Optical Film Formation Analysis
A new optical technology is presented, based on Multispeckle
Diffusing-Wave Spectroscopy, to study film formation from coatings.

Film formation of latex is described in the literature as a three/four stages process: Stage I: evaporation of water; Stage II: particle ordering or packing where the particles start to interact; Stage III: particle deformation where particles in a closed-packed array with water-filled interstices deform to reach a rhombic dodecahedron with no more water; Stage IV: interdiffusion across polymer/polymer boundaries to form a uniform film.
A new technique based on Multi Speckle Diffusing Wave Spectroscopy (MS-DWS) has recently been developed to study the film formation of coatings. In the case of latexes and most waterborne systems, the kinetics of film formation display a peculiar curve in four stages, which could correspond to the four stages detailed above.
In this work we present different experiments, which tend to prove that the four stages observed with this new technology fit well with the film formation of latexes as described in the literature. Different correlations with other techniques (gravimetric analysis, Raman confocal microscopy) are presented.
A wide range of characterization techniques have been used in the last years for research on coating drying, curing and film formation of latex1-4 (microscopy techniques, spectroscopy scattering and optical, thermal analysis, physical testing methods). For more routine analyses, the BK Drying Recorder is often used by paint manufacturers to extract characteristic drying times such as set-to-touch, tack-free or dry-hard times.5 Each of these above-mentioned techniques provides very useful information on film formation and drying processes. However, most of them are not capable of measuring the build-up of properties under realistic conditions of solvent evaporation and/or on the appropriate substrate.
We present here a new optical technique based on MultiSpeckle Diffusing-Wave Spectroscopy (MS-DWS)6-8 to study film formation of coatings. We studied a commercial coating and correlated the obtained film-formation kinetics with gravimetric analysis.

A laser light illuminates the coating sample; if the sample contains scattering materials (rough surface, latex particles, pigment particles, emulsion droplets, fibers, etc.), the photons are scattered by these objects bearing a different refractive index than the bulk. The scattered laser light is detected by a camera without lens; in these conditions, the camera monitor shows a peculiar image of granular appearance called “speckle” image 11,12 (Figure 1). When the sample undergoes a time-dependent activity, such as Brownian motion of particles inside a fluid or refractive index changes, the activity causes temporal fluctuations in the backscattered light and consequently changes of light intensity on the speckle image, i.e., intensity fluctuation of the speckle spots. A direct relation exists between the motion of scatterers inside the sample and the intensity fluctuations on the speckle image. Fast activity inside the sample generates fast changes of the backscattered light, and fast intensity fluctuations of the speckle spots. Inversely, a slow activity (slow motion of scatterers, slow changes of refractive index) induces slow changes of the backscattered light, and slow intensity fluctuations of the speckle spots.
In the case of a film-forming sample, the sample structure changes with time due for instance to solvent evaporation, chemical reaction, particle diffusion, etc., depending on the mechanism of film formation involved. The motion of scatterers slows down as the film progressively forms due to an increase of the film coherence and viscosity; as a consequence, the speed of the intensity fluctuations on the speckle image decreases with time. This will be referred to in this paper as the ‘fluidity factor’. The fluidity factor during a film-forming process can thus be measured and used to monitor structural changes in the drying coating sample.
The MS-DWS measurements were carried out using the Horus® Film Formation analyzer from Formulaction (France). The instrument is in a backscattering configuration; the camera sensor (CMOS) and the laser source are on the same side with respect to the analyzed sample and are gathered in a single measuring head. The laser source is a standard laser diode of power 0.9 mW and wavelength 655 nm. The camera is a standard 320x240 pixels sensor with a maximum frame rate of 30 images/s.
The samples were applied manually on the appropriate substrate. Just after casting the coating, the substrate was placed under the laser beam and the measurement started. The instrument bears four measuring heads allowing four simultaneous measurements of different samples.
Materials
Sample A was used to perform the experiments. It is a commercial coating based on an acrylic latex Tg -4 °C, density 1.04 g/mL, solid content 48% and particle size of 100 nm.
Sample A was spread manually using a stainless steel applicator (Doctor Blade type) giving a wet thickness of 120 microns. The coating was applied on a glass panel and the measurements were carried out at a relative humidity level of 40 ± 5%, and a temperature of 20 ± 1 °C.
