Five Steps to Fast, Precise Color Matching
There are three stages in the manufacturing process. The first is the actual batching itself. Barring unforeseen difficulties, one can reasonably estimate the amount of time this will take. The last stage involves filling and packaging of the finished product. Again, one can usually estimate with some certainty the length of this step.
The unpredictable phase of manufacturing paint typically lies with the middle step. This is when adjustments to each batch are made. Adjusting for properties such as viscosity and gloss are relatively easy. The more difficult adjustments are those that deal with color corrections or bringing material “on shade.” The fewer the number of these corrections, the more efficient and profitable the process becomes. There is a tremendous difference between a batch that requires three hits and one that requires 13. Those who can minimize the overall number of corrections establish a definite advantage over their competitors.
Following are six major color challenges facing the coatings industry today.
- Custom color matching — Is it fast and responsive?
- Product colors quality control — Are colors on-shade every time?
- Product deliveries — Are they “just in time”?
- Colorant expenses — Are they minimized?
- Scrap (waste) product — Can it be eliminated?
-
Scrap (waste) product — If it can’t be eliminated, can it be worked off effectively?
If these six items can be addressed successfully, then color can be managed efficiently and profitably. The best means by which to achieve these goals is through the use of computer color matching. While computer color matching could never replace the use of your eyes, it does offer the following advantages.
- Faster match turnaround that reduces metamerism by matching under multiple illuminants.
- Reduced formula costs by maximizing hiding while minimizing the amount of pigment needed to achieve it at a specified film thickness.
- The ability to establish numerical color tolerances to enhance pass/fail decision making.
- To help with “just in time” deliveries, the system should offer reliable color correction capabilities.
- Comprehensive capabilities to work off waste into new products.
Five central issues must be evaluated and analyzed before choosing a color-control system.
First, you should have a working knowledge and understanding of color theory and matching. This enables an educated decision to be made based on what is needed from a color-control system.
Second, the color-control system you choose should make available the use of expert-based technology to improve the success rate of new color matches. This technology should be based on historical information that is generated and saved by the user.
Third, you must be sure the software package’s capabilities meet your needs and is user friendly.
Next, displayed formula output should be manageable so that the information is in the right format and ready-to-use.
Last, you must make sure that color correction and recycling capabilities will operate effectively in real-life production applications.
If attention is paid to these five steps, then choosing the correct color-control system becomes easier. Following is a review of each step, providing a more comprehensive understanding of each.
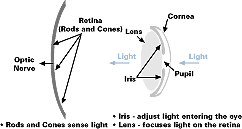
Step One: Understanding Color Theory
An understanding of color theory and matching is an important tool in evaluating the effectiveness of a color-matching system. Unfortunately, today there is a perception that these systems have become commodity items and, therefore, can be purchased and even operated by people who have no real understanding of color. This perception is false and often leads to mistakes being made during this process. These mistakes usually end up with one or more parties left with a sour taste in their mouth and ill feelings about each other. These can be prevented if knowledgeable individuals are brought into the decision-making fold.There are nine basic areas of color theory to consider. Following is a brief identification and explanation of each.
First, an individual should understand the theory of light, the visible spectrum and the prism. Visible light is a small portion of the electromagnetic spectrum. The electromagnetic spectrum covers everything from cosmic rays to UV rays to TV and radio waves. Wedged into the middle of these is the visible spectrum. Measured in units of nanometers (a billionth of a meter), the visible light spectrum lies within the range of 400–700 nanometers. Our eyes determine color based on the amount of light that is reflected back in any particular portion of the spectrum. Therefore, a phthalo blue pigment reflects its majority of light between approximately 420–480 nanometers, while absorbing light elsewhere throughout the spectrum. A green shade yellow may start reflecting light around 500 nm, while a redder shade yellow would start reflecting the majority of its light around 520 or 530 nm. The reason this yellow is a redder shade is because it absorbs more light in the green bandwidths of the spectrum. A spectrophotometer uses a prism to separate white light into its various wavelengths and therefore create a spectral “fingerprint” of a shade. In the real world, either an individual or a piece of software attempts to create a recipe of multiple pigment components that, when combined, ultimately reproduce the “fingerprint” of the target color.
Whether a human being or color-matching software is successful depends on many factors. First are the pigments available for use. I will guarantee that no software will be able to match a white shade with three black pigments. But I will also guarantee that no human will be able to do so either. Next, process control is very important. Without process control, predicting or calculating an adjustment becomes unreliable. Process control involves application, curing of the sample, etc.
Next, an understanding of the human eye is necessary. The eye allows light to pass through the iris, which adjusts the light as it enters the eye. This light is then passed through to a lens, which focuses light on the retina. The retina is made up of a series of rods and cones, which pass light through to the optic nerve (see Figure 3) that interacts with your brain and allows you to sense color. Everyone’s eyes see color differently based on factors such as age, fatigue, the influences of alcohol and/or drugs, certain foods, and a host of other variables.
