Cleaning Up in the Coating Business
A giant in the industrial-construction coating business, Henry Company optimizes production, minimizes labor and mess with a self-cleaning filter that virtually eliminates production stoppage due to filter cleaning and blocking.
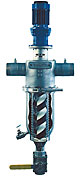
As a world leader in special industrial coatings and emulsions and the largest North American manufacturer of roof coatings and cements, Henry Company is no stranger to success, thanks to its focus on making customers’ jobs easier. For instance, to prevent contractor downtime on home or commercial jobsites due to clogged spray nozzles, the company proactively filters its asphalt-based roof, foundation and construction surface spray products to remove contaminants up to three times smaller than the tip of the sprayer.
While the company traditionally filtered its asphalt-based coating products with a metal blade-style filter, it saw room for improvement, particularly on the process and production side. “Our system filtered adequately, but was an aggravation to work with,” says Rick Baker, Henry Company’s Director of Engineering. Production bottlenecks occurred twice a day when two operators took up to an hour to clean or change the filter screen between batches. Four bolts had to be unscrewed, the housing dropped down and held, while 40 lbs. of oversize asphalt contaminant was poured into a bucket for reuse in another mix process. Finally, the unit had to be reassembled. The filter cleaning and changing process was messy, requiring the use of protective coverall suits and the spreading of splashguards on the floor.
To streamline production, clean up the work environment and enhance employee morale, Baker decided to conduct a one-week trial of a state-of-the-art, self-cleaning capable Eco Filter system from Russell Finex. Since the self-cleaning Russell Eco Filter system integrates directly into the pipeline, it eliminates labor-intensive manual cleaning tasks such as changing filter bags or cleaning filtration baskets. The filter element is kept continuously clean via a unique spiral wiper design, ensuring optimum filtration efficiency. Because of its design, cleaning the filter between batch runs is quick and easy with minimal disruption during production changeovers. Additionally, a unique Q-Tap valve allows the sampling of freshly filtered material so quality can be easily monitored on the fly without interrupting production.
"The trial didn't require a site visit, but Russell Finex sent a rep to ensure they understood our manufacturing process and any issues we had," says Baker. While the filter offered a filter management system capable of operation without operator involvement, Baker chose a configuration with an operator-controlled purge valve, well suited for batch operation. With an ability to drain oversize material before a filter change, the purge valve minimized spillage and aided material recovery for easy reuse directly back to the mixer.
"Our process downtime virtually disappeared because the filter cleaned itself and discharged oversize quickly and cleanly through the purge valve," says Baker. "In about 15 seconds, a single operator could empty oversize in a bucket for reuse. No mess, no bother, no coverall suit. Our lab confirmed the filter did its job."
When Henry Company purchased its own Eco Filter, "we immediately put it into production since any issues were worked out in the trial run," says Baker. Compared to previous manually cleaned filters, the Russell Eco Filter is saving the company a substantial amount of downtime, labor and even capital outlay cost.
"The Eco Filter has eliminated a production bottleneck so we're able to go from batch to batch without slowing down," says Baker. "It allows us to quickly, cleanly rework purge materials back into the product stream, and will save us about 500 hours of labor and $10,000 in labor costs this year. Since using a mobile stand lets us move the filter between three mix stations, it's also doing the work of three fixed location filters at a fraction of the cost."
Henry Company's operations staff appreciates the self-cleaning filter because it prevents the potential back strain or sprain of manually cleaning asphalt oversize from heavy filters, and allows them to wear standard personal protective equipment rather than cumbersome coverall suits. Since all material is drained from the filter purge valve prior to a filter change, it further reduces the potential for spill or splatter.
"Because our employees get the job done better, faster and cleaner with the self-cleaning filter, they love it," says Baker. "When customers walk in they say, 'Wow, do you do roof coatings here?' They see we're on top of our process and know if we're this clean internally, our product is clean and to spec too."
Baker notes another benefit from switching to the self-cleaning filter: he's spending much less time doing maintenance and repair. "With the manually cleaned filters, I was constantly chasing parts: wipe blades, housing brackets, filter elements and such," says Baker. "With the Eco Filter, I haven't yet had an outage, downtime or a need for replacement parts. And there have been no complaints from end customers."
As companies like Henry Company are discovering, the self-cleaning Russell Eco Filter fits neatly into existing production lines, in many instances adding significant capacity without requiring excessive space. Because it’s totally enclosed, it also prevents outside pollutants from contaminating product and protects operators from any spillage or fumes. Users see substantial improvement in product purity, throughput and waste elimination; and a choice of easily swapped filter elements can give additional flexibility to meet the quality demands of customers.
"The self-cleaning filter has added significantly to our bottom line and helped us toward our goal of continuous improvement," concludes Baker. "Manufacturers with continuous processes, especially those with high amounts of oversize or contaminant, could benefit even more."
For over 70 years Russell Finex has manufactured and supplied filters, screeners and separators to improve product quality, enhance productivity, safeguard worker health, and ensure powders and liquids are contamination-free. Throughout the world, Russell Finex serves a variety of industries with applications including coatings, food, pharmaceuticals, chemicals, adhesives, plastisols, metal powders and ceramics.
For more information contact Russell Finex, Inc., PO Box 69, Pineville, NC 28134; phone 704/588.9808; fax: 704/588.0738; e-mail sales@russellfinexinc.com; or visit the www.russellfinexusa.com.