Gravimetric Analysis
Weight loss measurements were performed on an analytical balance (Precisa XB 320M) coupled to a computer that recorded the weight as a function of time. The measurements were carried out simultaneously with the optical one on the same coating, placing the balance under the Horus®. Volume fraction of the latex was extracted from the weight loss in order to follow the packing of the latex particles during drying.
Confocal Raman Microscopy
Confocal Raman microscopy offers the possibility to acquire sample chemical information with a resolution down to the optical diffraction limit (~ 200 nm). This method allows analyzing the local distribution of different components within a sample in ambient conditions and without requiring any special sample preparation. Confocal Raman microscopy combines two different techniques, namely confocal microscopy and Raman spectrometry. In confocal microscopy a small pinhole sitting in conjunction to the focus of the objective allows only the light coming from the focal plane to pass into the detector. This focal plane can be moved a few micrometers into the sample, which gives the opportunity of gaining 3D information. Raman spectroscopy uses the effect of inelastic scattering of monochromatic light on molecules. Raman spectra show beside the elastic scattered light energy-shifted peaks, which are characteristic for the scattering molecule and result from the excitation of vibrations in the molecule. Performing Raman microscopy, a Raman spectrum is recorded on every image pixel. When analyzing dedicated peaks of the spectra, a variety of images can be generated using only a single set of data. Post-measuring data evaluation makes identification of different components in the sample possible.
The measurements were performed with a WITec alpha300 system, which has a lateral resolution of 200 nm and a vertical resolution of 500 nm. The scan range for one image was 150 x 50 μm2 using a 532 nm laser for excitation.
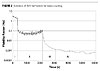
To explain the different variations observed on the kinetics,
gravimetric analysis of water loss was simultaneously performed on sample A.
The measurements of sample A are shown in Figure 3. The weight loss measured
with the balance was converted to volume fraction of latex as a function of
time. The wet content (52%) was assumed to be the value at T=0 for the
gravimetric analysis, and the assumption was made that all water had
disappeared when the balance showed a constant value. All experiments were
performed in duplicate in order to average the times and improve the
accuracy.
Times related to the different phases of MS-DWS kinetics and the
corresponding water-loss and latex volume fraction are reported in Table 1 and
Figure 3. The film-formation profile of sample A shows a film-forming process
in four main steps (Figure 2). Over the first 5 minutes (phase I), the fluidity
factor remains high (> 1 Hz) indicating fast motion of scatterers inside the
film. The fluidity factor decreases slowly as the water content goes from 52
wt.% to 43 wt.%. The volume fraction of latex is lower than 64%, indicating
that the scatterers are probably still well dispersed in bulk water. This first
phase corresponds to an evaporation
stage, i.e., the
water evaporates from the film surface, water molecules migrate from the liquid
to the atmosphere generating currents, hence fast Brownian motion of latex and
pigment particles.13-15
Raman confocal images of the coating during the evaporation stage, leads
to a blurred picture (Figure 4) as particle movements inside the film are too
quick.
At the beginning of phase II, a clear change appears on the kinetics with a sharp decrease of the signal, characteristic of an important increase of the viscosity of the system. This time, T1, fits well with the definition of the open time, which is described by Keddie1 as the stage where the viscosity reaches a critical value. It also correlates well with manual measurements of the open time.19 Phase II is characterized by accelerations and decelerations of the fluidity factor up to T2=35 minutes. During phase II, the water content continues to decrease from 43 wt.% to 11 wt.%. The evaporation rate is constant compared to phase I, as shown by the balance measurement (Figure 3). The volume fraction of latex increases up to 83 %, which fits with the formation of a close-packing array with deformable particle. The turbulent signal and the high concentration in solids indicate that scatterers start to interfere in the motion of each other; the particles rearrange and organize. Phase II can be defined as a packing stage. Such noisy signal has been observed as well on the MS-DWS experiments performed on a drying paint by Scheffold et al.15a It reflects temporally dynamics heterogeneities, i.e., scatterers moving at different speeds in the analyzed zone, strongly reminiscent of that of jammed colloids.15b
The Raman confocal microscopy image (Figure 5) shows that the particles
are clearly visible this time, compared to the evaporation stage. The movement
of the particles is therefore significantly reduced. This also correlates with
the packing stage, where particles are in close contact.
