Particle Sizing for Coatings Spray Applications
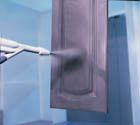
In the coatings industry spray systems are used to apply both powder and liquid coatings to a variety of substrates. Particle size is a key variable for both wet and dry systems, as it has a direct impact on the handling properties of the materials used and on the quality of the finished coating. Particle size measurement and control is therefore critical in the development of optimized transfer systems, and in the delivery of coatings with the required final properties.
For liquid coatings, droplet size determination is an essential part of assessing atomization efficiency. Changing the properties of the spray plume by manipulating variables such as nozzle geometry and atomization pressure is important in maximizing the amount of paint transferred onto the substrate. For paint systems with high solids loadings, good transfer efficiencies are particularly beneficial as these help to avoid the relatively high cost associated with any waste. High solids systems are used increasingly, as they reduce solvent handling problems and can deliver improved coverage.

Furthermore, the particle size of a powder coating correlates not only with its flow and dispersion characteristics, but also more generally with its behavior during the application process, and with the properties of the finished film. The most commonly used method of powder coating application is electrostatic spraying. Fine particles can be useful in these processes, tending to wrap around an object, coating both sides. On the other hand, larger particles are easier to charge and control, and have a high degree of straight-line inertia, which allows them to penetrate more successfully into the corners of an object.
During curing, when the particles melt and flow to form a smooth finish, small particles are preferable because they pack well on the substrate surface and melt easily, under relatively benign curing conditions. They can, however, produce a poor surface finish – an orange peel effect – either as a result of melting too rapidly or because of ‘back-spray’ during application. Larger particles are associated with relatively severe curing conditions, and if they do not melt completely may leave imperfections in the final film. As such, control of both the maximum and minimum particle size is important in order to ensure that the finish achieved is acceptable.
This article, the third in a series looking at various issues connected with particle size analysis for the coatings industry, focuses specifically on particle size analysis for spray applications. The specific difficulties associated with analyzing sprays will be explored with reference to significant features of modern laser diffraction systems, which make them ideal for this application. A case study describing a practical application of particle size analysis is presented.

Spray Application Demands
Carrying out the routine size analysis of sprays can be challenging for a number of reasons. Spray events can be rapid or, during continuous spraying, can show variations in particle size over short time scales, which can be indicative of poor nozzle performance. Because of the impact of atomization conditions on nozzle performance, a wide range of particle sizes may be produced, especially when moving from the start-up phase of atomization to equilibrium conditions. Furthermore, the particle size data obtained for sprays are relevant only if they are captured as the spray is produced. This requires measurements to be made in situ without risking contamination of the measurement system or needing to sub-sample or dilute the spray.The technique of laser diffraction offers many advantages for spray characterization.
- A wide dynamic measuring range – particle sizes ranging from 0.1 microns to a few millimeters can be characterized, enabling the detection of both fine spray droplets and poorly atomized material in the same measurement.
- Rapid data acquisition – a single measurement takes less than 0.5 milliseconds, allowing the study of atomization dynamics.
- Flexibility – the technique can characterize particles distributed over relatively long distances (up to 2 meters), facilitating the measurement of sprays with different plume geometries.
- High concentration measurements – laser diffraction can generate accurate results at high droplet concentrations, for direct measurement close to the spray nozzle.
- Generation of volume-based particle size distributions – this is normally equivalent to a weight distribution. It is relevant to many spray processes, indicating where most of the mass of material is located in terms of particle size.

The technique of laser diffraction calculates particle size distributions by measuring the intensity of light scattered at different angles as the spray particles pass through a laser beam. Underpinning this calculation is the assumption that the light detected by the measurement system has only been scattered by a single particle. For dilute samples this assumption holds true. When measuring concentrated sprays, however, multiple scattering can be observed, where light is scattered by more than one particle before detection. This can result in under-estimation of the spray particle size.
More sophisticated instruments can predict the effect of multiple scattering by using an analysis algorithm where the probability that more than one scattering event will occur is taken into account. This allows the particle size to be measured at high concentrations, where the amount of laser light transmitted through the spray is low (Figure 1).
The following case study demonstrates the type of work that can be carried out using a laser diffraction particle size analyzer designed to take account of the conditions detailed above. In this case the instrument used was a Malvern Spraytec.

