Radiation Curing Of Wood Coatings
Together with other partners in the market, raw-material suppliers are requested to offer solutions to the various problems.

The UV Market
Worldwide consumption of radiation-curable acrylates in 1998 accounts for approximately 100,000 tons, with the majority in the United States and Europe (see Figure 1). The growth rate is estimated to be 8% per annum over the next 10 years.Other binder types, such as unsaturated polyesters dissolved in acrylates, styrene or vinyl ethers, currently do not share the same commercial importance as acrylates.


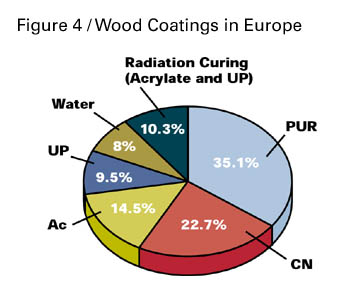

At the beginning of radiation curing in the early 1970s, unsaturated polyesters dissolved in styrene dominated the market; they are still of major importance due to cost reasons.
The first acrylates used in wood coatings were epoxy acrylates and polyester acrylates. They provide high reactivity, hardness and chemical resistance.
One of the driving forces for further development in acrylates for radiation curing is the reduction of emittable solvents (VOCs), which have to be reduced by law in Europe soon.

A first step on the road to the wider use of radiation curing was the development of waterbased products. At first this seemed contrary to the goal of 100% systems. However, the decisive advantage of such a system is to overcome the drawbacks of conventional radiation curing and those of conventional polymer dispersions. The advantages include the ability to be thinnable with water; spray and curtain coater application are possible; good matting properties; and less polymer shrinkage and thus better adhesion.
It is possible to transfer all resin types into an aqueous medium. The resulting systems are either water thinnable solutions or emulsions stabilized with protective colloids with or without physical drying properties. Modern drying processes like Hydrex, high-frequency, near-infrared (NIR) and microwave contribute to efficient drying of water-based systems. New recycling processes allow almost 100% usage of the material applied.
Developments in the field of radiation-curable powders are aimed at the coating of wood and metal. The idea here is to overcome the difficulties associated with powder coating technology — the inability to separate the processes of film forming and crosslinking — and conventional UV coatings – poor adhesion on certain substrates, for example. Better flow is achieved by crosslinking the polymer after and not during the film formation. This new technology is just beginning and seems to be especially suitable for coating of MDF.


Radiation-Curable Wood Coatings
The coating system for wood is subject to a variety of requirements that can only be met by combining different layers of coating materials. For a complete system, there are a variety of possible solutions which are dependent in each individual case on the available production line and on the quality of the substrate. However, all systems share the requirements for good adhesion to the substrate, good inter-coat adhesion and good resistance to chemicals (such as cleaning products, red wine, coffee, etc.).Adhesion To The Substrate
The requirement for good adhesion to the substrate is at present usually achieved through the use of an aqueous adhesion primer. The adhesion-promoting effect, which is manifested in a good coin test, is achieved by partial swelling or erection of the wood fibers. This operation increases the surface area and therefore offers increased possibilities for mechanical anchoring of the coating to the wood. In practice it is important to notice that approximately 10 g/m2 of this adhesion primer, with a water content of only about 20%, implants the desired effect, and it is possible to dispense with a thermal drying apparatus which removes the water prior to UV exposure.Another alternative besides the increase in adhesion based on physical/mechanical effects is the use of a 100% material (100% solids content) in combination with polyisocyanates.
This dual-cure system imposes certain requirements on the hydroxyl number of the resin even at the stage of selecting the acrylic ester prepolymer, since the NCO groups must be present in excess in order to achieve a perceptible improvement in adhesion. In order to formulate the primer as a one-component system it is important to combine the isocyanate component with a radiation-curable prepolymer of relatively low hydroxyl number. In the first step, the reaction between the NCO groups of the isocyanate component and the OH groups in the acrylic ester resin leads to an increase in viscosity which must not exceed the processing viscosity. After the end of this first reaction, the excess NCO groups remain, and following application react with the hydroxyl groups in the wood forming true chemical bonds to the substrate. They therefore have a strong adhesion-promoting effect.
Intercoat Adhesion
In order to obtain good intercoat adhesion, two methods are generally available. Depending on the subsequent coat, the underlying coat is just gelled partially; in other words, the UV dose for polymerization is deliberately kept low such that the reaction of the reactive groups on the surface is incomplete. Then, when the subsequent coat is exposed, true chemical bonds are formed between the individual coats. The facility for partial gelling is highly effective and also makes economic sense, since it is possible to use UV lamps with a lower output, or less photoinitiator.The second possibility for good intercoat adhesion is to sand a cured coat. This not only produces better adhesion of the subsequent coat but has the further effect of eliminating unevenness (grainy system) and therefore of achieving improved optical characteristics. Intermediate sanding is therefore usually carried out prior to application of the topcoat.