At the beginning of phase III, the fluidity factor decreases, sharply indicating a drastic reduction of the average motion speed of scatterers inside the sample. The water content in the film goes from 11 wt.% to 7-8 wt.%, and further on to 0% in phase IV, assuming that all the water has escaped from the film when the balance shows a constant value (Figure 3). At the beginning of phase III, we can assume that the water content (11 wt.%) corresponds only to interstitial water remaining in the film. The drastic reduction of the scatterers mobility can be attributed to the disappearance of the bulk water, close-packing of particles being reached, and the particles deformation to reach a rhombic dodecahedron (RDC) system. During phase III, the kinetics profile shows a sharp and smooth decrease of the fluidity factor up to 50 minutes. This is also consistent with literature1, where the third stage of the latex film formation, described as the particle deformation stage, is closely linked to the visco-elastic properties of the latex.
The continuous reduction of the scatterers’ motion after the total evaporation of water in phase IV indicates a continuous increase of the film coherence. It can last days. Phase IV observed on the kinetics of sample A can be defined as an interdiffusion stage.
Film formation of latex coatings has been intensively studied over the
past 20 years, but the complete mechanism is still subject to interrogations
and different theories are proposed to attempt to explain the film-formation of
such systems.16-18 Current understanding of film formation from
latex coatings consists of 4 stages: (i) the first stage is described as an
evaporation stage where particles are still free to move; (ii) the second stage
corresponds to the particle ordering or packing stage, i.e., particles
immobilize by multiple contacts with one another when solvent evaporates; (iii)
the third stage consist in compaction or deformation of particles to fill the
voids left by water evaporation, i.e., elimination of pore spaces by
progressive flattening and rearrangements of particles; (iv) the final stage is
a ‘coalescence’ stage, i.e., fusion of particles due to interdiffusion of the
polymer through particle-particle boundaries.18
The different phases of the MS-DWS kinetics of sample A indicate that the motion of scatterers inside the sample seems to correlate well with what is described in the literature. Figure 6 gives a schematic representation and our interpretation of the different phases observed on the kinetics: (I) concentration upon bulk water evaporation, (II) rearrangement and packing of particles, (III) particle deformation by evaporation of interstitial water, and (IV) interdiffusion/coalescence processes between the latex particles.
This paper was presented at The Waterborne Symposium sponsored by The University of Southern Mississippi School of Polymers and High Performance Materials and The Southern Society for Coatings Technology, 2009, New Orleans, LA.

Film formation of latex is described in the literature as a three/four stages process: Stage I: evaporation of water; Stage II: particle ordering or packing where the particles start to interact; Stage III: particle deformation where particles in a closed-packed array with water-filled interstices deform to reach a rhombic dodecahedron with no more water; Stage IV: interdiffusion across polymer/polymer boundaries to form a uniform film.
A new technique based on Multi Speckle Diffusing Wave Spectroscopy (MS-DWS) has recently been developed to study the film formation of coatings. In the case of latexes and most waterborne systems, the kinetics of film formation display a peculiar curve in four stages, which could correspond to the four stages detailed above.
In this work we present different experiments, which tend to prove that the four stages observed with this new technology fit well with the film formation of latexes as described in the literature. Different correlations with other techniques (gravimetric analysis, Raman confocal microscopy) are presented.
Introduction
Film formation control and understanding is of great importance for coating manufacturers and raw material suppliers. They have to innovate constantly to provide new, high-performance products to comply with the recent European Union environmental legislations. These new formulations are based on different chemistries, hence undergo different film-formation processes compared to the classical solvent-based formulas, leading to different final properties of the coating.A wide range of characterization techniques have been used in the last years for research on coating drying, curing and film formation of latex1-4 (microscopy techniques, spectroscopy scattering and optical, thermal analysis, physical testing methods). For more routine analyses, the BK Drying Recorder is often used by paint manufacturers to extract characteristic drying times such as set-to-touch, tack-free or dry-hard times.5 Each of these above-mentioned techniques provides very useful information on film formation and drying processes. However, most of them are not capable of measuring the build-up of properties under realistic conditions of solvent evaporation and/or on the appropriate substrate.
We present here a new optical technique based on MultiSpeckle Diffusing-Wave Spectroscopy (MS-DWS)6-8 to study film formation of coatings. We studied a commercial coating and correlated the obtained film-formation kinetics with gravimetric analysis.

