Computer Color-Formulation & Batch-Correction Software
To be truly user-oriented, software designers must recognize that the people using the system have different skill levels. The developers of
ChromaCalc(r) 3, Datacolor's latest formulation software package, realized that most companies have employees whose experience falls into one of three levels:
- The inexperienced laboratory technician who is just learning how to formulate colors.
- The more experienced colorist who wants to maximize his or her efficiency and productivity.
- The highly experienced color scientist, a power user who wants to use the formulation system in new and creative ways.
Software developers must recognize that a user's skill level will change over time. The ChromaCalc development team took advantage of an array of development tools and conventions to accommodate these multiple skill levels. Their solution incorporated the following navigation features:
- Menus and easy-to-understand help for the beginner.
- Toolbar buttons and on-screen reminders for the intermediate user.
- Keyboard accelerators and a complete on-line reference for the advanced user.
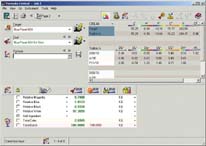
The Graphic User Interface (GUI)
A colorist should be able to simply measure a target and have the system ready to match or search - or, without calling up a new screen, the colorist should be able to add a trial and go right to correction. Formula displays should be dynamic and automatically adapt to the colorist's input.
ChromaCalc achieves this flexibility by making a single window, "Formula Central(tm)," the fundamental location for color matching and correction tasks (see Figure 1). This window includes a "formula grid" that dynamically responds to input from the user. When an ingredient amount or formula variable is changed, the related data in the formula is automatically updated, without any cue from the user; there is no requirement for the user to re-measure, recall or rematch.
Job Templates and Workflow Management
ChromaCalc 3 manages workflow using the methodology used successfully by humans to efficiently collect, record and retrieve batch histories. All information for each step in the matching process is saved as a page in an electronic notebook. This allows the colorist to organize, save and access comprehensive information pertaining to a particular color-matching job. Job records are readily available, and easy to access and view. When the colorist accesses a job, all selections, settings, data and results for the job are automatically displayed. Past steps may be reviewed, changed or repeated with a single mouse click.
Job templates allow the colorist to save a workflow that has worked particularly well for future use. This stands in contrast to previous color-matching packages, which offered default settings only for certain options, and often on a global basis.
Formulation Features
The "Autoformulate" feature adopts three tactics used by colorists to match a color. It begins by searching stored formulas for acceptable matches to the new target color. Working with existing formulas provides a tremendous advantage in a production environment. When an existing formula is scaled up to production quantities, there will be fewer surprises during processing. This saves labor and raw materials costs, and speeds the turnaround time of the batch. If the program fails to find a formula that is an acceptable match as is, Autoformulate next searches for formulas that, with slight modifications, will match the target color. It then corrects those formulas to achieve acceptable matches. Finally, Autoformulate will mathematically mix colorants from scratch to calculate color matches. When displaying formulas in ChromaCalc 3, formulas found during the search phase are displayed first, those found during the search and correct phase next, followed by the from-scratch formulas.
Formulation software should offer a manual adjustment feature that allows the colorist to electronically adjust the formula. This can be very useful for compensating for process effects. For example, the formula for an off-white target may be deliberately made lighter and bluer to compensate for a manufacturing process in which the color goes darker and yellower.
Gloss Compensation
Gloss depends on the smoothness of the paint film's surface. The smoother the surface, the higher the gloss, and the color appearance changes as the gloss is changed. Since many customer standards submitted to a paint company for paint matching may have a different gloss than the final paint, the color difference caused by gloss differences becomes a major industrial problem. Changes to a paint formulation are required to minimize the color difference between the two paint films when the gloss of the samples is different.Consider a glossy blue paint film with a gloss >90 (on a 60-deg gloss meter). Reduce the 90 gloss of the paint sample to 60 and prepare a sample. The high-gloss film will look deeper and richer (darker with higher chroma) than the semigloss film. However, when the visual color difference between the two films is minimized by changing the formulation of the semigloss paint, the measured color difference will increase. This is because the instruments typically used with formulation systems have integrating spheres, which will minimize the effect of gloss on the color measurement. If the two original blue paint films are measured with an integrating sphere instrument, they will have a very small color difference even though they look very different.
Gloss compensation, a ChromaCalc proprietary feature, provides a solution to this problem. Measurements made using the gloss compensation feature are transformed into a visual color space before the formulation is predicted. Doing this minimizes the visual color difference between the formulated paint and the target. To avoid problems in manufacturing, the paint formula generated using gloss compensation should become the production standard.

Matching Algorithms
The vast majority of computer color-matching systems use the equations published by Paul Kubelka and Franz Munk1,2,3 to predict the colorant concentrations required to match a particular color. Optimizers control the internal decisions made by the program during the calculation of initial formulations and batch corrections. Optimization algorithms published by Eugene Allen4,5 were implemented in many of the commercial color-matching programs developed since the 1970s, and were typically implemented using a single goal. The most common optimization single-goal was to achieve the lowest color difference possible (in the primary Illuminant/Observer condition) between the predicted color and the target color. In these programs, a starting formulation is given to the optimizer. The optimizer evaluates how close the starting formulation is to the goal. If necessary, the optimizer modifies the starting formulation and determines whether or not the modified formula has reached the goal. If it hasn't, the formula is modified once more and the result evaluated. This process continues until the optimizer calculates a formulation as close to the goal as possible. Typically, this goal was embedded into the code of the program. While the colorist could select the color difference calculation and Illuminant/Observer combination to be used, the goal itself could not be modified.Advanced optimizers permit the colorist to customize color-matching and/or batch-correction goals for each job. ChromaCalc allows the colorist to select up to five properties as the basis for optimization, including color difference, curve fit and metamerism index (see Figure 2). Weights can then be assigned to each property to account for its relative importance in the optimized formula. The sum of the weighted-properties becomes the goal function of the optimizer. The optimizer will try to satisfy the goal function, and the resulting formulas will show colorant amounts that have been optimized for all of the selected properties.
