-3) topcoats. A commercially available waterborne system (COM-1) using an acrylic topcoat was also used for comparison.
Overall, PUA-1 performed very well versus the much higher VOC commercial systems, only showing some staining in the mustard spot resistance. Similar testing typical for furniture coatings was also done for self-sealed systems over a maple substrate. Comparisons with AC-1 and the solventborne and waterborne commercial systems are included in Table 7. Overall, PUA-1 performed very well, with excellent solvent resistance compared to the industry standards.
Figure 5 shows gloss retention results for the topcoats only, applied to metal panels, and exposed to UV-A light in a QUV accelerated weathering cabinet. Also included in the test was a clear coating based on the polyester PUD used to make PUA-1. Although the PUD does not have excellent gloss retention by itself, blending it with an acrylic to form PUA-1 does not hurt the gloss retention of the blend.
In fact, all of the acrylic-based materials shown in Figure 5 performed well in UV-A exposure, including AC-1, and the commercial waterborne and solventborne acrylic topcoats used in the commercial systems COM-1 and COM-2. Of the five wood systems tested, only the nitrocellulose topcoat from COM-3 did poorly in UV-A exposure, showing a large drop in gloss after only 300 h. The nitrocellulose topcoat also yellowed significantly on exposure. In contrast, the acrylic systems maintained their gloss and color even after more than 900 hours. This result is perhaps not too surprising given the well known UV stability of acrylic polymers, but demonstrates a main benefit that an acrylic wood finish could provide.
Conclusions
A unique acrylic/polyurethane technology has been described that offers a new mechanism for the faster release of coalescent from industrial wood coatings. The combination of a hard acrylic phase and a soft polyurethane phase results in polymers that offer faster hardness development compared to the hard acrylic by itself. In addition, other properties that correlate with hardness, such as block, print and mar resistance, are improved. The key is the formation of a “percolation network” of the soft polyurethane throughout the dry coating. Volatile coalescents will diffuse faster through the soft polyurethane phase due to free volume effects, and the continuous network provides a pathway for the coalescent to escape more quickly. In addition to property improvements, the faster coalescent release shows promise for wood coating formulations with lower TVOC emissions, a characteristic sought by manufacturers of wood products such as furniture, cabinets and building materials, as well as their coatings suppliers. For example, the ability of a coating to release the majority of its volatile materials prior to the packaging and use of a piece of furniture should eventually lead to better indoor air quality for the consumer and a competitive advantage for the furniture manufacturer. The new acrylic/polyurethane technology described here offers those qualities in an environmentally advanced, one-component, low-VOC waterborne coating, and provides the coatings industry with a powerful tool for industrial wood coatings.
Acknowledgements
The authors would like to thank Dr. Lawrence Mink and Dr. Wei Xie from the Dow Analytical Sciences group for their assistance in the GC/MS analysis of residual coalescent and static chamber TVOC measurements.
This paper was presented at the 38th Annual Waterborne Symposium, February 2011 in New Orleans.
Looking for a reprint of this article?
From high-res PDFs to custom plaques, order your copy today!