Measurement Principle
We developed an original MS-DWS technique using a simple and direct processing of the backscattered light. This innovative processing, embedded since 2006 in a commercially available instrument (see experimental section) and patented, is named Adaptive Speckle Imaging Interferometry or A.S.I.I.9,10 The set-up of the MS-DWS experiment is presented in Figure 1.A laser light illuminates the coating sample; if the sample contains scattering materials (rough surface, latex particles, pigment particles, emulsion droplets, fibers, etc.), the photons are scattered by these objects bearing a different refractive index than the bulk. The scattered laser light is detected by a camera without lens; in these conditions, the camera monitor shows a peculiar image of granular appearance called “speckle” image 11,12 (Figure 1). When the sample undergoes a time-dependent activity, such as Brownian motion of particles inside a fluid or refractive index changes, the activity causes temporal fluctuations in the backscattered light and consequently changes of light intensity on the speckle image, i.e., intensity fluctuation of the speckle spots. A direct relation exists between the motion of scatterers inside the sample and the intensity fluctuations on the speckle image. Fast activity inside the sample generates fast changes of the backscattered light, and fast intensity fluctuations of the speckle spots. Inversely, a slow activity (slow motion of scatterers, slow changes of refractive index) induces slow changes of the backscattered light, and slow intensity fluctuations of the speckle spots.
In the case of a film-forming sample, the sample structure changes with time due for instance to solvent evaporation, chemical reaction, particle diffusion, etc., depending on the mechanism of film formation involved. The motion of scatterers slows down as the film progressively forms due to an increase of the film coherence and viscosity; as a consequence, the speed of the intensity fluctuations on the speckle image decreases with time. This will be referred to in this paper as the ‘fluidity factor’. The fluidity factor during a film-forming process can thus be measured and used to monitor structural changes in the drying coating sample.
Experimental
MS-DWS ExperimentsThe MS-DWS measurements were carried out using the Horus® Film Formation analyzer from Formulaction (France). The instrument is in a backscattering configuration; the camera sensor (CMOS) and the laser source are on the same side with respect to the analyzed sample and are gathered in a single measuring head. The laser source is a standard laser diode of power 0.9 mW and wavelength 655 nm. The camera is a standard 320x240 pixels sensor with a maximum frame rate of 30 images/s.
The samples were applied manually on the appropriate substrate. Just after casting the coating, the substrate was placed under the laser beam and the measurement started. The instrument bears four measuring heads allowing four simultaneous measurements of different samples.
Materials
Sample A was used to perform the experiments. It is a commercial coating based on an acrylic latex Tg -4 °C, density 1.04 g/mL, solid content 48% and particle size of 100 nm.
Sample A was spread manually using a stainless steel applicator (Doctor Blade type) giving a wet thickness of 120 microns. The coating was applied on a glass panel and the measurements were carried out at a relative humidity level of 40 ± 5%, and a temperature of 20 ± 1 °C.
Gravimetric Analysis
Weight loss measurements were performed on an analytical balance (Precisa XB 320M) coupled to a computer that recorded the weight as a function of time. The measurements were carried out simultaneously with the optical one on the same coating, placing the balance under the Horus®. Volume fraction of the latex was extracted from the weight loss in order to follow the packing of the latex particles during drying.
Confocal Raman Microscopy
Confocal Raman microscopy offers the possibility to acquire sample chemical information with a resolution down to the optical diffraction limit (~ 200 nm). This method allows analyzing the local distribution of different components within a sample in ambient conditions and without requiring any special sample preparation. Confocal Raman microscopy combines two different techniques, namely confocal microscopy and Raman spectrometry. In confocal microscopy a small pinhole sitting in conjunction to the focus of the objective allows only the light coming from the focal plane to pass into the detector. This focal plane can be moved a few micrometers into the sample, which gives the opportunity of gaining 3D information. Raman spectroscopy uses the effect of inelastic scattering of monochromatic light on molecules. Raman spectra show beside the elastic scattered light energy-shifted peaks, which are characteristic for the scattering molecule and result from the excitation of vibrations in the molecule. Performing Raman microscopy, a Raman spectrum is recorded on every image pixel. When analyzing dedicated peaks of the spectra, a variety of images can be generated using only a single set of data. Post-measuring data evaluation makes identification of different components in the sample possible.