The third point is that three criteria must be present to interpret color. One needs light, an object and an observer. If one or more of these is missing, color, as we know it, ceases to exist.
Metamerism and its effect on us needs to be understood. Metamerism is present when two objects match under one light source, but fail to do so under another. The most common cause for this is because one sample contains a pigment or pigments that do not exist in the other sample. As an example, samples match under daylight but mismatch under incandescent lighting. Since color is one of the primary motivations behind consumer purchases, the presence of these phenomena can spell trouble.
Fifth on the list is standardizing viewing methods of samples. I have visited many customers over the years and perhaps 90% of them have a light booth of some type in their laboratory. Of this number I would be surprised if 30% of them actually use it. Light booths supply us with an objective means of evaluating colors visually. Many color acceptance issues would simply disappear if control labs actually used this tool on a regular basis.
Understanding numerical color space is vital in these operations as well. While numbers themselves do not always agree with what we see, they still present a clear and objective means by which to evaluate color. A working knowledge of all color coordinates is important and reduces communicating color with phrases such as “a little redder” or “two shades more yellow.” These expressions are entirely subjective and very difficult to understand — 10 individuals will have 10 different interpretations. Using numbers means we all start and stop at the same point. This could allow different individuals to produce the same color at different locations without ever talking to one another. The most commonly used color space in the coatings industry today is the CIE system, although some sectors of the coatings industry still use FMCII and Hunter Lab, and to a lesser extent CMC.
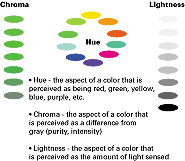
Color tolerancing allows suppliers and customers to establish real limits when it comes to color matching. Used properly, these tolerances allow a supplier to match within agreed upon numerical limits. Once sensible limits are established, a supplier should be able to match within these limits secure in the knowledge that their customer will accept shipments that fall within the specified tolerances. If shipments fall within the numerical window and are rejected by the customer, then the existing tolerances should be reevaluated and modified if necessary.
Last, but not least, is the type of spectrophotometer needed for your system. Datacolor provides a series of flash instruments using MC-90 spectrometers (see Figure 5). This technology allows for close tolerance measuring capability and excellent inter instrument agreement of under a .15 Cielab Delta E maximum. These instruments are also fully automatic and include specular component included and excluded measuring capabilities. Other features include aperture detection, sample viewing zoom lens and a light source ultraviolet calibrator. Whether your choice is a benchtop or a handheld instrument, all are xenon pulse flash instruments, which minimizes sample heating and, as a result, erratic measurements. Remember that a spectrophotometer is as important to your success as the lab techniques addressed earlier.
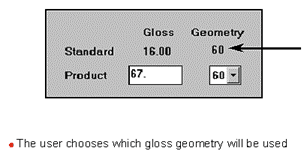
Step Two: Use Expert Technology
The next factor to consider when evaluating a color system’s value is whether the software itself contains advanced technological functions. Two functions of particular value are gloss compensation and the use of historical formula information contained in a color library to further improve initial formulations.Gloss compensation enables formulas to be calculated while considering visual differences due to gloss differences between two samples. This is a mathematical compensation using “gloss values” generated by a spectrophotometer (see Figure 6). This mathematical compensation adjusts the actual measured curves, such as of a glossy sample and a flat sample. The perfect example would be that of a gloss black and flat black. Using traditional specular included measurement information the calculated numerical differences would be minimal. This would belie what your eyes actually see, in that the flat sample would appear to be much lighter due to the presence of gloss altering inert ingredients. When applying these gloss values to the calculations, the adjusted curve of the flat sample would shift up, while the glossy sample would shift down. When using this information to calculate color differences, we now have values that indicate the flat sample is considerably lighter, agreeing more with your eyes. When we apply the same principal to actual formulation and matching, the calculated formulas compensate for these differences by adding more or less white, while normalizing the other ingredients.
Another useful feature allows users to draw on historical formula data to improve initial color matching. Users populate a color library with samples he or she makes in their everyday work. No special preparation is needed as long as the operator knows, with reasonable certainty, what components made up a particular sample. Therefore, any drawdowns or sprayed panels that are generated from either a QC or development laboratory are prime candidates for the color library. These samples are then stored and the system calculates certain performance or behavioral information about the colorants used in this sample. When future unknown colors are matched, the software will draw on this information and attempt to correct stored formulas that are close to the target. In the process, the performance data is applied so that differences in colorant performance are adjusted for and the initial formula is displayed using these adjusted colorant amounts. When used properly, the color library reduces laboratory trials considerably, thus saving time and money. Datacolor International’s Data Match color matching software employs both of these advanced features.
