High-Performance Coating Protects Tanks at Bio-Polymer Production Plant
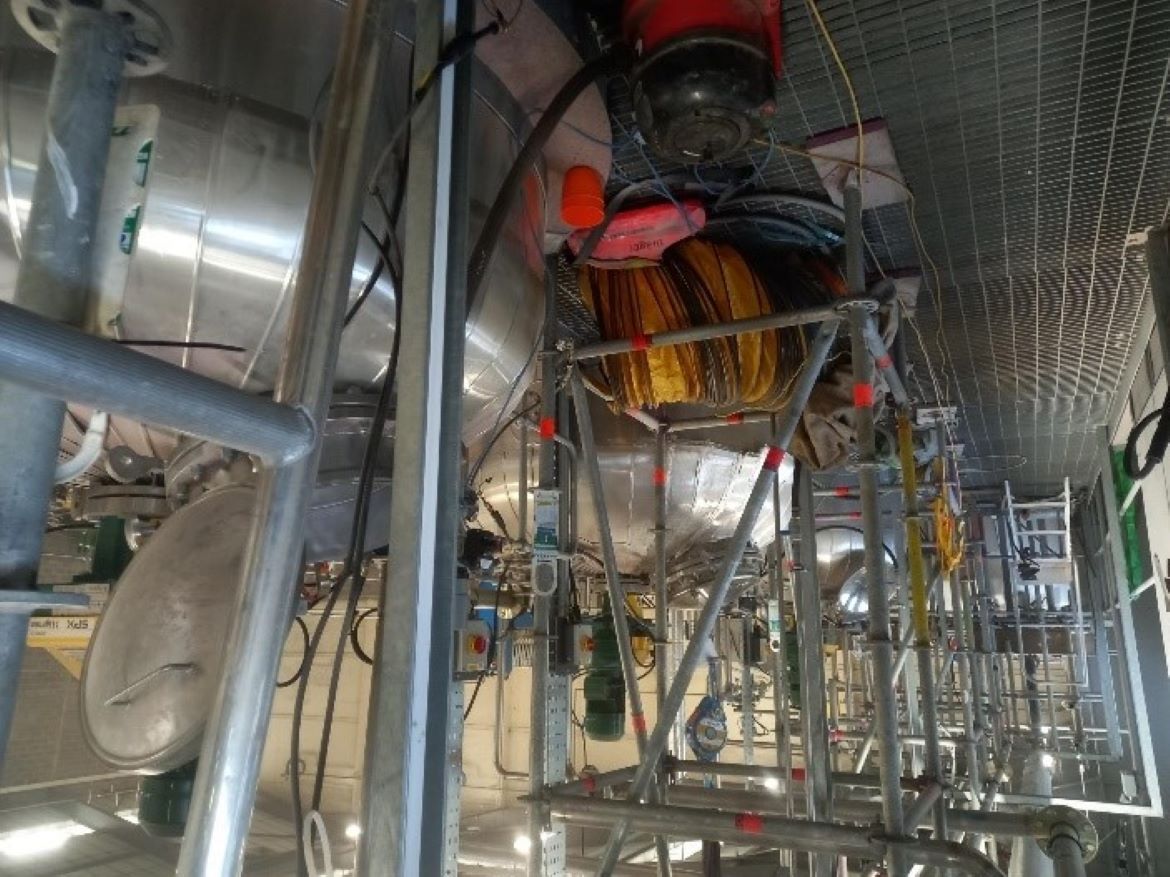
High-performance coating required to protect tanks against corrosion.
At a chitosan production plant in Scotland, United Kingdom, a high-performance, anti-corrosion coating was used to coat the internal lining of three tanks, protecting them against aggressive, acidic substances for the long term. Given the important role the tanks play in the process of turning large amounts of shellfish byproduct into the bio-polymer chitosan, it was imperative that these assets were safeguarded against future damage with the use of a high-performance coating.
Production of Bio-Polymer from Shellfish Shell Byproduct
CuanTec has created a circular economic business model designed to mitigate the carbon footprint created from the unnecessary disposal of unused shell within the shellfish industry and converting it into valuable chitosan products.
Indeed, the carbon footprint of food waste is staggering. According to data from the UN, food waste contributes to 8% of global greenhouse gas emissions. This means that if food waste was a country, it would be the third-largest emitting country in the world.
At COP28, negotiators from 200 parties agreed on the science from the Intergovernmental Panel on Climate Change (IPCC) that global greenhouse gas emissions need to ‘be reduced by 43% by 2030’, in order to limit warming to 1.5 °C (2.7 °F) by 2050, in line with the Paris Agreement. With this in mind, circular business models such as that offered by CuanTec, play an important role in mitigating carbon footprints and limiting global warming to 1.5 °C (2.7 °F).
