Enhancing Radiation-Curable Coatings with Silicone Surface Additives
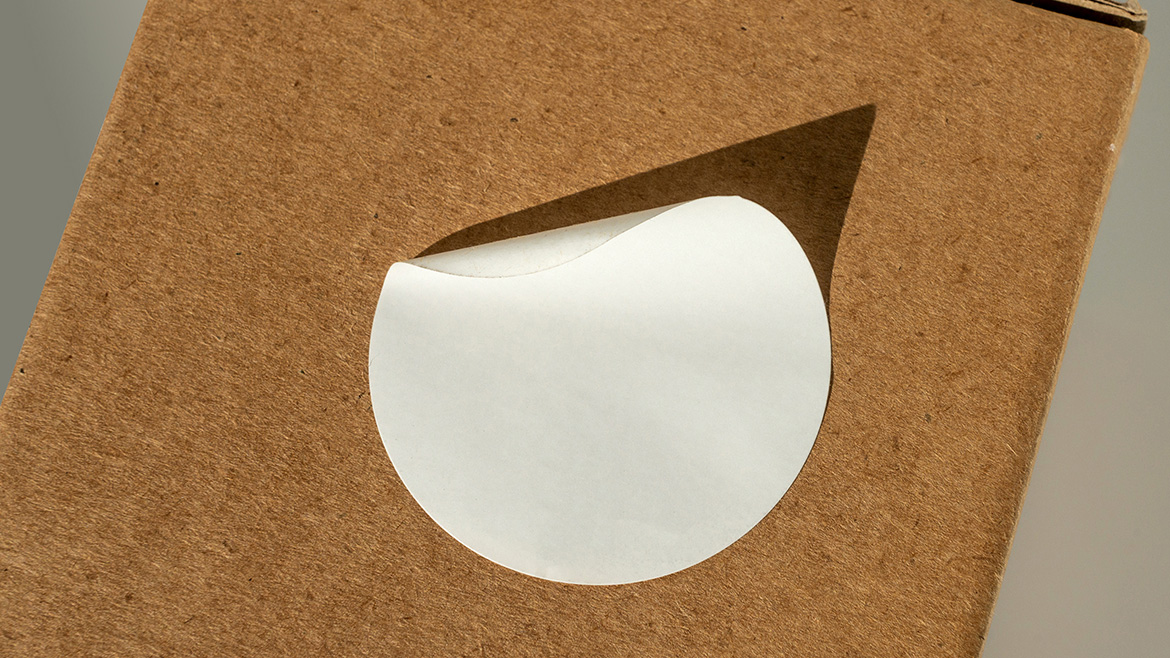
Radiation-curable coatings, such as ultraviolet (UV) and electron-beam (EB) curing systems, are widely recognized for their fast-curing times, environmental benefits and superior finish quality. These coatings are commonly used in the printing and packaging industries to enhance the appearance and durability of printed materials. However, to achieve optimal surface properties and long-term durability, specialized additives are often required. Among these, silicone-based surface additives stand out due to their unique chemical and physical attributes.
The Role of Silicone Additives in Radiation-Curable Coatings
Silicone additives are particularly effective in enhancing the performance of radiation-curable coatings. Their primary advantage lies in their ability to reduce surface tension, which improves wetting and spreading of the coating, resulting in surfaces with fewer imperfections such as craters and pinholes. Additionally, silicones contribute to improved flow and leveling, ensuring even distribution and uniform thickness across the coated surface. They also enhance slip and mar resistance, making the surface more durable. These properties are crucial for applications in industries that demand high-performance coatings.
Key Considerations for Developing New Additives
The development of new additives for radiation-curable systems must address a diverse set of requirements, as end users have specific and often challenging needs.

