Thirty Days to Coat a Bridge
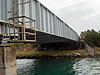
Since the World War II era, desiccant dehumidification technology has been utilized to protect technical equipment and ocean-going cargo from the negative effects of corrosion. In fact, the use of desiccant dehumidifiers has been the backbone of the structural remediation industry in the wake of devastating hurricanes and floods for nearly half a century.
In the early 1980s, the technology was introduced to the coatings industry as a method to help control flash rusting, enabling the applicator to provide a superior finish even in the harshest environments. This new process provided a solution to owners and contractors combating the most complex of challenges – controlling Mother Nature.
Over the last 30 years, this technology has transformed itself into a sophisticated and mainstream method that is utilized in many blasting and coating applications completed today.
One such example is a project for the Onslow Beach Bridge, a 210-foot-long, 40-foot-wide bridge near Camp Lejeune, NC, used by service members, retirees and employees assigned to Marine Corps Base Camp Lejeune, Marine Corps Air Station New River, and Marine Corps Air Station Cherry Point.
The bridge, which traverses the Atlantic Intracoastal Waterway, was long overdue for a paint job to better protect it from corrosion and increase its longevity. The project scope mandated that the bridge be sandblasted and painted, and have its rivets and bearing pad replaced. The U.S. Marine Corps of engineers who oversaw the project stipulated that the work be completed in 30 days due to training and other exercises scheduled a month later that required use of the bridge.
The painting contractor hired a moisture control and water damage recovery firm to handle the temporary humidity control portion of the project during the 30-day timeframe.
The specification requirements for the Onslow Beach Bridge included a near-white SSPC-SP 10 blast with grit abrasive to remove all of the previous coatings, followed by the use of a zinc epoxy primer with a 2-3 mil paint thickness to serve as the anti-corrosion base. After the primer, the project specified application of an intermediate epoxy of 6-8 mils thickness. Finally, the project required application of a coat of 2-3 mil thickness polyurethane to serve as the finish coat. Following the coatings, a test needed to be conducted to make sure the application thicknesses were accurate.
In total, 78,000 total square feet of area would be high pressure washed, blasted, and coated inside a 240,000 cubic feet containment area. In my experience, under normal conditions, a contractor would prefer about 60 days to complete a project of this size and scope. The challenge was to create the optimal conditions inside the containment to fast track completion of the project in 30 days or face penalties for missing the demanding deadline.

Creating an Ideal Environment
The general concept behind the use of temporary dehumidification equipment in a steel coating application is to create an optimum differential between the dew point temperature in the space and the temperature of the actual surface. If the surface temperature reaches the interior dew point temperature, moisture vapor from the air will condense on the surface. This condensation can lead to flash rusting, inter-coat adhesion problems and related curing issues. Additionally, the temporary system is designed to create a climate that is conducive for the proper curing of the coating.Most coating manufacturers’ data sheets recommend ideal conditions in which to apply the coatings. If the temperature is too high or too low, the coating can be subject to curing issues, improper wetting out of the coatings material and adhesion problems. Condensation, temperature extremes and curing problems can create expensive delays, rework and warranty repair costs that can impact the overall service life of the project. The temporary climate control system helps maintain all environmental conditions that should lead to a successful coating application. In theory, if all is done in accordance to the manufacturer’s specifications for application and environmental controls, the coating will provide a long, productive service life.
The rate of corrosion is dependent upon the amount of moisture present. For example, moisture at levels below 50% will produce less corrosion than at 70%. Moisture levels above 50% create conditions that accelerate corrosion exponentially, leading to flash rusting. As such, the key to corrosion control is to control the moisture level.
The Onslow Beach Bridge project required that desiccant dehumidification equipment maintain a minimum 5
Desiccant Dehumidification Benefits
Desiccant dehumidification is the “work horse” for moisture removal from the air. This process consists of drawing ambient air through a desiccant substrate, which captures moisture from the air within a wheel. This process is called adsorption. In desiccant dehumidification systems, the desiccant support structure is a wheel. The desiccant – a titanium-enhanced silica gel – is infused into a corrugated composite material that resembles the honeycombs of a beehive and this is formed into a wheel.The saturated wheel is then dried by a separate heated air stream to reactivate the wheel. The air is delivered to the space at extremely low dew points and relative humidity levels. Depending on the time of the year that the project is occurring, care should be taken to control the temperatures in the interior area. A direct expansion (DX) package customized air conditioning unit can be combined with the desiccant to optimize the controlled climate.
The benefits of using temporary climate control equipment during blast and coating applications can be summed in two key areas: cost savings and quality. Creating conditions that will reduce corrosion growth has a direct impact on the cost savings for the overall project. Increased productivity from limited blast and coat cycles create significant cost savings due to reduced down times. The ability to reduce the overall man hours on the project, reduce rental equipment days and reduce waste easily justifies the use of the temporary climate control equipment.
