Expanding the Aircraft’s Lifespan with Advanced Aerospace Coatings
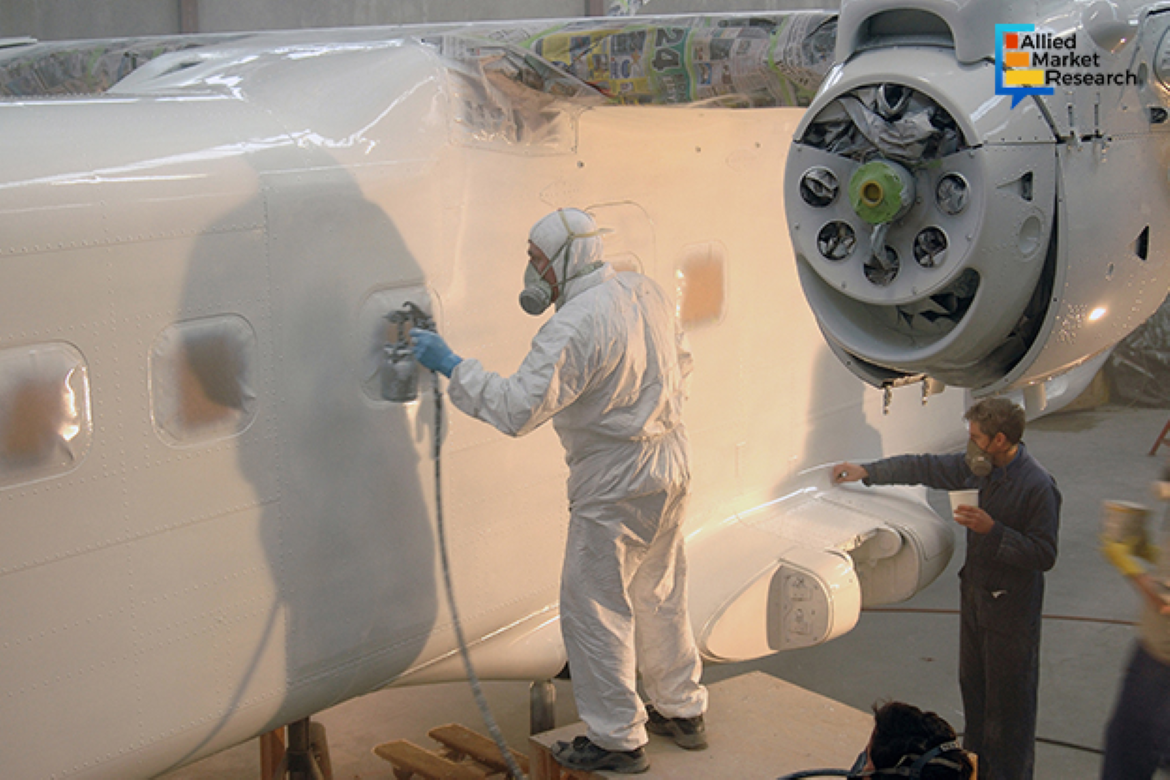
Image courtesy of Allied Analytics.
Aircraft require frequent repair and maintenance due to high climatic stress causing wear and tear of metal surfaces. Aerospace coating protects these parts from fog, UV rays, solar heat, corrosion, and other harsh weather conditions. It also minimizes aircraft weight, reduces carbon footprint, and improves fuel efficiency. These coatings have witnessed transformation due to the discovery of advanced formulations and materials.
How Do Advanced Coatings Protect Modern Aircraft?
One of the advanced innovations in aircraft coatings is nanotechnology-based coatings. These coatings provide increased fuel efficiency, improved durability, and high corrosion resistance. Nano-coatings are ideal for a superior level of protection along with a lightweight profile. On the other hand, thermal barrier coatings improve engine performance and efficiency in aerospace applications. The coatings are formulated to lower heat transfer and adhere to adverse temperatures. Due to the optimized engine performance, fuel efficiency and power output also increase.
