Do We Need to Reconsider the Preservative Package When Reducing the VOC of Surface Coatings?
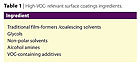
Lowering VOCs in surface coatings as a result of local legislation or environmental consciousness is, by now, well known to the industry. The most restrictive VOC limits remain those imposed in July 2006 by the South Coast Air Quality Management District (SCAQMD), particularly for non-flat architectural and floor coatings.1 Further reductions will follow, and restrictions for more coatings categories will apply in July 2007 and 2008.1 In the Northeast and mid-Atlantic states, the Ozone Transport Commission (OTC),2 has imposed limits that are not as prescriptive as those of the SCAQMD, but which are believed will be adopted by the EPA and Canada.3 It is likely that the OTC limits may also be adopted by the Lake Michigan Air Directors Consortium (LADCO) in the near future.3

VOC Reduction
Although there remains global disagreement on a single definition of VOC,4 what the limits should be and how they should be measured, the concept and benefits of VOC reduction are well understood and generally supported by the industry. Lists of compliant manufacturers or suppliers are available to consumers who support VOC reduction efforts, making compliance crucial for business maintenance and sustainable growth.The VOC reduction process for traditional solventborne coatings began many years ago, with the development of, amongst others, high-solids and water-dispersed alkyds, powder coatings, waterborne urethanes and water-based protective coatings with markedly improved durability and versatility. With the first phase of VOC reduction of surface coatings being essentially complete, further VOC reduction in water-based coatings would constitute the next milestone.
For the most part, VOC reduction is being
achieved by reducing, eliminating or using alternatives to high-VOC-relevant
raw materials and additives used in coatings manufacture (Table 1). In addition
to concentrating on the ingredients listed in Table 1, bulk volume coatings raw materials such as
polymer emulsions and slurries are receiving close scrutiny. Some manufacturers
are even screening small-volume additives for VOC compliance, and screening of
biocides in this respect is no exception.

Effect of Formulation Changes
As is often the case, any formulation changes are bound to have some other effect(s). We have noted over the years (as would be expected) that formulations with low VOC usually display greater susceptibility to in-can microbiological spoilage than similar formulations with higher VOC content. This, we believe, not only results from the reduction in VOC (and in some instances lower free monomer content) and concomitant increase in available water [water activity], but may also be a result of reduced availability of the in-can biocide whose presence in the aqueous phase is influenced by the VOCs removed and/or a reduction in pH.We have observed that customers who formulated higher-VOC formulations using benzisothiazolinone (BIT) as the sole in-can biocide for many years began to experience spoilage problems soon after they reduced the VOC content of those formulations. We believe that one of the significant contributors to the spoilage was the decreased availability of the BIT in the aqueous phase. BIT may partition from the aqueous phase if components in which it is soluble are removed (most components listed in Table 1) and/or, if the pH is reduced to below the critical partitioning point of BIT in the formulation - this would be the point at which a conversion from the BIT-salt to BIT would occur. A reduction in pH had been reported by some manufacturers following removal of alcohol amine from the formulation. Even a small shift in pH could be relevant in this respect, and must be borne in mind. The solubility of other in-can biocide active ingredients such as chloromethyl isothiazolinone and methyl isothiazolinone (CIT/MIT) combination and methyl isothiazolinone (MIT) are not affected by such reduction in pH.
Biocide migration into any non-aqueous phase would leave less biocide available to protect the formulation where it is needed (in the aqueous phase), particularly if little or no margin of safety had been considered when the original biocide addition level was optimized. Small increases in microbiological activity within the manufacturing facility or raw materials would then not be dealt with by the coating biocide, and spoilage could result.
At around the same time when VOCs were being reduced in existing formulations, we also noticed an increase in incidence of unusual gram-negative contaminants (in addition to the normal Pseudomonads and related spoilage organisms) as well as (in some cases) an increase in gram-positive bacterial spores in such formulations. Although some of this could have been coincidental, we believe that this could have resulted from sub-lethal levels of BIT remaining in the aqueous phase. These issues can be overcome by using the most appropriate combination in-can biocide having more than just a single active component.
Although there are many combination biocides available, ACTICIDE® MBS has been listed as an example in this excerpt (Table 2), since this biocide has many more advantages than its counterparts. Although ACTICIDE MBS contains BIT, the effectiveness of the polar MIT component against the Pseudomonads (and other problematic spoilage organisms), as well as the synergistic effects of the combination has been proven to be a very effective alternative to only BIT in low-VOC formulations (Table 3). ACTICIDE MBL has similar characteristics to ACTICIDE MBS, but has even greater antimicrobial capabilities, as a result of having a third active ingredient component.
As prime manufacturers of CIT/MIT, MIT, BIT, OIT and DCOIT active ingredients, and suppliers into the global market for more than 40 years, THOR/Acti-Chem has taken note of, and in many instances out-paced legislation with respect to VOC and environmental/health and safety aspects of biocides. THOR was the leader in manufacturing water-based BIT and OIT as well as other water-based dry-film combination biocides, including those containing water-dispersed IPBC. We are also able to control the release of a variety of biocide active ingredients for dry-film applications, making them not only safer to handle but also significantly reducing any possible adverse effects on the environment.
In addition to pressures of low VOC, there is also an increased interest in restricting the use of formaldehyde in some countries and this might become more prominent in selected states in America. The increase in susceptibility of low-VOC formulations would, by inference, require a greater amount of formaldehyde donor-type biocide to be added to increase the margin of safety against spoilage in such formulations, which might be regarded as counter-productive from the perspective of Air Quality Management oriented organizations.

Conclusion
There are many choices of in-can and dry-film biocides that can be used in formulations with VOC restrictions, most of which themselves have less than 0.1% VOC. As mentioned previously, combination biocides mostly offer benefits above and beyond biocides based on single active ingredients. Care should be exercised in reviewing in-can preservative packages when adjusting existing formulations for VOC compliance, since the degree of preservation may be adversely affected, or significantly different from the original formulation.Looking for a reprint of this article?
From high-res PDFs to custom plaques, order your copy today!