A critical component of these surface-active additives is silicone, specifically polydimethylsiloxane (PDMS). PDMS is known for its strong tendency to migrate to the coating/air interface due to its incompatibility with most organic materials. This migration reduces surface tension, promoting better substrate wetting and defoaming. However, pure PDMS can present drawbacks when applied to coatings, making organic modification necessary to improve its compatibility with polymeric binder formulations.
By incorporating crosslinkable groups into the additive structures, these modified silicones can permanently integrate into the coating matrix, offering durable properties like slip and release while minimizing their migration. Moreover, because radiation curing is environmentally friendly — featuring low emissions and energy consumption — new additives must also be colorless, odorless and produced through robust, waste-preventing processes to meet regulatory and economic standards.
Regulatory Requirements and Compliance
New additives, especially those based on PDMS, must comply with stringent regulatory requirements. For example, they must contain less than 0.1% of certain cyclic siloxanes (D4, D5, D6) to avoid being classified as substances of very high concern (SVHC) under EU regulations. In packaging materials, compliance with the Swiss Ordinance on Materials and Articles, which regulates materials in contact with food, is also essential. These regulations ensure that the additives are safe for use in applications where health risks are a concern.
In conclusion, the optimal combination of chemistry, process technology and additive composition is crucial in determining the compatibility, effectiveness and overall performance of the additives across various radiation-curable systems.
Advancements in Additive Technology
Tape release properties are essential in applications where adhesive tapes must be applied and removed during subsequent processing, such as in the packaging industry, where UV-varnished surfaces often require protective films or tapes during transportation and storage. The effectiveness of tape release properties can significantly influence both the quality and efficiency of these processes.
The interaction between the varnish and the adhesive used in the tape is also vital. Different adhesives respond uniquely to various varnish surfaces, so testing compatibility between the UV varnish and specific tape adhesives is essential to ensure clean removal without residue or surface damage.
Silicone additives play a crucial role by creating a low-energy surface that reduces adhesion between the varnish and adhesive tape, facilitating easy and clean removal.
The Importance of Functionality for Optimal Application Performance
The degree of functionality in additive structures is critical for achieving superior performance in radiation-curable coatings. As previously mentioned, the chemical reactivity of these additives plays a key role in enhancing both the durability and overall effectiveness of the coating. This reactivity refers to the presence of radiation-curable functional groups within the additive structures, which form covalent bonds with the coating matrix during the curing process.
With conventional technology, the resulting additives are a mixture of polymeric structures with varying degrees of functionality. Some polymer chains are difunctional, while others are only monofunctional, and a portion remains completely unfunctional. This unfunctional portion, in particular, causes issues when strong tape release properties are required. Unfunctional and monofunctional structures do not bond adequately with the coating matrix, making them prone to migration through the interface between the coating and adhesive, into the tape’s glue. This migration negatively impacts tape release performance.

By utilizing new technology, the degree of functionality can be precisely controlled, resulting in structures that are strictly difunctional. These structures form strong, permanent bonds at the coating’s surface, significantly reducing the likelihood of migration into the adhesive layer. As a result, the additives provide superior, long-lasting tape release properties.
To further explore the impact of functionality on coating properties, additive structures with varying degrees of functionality, ranging from 100% to 0%, were synthesized. To ensure accurate comparisons, the polysiloxane component and the organic modification of all structures were kept consistent in terms of molecular weight and chemical composition.
The additives A to E were all incorporated (with a dosage of 5% based on the total formulation) into a UV printing ink (based on Laromer LR 8986, EBECRYL 210 and HDDA). The samples were drawn up on a PET film (company: Pütz Folien, trade name Hostaphan GN 460) using an automatic K Lox Printing Proofer from Erichsen with a 6-µm spiral doctor blade. The wet coatings were hardened with the Aktiprint Mini UV conveyor (120 W/cm and a belt speed of 12 m/min) in three consecutive runs.
The tape release performance was measured according to ASTM D3330. For this purpose, Tesafilm (transparent office box 57404, length of approximately 24 cm) was applied to the coating and pressed down using finger pressure. The tape release was then measured as described in the mentioned ASTM method. Lower force values indicate better tape release properties, reflecting the effectiveness of the additive.
The contact angle (water) was determined using a KRÜSS DSA100 with imaging software.
The initial coefficient of friction (COF) values were measured using a Thwing-Albert FP 2260. A lower force required to slide the reference weight across the surface indicates a smoother surface and results in a lower COF value, signifying higher slip.
To investigate the durability of the coatings, a finger (16 mm diameter) of a Crockmeter (downward force 9 N, stroke length 104 ± 3 mm) equipped with a dust-free cloth (SONTARA blue, Glatfelter Gernsbach GmbH) soaked with MEK (as the test solvent) was placed on the surface of the coating and the following test procedure was performed:
- Step 1: One double stroke, then change the cloth.
- Step 2: Ten double strokes.
- Step 3: Measurement of COF value, tape release properties, contact angle (water).
- Step 4: Change the cloth.
- Step 5: Another 30 double strokes, cloth changed after every 10 double strokes.
- Step 6: Measurement of COF value, tape release properties, contact angle (water).
The results are summarized in Table 1.

Analysis of the data reveals that the initial coefficients of friction (COF) and tape release values for the control formulation (without additives) are relatively high, while the water contact angle of 79° falls within the range typical of standard organic coatings.
In contrast, the initial COF and tape release values for additives A through E are significantly lower than those of the control, indicating that all additives migrated to the surface. The water contact angles increased compared to the control formulation due to the nonpolar nature of the polydimethylsiloxane (PDMS)-based additives.
After 10 double strokes, there was no significant change in the control values. COF values for all additives increased but were still within the error limits of the test method and still remained lower than the control value. The situation for the tape release and water contact angles was different: Additive A, which is fully functional, showed the lowest tape release and highest contact angle values, while additives B to E performed less effectively.
After 40 double strokes, no real change in the values of the control formulation could be observed. Tape release properties and COF both remained at a high level. Fully functional additive A shows a stable performance: When comparing all three measured values after 10 double strokes with the measured values after 40 double strokes, they remained the same. Additive A is strongly incorporated into the coating matrix and provides a stable and long-lasting effect.
In contrast, additives B, C, D and E, which possess a functionality of 75% or less, exhibited poor performance, with their contact angles and COF values approaching those of the control formulation. Additive B showed performance closest to that of additive A; however, its tape release value of 1.2 N was not as effective as additive A’s value of 0.1 N. Moreover, the COF and contact angles for additive B differed significantly from those of additive A.
In summary, the presence of nonfunctionalized structures in additives B through E was diminished when wiped with solvent-soaked cloths, leading to inadequate application performance. In contrast, a fully functionalized structure ensures proper crosslinking and thus delivers a reliable and long-lasting performance.
Benchmarking of Surface Additives Based on New Technology Compared to State-of-the-Art Products
Optical Appearance
There are numerous surface additives available for radiation-curable systems, each varying in appearance. Some products are dark-colored, cloudy or even two-phase liquids containing residual catalysts used during production. These catalysts remain in the final product, affecting its appearance.

