An Easy Additive Approach for Replacing Fluorocarbon Surfactants
in Water-Based Paints for Hot Block Resistance

Credit: revelpix, Creatas Video+, via Getty Images.
Manufacturers of waterborne coatings are encountering heightened regulatory demands to transition towards more eco-friendly formulations. These formulations must not only have low VOC levels, but also exclude substances of very high concern (SVHC) such as fluorocarbon surfactants (FCS) and alkyl phenol ethoxylates (APEs). This situation has resulted in a challenging scenario for formulators striving to incorporate greener additives, while ensuring that the performance of the coating remains uncompromised.
Fluorocarbon surfactants, in particular, remain a challenge for formulators to replace due to their unique structure and the balance of properties they bring to the formulation. One of the key performance properties formulators use fluorocarbon surfactants for is early—1 day dry—hot block resistance. This is a critical property in waterborne, semi-gloss to gloss formulations targeted in low-VOC applications. For decades, FCS have been used to enable this performance attribute without negatively affecting other application properties. However, FCS are part of a broad class of chemicals known as perfluoroalkyl or polyfluoroalkyl substances (PFAS). PFAS have the potential to be a health concern because they do not break down easily, and can stay in the environment and in the human body for a long time (which is why they are sometimes referred to as forever chemicals).1 Because of this, regulatory pressure has increased around the world to find safe and environmentally friendly replacements for fluorosurfactants in numerous industries.
To address this need in architectural coatings, a study of alternative technologies was conducted with specific focus on water-based architectural coatings. This thorough investigation revealed that modifying a specific phosphate ester could provide a straightforward solution that delivers excellent early hot block resistance and a well-rounded balance of application properties. This research culminated in the development of Rhodoline HBR®, a new anti-blocking additive for waterborne coatings.
What is Blocking Resistance?
Block resistance is the capability of a paint, when applied to two surfaces, not to stick to itself upon contact when pressure is applied under various temperature and humidity conditions. For example, good block resistance helps keep a door from sticking to the jam, or a window from sticking to its frame. Blocking usually depends on the hardness of the coating, the pressure, temperature, humidity, dry time, solvent evaporation, and duration of time the surfaces are in contact with each other. Figure 1 is a cartoon schematic demonstrating good and poor block resistance.

Block resistance is reported on a numerical scale of 0-10, which corresponds to a subjective tack and seal rating determined by the operator.2 The rating system is defined below in Figure 2 in appropriate descriptive terms. Most paint containing FCS can reach an early hot block rating of 8-10, which means little-to-no tack when the paint is pressed together. For the purpose of evaluating our additive, FCS were targeted as pass control for performance.

Experimental
Formulation and Paint Details
To test the performance of the various additives, we initiated the project by preparing a binder-rich master paint (formulation listed in Table 1), pouring off into separate containers, and then post-adding the various additives. The paints were equilibrated overnight, and then were drawn down to test for gloss and block resistance. A commercial FCS, at the recommended use level, was the target control. The latex used in the initial study was an internally prepared, all-acrylic (BA/MMA/MAA), 100-nm particle-size latex with an MFFT of around 10 °C. The master paint was prepared at a pigment volume concentration (PVC) of 22%, a volume solids (VS) of 35%, and a VOC of ~50 g/L.