Furthermore, smart coating is another innovation in the coatings sector that possesses self-healing properties. These coatings autonomously heal minor scratches and damage, which can ultimately increase the aircraft’s lifespan. These coatings provide anti-icing and anti-corrosive properties to withstand harsh climatic conditions like volatile temperatures. Advanced coatings with sensors track corrosion levels, temperature, and stress to offer real-time data. This sensor integration makes coatings responsive and enhances maintenance efficiency along with the required safety.
Advanced Protection Against Wear and Friction
Advanced coatings with the ability to reduce wear and tear enhance the maintenance processes and assembly. Tungsten disulfide and molybdenum disulfide are widely used coatings that minimize wear and friction on fasteners. They lower the risk of seizing and galling by providing a low-friction surface. This surface simplifies the removal and installation of fasteners. The focus on friction and wear reduction is fueling the integration of coatings that improve the maintainability and durability of aerospace fasteners.
Rising Demand for Sustainable and Eco-Friendly Coatings
The aerospace industry is highly focused on providing eco-friendly and sustainable solutions. Organizations are developing environmentally friendly coatings to adhere to strict regulatory standards. This involves adopting eco-friendly methodologies, incorporating non-toxic materials, and utilizing low-VOC compounds to minimize environmental impact. Also, manufacturers prefer the use of water-based and solvent-free formulations along with recycled components. At the same time, advanced coating technologies are offering long-lasting solutions to minimize frequent maintenance and replacements to meet sustainability goals.
Role of Digitalization in Aerospace Coatings
Through advancements in digitalization, advanced simulation tools and data analytics enhance the coating process, predict its performance, and optimize coating formulas. Digitalization has also enabled coatings to be painted onto the more intricate 3D-printed parts, which are on the rise.
Sherwin-Williams Introduced the Latest Aerospace Conductive Coating
Sherwin-Williams Aerospace Coatings expanded its undercoats range by adding the latest aerospace conductive coating (CM0485115) in September 2023. This product enables aircraft owners to impart conductivity onto composite and aluminum substrates.
The coating produces an anti-static conductive film on their surfaces to provide high conductivity to non-conductive substrates. The coating is formulated with superior adhesion and delivers robust fluid resistance. It is well-suited for all non-electrostatic spray devices and can be applied onto composite substrates and pre-primed aluminum to get high conductivity. The coat should be applied in a continuous, singular film for the best outcome.
Daher’s New Kodiak Aircraft Paint Facility
Daher’s Aircraft Division started its new 9,000-square-foot paint facility at the Kodiak Aircraft Company production site in October 2023. The facility streamlined Sandpoint’s manufacturing process and further enhanced the build quality for this turboprop aircraft produced in the Kodiak 900 and Kodiak 100 versions. Daher invested $2.7 million in this facility, which has separate paint areas and booths.
AkzoNobel Started the Renovation of the Aerospace Coatings Site in France
AkzoNobel began the modernization and redevelopment of its Aerospace Coatings manufacturing site at Pamiers, France, in July 2024. The investment involves an improvement of the existing amenities to boost the sustainability of the project over the long term.
The facility is estimated to be finished by the end of 2026 and is projected to result in a 50% surge in overall capacity. An investment in two R&D laboratories for cabin interior coatings and structure coatings is anticipated to support product innovation. The objective behind this investment is to produce chromate-free products for a sustainable future.
Conclusion
Aerospace coatings offer advanced protection to metallic parts of the aircraft. Advanced materials and manufacturing techniques improve the efficiency and performance of these layers. However, the growing demand for eco-friendly coatings highlights the shift of the aerospace industry toward sustainability. Also, innovative product discoveries by leading players are opening new avenues of growth and strengthening their positions in the dynamic industry.
Looking for a reprint of this article?
From high-res PDFs to custom plaques, order your copy today!