Examples For Mixed Systems -Parquet Coatings
The requirements like abrasion resistance can be met by different systems. The coating is depicted more closely with reference to two typical systems. Which system is chosen depends on the available production line and its machinery (application equipment, UV exposure devices, and sanders). An example is shown in Table 4.The way in which the aqueous adhesion primer promotes adhesion has already been discussed. A further effect, which is also supported by the use of a highly viscous and highly filled filler coat, is the prevention of end-grain discoloration. This terms refers to the darkening of the end faces of the wear layer as a result of penetrated liquid coating material, which undergoes inadequate interaction with UV light during exposure and is therefore not fully cured. The real advantage of the high (about 40–50 g/m2) filler layer, however, is a different one. If the surface of the uncoated substrate is uneven, then it can be smoothed by sanding the filler layer, thus providing an improved visual appearance (levelness) of the finished product. What is accepted, therefore, is an increased sanding requirement and, in some cases, slight reductions in transparency as a result of the highly filled filler.

Furniture Coatings - Mixed Systems In Furniture Coatings
Prefinished parquet is typically coated using a complete UV system; however, there are applications in which UV-curable coats are combined with coats which use different coating technologies. Such systems are referred to as mixed or hybrid systems. By way of example, some of the possible combinations will be mentioned here, and their technical advantages highlighted.Waterborne Coating + UV Coating
On highly absorbent substrates in particular, the UV coating material may be lost by deep penetration. The consequence is that the UV coating material present within the substrate does not come into contact with UV light, and avoids polymerization. Over a prolonged period, uncrosslinked components of low molecular mass migrate to the surface, where they can give rise to odor problems or greasy surfaces. For this reason it is advisable to seal MDF boards, for example with an aqueous dispersion lacquer prior to UV coating.UV Coating + Waterborne Coating
In contrast to conventional waterborne coating materials, 100% UV materials produce much greater grain highlighting on wood. This effect can be put to good use by ensuring that the first coat, applied at a low rate, consists of such a UV material. Only one UV unit is then required in the production line.UV Coating + NC Coating
The low solids content of a nitrocellulose (NC) lacquer necessitates a large number of applications in order to achieve a relatively high application rate. To reduce this time-consuming and costly effort, the desired amount can be applied in a single application using a UV material. Subsequently, a single NC coat is applied, after sanding, to provide the desired sensory properties of the surface.UV Coating + PU Coating
Following application of the UV coats by means of rollers, the rolled structure is removed by appropriate sanding machines. A PU spray coating is then used for the actual topcoat, bringing with it sufficient resistance and ensuring excellent leveling.
Solvent Balance
Although the previously described hybrid systems are in many cases compromise solutions — since they involve longer drying times (in the case of waterbornes and PU materials) or high-VOC emissions (NC lacquers) — they are not without their significance in industry. The practicability of such systems under increasingly stringent solvent emission limits in the future is highlighted by the comparison of an NC with a UV coating (see Tables 6-7).The significantly improved solvent balance is not the only advantage of the UV system over its NC counterpart. The closely crosslinked UV coating also gives greater chemical resistance than a physically dried, partially resoluble NC coating.
Outlook
There are good chances for successful further growth of radiation curable wood coatings. Not only applicational properties but also ecological and economical advantages are obvious. Further developments in all areas of raw materials, application technologies and curing equipment will contribute to a global dissemination of radiation curing for wood coatings.This paper was originally presented at RadTech 1999 in Berlin, Germany. Full proceedings from RadTech are available from Gary Cohen, RadTech USA, gary@radtech.org, for $125, or from Jurg Seidel in Europe, radtech.seidel@bluewin.ch, for 110 euros.
Looking for a reprint of this article?
From high-res PDFs to custom plaques, order your copy today!