Dynamic Surface Tension and Surface Energy in Ink Formulations and Substrates
Solventborne formulations, with their naturally lower surface tensions, wet readily and transfer well onto most substrates, even though they may have higher coefficients of spreading on select substrates. The increasing shift to waterborne ink, due to environmental concerns, has inherent problems of surface wetting, foaming, and flow and leveling, common to all waterborne systems. Waterborne inks require alcohols and surfactants to lower their surface tensions to acceptable levels for transfer, spreading and adhesion.
Alcohols have low surface tensions and are “non-active,” but most common surfactants used in waterborne systems generally have high surface activity that varies with changes in concentration, molecular weight and structure. A coating application is a dynamic process, and active surfactants cause surface tensions to change as speeds and formulations change. Surfactant activity directly impacts coating spread and adhesion. The surface tension of inks must be lower than the wetting tension of substrates to attain good printability, adhesive bondability, or ink lay down.
Formulation Changes
Formulation and application of waterborne ink are influenced somewhat by controllable, external factors, such as shipping and storage, freezing and thawing, both before and after each process takes place. The physical properties of handling and mixing systems, to a large degree, are fixed and uncontrollable. Many facilities suffer the uncontrollable effects of seasonal changes — hot summer vs. cold winter environments, for example. Inks can and often do change at the formulation site, and change even more just prior to, and during, application. What is often formulated and tested in the laboratory is not what is ultimately used during application. Alcohols and reagents are lost to evaporation, and these losses can go undetected unless testing can be done at formulation and process sites. When any ink or coating is applied, surfactant molecules in the bulk solution react by diffusing to the interface. It is at this interface that the surfactant molecules try to line up with their hydrophobic ends pointed at the interface and the surface tension is lowered. The concentration and nature of the surfactant determines how much the surface tension can be reduced, but the speed at which diffusion takes place influences how fast wetting will occur. Wetability, and ultimately “coatability,” is influenced by the combined physical and chemical properties of the constituents. This article will examine the area of controllable factors, with emphasis on techniques used to measure the dynamic surface tension of inks and the wetting tension of the solid surface (substrate) to be coated.

Surface Tension and Surfactants
Surface tension can be thought of as the force that “holds” a fluid together in the presence of air, within its own confines — the tangential intermolecular force of attraction between adjacent molecules. Surface tension dictates whether a coating will wet and spread over, or retract from, a solid surface. Surface tension is expressed as force per unit of width; as dynes/cm (or mN/m). Water has a high surface tension, in the range of 72 dynes/cm while alcohols are in a low range of 20 to 22 dynes/cm. Solvents, typically used in solventborne formulations, are in the 20–30 dynes/cm range. This is the major reason that substituting waterborne formulations, with their high inherent surface tension values, for much lower surface tension solventborne systems is a major challenge.Surfactants are used because of their ability to reduce surface tension. They are classified by the ionic charge of the surface acting part of the molecule. Anionic surfactants have a negative molecular charge, cationics positive, and nonionics no charge. Amphoterics have both positive and negative charges. Anionics and nonionic surfactants provide most of industrial surfactant requirements. Selection of surfactants is based on specific needs and often mixed surfactants are used.
In general, surfactants with a smaller (lighter) molecule mass (short hydrophobic tail) diffuse more rapidly to the interface, and are vertically adsorbed at the interface, causing a compressive force to act on the surface thereby reducing surface energy or surface tension. Nonionic surfactants with ethylene oxide groups usually diffuse very rapidly to the surface while fluorinated surfactants are slower and more effective at equilibrium. Most surfactants at higher concentrations exert strong molecular attractions between adjacent molecules causing strong surface films, the strength of which determines the surface properties of the surfactant solutions.
At the instant a coating is deposited on a substrate, at zero time of new surface generation, the concentration of surface active molecules at the interface will be the same as in the bulk solution; equal to the surface tension of the pure solvent. The surfactant molecules then begin to diffuse to, and adsorb at, the newly created fluid/substrate interface and the fluid/air interface. It takes a finite amount of time for the surface tension to reach equilibrium, anywhere from several seconds to several minutes. This is why the relevant parameter in designing formulations is dynamic surface tension rather than static (also known as equilibrium) surface tension.
