Reactive Acrylic Copolymers for Use in Low-Extractable Coatings

coralimages / Adobe Stock
Industrial coatings play an important role in many of the products used in everyday life. These coatings may be solvent-based, waterborne, powder or radiation-cured, to name a few. Of these coating types, waterborne is the most widely used, followed by solvent-based, powder and radiation-cured.¹ With growing regulatory pressure to reduce/eliminate VOCs, 100% solids UV/EB radiation-cured coatings have become a popular alternative to solvent-based coatings. When comparing the properties between the two coating types, both can be formulated to create scratch-resistant coatings with high hardness. The same cannot be said when formulating a hard and flexible coating. Solvent-based coatings have the advantage of using high-molecular-weight polymers, which can provide both hardness and flexibility, while UV/EB coatings are typically comprised of monomers and oligomers, which have a much lower molecular weight. In addition, the application viscosity for 100% solids coatings tends to limit formulations in terms of the concentration of oligomer being used, which in UV/EB formulations is the closest component to a “polymeric” material.
Another factor to consider when transitioning to a UV system is the need for a photoinitiator. Photoinitiators are necessary to initiate the polymerization reaction once exposed to UV light. In recent years, the UV coatings industry has faced regulatory challenges regarding the reclassification of many common photoinitiators as substances of very high concern. While there are some coating markets where the migration of photoinitiators and their classification is not a concern, there are many markets that are affected by these regulatory changes.
One way to mitigate the likelihood of a photoinitiator migrating out of a coating is to bind the initiating species to a polymeric or oligomeric backbone so that it becomes part of the cured network. Given that these “polymeric” initiators will be used in formulations at higher weight percentages than small-molecule photoinitiators, it is important to choose polymers or oligomers that enhance the coating’s performance. As noted above, traditional acrylate monomers and oligomers can be used to formulate a wide variety of coatings; however, balancing hardness and flexibility is a challenge. Acrylic copolymers and acrylated acrylics (Ac-Acs) can be used in UV/EB systems as both inert and reactive resins (respectively) to reduce shrinkage and increase flexibility. For this article, an overview of the performance properties of acrylic copolymers with initiating species grafted onto the backbone will be discussed.
Materials and Experimental Methods
Acrylic Copolymer Design
Acrylic copolymers, as the name suggests, are polymers composed of at least two acrylate monomers. The properties of these polymers are governed by the properties of the individual monomers, along with the molecular weight of the polymer. A typical acrylic copolymer will use a combination of high- and low-glass-transition-temperature (Tg) monomers to tune the Tg of the polymer, which in turn can affect the hardness of the cured coating. In terms of molecular weight, a copolymer with a high molecular weight is likely to be more flexible than a lower molecular weight analog. While this may make higher-molecular-weight copolymers appear more desirable, it is important to remember that too high of a molecular weight will impact their solubility in a 100% solids UV/EB formulation.
All these factors were considered when designing the copolymer backbone. To determine the effect of backbone structure on the coating properties, five monomers with differing glass-transition temperatures were used to synthesize a variety of copolymers with Tg values ranging from 40 °C to 70 °C. The molecular weights of the copolymers were also kept constant (Mn ~30,000 g/mol). Considering that the migration of photo-initiating species should be minimized, a Norrish Type II initiator (benzophenone-based) was chosen as the chromophore to bind into the polymer (Figure 1). Norrish Type II initiators only generate one radical upon exposure to UV, unlike Norrish Type I initiators, which generate two radicals and can have more complex photo by-products. The benzophenone-based chromophore was reacted into the polymer backbones at 4% wt so that once the reactive acrylic copolymers were diluted with 50% monomer, the concentration of chromophore was still high enough to cure a thin film.
