Novel Composite Light Stabilizers for Durability Protection of Coatings on Carbon Fiber Composite Materials
June 10, 2024
Novel Composite Light Stabilizers for Durability Protection of Coatings on Carbon Fiber Composite Materials
June 10, 2024Carbon fiber-reinforced polymer (CFRP) has a long history of application, dating back to the space race between the United States and the Soviet Union (now Russia) in the 1950s. Scientists sought a material with high mechanical strength and lightweight properties, which led to the wide-spread adoption of CFRP. Its advantages, including lightweight, excellent heat resistance, low coefficient of thermal expansion, impact resistance, corrosion resistance, and fatigue resistance, coupled with its elegant woven appearance, make it suitable for various service environments. CFRP products are widely used in industries such as automotive, wind power generation, aerospace, rail transportation, healthcare, sports equipment, etc. Therefore, they encounter various aging mechanisms.1
With advancements in technology and the pursuit of lightweight solutions, research data from the U.S. Department of Energy and other institutions indicate that reducing vehicle weight by 10% results in a 6-8% decrease in fuel consumption and a 5-6% reduction in emissions. Additionally, with the development of electric vehicles, it is evident that vehicle lightweighting is a key trend for the future. In Asia, over a quarter of carbon fiber composite materials were used in sporting and leisure goods in 2016, while wind power generation-related applications accounted for approximately 20% of CFRP composite usage. With the global trends toward fuel-efficient vehicles and electric cars, the use of carbon fiber composite materials in the automotive sector is expected to grow at an annual rate exceeding 20%. It’s projected that by 2030, carbon fiber composite materials will become the primary application in Asia, accounting for over a third of its usage.3
According to a report released by the global market research firm Japan Fuji Economic, carbon fiber composite materials are highly regarded for their lightweight and high-strength properties, and their applications are increasing in fields such as aerospace, automotive, and wind power generation. It is projected that the global carbon fiber composite materials market size will reach 1.4284 trillion yen in 2018 and 3.58 trillion yen by 2030, which is 2.6 times the level in 2017. Specifically, the market for carbon fiber composite materials is expected to grow from 1.3656 trillion yen in 2018 to 3.2018 trillion yen by 2030. In terms of applications, aerospace, wind power generation, automotive, and sports/leisure applications are the main areas, with increasing demand, especially for wind turbine blades. In the automotive sector, car manufacturers are pushing for the development of carbon fiber composite material utilization technology. Currently, European automakers are in a leading position in development and application. However, with the increase in demand for automotive lightweighting due to policies and the booming electric vehicle market, it is expected that Chinese automakers will adopt these technologies in the future. Around 2025, companies such as Airbus and Boeing plan to start pro-duction of next-generation aircraft models and ramp up mass production.4,5
Carbon fiber composite material products have a modern aesthetic appeal, and as consumers increasingly value aesthetics, maintaining a glossy appearance has become one of the considerations for the durability of carbon fiber composite materials. Although carbon fiber composite materials have ad-vantages such as corrosion and fatigue resistance, there is currently limited research on their aging re-sistance. This article first explores the aging resistance of carbon fiber composite materials and further investigates the protective effects of coatings. The study examines the commonly used ultraviolet ab-sorbers (UVA), hindered amine light stabilizers (HALS), and the newly developed Eversorb® CP1 additive in the paint industry. Finally, DOE is applied to investigate the effects of different doses of CP1 and DFT on weather resistance and adhesion.6-11 Hopefully, this research will contribute to a better understanding of the weather resistance of carbon fiber composite materials in the industry.
Experiment
Experimental Materials
- Acrylic polyol resin, industrial grade, commercially available product.
- Aliphatic polyisocyanate curing agent, industrial grade, commercially available product.
- Eversorb CP1 ultraviolet absorber (UVA), hindered amine light stabilizer (HALS), industrial grade, Everlight Chemical Industrial Corporation.
- Carbon fiber composite material, commercial grade ,commercially available product.