Sophisticated optimizers can predict formulations that are not only optimized for the selected properties, but that satisfy additional requirements referred to as constraints. These are requirements of the formula that are not part of the optimizer goal function, and can include features such as pigment loading, hiding, film thickness and colorant amounts.
Sorting Algorithms
Predicted formulas are initially sorted according to the match optimizer's goal functions. A number of predicted formulas may meet the criteria for an acceptable color match. However, the colorist may consider additional criteria for selecting the best formula for manufacture. For example, the colorist will usually take cost into account in choosing a formulation, but would not necessarily want to optimize the match using cost as one of the criteria. Sorting algorithms provides the ability to display the matches in a meaningful way using a sort function. Advanced formulation software includes customized sorting functions, in which the different sorting criteria, such as cost and metamerism, can be assigned weights.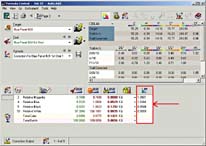
Batch-Correction Features
Batch-correction software should take advantage of performance information about the ingredients being processed. Correction programs typically calculate performance factors, which are related to the strength of a particular batch of colorant (see Figure 3). This performance behavior is quantified and used to adjust the amounts of each ingredient that is added to the batch. For example, if one colorant is performing stronger than expected, the amount of material added may be reduced to compensate for this behavior. The software should also allow the user to place limits on the magnitude of performance factors. When the performance factor for an individual ingredient falls outside of a range determined by the user, the amount of the ingredient used during correction will not be adjusted based on the current performance factor. This prevents the use of performance factors that fall outside the expected behavior of an ingredient. For example, a colorant may appear to be stronger or weaker than expected because of a weighing error, rather than a tinting strength difference between different lots of colorants.Another correction tool, "optical constant adjustment factors," has appeared in correction software since the 1990s. Adjustments to the predicted correction are based on differences between the theoretical and actual absorption and scattering coefficients (the Kubelka-Munk K and S values) for the ingredient6. This is particularly useful when there is a chemical interaction among colorants, or between the colorants and the vehicle, resulting in shade changes when the materials are combined. It can also compensate between small differences in the shade of two batches of the same colorant.
ChromaCalc 3 offers the choice of adjusting batch correction using either performance factors or optical constants. Its most striking advantage is that it offers the ability to combine the application of both performance factors and optical constants to the single batch correction calculation to further improve the predicted correction.
Batch-correction software should always include a manual addition feature. This feature lets the colorist change the ingredient amounts to be added, and to observe the effects of the change.
Batch-Correction Algorithms
Clearly, the quality of the final color match is the fundamental concern. For many reasons, the initial match prediction does not always produce an acceptable match to the target, and a correction is needed. Batch-correction algorithms have typically used the same goal function as the matching algorithms and, in older software packages, the program's single-mindedness with respect to its goal - a perfect match in the primary Illuminant/Observer condition - often produced corrections that were not practical. For example, it was not uncommon to receive a correction to a batch that predicted a perfect match to the target, but resulted in a colorant addition that doubled or tripled the size of the batch.
Modern optimizers allow the colorist to use a different goal function for the batch correction, often eliminating the need for a "trial and error," manual batch correction. For example, the operator will often attempt to reduce the size of the correction by optimizing on hue, the most critical part of a visual color difference. By optimizing the correction for hue, the addition could be greatly reduced while generating an acceptable match to the target. Another example of an impractical correction relates to film thickness. The program may provide a correction of a reasonable size, but the film thickness required to achieve the match cannot be achieved.
Conclusion
Intelligent and powerful, the latest generation of color-matching and correction software has been designed to meet the ongoing challenges of the paint and colorant market. The obvious features to be considered when evaluating these packages are the technical advances each offers. However, the key to selecting the right color-matching system lies in the ability of the software package to adapt to your needs. The most useful system will include features that target the various abilities of your colorists; the processes used in your laboratory or production facility, and the unique formulation requirements of your industry, to ensure that it is an indispensable tool.References
1 Kubelka, P.; and Munk, Franz. Ein Beitrag zur Optik der Farbanstriche. Z. Tech. Phys., 1931, 12, 593-601.2 Kubelka, P.; New Contributions to the Optics of Intensely Light-Scattering Materials, Part I. J. Opt. Soc. Am., 1948, 38, 448-457, 1067.
3 Kubelka, P.; New Contributions to the Optics of Intensely Light-Scattering Materials, Part II. Non-homogeneous Layers. J. Opt. Soc. Am., 1954, 44, 330-355.
4 Allen, E.; Basic Equations Used in Computer Color Matching. J. Opt. Soc. Am., 1966, 56, 1256-1259.
5 Allen, E.; Basic Equations Used in Computer Color Matching, II. Tristimulus Match, Two-Constant Theory. J. Opt. Soc. Am., 1974, 64, 991-993.
6 Karamantscheva, I.; Martin, D.; Rappoport, F.; Rohner, E.; and Van Hout, F.J. Smart Match Expert System for Textile Color Formulation. Available from Customer Service, Datacolor, 5 Princess Road, Lawrenceville, NJ 08648.
For more information, contact Datacolor, 5 Princess Road, Lawrenceville, NJ 08648.
Looking for a reprint of this article?
From high-res PDFs to custom plaques, order your copy today!