Safeguarding Key Assets
Considering the important role businesses such as CuanTec play in this decarbonization and upcycling journey, it is absolutely fundamental that key assets within these types of businesses, such as machinery, equipment, buildings and structures, are safeguarded to an excellent standard. Otherwise, damage and wear can jeopardize the integrity of assets, and therefore this can undermine the environmental benefits these types of business models offer.
For example, the carbon footprint of steel is phenomenal: for every tonne of steel produced, nearly double the amount of carbon dioxide (CO2) is released back into the atmosphere. Therefore, if a steel asset becomes damaged, not only can this lead to costly replacement fees, but this process can also incur a hefty carbon footprint as well.
As such, numerous industries invest in industrial repair composites and high-performance coatings in order to bypass this replacement process. In this way, polymeric technology mirrors the circular economic model of businesses like CuanTec, as this technology can repair, protect and even intrinsically improve assets that would otherwise be decommissioned and sent to landfill. Thus, it could be argued that polymeric technology has a critical part to play in the decarbonization of multiple sectors, supporting a net zero by 2050 pathway.
Pre-Used Tanks in Need of Rigorous Corrosion Mitigation Measures
CuanTec wanted to deploy three steel tanks in their process of turning shellfish shell into high quality, traceable chitosan products, made to the exacting technical specifications of their customers. The tanks had already been in use elsewhere, but were otherwise still in good condition. In order to ensure the tanks were capable of withstanding the harsh chemicals they would come into contact with, the customer decided to invest in some polymeric technology to protect them.
System Specification: High-Performance Coating
Following an inspection from Clive Leadbitter, Senior Field Sales Engineer at authorized Belzona Distributorship, Belzona UK, the high-performance coating, Belzona 1391T, was specified. As this system is capable of protecting assets against corrosion in extremely aggressive and acidic environments, this was the ideal solution for the steel substrate for this specific application.
In addition, as the coating can be applied in situ without the need for hot work, this would ensure that the application was carried out as quickly as possible, whilst minimizing the health and safety risks that can arise when hot work is involved.
Belzona 1391T has undergone direct food contact (FDA) testing, the results can be found here.
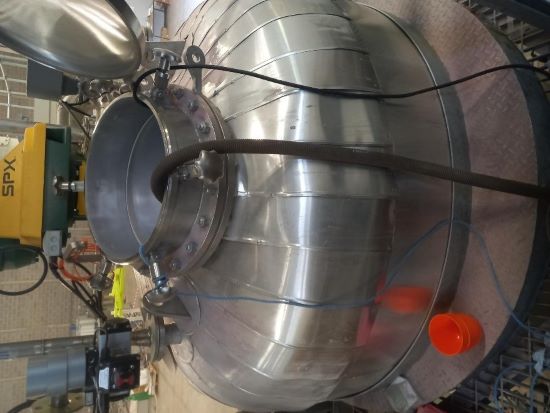
Application Procedure
Commenting on the application procedure, Clive said: “Surface preparation was carried out by grit-blasting. Following this, using a stiff-bristled brush, two coats of the coating were applied at a thickness of 450 µm (17.72 mil) per coat. Once the application had cured within the space of 24 hours, the application was complete.”
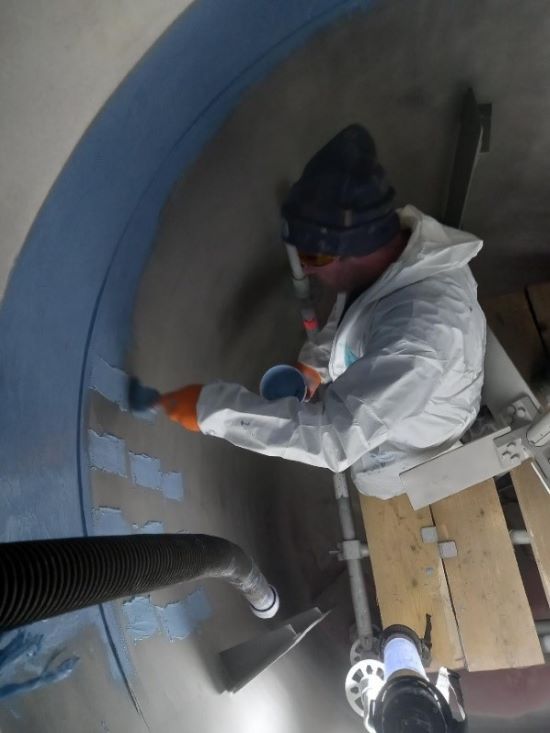
Considering the important role businesses like CuanTec play in carbon mitigation, it is absolutely critical that key assets are protected for the long term against damage such as erosion and corrosion. As such, polymeric technology plays an important part in safeguarding these assets, and therefore contributing to the net zero by 2050 pathway.
For more information, please visit: www.belzona.co.uk.
*Images courtesy of Belzona.
Looking for a reprint of this article?
From high-res PDFs to custom plaques, order your copy today!