Step Three: Color-Matching Capabilities
Next, we must look at the software’s actual matching capabilities. The best color-control systems use different mathematical models for different types of coatings. For instance, a model for transparent stains should exist where no TiO2 is present in the formula but substrate is a major factor in the match. This model should treat the substrate as another “colored” component in the match.Another model should be available for TiO2-containing coatings that only partially hide the substrate but where the substrate is a contributing factor in the finished match. This substrate needs to be characterized. The last model should handle opaque or very nearly opaque coatings as well where substrate doesn’t influence the final color we see.
The right software should also include features that allow users to scale the formula by various methods. For instance, you should be able to base the predicted formula on the total amount of white you want present. Or, you could scale the formula based on the amount of vehicle needed in the match.
Another useful option is one that enables loading and opacity options. These options have the potential to save tremendous amounts of money since they allow you to maximize the degree of needed hiding while minimizing the amount of pigment necessary to do it. Available with this is the ability to match at varying film thickness that will further adjust pigment load.
Step Four: Formula Management
Formula display and management features should be plentiful and easy to use. Formulas should be able to be displayed and scanned easily and in a format that is useful to users. Multiple-formula forms should be available. That is, the same formula should be able to be expressed in a dispersed paste mode and an equivalent form of dry pigment using conversion factors the user supplies the software.These formulas should also be able to be displayed in single-formula detailed format or multiple-formula spreadsheet formats. While the single formula display offers a greater quantity of information about the recipe, the spreadsheet allows one to view multiple formulas easily and perhaps choose a more desirable pigment combination before viewing that combination in detail.
Sorting capabilities are also important. After the software has processed all possible combinations (with the factored number based on input information) it must now be able to sort or order them according to specific criteria. Options such as ‘curve fit sort’ and ‘Delta E sort’ should be available, as well as ‘order based’ on the amount of recycles used and cost. The user should be able to change the presort method with the click of a mouse.
One last feature should be the program’s means of storing information for easy future recall. If one combination, when put to trial in the lab, does not work or produces an otherwise undesirable result, the user should be able to easily recall the other calculated formulas so that another choice can be made.
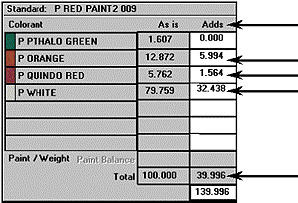
Step Five: Color Correction and Recycles
Last, and most important, are the correction and recycle options available for use. This article stated that the single most important option a color-control system can have is its correction capabilities. Without accurate corrections, the system loses a great deal of its value. This is important in the lab, but much more so in a production environment. Saving time translates directly to dollars saved. One less color shot per batch extrapolated over a year would result in an enormous cost savings.Even personnel with limited color-system experience should easily and conveniently run corrections. Datacolor’s correction programs have always been the strength of their software packages. They allow users to exercise numerous options, including automatic correction where the software tells you what to add in order to obtain the best possible match based on the batch size (see Figure 7). Sometimes a match doesn’t need to be “perfect” and the operator using a manual adjustment mode can reduce colorant adjustment amounts. This mode enables the operator to match to a target other than zero. If added colorant amounts are reduced, further cost savings are realized. All the while, the theoretical color difference is modified to reflect the amount of colorant you wish to add. Unlike actual production, if an operator overshoots the color within the correction program, no harm is done since they can easily back that amount out and try again. Until you actually decide to physically add to the batch itself, an operator can experiment endlessly. This also proves to be a valuable educational tool as well.
Recycle opportunities are also necessary tools. With environmental concerns today, it is extremely valuable to be able to work off materials in an expedient manner. The program should be able to not only treat the waste material as another colorant in the match, but should also be able to consider the amount of recycle material you have available to match with. What good is a formula that would work if you only had an additional 25 pounds of rework but don’t? Using Data Match and its recycle options, not only can this be considered when formulating but multiple wastes can be tried at the same time.
Summary
Choosing a color system is an important decision for a company to make. It is also not an easy one. Whether you are a large manufacturer with 10 locations, or a small single niche supplier, owning one today is vital to maintaining a competitive advantage. This article is designed to help you understand what needs to be evaluated in order to make a choice. Remember, not all color-control systems are equal. Therefore, choosing one should be based on what your individual needs require and the ease of use of the system itself. Look them over and choose wisely.
For more information on color matching, contact Datacolor International, 5 Princess Road, Lawrenceville, NJ 08648; phone 800/982.6497; visit www.datacolor.com; e-mail
marketing@datacolor.com.
Links
Looking for a reprint of this article?
From high-res PDFs to custom plaques, order your copy today!