New Silicone-Free Super-Wetting Surfactants for Waterborne Coatings

Additives that improve the wetting behavior of coatings on wood substrates have grown in importance over the last decade. As a result, the super-wetting agents market is growing; Maximize Market Research (MMR) projects growth at about 6% CAGR over the next five years. These additives play a significant role in providing a smooth and defect-free surface, and enhance the penetration of the coating into the wood substrate.
Good wetting performance improves the visual and aesthetic appeal of the coating on the wood surface and, thereby, the finished wood product, such as a parquet floor, a cabinet, or wooden furniture. Most of these coatings are spray-applied, and to prevent the formation of pinholes and cratering, the coatings need to wet the surface rapidly and entirely without excessive foaming. Consequently, these additives must provide a good balance of wetting and low foaming to be effective.
Additionally, there is a growing interest among paint manufacturers of waterborne industrial coatings in offering their customers more environmentally safe and cost-efficient wetting agents. This market trend is resulting in the need to identify alternatives to silicone surfactants and fluoroalkyl-based wetting agents that provide the same or better wetting performance—a challenging proposition since all premium wetting agents are applied in premium, high-performance industrial coating systems.
This article will introduce an innovative approach to enhancing wetting behavior based on a comparative evaluation of silicone-free and silicone-based surfactants, focusing on surface tension and contact angle. The product, Easy-Wet™ 300 substrate wetting agent, is a carbon-based technology from one of Ashland's breakthrough platform technologies.
Surface Tension
Surface tension is not just a factor but a key determinant in the quality of applied coating systems. It influences wetting behavior, adhesion, film thickness, and overall coating quality. Understanding and implementing technologies like Easy-Wet 300 can significantly enhance the quality of a coating because of the way it interacts with both water-based and solvent-based paint systems.
Traditional surfactants used to improve wetting can consist of four main types: anionic, non-ionic, cationic, and zwitterionic. These surfactants typically have a hydrophilic end and a hydrophobic tail, usually alkyl or fluoroalkyl. They aggregate in water at the interface and help lower the surface or interfacial tension, enabling wetting. Surface tension measures solvent (water) molecules’ "cohesion." In other words, lower surface tension promotes substrate wetting, and water droplets spread on the surface. Conversely, higher surface tension can result in "beading" on the surface.
Since water has a very-high surface tension around 72 dynes/cm, and typical coating surfaces have surface energies around 35-45 dynes/cm, for adequate wetting to occur, the surface tension in water needs to be lower—generally, the lower, the better. Currently used carbon-based surfactants typically don't display static surface tension values below 29 dynes/cm. Also, they tend to foam, resulting in surface imperfections such as pinholes and reduced surface appearance.
Historically, silicone-based surfactants have addressed this issue in wood coatings by lowering the static surface tension to around 21 dynes/cm. They are also good at controlling the amount of foam. However, reducing static or equilibrium surface tension is not the only factor contributing to good wetting.
This speed of wetting is equally essential. Depending on the application method, it is desirable to reduce the surface tension rapidly and have the surfactant molecules reach the newly created surface very quickly to facilitate good wetting. One disadvantage of silicones is that they can lead to inter-coat adhesion failure since they concentrate on the coated surface, which causes problems due to their hydrophobic nature.
The right balance of properties provides good wetting and surface finish. Easy-Wet 300 wetting agent offers a practical and cost-effective solution. It substantially reduces static and dynamic surface tension and aggregates in water at very-low concentrations to reduce surface tension at low dosages, making it a valuable tool in enhancing the quality of a coating.