Results and Discussion
Screening of Different Surfactant Chemistries
The scope of the project was to identify an additive that could be easily used by the formulator, either as a post-add to an emulsion, or added directly into the formulation, that could match the block resistance performance of the FCS control. Initial screening started by evaluating common classes of surfactant chemistries used in architectural coatings to assess their blocking performance. The additives were screened at two levels, 3#/100 gallons and 6#/100 gallons, based on their solids content. All phosphate esters evaluated were pre-neutralized with ammonium hydroxide to a pH of 7.0-8.0 to prevent shocking during addition.
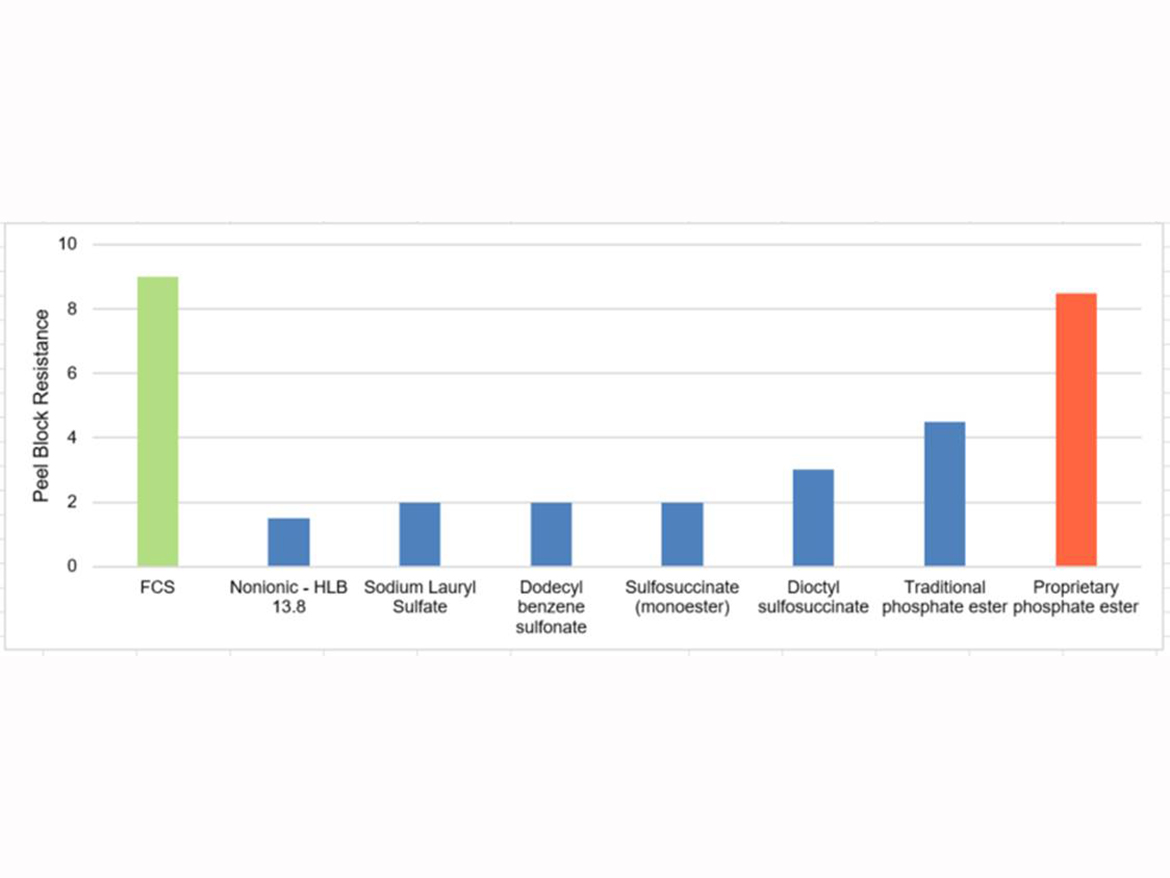
As expected, we found that traditional surfactants used in architectural coatings do not provide the blocking resistance necessary to replace the FCS, even at high levels. However, in our deeper dive into phosphate ester chemistry, we found that a medium hydrophobic chain phosphate ester showed excellent early hot block resistance that was comparable to the FCS.
Phosphate Ester Neutralization
Phosphate esters are acidic in nature and, due to their low pH, can be challenging for the formulator to add directly to the formulation or emulsion. Thus, the target was to prepare a stable neutralized version using potassium hydroxide as the base. Potassium hydroxide was chosen as this is a common neutralizing agent for coatings additives, and also does not contain the odor of an ammonium-neutralized product. Upon neutralization, it was observed that the proprietary phosphate ester would not remain stable over time and various temperatures (Figure 4a). Therefore, our focus was shifted to process optimization of the phosphate ester chemistry to improve the stability of the neutralized product. As shown in Figure 4b, after optimizing the process of the novel block additive, a stable, 40%-solids, potassium salt-neutralized product was developed. The newly developed version remained a stable, homogeneous solution even at low temperatures (Figure 4c). This led to the development of the novel anti-blocking additive Rhodoline HBR.

Novel Block Additive
To validate the performance of the novel block additive, the internal SG formulation and latex from Table 1 was used. For this comparison study, the only variable in the paint preparations was the wetting agent. For the fail control paint, a mid-HLB non-ionic wetting aid was used at 2 lb./100gal., based on active contents. In the pass control paint, the non-ionic wetting aid was kept and 0.04%-FCS (active ingredient/100 gal) was added to the formulation. For the novel anti-blocking additive, the non-ionic wetting agent was removed from the formulation and replaced with the novel anti-blocking additive at the same level—2 lb/100 gal—based on actives. All additives were introduced during the letdown stage of the formulation.
As seen in Figure 5, our new novel block additive demonstrated excellent early hot block resistance equivalent to the FCS control in the screening semi-gloss formulation. In addition, several other key paint performance properties were evaluated, and the new novel block additive did not show any detrimental effects (Figure 6).


