Characterization of Substrate Surface and Coatings Using Advanced Analytical Tools

For a durable adhesion, a pretreatment of the substrate is inevitable. The substrate often needs to be cleaned before a primer/coupling agent/plasma is applied. An extremely accurate and reliable characterization of the substrate surface at the nanometer scale is imperative. AFM, contact angle, ESCA and TOFSIMS are extremely useful techniques for combating contamination and providing quality assurance for reproducible pretreatment.
As a substrate is coated and cured with a urethane/epoxy system, for example, advanced thermal analytical techniques like MDSC, DM(T)A and DE(T)A are proving to be successful tools in ensuring the application and quality of the coating materials. An in-depth understanding of the structure property relationship with regard to mixing ratio and cure mode of the coating materials is a pre-requisite for their successful application and long-term durability.

Introduction
Most coatings are the result of the marriage between two different materials - an organic or an inorganic substrate and a polymeric resin - that form adhesive bonds with each other. The quality and durability of a coating is directly related to the nature of adhesion. Chemists tend to associate adhesion with the energy liberated when two surfaces meet to form an intimate contact termed as an interface. In other words, adhesion may be defined as the energy required to dismantle the interface between two materials. Physicists and engineers usually describe adhesion in terms of forces, with the force of adhesion being the maximum force exerted when two adhered materials are separated. There are many theories regarding the mechanism of adhesion - such as adsorption (van der Waals forces), electrostatic, diffusion (entanglement of polymers with a substrate), chemical bonding, mechanical interlocking etc., - all of which may play a significant role in interfacial bonding. The energy required to separate the coating and the substrate is a function of the adhesion level i.e., interactions at the interface, but it also depends on the mechanical and viscoelastic properties of the materials.When a polymeric coating is applied on a substrate, a chemical reaction takes place if each surface contains functional groups. It is often desirable to modify the substrate to ensure the reactivity at the interface by removing contamination and/or introducing functional groups. This simplified view of the interfacial or interphase bonding neglects physical forces between two materials that are influenced by variables such as surface roughness, for example. For a comprehensive characterization of coatings, surface analysis of the substrate (chemical as well as topographic) and thermal analysis of cured polymeric coating materials is of great importance.
The purpose of this work is to underline the importance of the substrate surface and the polymer (coating) viscoelastic/thermal properties for a durable adhesive behavior of polymer/substrate assemblies.

Surface Analysis
It is almost impossible to list all the factors that may affect adhesion of protective coatings because of the broad range of substrates that can be involved, or the variety of organic/polymeric materials utilized in coatings. Some aspects/contributions of FTIR (Fourier Transform Infrared Spectroscopy), ESCA (Electron Scanning Chemical Analysis), TOFSIMS (Time Of Flight Secondary Ion Mass Spectroscopy), AFM (Atomic Force Microscopy) and contact angle techniques are mentioned in Table 1.1FTIR is based on the absorption of infrared light as it passes through the sample. The IR spectrum, the amount of transmitted energy as a function of wave number, is obtained.
Generally, the FTIR surface techniques can be classified in two categories: reflection (ATR: attenuated total reflection) and non-reflection techniques (PAS: photoacoustic spectroscopy).
PAS utilizes the detection by a sensitive microphone of an acoustic signal emitted from a sample after absorption of a modulated radiation. This technique is proving increasingly useful for oxidation depth profiling of a polymeric surface after corona or plasma treatment.
FTIR has its limits when <10 nm depth of surface penetration is involved for characterization.

ESCA
In ESCA (also known as XPS), the sample is bombarded with soft X-rays, and the photoelectrons emitted are analyzed in terms of kinetic energy. For elemental surface analysis in the range of 1-5nm, ESCA has proved to be very useful. In Table 2, O/C ratio of a PP surface is analyzed with the help of ESCA and correlated with advancing and receding contact angle findings.
O/C ratio of at least 0.12 was found to be desirable for PP in printing and metal coating after surface treatment. ESCA is a very useful analytical tool for surface elemental analysis and also for establishing a correlation between the elemental composition and contact angle observations. ESCA has also been very helpful in monitoring the aluminum surface after plasma etching.2

TOFSIMS
The sample is bombarded with primary ions of 15-25 KV and the secondary ions are extracted perpendicular to the sample surface before being deflected to the detector. Whereas ESCA involves characterization of 1- 5nm surface depth and is mainly helpful in quantitative elemental analysis, TOFSIMS is suitable for surfaces < 1nm and gives information about molecular structure of monolayers at the surface. These two techniques complement each other quite often.TOFSIMS is a very effective method of detecting silicone (PDMS) and other release agents/surfactants frequently encountered as contaminants on metallic and polymeric substrates. Surface contamination is the most important enemy of surface engineering. What is more important is not a clean surface, but a CONTROLLED one. Surface analysis is the most effective weapon against the enemy. ESCA helps in quantifying silicone by measuring Si-content as a complementary technique to TOFSIMS, which is an excellent technique for detecting minute traces of contaminations/surfactants and release agent residues. Silicones, stearates, bis-stearamides, fluorinated hydrocarbons, anionic, cationic and nonionic surfactants represent typical examples.
Coupling agents like epoxy- and amino silanes are often applied as very thin layers on substrates like steel/aluminum before a polymeric coating is applied. In many cases, only TOFSIMS is able to characterize the very thin layer of the coupling agent on the substrate (Figure 1).
ESCA and TOFSIMS analyses have to be carried out at high vacuum, which is a disadvantage.

