
Coatings on wooden substrates for furniture, flooring and interior are a main application for radiation curing lacquers. Increased adhesion is an important target for development of UV coatings on wood. Superior adhesion leads to better whitening behavior (coin test) and abrasion resistance.
Guidelines to improve adhesion on wood are:
- Swelling of wooden fibres with waterborne UV primers to increase the substrate's surface area and its interaction with the coating.
Better wetting of oily surfaces e.g., teak, mahogany or rosewood by using coatings with low surface tension.
Chemical crosslinking of coating and substrate.
The surface of wood is seldom homogeneous. Varying surface tension (e.g., caused by oily components from the wood) and phenolic components with inhibiting effects on UV cure have a negative influence on the adhesion of coatings. Additional problems may arise from the very fast UV curing reaction during which a high amount of internal stress is built up in the coating.
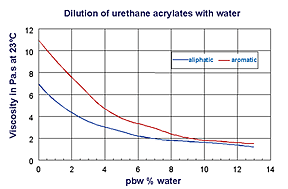
Waterborne UV Primers
The right choice of waterborne UV curing primers solves many of the above-mentioned adhesion problems. Water, together with the dispersed or dissolved polymers, is rapidly absorbed by the wood pores and capillaries. Fibers are swollen and lifted up, which increases the substrates surface area. Waterborne UV curing coatings are available as water-reducible/water-containing resins, emulsions or dispersions2 of different chemical nature. Figures 1-2 compare the relative properties of emulsions and dispersions. The best overall properties are achieved with polyurethane systems.Polyurethane dispersions are generally produced by the polyaddition of diisocyanates with bivalent compounds that react with isocyanates. Emulsifying groups such as polyether or ammonium carboxylate (internal emulsifiers) are also incorporated into the polyurethane structure. The key factor in UV curing PUR dispersions is how the acrylic double bonds enter the polymer. Previously, the only dispersions known were those in which hydroxyfunctional acrylate monomers such as 2-hydroxyethyl acrylate were used as the UV curing component. As these acrylate monomers are monofunctional components, which stop the formation of the polyurethane polymer, it is very difficult to produce high molecular weights with an adequate density of double bonds.
Recent developments no longer use monomeric acrylates as the double bond components but rather oligomeric or polymeric compounds such as polyester and epoxy acrylates, which have their own hydroxyfunctionality. Figure 3 shows the structure of high-molecular-weight PUR dispersions.
The combination of different components allows the specific design of UV curing polyurethane dispersions. By varying the saturated and unsaturated polymer building blocks, by choosing different diisocyanates, by using monomeric diols or diamines - also mono- or polyfunctional building blocks - and by varying the process technology, the properties of the polymers can be customized. Examples of such properties are physical drying, UV reactivity, hardness and elasticity, glass-transition temperature (Tg), and other solids-related properties of the paint film.
Also urethane acrylates that can be formulated with about 10% water for roller coating application are well-suited for application on wood (see Figure 4). Here, the amount of water that has to be forced out of the coating during drying is minimized. Figure 5 summarizes the advantages of PUR dispersions, PUR emulsions and water-reducible urethane acrylates.

Optimizing UV Resins
If the use of waterborne material is not possible for a given coating process, resins with a reduced shrinkage during polymerization and improved wetting are needed. Figure 6 compares a standard polyester acrylate with an unsaturated polyester in DPGDA. With the latter, good adhesion - especially on oily wood types like mahogany, teak or rosewood - is achieved. The lower double-bond density, however, means a reduced UV reactivity.Wood contains many phenolic compounds, which have similar chemical structures compared to the substances that are commonly used to stabilize acrylate resins. In a model experiment, commercial-grade hexanediol diacrylate (HDDA) was used to extract shredded teak wood (3 pbw. HDDA on 1 pbw. teak). Analysis of the extract by means of GC-MS revealed substantial amounts of the expected phenolic type species. Varying amounts of teak HDDA extract were further used to formulate coatings based on the above-mentioned unsaturated polyester in DPGDA. The formulations were tested for UV reactivity in relation to the amount of teak HDDA extract added. Reduced reactivity in comparison to a formulation with standard HDDA was found only with high amounts of teak HDDA extract.
