Rheology For Coatings

Rheology is the study of how materials flow and deform when subjected to external forces. Rheological measurements therefore define some of the fundamental properties of materials and can be used effectively to characterize and predict product behavior. For coatings, product behavior under very different sets of conditions must be well understood and controlled in order for the product to be successful. A coating, for example, must be stable during storage, easy to apply using whatever application process is appropriate, and, ideally, the final surface finish should be smooth and drip-free. All three of these aspects of paint performance are linked to product rheology. As a result, rheological evaluation has become a key step in the development and monitoring of coatings.
The aim of this article is to provide a simple introduction to rheology, highlighting its applicability to the coatings industry. Basic rheological terms are defined, methods for their measurement are discussed with reference to the capabilities of rotational rheometers, and their relevance is outlined. A series of industrial examples highlights the practical benefits of rheological studies.
Rheological Terms
Rheological measurements can provide information relating to the fundamental structural properties of the material, and can be used to simulate the way in which a material will behave under a given set of processing or application conditions. The following terms are commonly used.
In addition, terms describing more complex aspects of rheological behavior relevant in the characterization of coatings have been defined.

Measuring Rheological Properties
Historically, flow cups and viscometers have been used to evaluate rheological behavior, but these systems, which only allow evaluation over a limited shear rate range, do not provide the information that can be obtained using a modern rheometer. Current instruments have a range of features that facilitate the accurate and effective study of many aspects of rheological behavior. The following are of particular relevance.
Accurate Temperature Control
As discussed above, viscosity is strongly dependent on temperature, which must be accurately controlled in order to simulate the conditions experienced by a coating sample, and to obtain reliable viscosity measurement.
Narrow Sample Gap
To measure the rheological properties of a material using a rotational rheometer, normally a sample is sandwiched between a cone and plate: shear is applied by rotating the cone. To allow accurate determination of the shear rate, rheometers have a narrow, precisely defined gap between the cone and plate. In contrast, some viscometers have a relatively large, less well-defined gap between the rotating surface and the surface constraining the material. When analyzing very viscous materials with this type of system, the parts of the sample furthest away from the rotating surface may be stationary, and, as a result, accurate measures of shear rate across the sample are very difficult to define.