AFM
Surface roughness contributes to the adhesion of paints/coatings by way of interlocking. The level of surface roughness needs to be controlled accurately. Atomic Force Microscopy is being increasingly employed for characterization in the sub-micron range.
Figure 2 shows roughness induced at the PP surface by corona treatment.
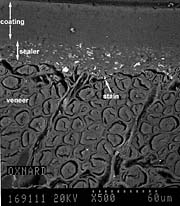
Characterization of Cure Mode of Polymeric Coatings
The strength and durability of polymer coatings is a combined effect of interfacial and cohesive factors. Besides the interface, cohesive properties of the polymeric coating bulk are very important. The cohesive energy is determined largely by the molecular structure arising from careful curing of coatings; cure reactions can be monitored by thermal analysis.3MDSC (Modulated Differential Scanning Calorimetry)
DSC has been employed for over two decades for investigating cure kinetics of adhesives/coatings. With rising demands of high-performance coatings, the resolution and sensitivity of this technique became inadequate.
MDSC, a recent development of conventional DSC, has gained importance by overcoming the limitations of the latter. Specifically, a sinusoidal modulation of the heating profile is overlaid on the conventional linear heating. The net effect - i.e. increased resolution and sensitivity - is the same as if two experiments were run simultaneously. MDSC separates reversing and non-reversing components of the heat flow, so that the real glass transition temperature, Tg, is determined from the reversing heat flow curve (Figure 3).
DMTA (Dynamic Mechanical Thermal Analysis)
DMTA defines the extent of cure and hence the molecular architecture by measuring modulus and mechanical damping or loss with respect to temperature and frequency.When a sinusoidal stress is applied to the (viscoelastic) sample, the strain response lags behind the stress applied. E* is then resolved into E' (elastic/storage) modulus and E'' (viscous / loss) modulus components.
The ratio E''/E' = tan d, often referred to as mechanical loss or damping, is a very useful parameter.
The peak maximum of tan d is defined as Tg of the cured adhesive/coating (Figure 4). DMTA (also known as DMA) is an extremely sensitive and useful technique but has the obvious disadvantage of sample geometry and preparation.
DETA/DEA (Dielectric Thermal Analysis):
In the presence of polar groups in the coating materials (for example, epoxies and PUs), this technique has proved to be the most sensitive of the three techniques mentioned here. A sinusoidal electric field is applied to the sample and the electric displacement followed. The complex dielectric permitivity e * obtained can be resolved into the storage component e ' and loss component e ''. The dielectric loss tan d = e ''/e ' is determined with respect to temperature. The higher degree of cure (165 °C) is manifested in decreased dielectric loss (denoted by "xxx" in Figure 4). The coating denoted by "ooo" in the figure was cured at 145 °C for the same period.
DETA is very sensitive for detecting moisture absorption at the interface and in the polymeric bulk material. This technique has also the disadvantage of sample geometry and preparation.
Conclusions
Strength and durability of coatings depend very much on the integrity of the interface and the dimensional stability of the polymeric coating substance after cure/crosslinking reactions. For high-quality products, an accurate characterization of the substrate surface and cure mode of polymeric coating is of utmost importance.
A combination of advanced analytical techniques ESCA/TOFSIMS has become increasingly essential for understanding the role of the interface. Besides the interface, the other important step is to look at the cohesive properties of the polymeric bulk. MDSC and DMTA, DETA (provided polar groups are available in the polymer) have proved to be the most powerful complementary techniques for quality assurance of cured resins and are responding well to the demanding applications of coatings.
Acknowledgement
MDSC, DMTA and DETA/DEA experiments were carried out at Comtech GmbH for which the author is thankful to Mrs. Christa Pflugbeil. ESCA and TOFSIMS analyses were conducted by our cooperation partners on contract basis. c
For more information, contact Dr. Amir Hussain, Comtech GmbH, e-mail comtech-labor@t-online.de, or visit www.comtech-labor.de.
References
1 A. Hussain, A. Haftungseigenschaften unter Kontrolle, Kleben & Dichten, Jahrgang 40, 9/96 .2 Turner, R. H.; and Boerio, F. J. J. Adhesion 78, 465-494 (2002).
3 Hussain, A. Characterisation of the Cure of High-Performance Adhesives by Various Techniques, Structural Adhesives in Engineering V, Fifth Intern. Conf., Bristol, 1-3 April 1998.
This paper was presented at the 7th Nürnberg Congress, European Coatings Show, April 2003, Nürnberg, Germany.
Looking for a reprint of this article?
From high-res PDFs to custom plaques, order your copy today!