A History of Wood Restoration

Wood has been used as an article of construction since before the dawn of civilization. One of the earliest methods of increasing the durability or longevity of wood was fire, hardening the tip of a wooden spear or arrow. This caused the resins in the wood to harden more than what was produced by the living tree, giving a stronger, more durable point that could pierce simple leather armor, and efficiently kill game animals. This process also sterilized the wood, which was important since the varieties of fungi that eat wood are many and common.
Some varieties of wood also contain natural antibiotics; when present, these help to give the wood longer life by giving resistance to the microorganisms that regard wood as food.
Wood used for weapons or other utilitarian articles tended to wear out before it rotted, while wood used for construction tended to rot before it wore out. In relative terms, wood wore out quickly but rotted slowly.
Wood used for architectural purposes only exhibited long life under extremely cold conditions or when in an oxygen-free environment, as the microorganisms that feed on wood require oxygen. The air contains about 20% oxygen.
Old wooden ships hundreds of years old and buried in mud have been found, and wooden ships and buildings hundreds of years old and in very good condition have been found in Arctic climates such as Alaska and northern Canada. It is possible that the fabled ark of Noah, several thousand years old, has been found entombed in ice on Mount Ararat in Turkey.
When wood was used at temperatures where fungi and bacteria are active, the only known technology of "restoration" was to cut out the deteriorated area and glue in a fitted replacement portion. In ship repair, in the last hundred years, the insert was known as a "Dutchman."
For general repair and preservation, hot tar might be used. While creating a somewhat waterproof seal with little physical strength, hot tar tended to sterilize the wood and this - plus the tendency to seal the wood from the air at the location where the hot tar might be applied - contributed to the longevity of this technology. The Indians of the North American continent used tar as a sealant for birch bark canoes.
Tar, pine pitch or a mixture was commonly used as a sealing compound between the deck planks of wooden ships hundreds of years ago. The material was heated and poured into the seams where it solidified. The decks were thus sealed against water and rain leaking through to the cabins below. The sailors were usually barefoot and on hot days the tar would melt and transfer to the soles of their feet. British sailors thus acquired the nickname "tarheels."
The surface protection of wood was accomplished by treatment with the oils of various beans, berries or seeds, which had been found to dry and harden on exposure to the air. Today we call this material varnish. Joints between separate pieces of wood on older boats were usually filled with a paste of fibrous material, lead oxide and various vegetable oils or varnishes. The lead oxide served as a primitive fungicide to deter the rot that would begin when the inevitable fungus spores, carried by air or water, got into the space between two pieces of wood and proceeded to hatch, grow, and eat the wood.
An early method of increasing the rot resistance of wooden ships was to paint the masts, spars and other parts black. This absorbed more heat from the sun, dried out the wood after it had been rained upon, and thus created an inhospitable environment for fungal growth.
The marine environment is hundreds of times more severe than the architectural environment, in terms of both dampness and mechanical stress. Technology was thus forced to develop for marine maintenance and restoration, where little technology was forced to develop for architectural maintenance and restoration.
The Dawn of Contemporary Wood Restoration Technology
In the 1950s Shell Chemical Co. invented a commercial process for manufacturing a type of resin (which they called "epoxy" for technical reasons) and a variety of curing agents for it. The family of adhesives and coatings developed from these products turned out to be surprisingly versatile and compatible with a wide range of wood and metal and concrete materials. The U.S. Department of Defense rapidly developed improved versions of these paints and adhesives in their own research laboratories, to meet a range of military applications. They then solicited bids from the existing paint industry to manufacture these formulations. The industrial community was thus given a "jump-start" in commercializing products based on epoxy resins, as they now were known.Many large and small companies began to make "commercialized" or lower-cost versions of military formulations and to offer them to industry and the general public for just about any possible application, with no serious applications technology. By the late 1960s and '70s many small businesses had developed architectural maintenance products that were moderately successful, although a common failure mechanism was that at some later date an epoxy filler in the wood might come loose and rise up under a coat of paint, or rot to start up again behind a spot that had been "treated" with some "restoration" product.
These architectural maintenance products could not cross over successfully into the marine market place, as the quality of restoration possible in the architectural market was such that with luck a repair might last five or 10 years; in a marine environment that same quality of repair might last three months to two years. The technology was not viable in the more severe marine environment and only barely viable in the architectural environment. Thus, there were no epoxy restoration products that were successful for either the marine or architectural market places.
In 1972 I became aware of the need for something to handle deteriorated wood on boats, from a friend in the marine business. I developed a product and told a friend to try it. The short-term results were so successful that a demand appeared almost overnight, and the first formulation of Clear Penetrating Epoxy Sealer(tm), embodying the fundamental principles of the technology (though far from optimum) was introduced to the marine marketplace. By 1976 the product had spread to the architectural restoration marketplace, a filler and a glue had been added to the product line, and sales volume had dramatically increased, with the business growing from one person to six employees.