With a rheometer, the speed of rotation of the cone is varied in order to apply different shear rates. A conventional viscometer can be used to apply shear rates varying by up to three orders of magnitude; with a rotational rheometer this range can be increased to 10 orders of magnitude. The dynamic range of the instrument is heavily dependent on the accuracy and range of speed measurement. Modern systems such as the Bohlin Gemini (Figure 2: Malvern Instruments) can accurately measure rotational speeds from one revolution per year to 6,000 rpm (relating to shear rates of over 105 s-1). Figure 3 shows the different shear rates to which an adhesive coating could be subjected. The ability to measure at shear rates that reflect these processes is key, and therefore a rheometer with a wide dynamic range is significantly more useful for product evaluation than a viscometer.
Oscillatory Measurements
Conventional viscometers tend to be continuous in terms of stress or strain rate application; with rotational rheometers oscillatory experiments are possible. These dynamic experiments allow the viscoelastic behavior of a material to be investigated. This creates a whole range of non-destructive tests that can probe a material's structure to predict product performance. Viscoelastic parameters determined by oscillation measurements include the storage (elastic) modulus G' and the loss (viscous) modulus G''. The relative magnitude of these parameters shows whether the a material's structure is viscous-dominated i.e., likely to flow, or elastic-dominated i.e., likely to be a stable structure. Viscoelastic measurements are made as a function of frequency to determine the dominant material response over different timescales.
Rotational rheometers often come with integrated software to allow automated control of the instrument. Sophisticated software is available that allows complete control and analysis of the critical parameters for research and developing new materials, right through to automated quality control routines with pass/fail reporting.
Case Studies
In the following examples the practical relevance of rheological studies is illustrated in more detail, with reference to some specific examples from the coatings industry.
The Rheology of High-Speed Roller Coatings
The rheological properties of high-speed roller coatings at both low and high shear rates are relevant to the design and formulation of an effective product. Low shear viscosity data can be used to predict behavior during storage, roller pick-up and leveling, whilst high shear-rate data gives information about the coating's transfer properties and mechanical stability.
Figure 4 shows data from measurements made across a wide range of different shear rates for three different samples of adhesive coatings. It is clear that at relatively low shear rates the viscosities of the three samples are very similar. With a conventional viscometer the samples would therefore appear to be essentially the same. At the high shear rates that are more representative of conditions to which the sample would be subjected during the application process, the behavior of the three is noticeably different. Sample A exhibits the lowest viscosity (at high shear rates) and, therefore, would be expected to have the best transfer properties. Sample C, on the other hand, shows a significant rise in viscosity, indicating mechanical instability.
The study illustrates how easily performed rheological measurements deliver data that can be used to develop and assess the performance of different formulations. By reducing the need for pilot plant trials and other costly investigations, such studies can make a useful contribution to minimizing the cost of developing successful products.
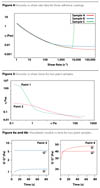
Predicting Paint Behavior
Paints are complex colloidal suspensions that usually contain a variety of components including extenders, pigments, flow modifiers and binders. During processing and application, paints are subjected to a variety of different shear regimes and so the formulation must be manipulated to ensure that all aspects of product performance meet requirements. In the production process for example, paint is pumped around the plant, subjecting it to moderate to high shear. Storage and transportation are low-shear processes. Application can vary from moderate (dipping) to high shear (roller coating, spraying). As the applied paint dries or is cured, surface tension and gravitational forces (low shear) have an effect.Figure 5 shows viscosity data collected for two paint samples. At low shear stress, Paint 1 is more viscous than Paint 2; Paint 2 has a lower viscosity. At high shear rates the viscosities are closely matched, resulting in similar properties during brushing. Low shear rate data indicate how the material is likely to behave as it dries and levels; these results indicate that Paint 1 is more likely to show brush marks than Paint 2. Paint 1 has the higher viscosity and therefore a higher resistance to flow - something that would smooth out brush marks under low gravitational stress, which is the major force acting on the sample. Obviously the paint requires an appreciable viscosity at these shear rates, otherwise it would have no resistance to flowing off the surface completely!
Combining a pre-shear condition with oscillatory (viscoelastic) testing provides information about the thixotropic time-dependent structure re-build of a paint following application. The initial pre-shear step, at a reasonably high shear stress (or shear rate), simulates the process of brushing the paint onto a substrate. The continuous shear is stopped and the material is then subjected to a low-stress oscillatory test at fixed frequency to study the structure re-build that occurs in the paint.
As mentioned earlier, it is important that the paint flows sufficiently after application to allow leveling to occur, but not so much that it sags. In terms of the viscoelastic rheological parameters obtained from oscillatory testing, this means that immediately after the shear condition, the loss (viscous) modulus G'' should dominate the storage (elastic) modulus G', such that some flow is possible to allow the paint to level. At some finite timescale there should be a crossover in behavior such that G' becomes dominant. From this point, the material response shows gel-like properties and is unlikely to continue flowing, having achieved the desired surface finish. Figures 6a and 6b show the viscoelastic response of two paints after rotational shear. The curves indicate that paint 3 (Figure 6a) may show excessive sag behavior, as the loss modulus G'' is always the dominant parameter. Paint 4 should exhibit good levelling and sag properties due to the structure becoming elastically dominated after a finite period.

The Impact of Temperature on Product Properties
Rheometers can also be used to investigate how rheological behavior changes with temperature, and hence to assess the suitability of different products for high-temperature applications. Viscosity versus shear rate was measured for a sample at several temperatures in the range 20 to 65 ºC (Figure 7). As expected, viscosity was found to decrease with increasing temperature at all shear rates at temperatures below 50 ºC. Above this temperature however, at low shear rates, more unusual behavior was observed and high-viscosity values were recorded. These viscosity values are attributed to flocculation in the sample showing that this formulation is unlikely to be suitable for high-temperature applications. Higher shear rates are insensitive to this flocculation because the higher forces involved simply break down the structure.Conclusion
Rheological properties describe key aspects of the behavior of materials and are therefore important in terms of rationalizing product performance and developing new products with the required properties. During processing and application, paints and coatings are subjected to different shear rates, and it is important that rheological evaluation of these materials takes this into account. Rheometers are designed to allow valuable rheological studies to be performed efficiently, enhancing the accessibility of relevant data. The case studies discussed clearly illustrate the practical value of this data.Looking for a reprint of this article?
From high-res PDFs to custom plaques, order your copy today!