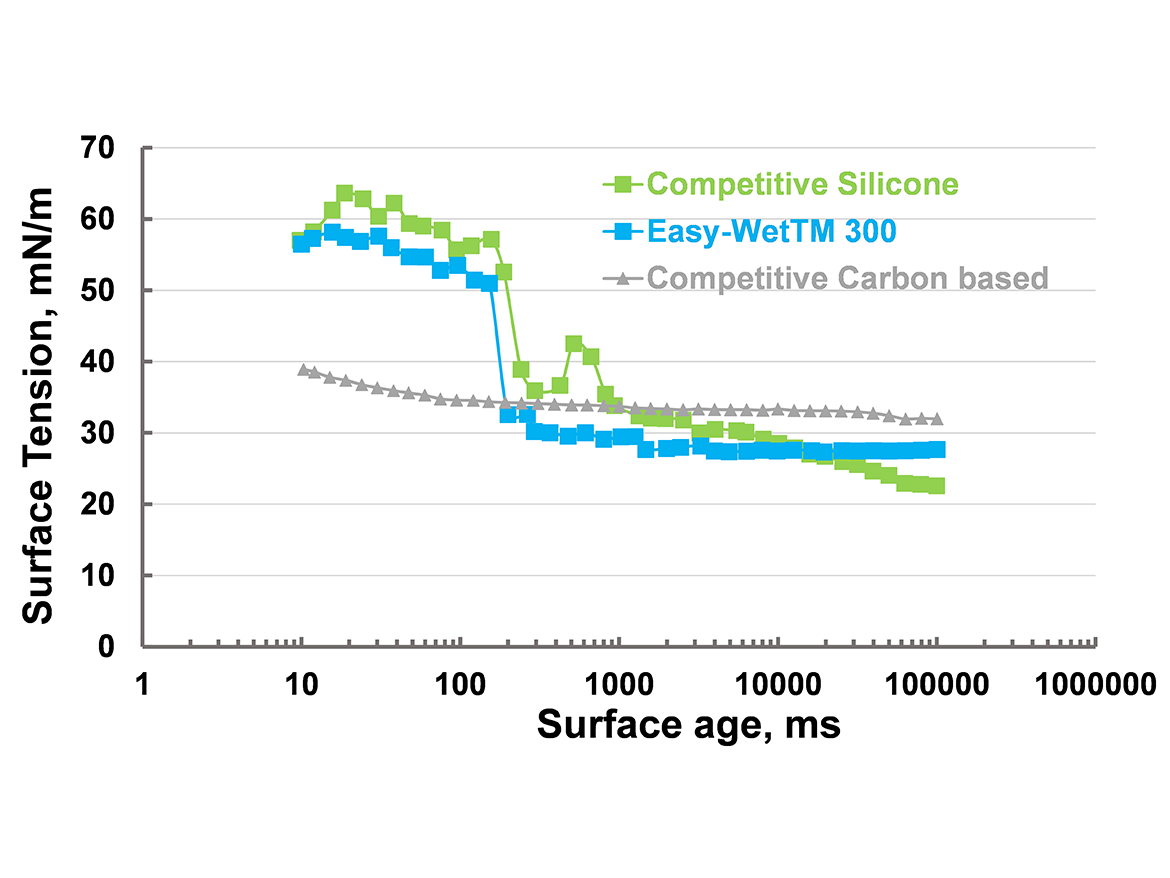
The new wetting agent reduces surface tension more rapidly with time compared to the competitive silicone, even though the equilibrium surface tension value for the silicone is lower (21 dynes/cm compared to 27 dynes/cm). In comparison, the carbon-based competitive product has a lower surface tension at shorter time scales. Still, the drop in surface tension is gradual, and the equilibrium surface tension is higher. The contact angle is another critical indicator of a substrate's wettability. Good wetting occurs when the contact angle is low and greatly influences adhesion or how the coating spreads and adheres to the surface.
The competitive silicone and Easy-Wet have similar wetting profiles. In contrast, the contact angle for the competitive carbon-based surfactant is much higher; therefore, its wetting behavior is not as good, as illustrated in Figure 2.