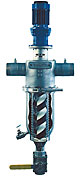
As a world leader in special industrial coatings and emulsions and the largest North American manufacturer of roof coatings and cements, Henry Company is no stranger to success, thanks to its focus on making customers’ jobs easier. For instance, to prevent contractor downtime on home or commercial jobsites due to clogged spray nozzles, the company proactively filters its asphalt-based roof, foundation and construction surface spray products to remove contaminants up to three times smaller than the tip of the sprayer.
While the company traditionally filtered its asphalt-based coating products with a metal blade-style filter, it saw room for improvement, particularly on the process and production side. “Our system filtered adequately, but was an aggravation to work with,” says Rick Baker, Henry Company’s Director of Engineering. Production bottlenecks occurred twice a day when two operators took up to an hour to clean or change the filter screen between batches. Four bolts had to be unscrewed, the housing dropped down and held, while 40 lbs. of oversize asphalt contaminant was poured into a bucket for reuse in another mix process. Finally, the unit had to be reassembled. The filter cleaning and changing process was messy, requiring the use of protective coverall suits and the spreading of splashguards on the floor.
To streamline production, clean up the work environment and enhance employee morale, Baker decided to conduct a one-week trial of a state-of-the-art, self-cleaning capable Eco Filter system from Russell Finex. Since the self-cleaning Russell Eco Filter system integrates directly into the pipeline, it eliminates labor-intensive manual cleaning tasks such as changing filter bags or cleaning filtration baskets. The filter element is kept continuously clean via a unique spiral wiper design, ensuring optimum filtration efficiency. Because of its design, cleaning the filter between batch runs is quick and easy with minimal disruption during production changeovers. Additionally, a unique Q-Tap valve allows the sampling of freshly filtered material so quality can be easily monitored on the fly without interrupting production.
"The trial didn't require a site visit, but Russell Finex sent a rep to ensure they understood our manufacturing process and any issues we had," says Baker. While the filter offered a filter management system capable of operation without operator involvement, Baker chose a configuration with an operator-controlled purge valve, well suited for batch operation. With an ability to drain oversize material before a filter change, the purge valve minimized spillage and aided material recovery for easy reuse directly back to the mixer.
"Our process downtime virtually disappeared because the filter cleaned itself and discharged oversize quickly and cleanly through the purge valve," says Baker. "In about 15 seconds, a single operator could empty oversize in a bucket for reuse. No mess, no bother, no coverall suit. Our lab confirmed the filter did its job."
When Henry Company purchased its own Eco Filter, "we immediately put it into production since any issues were worked out in the trial run," says Baker. Compared to previous manually cleaned filters, the Russell Eco Filter is saving the company a substantial amount of downtime, labor and even capital outlay cost.
"The Eco Filter has eliminated a production bottleneck so we're able to go from batch to batch without slowing down," says Baker. "It allows us to quickly, cleanly rework purge materials back into the product stream, and will save us about 500 hours of labor and $10,000 in labor costs this year. Since using a mobile stand lets us move the filter between three mix stations, it's also doing the work of three fixed location filters at a fraction of the cost."
Henry Company's operations staff appreciates the self-cleaning filter because it prevents the potential back strain or sprain of manually cleaning asphalt oversize from heavy filters, and allows them to wear standard personal protective equipment rather than cumbersome coverall suits. Since all material is drained from the filter purge valve prior to a filter change, it further reduces the potential for spill or splatter.
"Because our employees get the job done better, faster and cleaner with the self-cleaning filter, they love it," says Baker. "When customers walk in they say, 'Wow, do you do roof coatings here?' They see we're on top of our process and know if we're this clean internally, our product is clean and to spec too."
Baker notes another benefit from switching to the self-cleaning filter: he's spending much less time doing maintenance and repair. "With the manually cleaned filters, I was constantly chasing parts: wipe blades, housing brackets, filter elements and such," says Baker. "With the Eco Filter, I haven't yet had an outage, downtime or a need for replacement parts. And there have been no complaints from end customers."
As companies like Henry Company are discovering, the self-cleaning Russell Eco Filter fits neatly into existing production lines, in many instances adding significant capacity without requiring excessive space. Because it’s totally enclosed, it also prevents outside pollutants from contaminating product and protects operators from any spillage or fumes. Users see substantial improvement in product purity, throughput and waste elimination; and a choice of easily swapped filter elements can give additional flexibility to meet the quality demands of customers.
"The self-cleaning filter has added significantly to our bottom line and helped us toward our goal of continuous improvement," concludes Baker. "Manufacturers with continuous processes, especially those with high amounts of oversize or contaminant, could benefit even more."
For over 70 years Russell Finex has manufactured and supplied filters, screeners and separators to improve product quality, enhance productivity, safeguard worker health, and ensure powders and liquids are contamination-free. Throughout the world, Russell Finex serves a variety of industries with applications including coatings, food, pharmaceuticals, chemicals, adhesives, plastisols, metal powders and ceramics.
For more information contact Russell Finex, Inc., PO Box 69, Pineville, NC 28134; phone 704/588.9808; fax: 704/588.0738; e-mail sales@russellfinexinc.com; or visit the www.russellfinexusa.com.
Looking for a reprint of this article?
From high-res PDFs to custom plaques, order your copy today!