The measurements were performed with a WITec alpha300 system, which has a lateral resolution of 200 nm and a vertical resolution of 500 nm. The scan range for one image was 150 x 50 μm2 using a 532 nm laser for excitation.
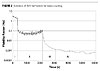
Results and Discussion
The film-formation process of a water-based latex coating, sample A, was studied using our MS-DWS technique. The kinetics is shown in Figure 2.
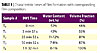
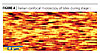
At the beginning of phase II, a clear change appears on the kinetics with a sharp decrease of the signal, characteristic of an important increase of the viscosity of the system. This time, T1, fits well with the definition of the open time, which is described by Keddie1 as the stage where the viscosity reaches a critical value. It also correlates well with manual measurements of the open time.19 Phase II is characterized by accelerations and decelerations of the fluidity factor up to T2=35 minutes. During phase II, the water content continues to decrease from 43 wt.% to 11 wt.%. The evaporation rate is constant compared to phase I, as shown by the balance measurement (Figure 3). The volume fraction of latex increases up to 83 %, which fits with the formation of a close-packing array with deformable particle. The turbulent signal and the high concentration in solids indicate that scatterers start to interfere in the motion of each other; the particles rearrange and organize. Phase II can be defined as a packing stage. Such noisy signal has been observed as well on the MS-DWS experiments performed on a drying paint by Scheffold et al.15a It reflects temporally dynamics heterogeneities, i.e., scatterers moving at different speeds in the analyzed zone, strongly reminiscent of that of jammed colloids.15b

At the beginning of phase III, the fluidity factor decreases, sharply indicating a drastic reduction of the average motion speed of scatterers inside the sample. The water content in the film goes from 11 wt.% to 7-8 wt.%, and further on to 0% in phase IV, assuming that all the water has escaped from the film when the balance shows a constant value (Figure 3). At the beginning of phase III, we can assume that the water content (11 wt.%) corresponds only to interstitial water remaining in the film. The drastic reduction of the scatterers mobility can be attributed to the disappearance of the bulk water, close-packing of particles being reached, and the particles deformation to reach a rhombic dodecahedron (RDC) system. During phase III, the kinetics profile shows a sharp and smooth decrease of the fluidity factor up to 50 minutes. This is also consistent with literature1, where the third stage of the latex film formation, described as the particle deformation stage, is closely linked to the visco-elastic properties of the latex.
The continuous reduction of the scatterers’ motion after the total evaporation of water in phase IV indicates a continuous increase of the film coherence. It can last days. Phase IV observed on the kinetics of sample A can be defined as an interdiffusion stage.

The different phases of the MS-DWS kinetics of sample A indicate that the motion of scatterers inside the sample seems to correlate well with what is described in the literature. Figure 6 gives a schematic representation and our interpretation of the different phases observed on the kinetics: (I) concentration upon bulk water evaporation, (II) rearrangement and packing of particles, (III) particle deformation by evaporation of interstitial water, and (IV) interdiffusion/coalescence processes between the latex particles.
Conclusion
We have presented a new optical technology, based on Multispeckle Diffusing-Wave Spectroscopy, to study film formation from coatings. This technology monitors and displays in real time the motion of scatterers (particles, droplets, interfaces) inside the sample as a function of time. Measurements have been performed on a water-based formulation and have been compared with gravimetric analysis. Raman confocal microscopy was also carried out during the film formation, giving evidences of the film-forming process. Four phases are systematically observed in the film-formation kinetics of water-based coatings and have been identified as evaporation (I), packing (II), particle deformation (III) and interdiffusion (IV) phases, as described in the literature. The different changes in slope and shape observed in the kinetics could be related to changes in the film structure. The measurement is simple to perform: the coating is cast on a substrate (any kind of coating can be used), placed under the laser beam and the measurement is started without any required calibration or set-up parameters. This new MS-DWS technique, coupled to our A.S.I.I. processing, is an original and nonintrusive tool to investigate film formation processes in representative conditions, thus providing unique and complementary information compared to existing techniques and objectively determining open-time on appropriate substrates.This paper was presented at The Waterborne Symposium sponsored by The University of Southern Mississippi School of Polymers and High Performance Materials and The Southern Society for Coatings Technology, 2009, New Orleans, LA.
Looking for a reprint of this article?
From high-res PDFs to custom plaques, order your copy today!