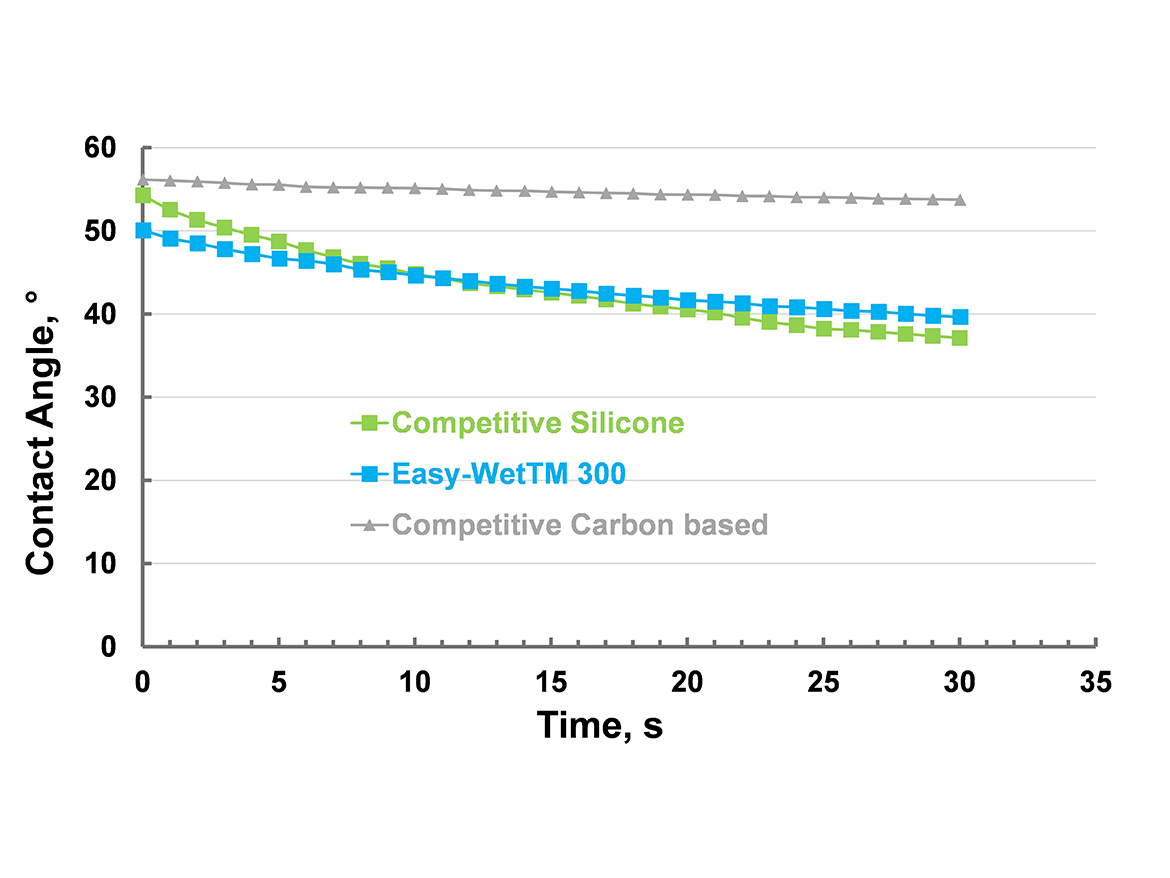
Compatibility
Another challenge for wood coating manufacturers is when there are issues with compatibility due to contaminants in the system, or the use of incompatible defoamers. This incompatibility leads to severe cratering effects on the coating film. Adding super wetting agents based on silicones can be helpful, especially as fluorosurfactants are increasingly scrutinized because of environmental hazards. Table 1 shows a 1K waterborne parquet flooring composition in which 1% of various surfactants have been added to correct a cratering or incompatibility issue. Figure 3 shows the drawdowns of these coatings and the varying degrees of cratering after adding 1% additive. The data indicates that silicone-based surfactants are much better than silicone-free surfactants in addressing incompatibility issues. However, the data indicates that Easy-Wet 300 can also clearly resolve the incompatibility issue and produce a smooth, defect-free film.
