Novel Applications for Fluorosurfactants in Low-VOC Coatings

Introduction
The worldwide coatings industry has been pursuing the development of low-VOC and VOC-free architectural coatings to meet new government regulations, and to protect the environment, applicators and building occupants. In these coatings, reduced VOC brought many challenges in resin system and formulation design. Traditional solvents in latex coatings serve as a coalescent aid for film formation, open-time agent to prevent over-brush coating defects, and anti-freeze agent to prevent instability in freeze-thaw cycles. In addition to these properties, solvents also impact a latex coating’s wetability, foaming, blocking and leveling. Many functional additives have been developed to address these issues in low-VOC coatings.1Fluorosurfactant use in coatings dates back to the 1970s.2 They were used as wetting agents and to improve leveling for many years in various coatings systems.3 In the past decade, more demanding performance requirements were expected from coatings users. In addition, the trend to lower solvent use levels was creating new challenges for the coatings chemist. Fluorosurfactants are useful additives in solving low-VOC coating-related problems in architectural coatings, such as anti-crater, anti-block and shorter open times in addition to their traditional role as wetting agents.
Telomer-based fluorosurfactants contain perfluoroalkyl chains and various functional groups. They have unique properties in significantly reducing surface tension in all aqueous, solvent and neat systems. They are air-liquid interface active, providing wetting, re-wet and oil repellency while meeting surface tension needs in coatings. They have been used in solving low-VOC formulation problems mentioned above. Until very recently, fluorosurfactants were used to address formulation problems near the end of the coating development cycle. Our recent research and practice have demonstrated that fluorosurfactants are most useful and cost effective due to the multiple functions they provide in formulating a low- or VOC-free architectural coating. The formulator can reduce other ingredients and create high-performance paints by minimizing the use of other coating additives, such as defoamers, wetting agents, leveling aids, anti-block additives and open-time extenders. Oil repellency and other functions that fluorosurfactants provide have also made them attractive to formulators in developing dirt pickup-resistance exterior paints.
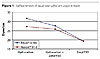
Surface Tension Reduction
With today’s diversified coating substrates and waterborne low-VOC coating systems, surface tension reduction is essential for application and good film formation. High surface tension will cause paint film defects such as craters, fish eyes, pin holes, orange peel and poor thin film control. Telomer-based fluorosurfactants are very powerful at very low concentration in reducing surface tension. The use rate of fluorosurfactants is very low compared to hydrocarbon and silicone surfactants. Average CMCs of this class are about 0.02% on active ingredient bases. This allows the coating to use very small amounts and still achieve wetting and leveling, with reduced foam to achieve defect-free coatings on conventional and hard-to-wet surfaces, such as plastics.Table 1 shows selected Zonyl® fluorosurfactants’ surface tension in deionized water (DI), measured by tensiometer. Compared to hydrocarbon and silicone-based surfactants, fluorosurfactants have the most power to reduce surface tension. Not only can they reach 20 dynes/cm surface tension, but their CMCs are very low.
While fluorosurfactants are perceived by many as foam generators, certain types of fluorosurfactants act as defoamers in coatings when used at low levels. The grades we recommend for most architectural paint applications decrease foam when the formulation also minimizes the use of other foam-causing surfactants. In most cases, when fluorosurfactants are used other defoaming agent usage can be decreased or eliminated.
Fluorosurfactants also work synergistically with hydrocarbon surfactants in resin synthesis during emulsion polymerization. Their main functions are stabilizing the emulsion, controlling particle size and allowing the reduction of hydrocarbon emulsifier surfactants. Reducing hydrocarbon surfactants can also help reduce foaming in the paint formulation. After the polymerization, fluorosurfactants are carried over to the final coating formulation to provide the other properties provided by fluorosurfactants.
Figure 1 shows surface tension reduction in DI water of hydrocarbon surfactants alone and mixtures of hydrocarbon surfactants with Zonyl at an equal cost basis. This experiment was run with two hydrocarbon surfactants and one fluorosurfactant. At $0.02 per pound cost of surfactants, the hydrocarbon surfactants alone were less effective than using $0.01 of hydrocarbon surfactant and $0.01 of Zonyl FSO. With $0.02 of Zonyl FSO alone, surface tension was reduced below 20 dynes/cm.

