Sustainability Secrets of Material Safety Data Sheets

What is a Material Safety Data Sheet (MSDS) and how does it fit into sustainability? This article will look at five key ways a company can use MSDS data to bolster its sustainability profile.
What is an MSDS?
An MSDS is exactly what it sounds like: a data sheet on material safety. They are also known simply as SDSs (Safety Data Sheets), but in the United States we still commonly use the MSDS moniker.All products with hazardous properties or elements will have an MSDS that you can, by law, obtain from the product’s manufacturing company or distributor.
Both Gartner Inc. and Aberdeen Group recently stated that companies wanting to use "environmental compliance" or "green" as a differentiator must first know which substances are in their products and product supply chain. Seeing product components and ingredients is called “visibility.”
This granular level of visibility into the chemicals in a product begins with an MSDS. This is good news, since MSDS data is usually accessible.
The MSDS and Paper
For any company, the first key question towards a more sustainable enterprise is: How much paper are we wasting?Michael Butler, Director of Environmental & Regulatory Affairs at Behr Process, touched on reducing paper waste in a related paper. “In 2001, Behr decided to move from a paper-based MSDS management system to an electronic MSDS system for all raw materials used in our paints, varnishes and coatings,” says Butler.
“The old paper system we used required a substantial amount of manpower (and the attendant energy) for maintenance and updates,” explains Butler. “There is a lot of information contained in an MSDS that is impractical to research in a paper-based system housed in multiple binders. Having documents readily accessible was an onerous task, since 20% of the MSDSs are revised each year. Revisions had to be copied, old versions removed, and new versions distributed and inserted. That’s a lot of paper juggling,” he adds.
That’s also a lot of unnecessary document generation and waste. Moving to a digital MSDS management solution is a more sustainable choice for almost any size company.
The MSDS and Purchasing Decisions
Sustainability is, in large part, what a company’s chemical footprint looks like. Are there a lot of pollutants coming out of the company – whether released through smokestacks or bundled into products? Many companies don’t realize that MSDSs contain data they can consolidate and use to analyze a chemical footprint, reduce it and report on it.Purchasing agents can request a product MSDS from the manufacturer before making bulk purchases. The benefit: save costs in disposal procedures, which are complicated for more hazardous products, and also mitigate employee safety, and health costs and risks.
You can use a simple numeric formula to arrive at actual figures for amounts of hazardous substances that your company kept out of the environment this year because of greener purchasing decisions.
Try this simple math: n containers of size x containing y% formaldehyde means your company saved the environment a specific amount z of hazardous substance. Just plug in the numbers: z = n(y% of x) where z is your conserved pollutants.
Obviously, these numbers and formulas can be spun by a more sophisticated software system. But you can start small and create sustainability metrics to feel good about.
If you are a purchasing agent buying raw materials in bulk, these numbers start to add up significantly and satisfyingly. As always, track what you avoided, saved and eliminated.
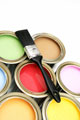
MSDS and Emissions
Manufacturers should always track decisions – however small – around replacing product ingredients with greener options. Here’s why: you can add up the results in emissions.The New York Times stated recently that “some commenters said the average company would need to spend between $100,000 and $850,000 on data management software” to meet emissions control standards. In fact, it doesn’t have to cost that much.
For instance, while still using your legacy processes and equipment, you can report on an estimated reduction in quantities of HAPs or VOCs emitted by even slightly modified ingredients. If you choose and purchase cleaner ingredients, the by-product comes out less hazardous to the air and ground.
Track it and report on it in press releases, Corporate Sustainability Reporting (CSR), or Toxic Release Inventory (TRI) reporting.
MSDS and EPA/TRI Reporting
Get credit for your sustainability efforts by reporting them. MSDS data, rolled up or taken one MSDS at a time, can help.“Required Federal reports include the more common industrial, such as the EPCRA TRI, report,” explains Michael Butler at Behr. EPCRA TRI stands for Emergency Planning and Right to Know Toxics Release Inventory. The TRI Program compiles the toxic release data on toxic chemical releases and waste management activities.
“People have a right to information that might affect their health and the health of their children, and EPA has a responsibility to provide it,” said EPA Administrator Lisa P. Jackson in April, 2009. “…TRI reporting requirements assure transparency and provides a crucial tool for safeguarding human health and the environment in our communities.”
“For these types of reports,” Butler says, “data can be extracted from the MSDS to list all the CAS (Chemical Abstract Service) numbers and ingredient percentages in use within each manufacturing location, along with the specific gravity/density,” he says.
Behr reports that for the past 10 years, the company has been using a web-based MSDS management system. The system simplifies many routine tasks and accomplishes the company’s MSDS responsibilities in near real-time.
“The system constitutes a best practices approach,” says Butler.
Conclusion
Because most companies already manage MSDSs in some way, it makes sense to combine data therein and regulatory mandates around chemicals, and to leverage MSDS data in a positive and meaningful way.The MSDS will help choose products and ingredients so that your company’s chemical footprint is less harmful. Simple math, well-managed MSDS data, and simple reporting can help you track and leverage these successes.
Sophisticated software? It works, but it’s not always required. Behr uses the Actio software system to manage its MSDS data; Actio being one of the more tenured solution purveyors in the substance data management space. This type of technology is certainly an option worth considering. The important thing is to start somewhere, even if just with a spreadsheet. Empower your organization with real data and real numbers. Regulatory challenges and increased enforcement and penalties created by EPA/TSCA, OSHA, CONEG, REACH, RoHS and GADSL guidelines are making it more cost effective to go green than ever before. The MSDS data you already have access to contains surprising and meaningful ways to enhance sustainability.
For more information, visit www.actio.net.
Looking for a reprint of this article?
From high-res PDFs to custom plaques, order your copy today!