The second benefit and possibly the most important is one of improved quality. Temporary climate control will provide the perfect conditions that will enhance the blasting, application and curing of the products being applied. Temporary climate control can reduce the spikes caused by regular fluctuations from fast-moving weather patterns such as cold or warm fronts or from day to night transitions. In essence, the coating needs to be applied to a well-prepared surface at the optimum temperature and humidity range for application and curing, to expect a system with a longer life expectancy. Additionally, a better-applied system overall will possibly lead to less warranty rework that can negatively affect the profitability of a project.
Utilizing Innovative Equipment for Energy Savings
For the Onslow Beach Bridge, it was determined that use of an energy-efficient and highly-effective desiccant drying system would allow the customer to save on generator fuel costs due to the lower amperage draw and smaller generator requirements. Use of a humidity control unit (HCU)-6000 pre-cooled with a 12.5 ton A/C system allowed the one-third sections of the containment concentrations to be maintained and in specification for the required periods.The HCU combines cooling and desiccant dehumidification technologies in one energy-efficient system to control dew point temperatures, even in hot, humid climates. The system operates cost effectively because all of the energy required for the regeneration of the desiccant wheel is recovered from the normally wasted condenser waste heat.
In order to document and verify that the conditions written in the specifications were met, a proprietary monitoring system provided by the DH manufacturer was utilized to record and graph conditions both inside and outside the containment.
Highlighting the unpredictability of Mother Nature, on the first day of the project, record heat waves struck the East Coast of the United States. For two weeks outside temperatures soared into the 100s and still the stringent parameters were maintained and the project was finished on time and on budget.
The amperage loads for the equipment used on this project were 99 full load amp requiring an 80 kw generator. Based on a 75% power factor at $5 per gallon the fuel cost would run approximately $14,000 for the month. If the contractor attempted to achieve the same results using straight dehumidification and direct expansion (DX) systems, two 30 ton DX units to pre and post cool an HC-4500 cfm dehumidifier would be needed. This amperage draw totals 278 full load amp and would require a 225kw generator.
Based on a 75% power factor and fuel at $5 per gallon, the fuel cost for a system without a desiccator for one month would be roughly $39,000. Thus, the fuel savings alone for this project were nearly three times the total cost of the equipment rental.
Innovative Remote Monitoring Equipment Key
An integral part of the Onslow Bridge job was use of an innovative technology for monitoring temporary dehumidification equipment on job sites. The ExactAire system from MCS allows technicians to conveniently monitor and configure the operation of temporary dehumidification, cooling and heating equipment remotely via a secure website.This online monitoring system keeps a virtual chart of the conditions inside the containment to verify that the specifications were maintained for painting inspectors and government executives. The data also can be used for any warranty or litigation issues that might arise. It measures both the conditions inside and outside the containment and the information is beamed to a satellite that is linked to the Internet so users can log in and monitor from an office or other remote location.
The detailed messages include the recorded conditions, and the location, make, model and serial number of the unit involved. Alert messages are completely customizable, allowing the user to choose whether alert messages are delivered via a pager, PC, e-mail, or text message on a cellular telephone.
With a password, the user can access the recorded conditions on the website and download them to a text or PDF file. This provides immediate access to accurate conditions recorded on the job that are less than 60 minutes old.
The system features a variety of benefits for users. For example, climate control settings can be changed at any time remotely from a secure website.
If a user wants to change the dew point spread that controls the dehumidifier, the technician can do that on the website and the system will download the new configuration to the climate control unit in the field. A notification will alert the technician if the system is not holding the appropriate temperature or dew point.
Often no one realizes a generator has failed until the damage has already occurred. A battery backup enables the remote monitoring technology to send a “power failure” message if the generator shuts down or if there is any loss of power.
The system relays a message when the surface temperature is approaching the dew point, or if the tank is out of the humidity range specified. In such cases, timely repairs can be made before desired conditions in the controlled space are lost.
There also is a cost benefit because the technology has the ability to turn the dehumidifier on and off based on the difference between the dew point and the surface temperature. Because the unit is modulated on and off to maintain conditions, significant fuel savings can be realized such as was the case during this project.
Summary
Temporary climate control is becoming a regular part of blasting and coating projects within the industry. Its ability to create improved coatings conditions and provide cost savings and quality workmanship to the owner and contractor is making it a popular method from a business viewpoint as well.For the Onslow Beach Bridge assignment, desiccant dehumidification played a major role in on-time completion of the project and resulted in significant energy savings. Testing afterward proved that all coating applications had passed for desired thickness and application strength.
The success of a temporary system rides heavily on the specification and how it is written, and significant savings can be achieved through the implementation of energy-efficient equipment and the use of monitoring devices. Electronic monitoring devices also add a level of comfort and control for all parties involved.
For further information, contact Benjamin Arens at barens@lcwa.com or 312/565.4626.
Looking for a reprint of this article?
From high-res PDFs to custom plaques, order your copy today!