Case Study - Laser Diffraction Analysis for Coating Nozzle Characterization
The droplet size distribution produced by a nozzle depends on the physical properties of the liquid being atomized and on parameters such as atomizer pressure, liquid flow rate, nozzle geometry and, in the case of twin fluid nozzles, flow rate of the secondary fluid. Order of magnitude estimates of droplet size can be determined from correlations based on the physical properties of the system and the geometry of the atomizer. However, the best way to optimize the nozzle configuration and operating conditions for a given application is to measure droplet size under the conditions of interest. In this study the effects of various parameters on droplet size were investigated experimentally, for a laboratory-scale twin fluid nozzle, using air as the secondary fluid.The influence of atomization pressure on droplet size is shown in Figure 2. Measurements were made in the axis of the spray plume, approximately 50 mm from the nozzle exit, using water as the test liquid. As intuitively expected, increasing the atomization pressure for a set liquid flow-rate decreases droplet size. Shear in the atomization zone increases with increasing pressure, resulting in formation of smaller droplets. However, it can be seen that large droplets are observed even at high pressure. This relates to the wetting of the nozzle during the operation of the atomizer.
The effect of changing the properties of the liquid can be seen in Figure 3. Here, the particle size produced by the same nozzle system studied above has been measured for the atomization of a 5% polyvinylpyrrolidone (PVP) solution. A bimodal droplet size distribution is observed for this liquid at low atomization pressures, with median particle size being much larger than for water. This observation is attributed to the viscous forces in the PVP solution, which impart a resistance to droplet formation when atomization energy is low. Increasing the atomization pressure leads to more-complete atomization of the spray, although the size remains large compared to water.
The nature of the atomization process can be further understood by observing how the droplet size changes over time. This is shown in Figure 4 for the atomization of the PVP solution at a pressure of 0.5 bar. Large variations in the coarse particle fraction are observed, as shown by the variability in the reported Dv90. There is also a progressive increase in the median particle size (Dv50) over time caused by polymer build-up on the nozzle. Increasing the atomization pressure improves the nozzle performance dramatically (Figure 5), confirming the need for increased atomization energy in this case to achieve full droplet break-up and a stable nozzle output.

Conclusion
Spray-based processes are widely used in the coatings industry for both liquid and powder applications. In both cases particle size analysis can contribute to the development of optimal transfer systems and production of coatings with the required finish. Laser diffraction is an ideal method for particle size analysis for many applications including those involving sprays. Although the analysis of sprays places significant demands on the technique, a robust laser diffraction instrument as exemplified by the Malvern Spraytec can be used to safely generate data of the required accuracy. These data can, in turn, be used by manufacturers to optimize both product and application processes.For further information, visit www.malvern.com, or email paul.kippax@malvern.com.

Sidebar: Malvern Spraytec
The Malvern Spraytec is a flexible and robust laser diffraction-based analyzer designed to meet industrial requirements for spray characterization. With a recently enhanced optical system that delivers an extremely broad measuring range from 0.1 to 2000 microns using just two lenses, and a data acquisition rate of 10 KHz, it can be used successfully for a range of applications.The enhanced optical design offers the advantage of an extended working range; particles as small as 0.5 micron can be analyzed from a distance of 150 mm. Keeping the optics at a distance from the spray is attractive from the point of view of reducing product build-up on the lens but this issue is specifically addressed through the inclusion of air purges that protect the optics. The electrical part of the unit is fully enclosed giving the instrument an IP65 rating.
The Spraytec has a configuration that is easy to customize to meet the requirements of a specific application. Full automation, easy-to-use software and auto-alignment of the lens and laser ensure that set-up is straightforward and operation is simple. Results presentation can be tailored to meet customer needs. A patented multiple scattering algorithm ensures that even concentrated sprays can be characterized accurately.
Looking for a reprint of this article?
From high-res PDFs to custom plaques, order your copy today!