Ultra-Low-VOC, High-Performance Waterborne Coatings


Until now these very low-VOC customers purchased these coatings because of their concerns for personal safety. At the same time the vast majority of waterborne coatings were formulated at about 250 g/L volatiles, which offers excellent film formation and provides acceptable performance properties for the many types of waterborne coatings sold.
As we all are aware, the volatile content of coatings has been more than an issue of choice; it has evolved during the last 40 years into the topic of many government regulations, both state and federal. The coatings industry has responded to each successive regulation with products that comply with the rule and still deliver most of the performance properties necessary to fulfill the function of paint - to protect and decorate. Keeping up with the regulations has cost the coatings industry dearly, forcing many small paint companies to close when unable to reformulate their products to comply with the regulations.
Over the years, Hazardous Air Pollutants (HAPS) have been listed and limited. In the United States, areas of high pollution have been described and regulations specific to geography have been issued. These are the OTC or Ozone Transport Commission rules. Reactivity of solvents has been quantified and rules based on reactivity rather than quantity have been suggested, but to date have not been implemented.

Issues Today
Now coatings formulators face their most difficult challenge. January 2006 marks the beginning of the latest and most stringent round of VOC reductions in California. Paint manufacturers are formulating again, hoping to comply with the new regulations, without sacrificing performance and profits. Compliance with the California rule necessitates that national companies have separate products for sale in California or reformulate all products for sale nationally that will comply with the low-VOC rule in California.

Function of Solvents
VOC describes the organic chemicals that evaporate during several approved test methods but exclude water. Some solvents have been declared "exempt" by the EPA, which means that they do not participate in atmospheric photochemical reactions. These include acetone, methylene chloride and tertiary butyl acetate. Unfortunately, these exempt solvents are not practical in all coatings formulations.The function of solvent varies depending on the coating type. In solventborne coatings the solvent is needed to dissolve the resin and thus reduce its viscosity. Most alkyds would be too viscous to handle without solvent. However, in waterborne coatings the solvent has a quite different function. It is needed to reduce the MFFT or minimum film forming temperature of the polymer. If the polymer is applied above the MFFT the resin will not form a continuous film, but a brittle, powdery film will be produced.
Many polymers have an MFFT above 25ºC and would not form continuous films when applied at room temperatures. Therefore, formulators add cosolvents or plasticizers to the coating to reduce the MFFT and achieve good film formation without using elevated temperatures.
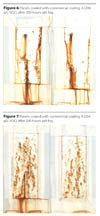
Another important consideration when formulating low-VOC coatings is the amount of solvent brought along in the additives used. Additive manufacturers should be contacted for suggestions on how to use additives without increasing the coating's VOC. No longer can formulators use their standard additive packages. The favorites of the past often will not be used in today's low-VOC world.

Low-VOC Polymer Advances
Researchers have been very aware of the challenges the industry faces. Creating resins that can successfully perform when formulated at very low VOC content has been a goal for many years. Various approaches have yielded polymers that deliver performance while requiring significantly less cosolvent. Formulations less than 100 g/L, and even 0 g/L in waterborne coatings, can be achieved without sacrificing performance.This has been accomplished by careful design of the polymer backbone, colloidal properties and polymerization ingredients. They include the use of a hydrophobic backbone, small particle size, optimum choice and level of surfactant and absence of water-soluble species. The shapes of the polymer as well as the ability to make polymers with core-shell configuration have also resulted in polymers with high performance and low VOC demand. Recently, several polymers have been introduced to the maintenance market that show excellent resistance properties to humidity, salt fog, chemicals and ultraviolet light. These resins perform well in the normal VOC ranges of 200 to 300 g/L. However, can they be formulated to deliver superior properties at very low VOC amounts?

Low-VOC Polymer Performance
A gloss white topcoat based on Resin 1 formulated at 90 g/L and another based on Resin 2 formulated at 0 g/L VOC were made in the lab and tested. These low-VOC paints were compared to commercial products sold in the industry for many years and containing standard VOC amounts in a large benchmark study. The commercial products were produced by four of the top five coatings manufacturers in the United States. They were formulated to perform on metal and wood and were directed toward the light-duty maintenance market.

Experimental Results
All testing was performed on cold rolled steel panels at dry film thicknesses between 1.75 and 2.00 mils. Panels were air dried for one week at 25 ºC and 50% relative humidity. Figures 1-9 and Table 1 are summaries of the results of these tests. The commercial products tested are designated A through G. To simplify the presentation of data, a rating system was developed that included blistering, rusting and scribe failure. A rating of 5 means no effect and a rating of 0 means complete failure.In addition to the described tests we observed that coatings made with Resin 1 and 2 and formulated at 90 g/L and 0 g/L exhibit excellent early water resistance, scrub resistance and low temperature coalescence.
As can be seen from Figure 10, the paints made with Resin 1 at 90 g/L and Resin 2 at 0 g/L VOC perform as well as or better than the commercial products at full VOC. There is no loss in performance at the low-VOC values. In fact, performance is improved considerably over most of the commercial products.