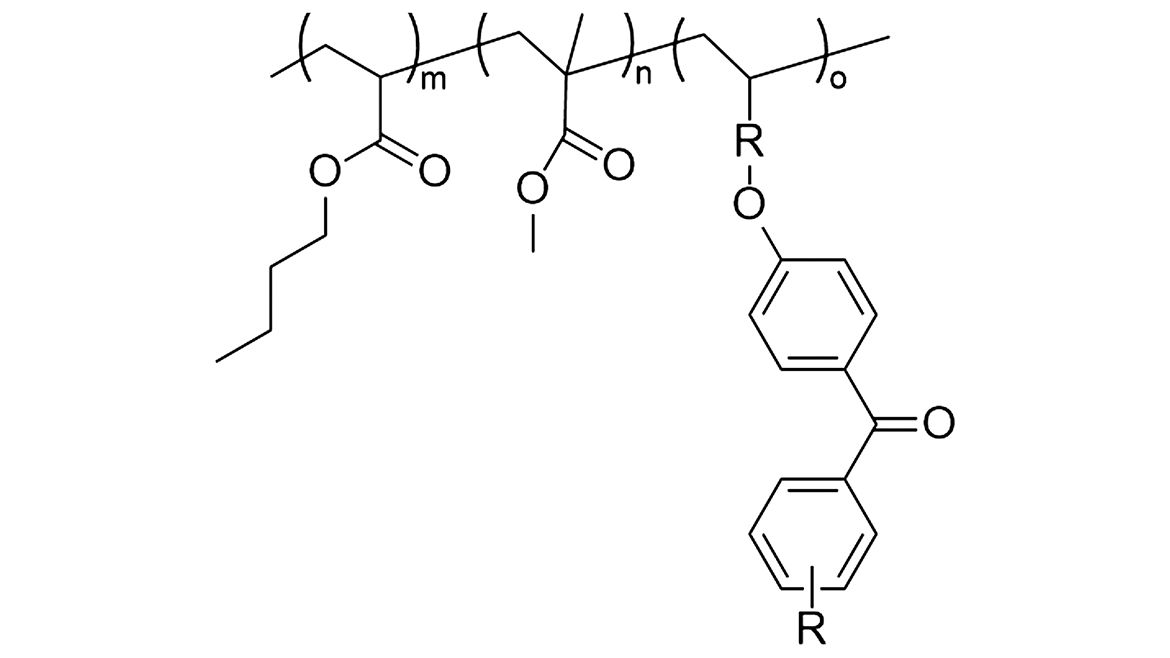
Table 1 shows the different monomer combinations that were used to synthesize the reactive acrylic copolymers (RACPs). The ratio of co-monomers needed to achieve the target Tg was determined using the Fox equation, and consequently, each copolymer has different monomer concentrations. For example, a higher concentration of IBOA was used to make RACP-1 with a Tg of 70 °C compared to the concentration of IBOA used to make RACP-1 with a Tg of 40 °C.
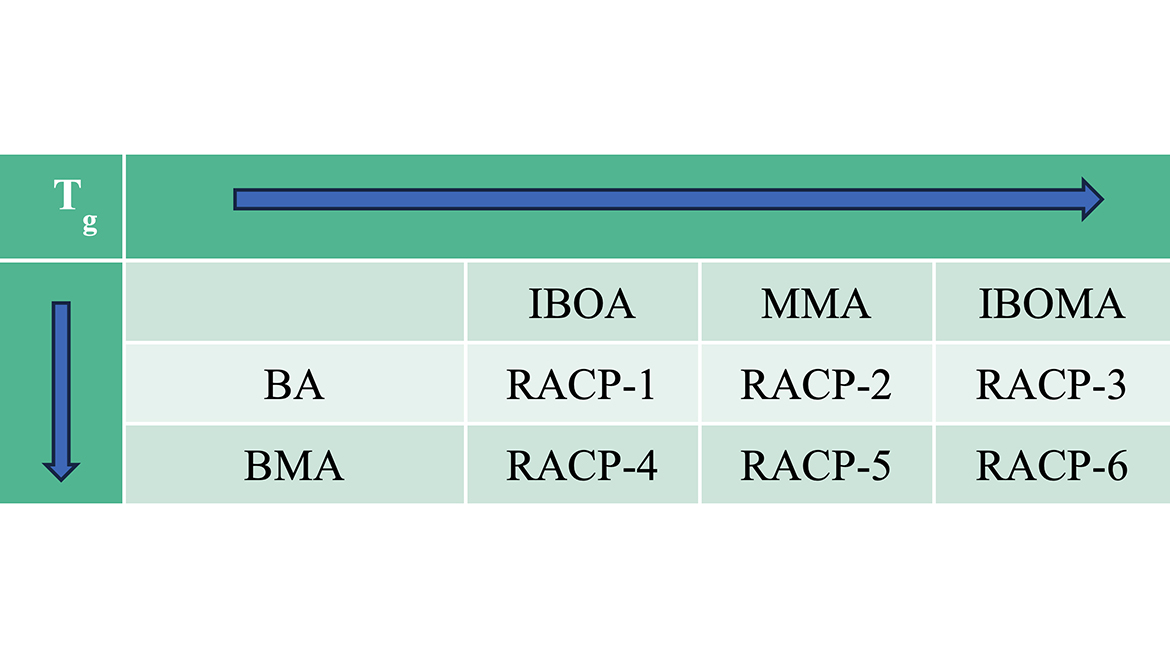
Table 1 (above) shows the different monomer combinations that were used to synthesize the reactive acrylic copolymers (RACPs). The ratio of co-monomers needed to achieve the target Tg was determined using the Fox equation, and consequently, each copolymer has different monomer concentrations. For example, a higher concentration of IBOA was used to make RACP-1 with a Tg of 70 °C compared to the concentration of IBOA used to make RACP-1 with a Tg of 40 °C.