Anti-Block
Blocking is a common defect in formulating a low-VOC architectural coating, especially with semi- and high-gloss paints. Conventional, high-VOC systems help resin coalescence during film formation along with the use of higher Tg resins, which have lower blocking tendencies. To reduce VOC, coatings are made with softer resins with lower glass transition temperatures. The lower Tg allows coalescing to occur with less solvent to meet the new formulation constraints. Core/shell technology has also been developed to solve this problem. However, block resistance of freshly cured paint films is reduced often to a level that is not acceptable in the final formulation. Our studies have shown that fluorosurfactants can cost-effectively improve block resistance with no impact on the gloss levels of the coating. They work very well with different sheen levels of latex paints, even with deep-based paints, which generally have more severe blocking problems due to heavy use of colorant dispersants.In a developmental deep-base semigloss paint, we were able to improve the block rating (ASTM D 4946) from 0 to 5 by adding 0.1% (a.i.) Zonyl 9361. Later study showed that if the colorant dispersant is reduced, the block rating was further improved with 0.05% (a.i.) Zonyl 9361. The addition of the fluorosurfactant did not change other properties of the coating.
Figure 2 showed the impact on block resistance with fluorosurfactants in two low-VOC paints. In both cases, multiple additives were replaced with one fluorosurfactant to achieve block resistance.

Open-Time Extension
Open time is the time that it takes the surface of the wet paint to form a partially dry top layer. Short open time causes coating defects in the over- and cross-painted areas. With low-VOC paint formulations, open time is normally reduced due to lack of slower evaporating solvents; this causes over-brush defects. Open time of a latex paint is influenced by the viscosity, rheology, surface leveling and water evaporation rate under a given relative humidity when the paint is applied. Selective Zonyl fluorosurfactants have demonstrated a positive impact on leveling and slow down water evaporation from the wet film surface, thus reducing the surface defects caused with short open time for latex paints. Using Zonyl additives at a low level can help reduce the use of open-time agents such as ethylene glycol and propylene glycol. Table 2 shows open-time test data obtained by a double thumb press method.4 A low-VOC (40 g/L) paint is modified with 0.1% (a.i.) of Zonyl agents. The drawdown with a 7-mil blade was made at 23 °C under 50% (+/-10%) relative humidity.

Dirt Pickup Resistance (DPR)
Dirt pickup for low-VOC exterior paint is one of the toughest challenges that formulators encounter. Many factors contribute to increased dirt pickup. High-PVC paints have higher surface area, allowing a greater area for dirt to accumulate; low Tg resins make the film soft and sticky under heat and moisture; and oil-affinitive surface-active additives attract environmental dirt and stains to the painted surface. There are two approaches that are currently taken by the industry to increase exterior DPR.One approach is to make the paint surface highly hydrophobic, measured by high water contact angle. This approach often uses a silicone-modified resin or silicone additives in the formulation. The challenge with this approach is that if the paint does not have high enough water repellency, which has a water contact angle above 130-145°, dirt stains will appear as dark streaks on the wall that are not removed by rain.
A second approach is to make the paint surface hydrophilic, so it will allow rain to rinse the surface. If this surface is also static dissipative it will repel airborne particles from the painted surface. Fluorosurfactants work well with the second approach. Fluorosurfactants serve three functions: allow the reduction of other oil-attracting additives; allow the reduction of hydrophobic additives; and add oil repellency to the paint. Because fluorosurfactants migrate to the film surface and enrich the top 25% depth of the paint surface, the amount needed to achieve oil repellency at the surface is very low. Figure 3 demonstrates that with selected Zonyl products, a commercial high gloss, low-VOC paint film maintained its water contact angle and significantly increased its oil contact angle. (In this example no other additives were removed, which would help in further reducing water contact angle.)
Figure 4 shows an example of formulating an exterior paint utilizing Zonyl 9361 as a wetting, leveling, anti-blocking and oil-repellent agent. In the formulation, a silicone-based leveling agent and a wax-based anti-blocking agent were removed, and a mineral oil-based defoamer was reduced by 20%. The overall result is that the paint with fluorosurfactants performed better in DPR after nine months outdoor exposure in a southern U.S. test field. The liquids in the picture are water (upper) and hexadecane (lower). They were used to determine the retention of surface repellency after exposure.

Summary
Based upon the studies we have presented above, fluorosurfactants are very useful, multi-functional additives for low-VOC architectural coating formulations. They provide wetting, leveling, defoaming, anti-block and open-time extension. Although they have been traditionally used to correct performance near the end of the formulation process, scientific research shows more and more evidence that fluorosurfactants are most effective when incorporated early during the coating system design to allow formulators to take out unnecessary (redundant) additives to achieve best results. This is particularly important in formulating low-VOC coatings and for reducing dirt-pickup in exterior paints.
Looking for a reprint of this article?
From high-res PDFs to custom plaques, order your copy today!