Milling Media Review - Part 1
This article reviews the effects of bead density. It is not intended to be an absolute guide or a scientific paper, but rather to highlight important factors and potential consequences for bead mill operation.
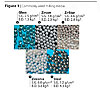
The choice of correct media is critical to efficient mill operation. An important factor in this regard is the density of the media itself. The following discussion reviews some of the main considerations and effects of “bead density”.

SE = r.V2.d3, where r= bead density, V = rotational speed and d = bead diameter
An additional consideration is the number of critical incidents that occur. This is known as the “Stress Number” (SN).
The Specific Milling Energy (Esp) needed to produce a certain mass of product is the energy supplied to the mill, related to the mass of solid particles processed. It is also proportional to the product of SE and SN.1
Esp ¥ SE.SN.EM.FE, where EM = energy supplied, FE = efficiency factor


With a 2.5 density bead, the positive force is too small to overcome the drag effect; the bead flows with the product, and grinding is ineffective. With a 4.0 density bead, the positive force is dominant and grinding is effective (Figure 4).
To compare the effects of variation in density, we can review a simplified situation where the conditions are static. We can consider the positive force to be reflective of the settling rate of the bead in a liquid. The settling rate, R, is given by:
R = 2 r2 g [r(bead) – r (liquid)] / 9h
The settling rate is affected by the viscosity and density of the liquid, bead size and bead density.
If we consider a 1 mm bead, then theoretical settling rates in a liquid of SG 1.5 and viscosity 1500 cps should be (Figure 5):



ZirPro is in a unique position with a range of products within an effective band of suitable bead densities as shown in Figure 8.
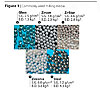
Bead Densities
Today there are numerous agitator mill designs used in microgrinding and dispersion applications. These mills use an ever-expanding range of milling media. Figure 1 details some of the more common types available.The choice of correct media is critical to efficient mill operation. An important factor in this regard is the density of the media itself. The following discussion reviews some of the main considerations and effects of “bead density”.

Milling Actions
Grinding, or de-agglomeration, is affected by impact, pressure and shear forces between grinding media and mill parts. Depending on the mill type, one of these forces can be the dominant grinding/dispersing action (Figure 2). In each situation there is a critical energy required to break the target particles. This “Stress Energy” (SE) is directly proportional to the bead density.SE = r.V2.d3, where r= bead density, V = rotational speed and d = bead diameter
An additional consideration is the number of critical incidents that occur. This is known as the “Stress Number” (SN).
The Specific Milling Energy (Esp) needed to produce a certain mass of product is the energy supplied to the mill, related to the mass of solid particles processed. It is also proportional to the product of SE and SN.1
Esp ¥ SE.SN.EM.FE, where EM = energy supplied, FE = efficiency factor

Bead Effects
Beads are accelerated by rotation of the machine’s discs or pegs, and the rate of acceleration (radial/tangential) is directly proportional to the density of the bead (Figure 3). Additionally, beads encounter drag effects from the product itself, e.g., liquid density, viscosity and flow rate. The bead resistance to this drag is critical to the efficiency of the grinding/dispersing process. If the drag effect is too great, grinding efficiency can drop; in extreme cases the beads can “hydraulically” pack, further limiting milling efficiency and severely increasing bead wear. Bead density is a major factor in overcoming the drag effect.
Effective Forces
There are positive and negative forces acting on the bead. The positive, due to acceleration and bead mass, contributes to the milling action. The negative, due to drag, disrupts the milling action. For effective grinding, the positive forces need to be larger than the negative forces.With a 2.5 density bead, the positive force is too small to overcome the drag effect; the bead flows with the product, and grinding is ineffective. With a 4.0 density bead, the positive force is dominant and grinding is effective (Figure 4).
To compare the effects of variation in density, we can review a simplified situation where the conditions are static. We can consider the positive force to be reflective of the settling rate of the bead in a liquid. The settling rate, R, is given by:
R = 2 r2 g [r(bead) – r (liquid)] / 9h

If we consider a 1 mm bead, then theoretical settling rates in a liquid of SG 1.5 and viscosity 1500 cps should be (Figure 5):
- GLASS (0.4 mm/sec)
- ZIRCON (0.8 mm/sec)
- ZIRSTAR (1.1 mm/ sec)
- ZIRCONIA (1.6 mm/sec)

Machine Fill Rate
Most mills are filled to a recommended optimal volume fill. Density, however, is a major factor in the overall efficiency and cost effectiveness of the process. For example, in most horizontal mills, the working volume is usually filled within the range shown in Figure 6. This gives the most effective grind while limiting temperature and wear development. Following are some examples for standard bead types, at 80% fill rate in a 100 liter machine.- GLASS 100 L x 80% x 1.5 (Bulk Density) = 120 kg Load
- ZIRCON 100 L x 80% x 2.3 (Bulk Density) = 184 kg Load
- ZIRCONIA 100 L x 80% x 3.6 (Bulk Density) = 304 kg Load

High Machine Wear
Logic would suggest that higher bead density leads to higher productivity. Higher bead density requires higher energy input, however this needs to relate to the specific milling energy. If energy input into the mill is excessive, then energy can be consumed for little relative improvement in quality. Additionally, excess energy can have negative effects, including heat generation, high mill wear and high bead wear (Figure 7).
Bead Selection
For efficient milling there is an optimum bead density to suit a particular operation/process or set of conditions. If the bead density is too low, optimum grind is not achieved. If it is too high, energy is consumed, and bead and mill wear increase.ZirPro is in a unique position with a range of products within an effective band of suitable bead densities as shown in Figure 8.
Looking for a reprint of this article?
From high-res PDFs to custom plaques, order your copy today!