Given that these copolymers are solid at room temperature, 50% TPGDA (tripropylene glycol diacrylate) was added to the copolymers to achieve a workable viscosity. Each sample was coated onto a bare aluminum panel and PET at 2 mils and cured using a microwave-powered 300 W/in mercury lamp with 1 J/cm2 of energy exposure. After conditioning for 24 hours, cross-hatch adhesion (ASTM D3359) and stain resistance were evaluated. For the stain resistance test, black permanent marker and mustard were applied to the coating for 1 hour and then wiped off with a dry paper towel (no cleaning solution or water used) before measuring the coating’s delta E using a colorimeter.
Results and Discussion
Figures 2 and 3 show the adhesion and stain resistance performance for all but one of the copolymers made. The 70 °C Tg RACP-3 copolymer was not tested due to its insolubility in 50% TPGDA, resulting in a nonhomogeneous coating. Based on the results, it is difficult to make conclusive statements about the correlation between Tg and performance properties. Across all the Tg samples, a full range of adhesion and stain resistance was observed. For adhesion to aluminum, a very minor decrease in performance was noted as the Tg increased, which may be attributed to the more brittle nature of the copolymer. It is harder to make a similar observation for coatings on PET since the cross-hatch penetrated both the coating and substrate, causing the PET to tear when the tape was pulled off (though the coating remained adhered to the PET in most cases).
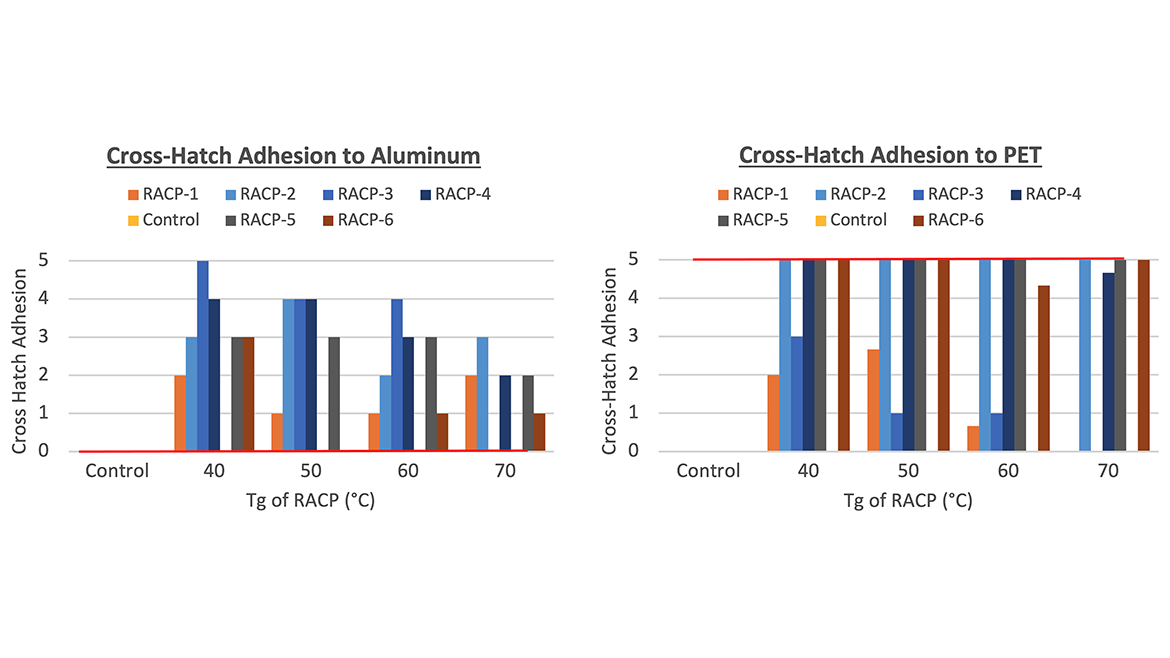
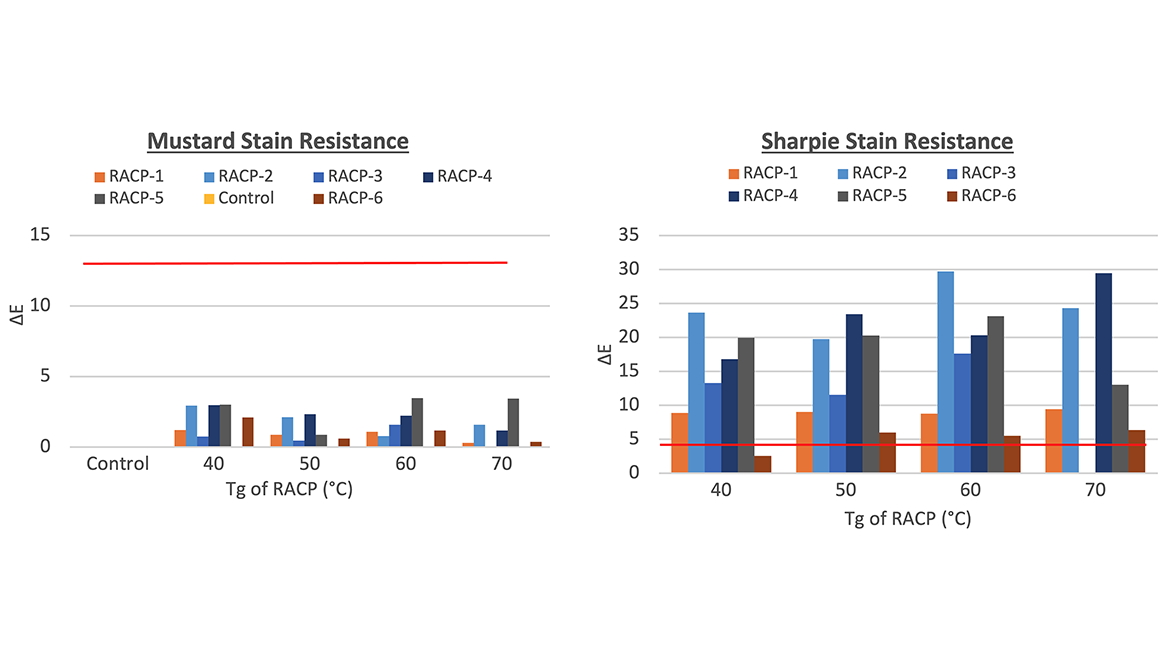
Neat TPGDA was also tested as a control with 2% benzophenone to match the chromophore level of the diluted RACP systems and is represented by the red benchmark line in the graphs. Compared to the control data, RACPs exhibited better adhesion to aluminum, and comparable or better stain resistance than neat TPGDA. Overall, the choice of RACP monomer appears to have a greater impact on performance properties than the ratio needed to achieve a specific Tg.
Reactive Acrylic Copolymer for Adhesion
In an effort to minimize the number of samples, RACP-3 was chosen as the best candidate to continue studying adhesion to aluminum along with cold-rolled steel (CRS) in place of PET. A new set of RACP-3 copolymers with a wider range of Tg targets (30 °C, 60 °C and 90 °C) was made to better parse out differences between samples. Since the goal is to understand the performance of RACPs as a low-shrinkage, more flexible option compared to traditional high-Tg acrylate oligomers, mandrel bend and König pendulum hardness tests were added to the matrix.