Master Painter's Institute Specifications
In the course of the benchmark testing, some very interesting questions arose. Many large coatings manufacturers are looking to have their products approved by the Master Painter's Institute. This group is based in Toronto, Canada, and is "dedicated to the establishment of quality standards and quality assurance in the painting and coating application industries, principally in the United States and Canada". The coatings manufacturers, in order to show the industry that their products meet specifications established and tested by an independent organization, have welcomed these standards of excellence. The contractor or specifying agency may demand MPI approval for a project being undertaken. Since these MPI approval listings have become more important every year, many large coatings manufacturers strive to meet the MPI specifications for many types of coatings.During the study we tested our commercial and experimental products against the MPI Specification # 164 Exterior W.B. Light Industrial Coating. Most of the commercial products passed the majority of the tests, yet most failed the weatherability specification. This entailed exposing panels to four hours of UVA-340 ultraviolet exposure at 60 ºC and to four hours of condensation without UVA at 40 ºC. To pass the test, coatings must lose less than 10 units of 60º gloss in 500 hours of cyclic exposure. Figure 11 shows what we learned about the commercial coatings in our benchmark as compared with the low-VOC formulations of four DSM NeoResins acrylics.
Table 2 reveals many interesting results. The two-component solventborne urethane started with close to 90° gloss as did the solventborne alkyd. However, both consistently lost gloss throughout the test, ending with gloss in the 20's after 2000 hours.
The waterborne commercial coatings at high VOC, and the experimental paints made at low VOC with Resin 1 and Resin 2, all showed significant loss at 500 hours, some performing better than others. Yet commercial A and the paints made with Resin 1 and 2 exhibited a gradual increase in gloss, recovering most of their original gloss after 2000 hours. The other commercial products lost gloss at various rates, resulting in lower gloss levels at the end of the test.
Although Resin 1 and 2 passed the #164 requirement at 2000 hours, they both failed the 500 hour requirement of less than 10 units gloss loss, losing 13.6 and 15.7 units respectively. We found that careful formulating to optimize film integrity improved the results, yet we were unable to reduce the gloss loss at 500 hours to less than 10 units.
The most striking result of all is that of coatings made with Resin 3 and Resin 4. These self-crosslinking acrylic polymers, when formulated at 90 g/L VOC in a white topcoat, showed no change in 60º gloss throughout the test. Weatherability performance such as this is extremely remarkable. This study reveals that these waterborne polymers can significantly outperform 2K solventborne urethanes, alkyds and the vast majority of waterborne acrylics when exposed to UV and condensation at elevated temperatures.
Although Resins 3 and 4 were not tested in the original benchmark study, subsequent work showed them to pass all the requirements of the Master Painters Institute #164 specification for Exterior Water Based Light Industrial Coatings. They also offered resistance properties well within acceptable ranges in the tests performed in the benchmark study.
Summary
This new generation of waterborne acrylic polymers with low-VOC demand and exceptional performance can be priced competitively with resins now on the market that require high cosolvent levels and offer marginal performance. Performance is better, VOC is drastically reduced and resin costs remain reasonable.In conclusion, we can say that formulations made with Resin 1 or Resin 2 containing less than 100 g/L VOC and 0 g/L VOC will provide excellent performance when compared to many commercial products that contain much higher VOC amounts. Resins 3 and 4 allow coating companies to pass MPI specification #164 formulated at less than 100 g/L VOC, which has proven quite a challenge in the past. Coatings manufacturers, wishing to reformulate products in order to comply with VOC regulations, can do so with a significant improvement in performance. For these reasons national products at very low VOCs may be introduced. These products will offer superior performance through many years of regulation changes.
Suggested Reading
1. Handbook of Coatings Additives; Calbo, L.J., Ed.; Marcel Dekker, Inc.: New York, 1987.
2. Camp, R.C. Benchmarking; ASQ Quality Press: New York, 1989.
3. Film Formation in Coatings; Provder, T., Urban, M.W., Eds.; American Chemical Society: Washington, DC, 2001.
4. Stout, R.L.; Ellis, W.H.; Solvents, 2nd ed.; Federation of Societies for Coatings Technology: Blue Bell, PA, 1998.
5. Wicks, Jr., Z.W. Film Formation, Federation of Societies for Coatings Technology: Blue Bell, PA, 1998.
6. Wicks, Jr., Z.W.; Pappas, P.S.; Jones, F.N. Organic Coatings: Science & Technology, 2nd ed., John Wiley & Sons: Hoboken, NJ, 1999.
This paper was presented at the annual PACE meeting, Tampa, FL, January 2006.
Looking for a reprint of this article?
From high-res PDFs to custom plaques, order your copy today!