Meanwhile, the technology was evolving and becoming optimized and more refined as the actual needs of the end users became better understood. Various painting contractors and remodeling contractors had begun to use the products for routine maintenance and restoration. The State of California Department of Parks and Recreation discovered these products, evaluated them and began to use them for the restoration of various historic structures.
A boat builder who happened to be working for the U.S. Government, stationed on Kwajalein Atoll in the South Pacific (part of the Pacific Missile Test Range), found that the epoxy sealer was useful in the maintenance of the wood buildings on Kwajalein, which housed the radar and electronics gear. Thereafter anywhere from 30-200 gal every few months were sold to the U.S. government and shipped to Kwajalein for continuing restoration of the wood buildings. This is significant because Kwajalein is hot, humid and gets about 100 inches a year of rainfall. The product was successful in maintaining old and new wood buildings that previously were simply torn down and replaced every few years. This continued through the end of the Cold War and even though many of the old wood buildings have been replaced with concrete, some wood structures remain and use of this product continues today.
Thus, once a viable technology for the restoration of deteriorated wood in a marine environment was developed, it spread and expanded rapidly in the architectural maintenance market place since it was an inherently viable technology.
The Modern Technology that Restores Deteriorated Wood
The technology underwent significant refinements in the laboratory in the late '80s and early '90s but none of this was released to the public since it was felt that a better customer-training program would be needed to take advantage of the latest refinements. The present customers had learned about the products through word-of-mouth or some limited advertising, and the only training possible for mail-order customers was the enclosed literature package.The technology had gained great acceptance among end users, including some pest-control operators who used the product to restore deteriorated wood despite written rules from their regulatory agency stating deteriorated wood must be removed. The technology did not have a theoretically derived origin but rather an experimental one. Thus, no authorities in the Forest Sciences Departments of Universities had evaluated the product and measured the properties of restored wood and certified that some percentage of restoration could be reproducibly achieved and measured under standard test conditions. In reality, this is impossible, since there is no such thing as a standard piece of rotten wood. Thus, no restoration standard was possible.
City building inspectors were now commonly coming into contact with the products and their use in a variety of circumstances, and more questions arose, as restoration of deteriorated wood was not covered by any building code. Yet people were using it and it seemed to work. The test was to jab the wood with an ice pick to assess the state of deterioration by the degree of penetration. After treatment with the Clear Penetrating Epoxy Sealer, the treated wood resisted penetration by an ice pick in a similar manner that new wood did.
Thus, restoration was accomplished in fact if not in law. In 1997 a surrogate standard for deteriorated wood was invented, with the discovery that the common cedar shingle had a very similar absorption of the epoxy sealer as lightly rotted wood. A series of tests were then done, using the Professional Version(tm), comparing treated wood and untreated wood, and actually measuring the effects of restoration of wood with this technology. The results are published at www.woodrestoration.com.
The building code and pest control operator regulations do now address restoration. References are cited at the end of the above publication.
The Future of the Restoration of Deteriorated Wood
The development of the professional versions of these products has now been accomplished, based on the knowledge gained, refinements, field tests and evaluation of the last 24 years. The trademark Lignu(r) was created and registered to denote the modern, high-performance family of wood restoration products. A training program and checksheet has been designed for Trained Applicators, employed by Licensed Restorers. Thus, the first barriers to mass distribution of the technology and its products have been removed.In the spring of 2001, the Lignu Specification was published at www.lignu.com, and the State of California Department of the State Architect approved that specification for restoration of deteriorated wood on all State property including schools.
Wood has been commonly used in construction for hundreds of years, and will certainly continue to be for hundreds more, due to the low cost and high production rate of wood by the natural vegetable life forms of this planet. Since the technology relies on restoration of deteriorated wood using, in great part, materials actually derived from wood, it is expected that these products and this technology will persist as long as wood itself is used in architectural construction.
For more information, contact The Lignu Technology Institute of Wood Restoration, 5100 Channel Avenue, Richmond, CA 94804-4646; phone 510/237.5986; fax 510/232.9921; visit www.woodrestoration.com or www.lignu.com.
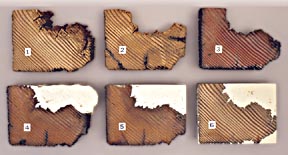
The Lignu Technical Institute of Wood Restoration
The process of wood restoration begins with the removal of completely decomposed wood, as shown in #1-3. The restorable wood is then impregnated with Lignu Impregnating Resin. Missing portions of wood are replaced with one of several Lignu fillers, chosen for the particular application circumference.The Lignu fillers are made from resins derived from the natural resins of wood. The final result is deteriorated wood restored, capable of many additional years of service.
Links
Looking for a reprint of this article?
From high-res PDFs to custom plaques, order your copy today!