This simple experiment shows that there is an inhibiting effect of the wood extractables. But under conditions closer to an actual coating process, it can be estimated that this inhibiting effect is low.
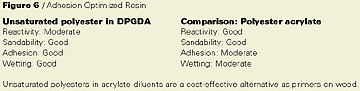
Chemical Crosslinking
Chemical crosslinking between coating and wooden substrate can be achieved with "dual-cure" formulations. Dual-cure formulations are taken here to mean those that crosslink not only by radical photopolymerization but also by an additional mechanism, namely the reaction of isocyanates with highly polar groups. The polar groups may be a constituent of one of the components in the formulation or may form through the effect of atmospheric moisture on the isocyanates. Alternatively, they may be bound in the substrate (see Figure 7).The use of urethane acrylates bearing free isocyanate groups results in significantly improved adhesion of the coating on wood. We conducted a model experiment to find out how exactly the chemical crosslinking takes place considering three probable mechanisms.
1. Moisture from the wood leads to the formation of urea groups at the coating substrate interface,
2. Aliphatic hydroxy groups of the cellulose fibers react with the isocyanates to yield aliphatic urethane groups or
3. Phenolic hydroxy groups, e.g., from lignin form aromatic urethanes.
We applied an aliphatic hexamethylene diisocyante isocyanurate polymer on wood and, as a control, on glass. Both coated substrates were stored under dry nitrogen atmosphere to exclude any influence from atmospheric moisture. Infrared spectra were recorded using a probe head that was moved along the z-axis through the coating layer. After one week, the control on glass showed no change in the IR spectra. The coating on wood, however, after a couple of hours showed a new peak as a shoulder at 1687 cm-1. This occurred in those spectra that were recorded close (< 2 Km) to the coating wood interface. The peak was evaluated as typical for an aromatic urethane by comparison with reference spectra from the literature. Aliphatic urethanes and ureas could not be detected in this experiment. Therefore, the most probable mechanism for the crosslinking of isocyanate functional urethane acrylates with wood is formation of additional urethane bonds with lignin type components of wood.
For dual-cure applications, the range of isocyanate functional urethane acrylates for outdoor use (Figure 8) is supplemented by a new range of low-viscosity products for indoor use (see Figure 9).
An application example for a parquet flooring coating process is given in Figure 10. The use of a dual-cure adhesion promoter leads to significant improvement in adhesion. The drawback of the primer formulation is the reduced pot life. There are, however, two advantages of using isocyanate modified urethane acrylates instead of just adding polyisocyanates to an acrylate resin formulation. Since the unmodified polyisocyanate is unreactive under UV irradiation, it will lower the UV reactivity of the formulation. Second, some of the polyisocyanate will not yet have reacted when the topcoat is applied. The polyisocyanate, therefore, can be extracted and induces a pot life on the topcoat roller coater that is applying a one-component system. Both problems can be avoided by using isocyanate functional urethane acrylates that link the isocyanate functions to the acrylate network.

Conclusion
Improving adhesion of UV curing coatings on wood can be achieved by different approaches. Using waterborne UV primers results in significantly enhanced adhesion. If water as solvent is not wanted, similar improvements are possible with dual-cure adhesion promoters. Here, isocyanate functional urethane acrylates are the resins of choice. If the pot life of dual-cure systems is not acceptable, 100% resins with optimized adhesion properties but lower UV reactivity are available.
For more information on adhesion of UV coatings on wood, contact Mike Johnson, Bayer Polymers phone 412/777.5573.
References
1 Cited after H.Pecina, O. Paprzycki, "Lack auf Holz", Vincentz Verlag, Hannover, 1995.2 In physics, the term emulsion usually describes insoluble liquid oligomers and polymers dispersed in water. The (umbrella) term dispersion allows no conclusion as to the state of aggregation of the disperse phase. In the coatings industry, both terms are often used to describe the state of a film after evaporation of the water. Emulsions yield tacky and dispersions tack-free films.