Surface tension dictates whether a coating will wet and spread over, or retract from, a solid substrate. Inks exhibit both an adhesive force that is a measurement of the degree of association of the coating for the substrate, and a cohesive force that is a measure of the degree of self-adhesion of the coating. Spreading coefficient is the difference between work of adhesion and work of cohesion. If work of adhesion is greater than work of cohesion then spontaneous spreading occurs. If work of cohesion is greater than work of adhesion, then retraction, a surface defect, occurs as the coating will preferentially associate with itself.
Classical belief is that many surface tension related properties such as detergency, foaming, and wetting, either maximize or minimize at the surfactant critical micelle concentration (CMC). These relationships, however, are based on classical measurements limited to static surface tension conditions, when equilibrium has been established between the surface layer and the bulk solution. Dynamic surface tension measurements of active surfactants reveal levels at which surfactant effectiveness is at its highest, which is not necessarily related to equilibrium CMCs. Dynamic measurements more accurately reflect actual, in-process, surfactant and coating performance. In effect, if you limit surfactant migration time (by using a faster coating process) you require more surfactant to perform the same job as in the slower process. Figure 1 illustrates a series of dynamic curves where the CMC point moves to the right (increasing concentration) as the curves move upward with decreasing surface age (decreasing surfactant migration time).
Ink Formulation Variables
Waterborne systems have some inherent advantages over solventborne systems, such as lower resolubility rates and higher viscosities, but they are more pH sensitive. Common formulations often combine a soluble resin in a water-amine-emulsion system. Therefore, pH is crucial. If too high, it can burn out the pigment and change coating viscosity, and if too low it may “kick out” resin and pigment from the water and leave pigment deposits. Resolubility problems in waterborne inks are primarily due to lack of a resin system being totally soluble in water. Some waterborne inks require use of organic cosolvents to achieve low enough surface tensions to wet certain substrates. Pigments possess a range of properties that influence bond strength, adhesion, pH stability, viscosity, color and coatability. Important attributes of binders include the ability to carry and disperse a range of pigments, to wet low surface energy substrates, to enhance coatability and drying, and to increase adhesion to substrates. Organic solvents, such as alcohols, glycols, and glycols ethers, can assist in adjustment of drying speed, controlling foam, and lowering of surface tension. Additives can act as adhesion promoters or bonding agents, particularly if pigment colors detrimentally influence the bonding and adhesive properties of the formulation. All of these formulation variables influence surface tension, and the coating will wet the substrate only if the surface tension is lower than the wetting tension, or critical surface energy, of the substrate. This does not guarantee that the ink will necessarily adhere to a substrate that it wets, but verifying that this requirement is met is certainly a crucial step in the right direction.

Surfactant Performance
Ink formulators can plot the overall performance of surfactants by measuring and characterizing them in three dimensions; with respect to surface tension, concentration, and diffusion time (surface age). This can be done manually, or with a series of dynamic surface tension runs at increasing surfactant concentrations, using a SensaDyne maximum bubble pressure tensiometer and automatic dispensing system. The result is a three-dimensional plot, as shown in Figure 2. This technique can also be used on surfactant-containing ink formulations to see effects of formulation changes. Non-active additives primarily shift the plot upward or downward, while changes in type of surfactant or concentration tilt and/or shift the plot.Surfactants that diffuse slowly may not lower surface tensions sufficiently, within dynamic coating time constraints, to acceptable levels and may be partially responsible for defects such as: Bénard cells (hexagonal cells with well marked centers produced by circulation patterns in thin films); craters (bowl-shaped depressions) or pin holes; crawling or retraction (dewetting of the applied coating); floating (mottled, blotchy, or streaked appearance); orange peel (surface bumpiness); and picture framing (edge buildup). Both rheology and surface tension modifications are used to reduce or eliminate surface defects. Increasing the viscosity can eliminate retraction, for example, but if a viscosity increase is not viable, then the formulator may have to address defect reduction through surfactant modification.