Initial testing of the acrylic copolymers showed poor adhesion to both aluminum and CRS. Upon further analysis, the newer batch of RACP-3 had an Mn much lower than the first batch. This likely resulted in a less flexible copolymer with lower adhesion to aluminum and CRS. To mitigate some of the brittleness, propoxylated neopentyl glycol diacrylate (PONPGDA) was substituted for the original diluting monomer (TPGDA). A comparison of the adhesion and hardness of the two systems across all Tg samples showed that adhesion improved in the PONPGDA samples for the 30 °C systems, while the TPGDA samples did not exhibit conclusive trends (Figure 4).
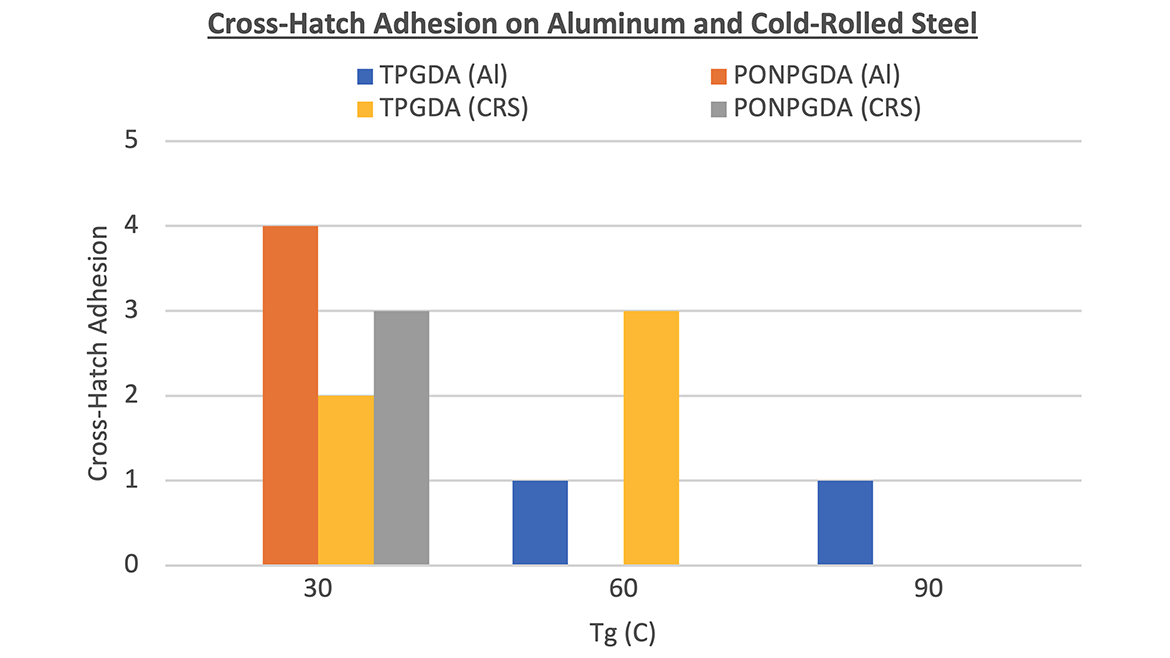
Although adhesion slightly improved in the 30 °C Tg system with PONPGDA, the samples failed the mandrel bend test. Given that the hardness values of the three different copolymer backbones (30 °C, 60 °C and 90 °C) all exceeded 100, focus shifted to the 30 °C copolymer. This copolymer showed the best adhesion and comparable hardness to the higher-Tg samples. Further studies were conducted where half of the PONPGDA monomer was substituted with either isobornyl acrylate (IBOA) or 3,3,5-trimethylcyclohexyl acrylate (TMCHA). Both systems demonstrated 100% adhesion to aluminum and CRS along with improved mandrel bend performance.
Reactive Acrylic Copolymer for Stain Resistance
Similar to the study conducted for adhesion, one reactive copolymer was chosen to minimize the number of variables. In this case, RACP-1 was identified as the best candidate to evaluate for stain resistance due to its performance and raw material availability. The concentration of chromophore on the backbone was also increased from 4% to 6% to see if a higher degree of cross-linking would affect the stain resistance properties observed in the previous round. The reactive copolymer was benchmarked against two resins commonly used in flooring applications where stain resistance is needed.