We also evaluated the efficacy and persistency of our new block additive. An experiment was structured to look at various use levels ranging from 0.5 lb to 5 lbs active material/100 gal and we found excellent early hot block results at use levels as low as 0.5 lb/100 gal (Figure 7). We also evaluated the block resistance after heat aging of the paints to ensure that the novel block additive would remain persistent and provide robust block resistance over time (Figure 7).

Other Formulation Variables
Many interior semi-gloss paints are formulated at very-low-VOC levels, typically less than 25 g/L. To target the very-low-VOC space, formulators typically use low-Tg binders and/or switch to a zero-VOC plasticizer, which makes achieving early hot block resistance even more challenging. To assess the anti-blocking performance of our additive in this space, we screened our novel block additive in a 22% PVC/36% VS, 0 g/L VOC formulation that also included a commercial plasticizer (Table 2). For this formulation, we used an internally prepared, all-acrylic latex with a target minimum film formation temperature (MFFT) of 0 °C. As can be seen in Figure 8, our novel block additive provided excellent early oven block resistance at a use level of just 1lb active material/100 gal. In addition, we saw excellent early hot block after heat aging of the paints, and also after tinting with 2 oz/gal of universal Phthalo blue colorant. No adverse effects on other key paint performance properties were observed. While the majority of our evaluations focused on all-acrylic resins, we also found excellent early hot block resistance in semi-gloss formulations based on styrene/acrylic and VAE resins.


Additive Characterization
Fluorocarbon surfactants provide excellent block resistance by their ability to migrate to the surface of the coating, and orient in a way that prevents the polymer-to-polymer contact that results in poor block resistance. In aqueous systems, surfactants will orient with the hydrophilic portion facing towards the water, while the hydrophobic tails extend away from the water and into the air. With this understanding, the surface of the paint films were analyzed by placing a drop of water on the surface and measuring the contact angle. We hypothesized that by having a higher concentration of additive at the surface, there would be an increase in the contact angle of the water droplet. As can be seen in figure 9, the paint prepared with the novel block additive had the highest contact angle as we expected. However, we found that the paints prepared with FCS and the non-ionic fail control had similar contact angle results which did not correlate to blocking resistance.

We also investigated surfactant interfacial packing, which pertains to the arrangement and concentration of surfactant molecules at the air/water boundary. Surfactants with greater interfacial packing should offer superior anti-blocking properties. One way to assess interfacial packing is through the measurement of surface tension. Low surface tension and interfacial packing are closely related, as surfactants that can pack densely at the interface are more effective at reducing surface tension. The surface tension was evaluated at critical micelle concentration (CMC) for all of the surfactants in the study and interestingly, the novel block additive exhibited the lowest surface tension value, and was nearly as low as the reported value for FCS (Figure 10).

Low surface tension alone does not necessarily translate to improved blocking resistance. The orientation of the surfactant molecule at the surface is equally critical in providing anti-blocking resistance; however, determining the orientation of a surfactant at the air/water interface requires complex imaging techniques in which we continue to explore. In addition, the interfacial packing of a surfactant can also vary depending on the formulation space, the binder chemistry, and other factors due to the complex nature of waterborne coatings. Further work continues to be explored to better understand the mechanism behind blocking resistance.
Conclusion
Replacement of fluorosurfactants in water-based coatings has proven to be very challenging as customers want an environmentally safer alternative that is easy to use, easy to handle, and can deliver early hot block resistance, without affecting other performance properties. Our novel block additive is environmentally friendly, can provide excellent early hot block resistance in waterborne coatings, and also has excellent wetting and good overall application properties. Rhodoline HBR, the new novel block additive, is supplied as a 40%-solids solution in water at neutral pH and low viscosity, allowing formulators the option to tailor their systems for improved anti-blocking by adding directly into the latex, or at any stage of the paint formulation. While this work is pertinent to water-based architectural coatings, we continue to explore other binder chemistries and adjacent applications where fluorocarbon surfactants are used. It may be likely that the new novel block additive can be leveraged towards wood and industrial coatings applications as well.
Acknowledgements
The authors would like to thank Dr. Celine Burel, Romane Tranchard, Kara Zytko, Tom Machamer, An Tran, and Eugene Anderson for providing crucial lab data during product development.
References
1 Per- and Polyfluoroalkyl Substances (PFAS) and Your Health. Agency for Toxic Substances and Disease Registry, 2020. https://www.atsdr.cdc.gov/pfas/index.html.
2 ASTM Standard Test Method for Blocking Resistance of Architectural Paints, Designation D 4946-89 (2017).
Looking for a reprint of this article?
From high-res PDFs to custom plaques, order your copy today!