A rapidly diffusing surfactant can mitigate surface defects by eliminating surface tension gradients. This occurs through rapid surfactant migration from high concentrations (low surface tension) to low concentrations (high surface tension). Formulators will sometimes mistakenly increase surfactant concentration in order to reduce gradients, rather than use a better surfactant. This can result in higher surfactant costs and other problems. A surfactant having both low equilibrium and dynamic surface tension in water may not necessarily have the same characteristics in a highly formulated system. Extra surfactant can become “tightly bound” with polymeric binders, or can be solubilized with pigment micelles, becoming ineffective in producing further surface tension reduction.
Some classes of surfactants have rapid diffusion characteristics because of unique polar molecular structures. This type of surfactant is capable of reducing surface tension with the extra benefit of reducing or preventing foam. Hydrophobe-hydrophile-hydrophobe structures, which displace materials that form solid structural films at the interface, make excellent wetting agents or surface tension reducers. These acetylenic diol-based surfactants have highly branched alkyl groups and are horizontally, rather than vertically, adsorbed at the air/liquid interface. At low concentrations these molecules cover large areas, but can be squeezed together as the concentration increases, exhibiting a unique compressible nature. The centrally located hydrophile gives the molecule a flat surface orientation, while the hydrophobic chain groups minimize intermolecular attraction, which contributes to low-foaming/defoaming capability. The disadvantage of a surfactant that only lowers surface tension is that separate defoamers may have to be added, which can themselves contribute to surface defects. Formulators should try to use a suitable surfactant that ideally has both low equilibrium and low dynamic surface tension values — low enough so that the coating is applied to the substrate at process speeds with a desirable viscosity. It is ideal if the surfactant used can perform more than a single function.

Surface Energy
Transfer and spreading of an ink on a substrate depends on the surface energy of the material delivering the ink, the surface tension of the ink, and the surface energy of the substrate receiving the ink. The substrate must have a surface energy higher than the ink, with forces of attraction great enough to promote good transfer and spreading, which in turn facilitates good adhesion. Additional factors affecting adhesion include release properties of the surface, substrate composition, and the structure of the substrate layer.Measuring the wetting tension, or surface energy, of substrates is commonly and inexpensively done with the use of “dyne liquid” solutions. These are purchased as a series of premixed solutions, each of a given wetting tension in dynes/cm. Users can also prepare their own solutions using a set of reagents, such as formamide (HCONH2) and Union Carbide’s ethyl Cellosolve® [ethylene glycol monoethyl ether (CH3CH2OCH2CH2OH)]. These particular non-active wetting solutions are prepared by mixing the two in proportions as designated in ASTM D 2578-84. This allows a series of wetting solutions to be formulated in a range from 30 to 56 dynes/cm, based on the proportions, as shown in Figure 3. To make drops or thin films more discernible, ASTM recommends adding a small amount of highly tincted dye. The ASTM method requires narrow standard temperature (23±2ºC) and relative humidity (50±5%) test conditions, due to the inverse temperature/ surface tension relationships of liquids.
The dyne liquid solution (DLS) must readily wet the surface for the substrate material to be at a wetting tension equal to the surface tension of the DLS used. The ASTM method clarifies this as a continuous one square inch film that remains intact for at least two seconds. If the liquid film spreads readily, then a higher surface tension DLS is needed. If the DLS breaks into droplets (beads up) then a lower surface tension DLS is needed. The user arrives at the equivalent surface energy value of the substrate, when the DLS remains spread out but has no particular tendency to bead up or spread further. Working upward, toward higher surface tensions, is recommended by the ASTM standard because wetability is easier to see than non-wetability. Problems with DLS formulations, whether purchased or mixed, can result when reagents are not immediately used, as they have a finite “shelf life.” Surface tensions will change due to contamination and/or evaporation. For example, ethyl Cellosolve is more volatile than formamide. When these two reagents are utilized, the lower dyne solutions that contain a greater percentage of ethyl Cellosolve are more susceptible to evaporation and a resultant increase in surface tension, a problem verified in long term studies of wetting tension solutions.