Additionally, some products are pre-dissolved in specific reactive diluents, limiting their versatility across different systems and applications. To address these drawbacks, a new class of additive structures has been developed, offering several advantages over existing products. A robust manufacturing process ensures the production of colorless, odorless and almost transparent additives with very low levels of cyclic siloxanes D4, D5 and D6 (each < 0.1%), meeting current regulatory standards. Moreover, these new additives contain 100%-active substance and feature strictly difunctional structures with high reactivity. This ensures excellent crosslinking with the coating matrix, delivering long-lasting performance.
Reduction of Surface Tension
Reduction of surface tension is a key factor influencing the quality of a final coating. Surface tension imbalances, either between the materials involved or within the coating itself, can arise from solvent or water evaporation, crosslinking of binders (monomer/oligomer combinations) or external contaminants like dust particles. During application and drying, these imbalances can lead to issues such as poor substrate wetting, crater formation, the appearance of Bénard cells or poor leveling. These defects not only compromise the optical appearance of the coating but also reduce its ability to protect the substrate.
The tested additives differ in chemical structure and functionality. The competitor 1, competitor 2 and additive 3 are based on state-of-the-art technology, whereas the new BYK-UV tape release additives are manufactured using the new technology. Competitor 1 has a medium-sized polysiloxane chain comparable to the silicone chain of BYK-UV 3595. Competitor 2 has a long polysiloxane chain comparable to that of BYK-UV 3590. Additive 3 has a shorter polysiloxane building block in comparison to competitor 1. All three state-of-the-art additives (competitor 1, competitor 2 and additive 3) have the disadvantages described in the previous paragraph (dark-colored, cloudy or even two-phase appearance) and additionally contain a certain amount of structures that are not fully functional. Regulatory compliance is also not achieved in every case, as these state-of-the-art products are not free of cyclic siloxanes (D4, D5, D6).
Table 2 presents the results of tests on five different additives at concentrations of 0.3% and 1%, using the reactive diluent mixture TPGDA/TMPTA (1:1) and HDDA as the test liquids. Surface tension measurements were conducted with a KRÜSS K100 tensiometer, employing the du Noüy ring method.

All additives effectively reduced surface tension compared to the control (without additives), demonstrating the strong surface orientation of the polysiloxane-based structures. Increasing the dosage to 1% showed no significant further reduction in surface tension, indicating that a 0.3% dosage is sufficient to achieve optimal surface tension reduction.
Tape Release Effect
Tape release is a critical feature in certain applications, where adhesive tapes and stickers must be easily removed from surfaces without leaving residue or causing damage. Polysiloxane-based additives are commonly used to enhance this release effect.
The five different additives were tested at three dosage levels (0.5%, 2% and 5%) based on the total formulation. A UV-curing overprint varnish (OPV) was selected as the test formulation. Tape release performance was evaluated according to ASTM D3330, where lower force values indicate better release properties.

As illustrated in Figure 4, additive 3 exhibited the highest force values at all three dosage levels, indicating the least effective tape release.
In contrast, BYK-UV 3595 performed similarly to competitor 1, while BYK-UV 3590 matched the performance of competitor 2. Notably, both new BYK-UV tape release additives exhibited a strong tape release performance, even at the lowest dosage level of 0.5%.
Summary
When developing new silicone surface additives for radiation-curable systems, multiple requirements must be met. As a leading supplier of additives, BYK is known for its expertise in silicone-based surface additives that reduce surface tension, increase slip and improve substrate wetting in inks, inkjet inks, overprint varnishes (OPVs) and coatings.
Building on this expertise, BYK has introduced two new crosslinkable additives, BYK-UV 3590 and BYK-UV 3595. These additives are notable for their exceptional tape release properties, high surface slip and excellent defoaming capabilities in UV printing inks, UV screen inks and UV OPVs. Both additives are strictly difunctional, minimizing migration after curing and providing long-lasting release properties. Their strong surface orientation significantly reduces surface tension, thus enhancing flow.
In addition, both new BYK-UV tape release additives are colorless, odorless and almost transparent, with very low levels of cyclic siloxanes D4, D5 and D6 (each < 0.1%).
For more information, click here.
Looking for a reprint of this article?
From high-res PDFs to custom plaques, order your copy today!