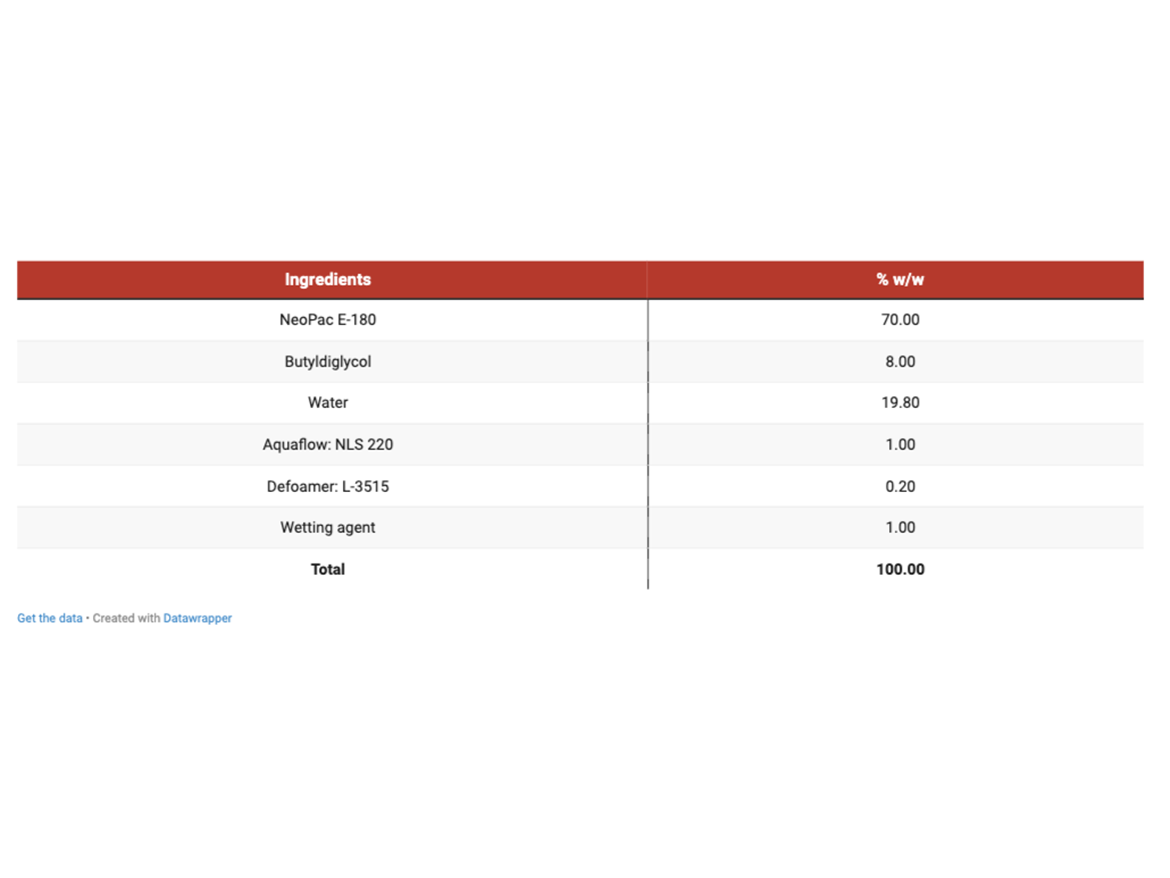

Summary
In conclusion, Ashland’s Easy-Wet 300 substrate wetting agent provides formulators with a sustainable and differentiated high-performing wetting agent. The product has very-low static surface tension and rapidly reduces the surface tension over time as measured by dynamic surface tension data. It provides a smooth coating finish without any defects such as pinholes, cratering, and leveling. It is highly compatible in multiple solvent systems and can be used to formulate solventborne and waterborne coatings. Finally, this new additive has very-low VOC, less than 1%, compared to other wetting agents.
For more information, click here.
Looking for a reprint of this article?
From high-res PDFs to custom plaques, order your copy today!