Maximum bubble pressure tensiometers can verify purchased DLS formulations and simplify the two-reagent method. Starting with a test solution of 100% ethyl Cellosolve (30 dynes/cm) and progressively adding formamide to increase the surface tension of the test solution, sequential testing of the substrate is done. Surface tension is measured before each progressive test, or at the end when the final mixture is judged to adequately wet the substrate. This final surface tension value is equal to the wetting tension of the substrate. This works well for surface tensions up to 40 dynes/cm, where the ratio ends up roughly two thirds formamide and one third ethyl Cellosolve. If the substrate wetting tension is suspected to be above 37 dynes/cm it is faster to start with a one to one ratio.
This method eliminates the need to use additional, often expensive and complex contact angle measuring instruments that are used to determine wetting tensions. Another advantage of using the SensaDyne tensiometer, since temperature is measured along with surface tension, is that wetting tensions can be determined under ambient conditions, out on the factory floor, for example, without needing an environmental test chamber. With the tested substrate most likely at ambient temperature and humidity, the surface tension reading of the DLS gives the surface energy at ambient (for which wetting tension is most pertinent) under conditions in which the printing process is most likely to take place.
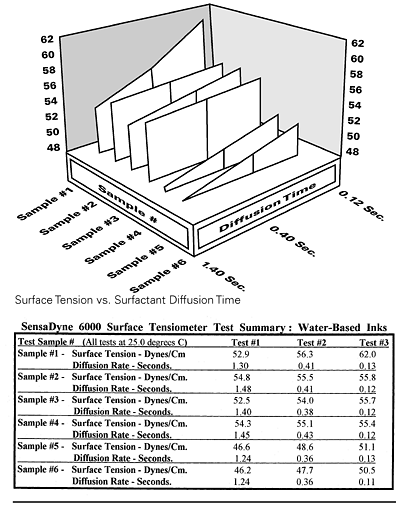
Summary
Instruments located adjacent to formulation or press sites must be simple to use, be suitable for both dynamic and static surface tension measurement, and not be effected by contaminants and any adverse site conditions.SensaDyne’s dynamic surface tension measurement technique is based on a patented modification of the maximum bubble pressure method. Two probes with 4.0 mm and 0.5 mm orifices are inserted into a fluid. The computerized instrument measures maximum differential bubble pressure at the orifices and calculates the fluid surface tension. Bubbling within the body of the fluid makes the system immune to surface contaminants and surface foam. The instrument is calibrated by pre-testing two fluid standards of known surface tension values, such as deionized water and alcohol. Immersing the probes in the middle of a sample is the extent of the expertise demanded of the user.
Surface tension values are used to compare the quality of newly formulated inks against previously measured inks. DLS wetting tensions are used to determine and compare new versus previously used substrates. Information can be obtained for three-dimensional characterization of active surfactant-containing formulations when the concentration of the surfactant or other additives is changed. Dynamic surface tension curves for a series of inks with active surfactants are illustrated in Figure 4. Formulations that exhibit both low equilibrium and low dynamic values can be determined prior to their use.
Comparing the data and dynamic curves of the first three water-based inks (Sample #1 through #3) in Figure 4, reveals that Sample #1 has a fairly steep dynamic curve that should give the lowest equilibrium surface tension once the curve flattens (to the left) and reaches its minimum value, at some time slower than the tested 1.4 seconds. However, it has the highest dynamic value (62) of the three at a surface age of 0.12 seconds. Sample #2 has the smallest slope, and would have the lowest dynamic value if the diffusion time allowed were much less than 0.12 seconds.

Formulation and coating problems can be greatly mitigated, or avoided entirely, by measuring surface tensions and wetting tensions of the companion substrates before the inks are used. Press site adaptable instruments allow faster and more positive problem mitigation by allowing changes to be verified and quantified immediately after formulation adjustments have been made. Formulators can improve transfer, spreading, and adhesion of inks by choosing surfactant and additive combinations that provide the best surface tension profiles for the application.
For more information on surface-tension measurement, contact SensaDyne Instruments, Chem-Dyne Research Corp., 2855 E. Brown Road, Suite 20, Mesa, AZ 85213.
Looking for a reprint of this article?
From high-res PDFs to custom plaques, order your copy today!