As shown in Figure 5, the RACP-1 sample had better stain resistance than the two benchmark coatings. The effect of chromophore concentration is illustrated in the second graph. Since the RACP-1 coatings were diluted with 50% monomer, the final chromophore concentrations were 1%, 2% and 3%. While one might expect higher chromophore concentrations to improve cure, FTIR-ATR measurements at the coating surface showed double bond conversions greater than 90% for all samples. This indicates that stain resistance correlates with the degree of cross-linking; the more photo-initiating sites present on the backbone, the more cross-linked the copolymer network.
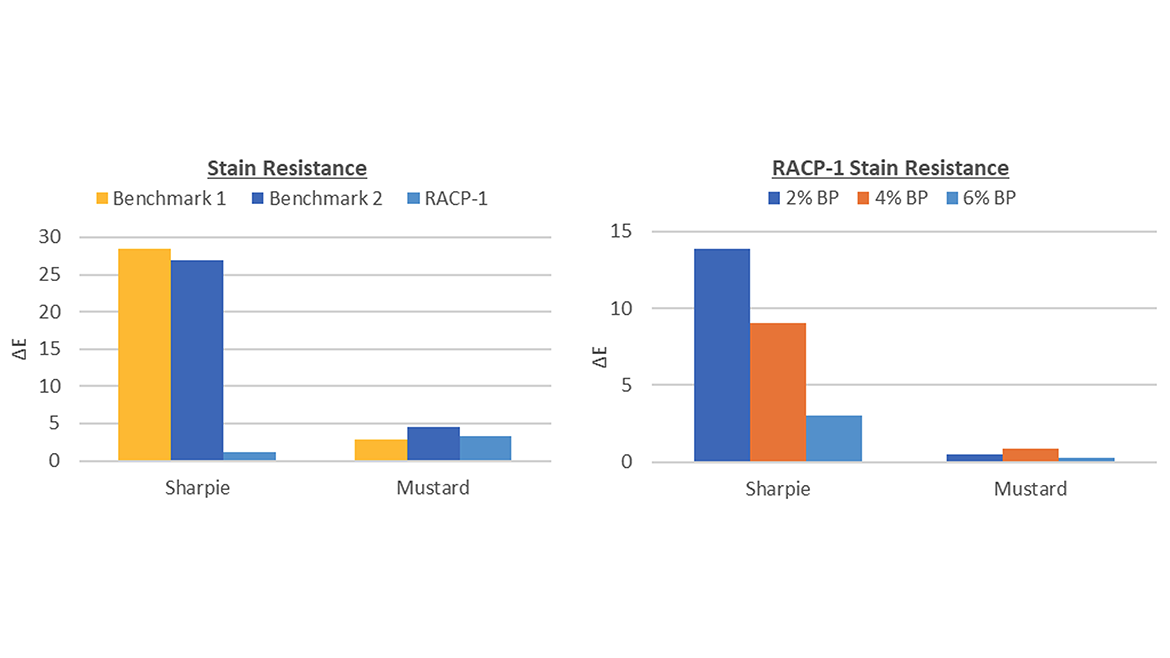
Conclusion
Acrylic copolymers are excellent resins for UV/EB applications due to their low shrinkage and compatibility with acrylate monomers and oligomers. By adding reactive chromophore sites onto the backbone, photoinitiator migration and its by-products can be significantly reduced, if not eliminated. FTIR-ATR data has shown that acrylate conversion is not compromised when using reactive copolymers as the initiating species.
Due to the high molecular weight of the copolymers, adhesion to metal substrates can be achieved without traditional adhesion promoters. Similarly, the copolymer backbone can be tailored to impart properties such as stain resistance and high hardness. Future work will focus on copolymers with higher chromophore concentrations and extractables tests for reactive copolymer formulations compared to traditional UV formulations.
For more information regarding Arkema’s solutions and expertise for UV/EB technologies, click here.
References
1 Challener C., Radiation-Cured Coatings Market Continues to Grow, CoatingsTech, Vol. 18, No. 6.
This paper was originally presented at the 2024 RadTech Conference in Orlando, Florida.
Looking for a reprint of this article?
From high-res PDFs to custom plaques, order your copy today!