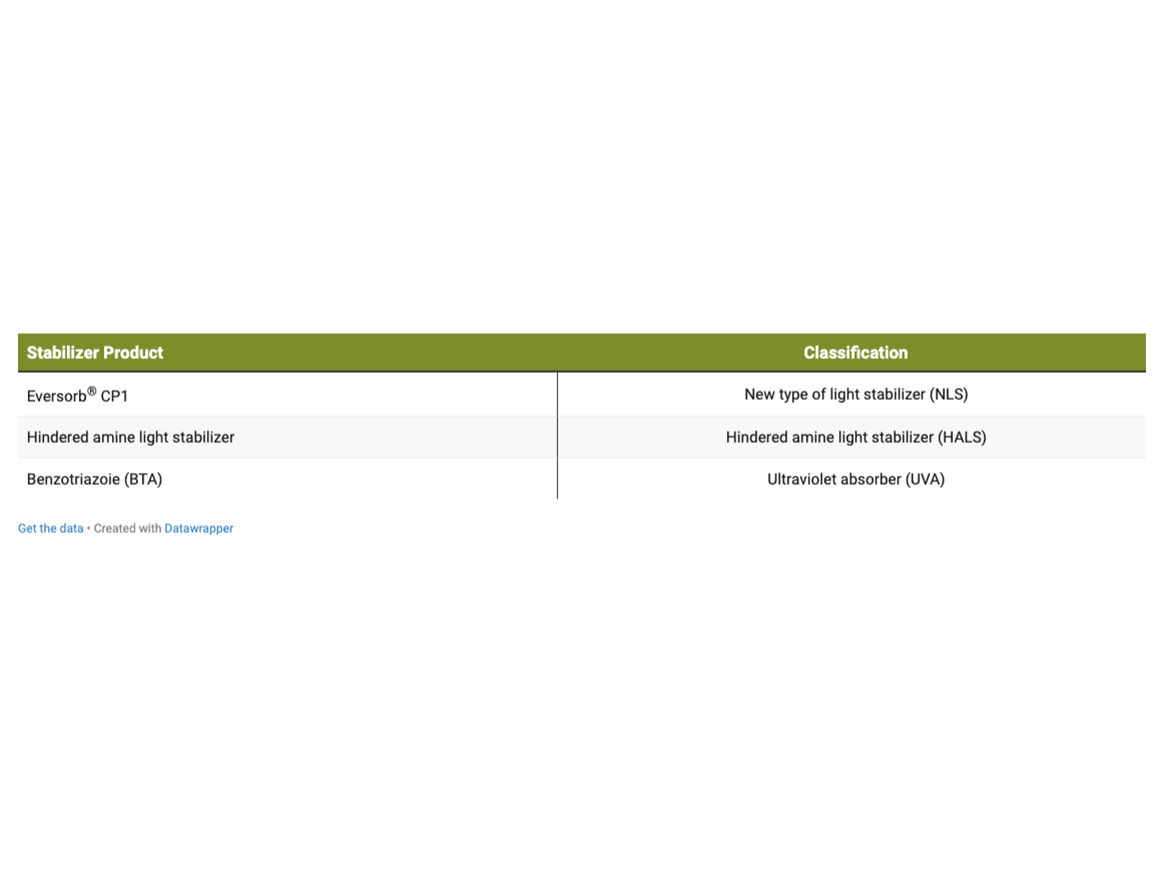
Experimental Device
Conduct artificial accelerated aging tests on untreated CFRP using ASTM G155 Cycle 1 testing for 150 hours, measure the initial color change.
- Weathering test machine (Xenon Weather-O-meter)
- Brand: Atlas, Type: Ci4000
- Colorimeter
- Brand: Konica Minolta, Type: CM5
- Gloss meter
- Brand: BYK, Type: Gardner GmbH
- Oven
- Brand: DENG YNG, Type: DO45
Looking for a reprint of this article?
From high-res PDFs to custom plaques, order your copy today!
Experimental Method
- Conduct artificial accelerated aging tests on untreated CFRP using ASTM G155 Cycle 1 testing for 150 hours, measure the initial color change.
- Mix acrylic polyol resin with aliphatic polyisocyanate curing agent and stir for 30 minutes. Apply a 30 μm (DFT) coating film on the CFRP. Conduct artificial accelerated aging test ASTM G155 Cycle 1 for 150 hours. Use a colorimeter and perform adhesion testing according to ASTM D3359 to observe color change and integrity of the paint film.
- Mix acrylic polyol resin with aliphatic polyisocyanate curing agent, and add Eversorb CP1, hindered amine light stabilizer, and benzotriazole (BTA). Stir for 30 minutes. Apply a 30 μm (DFT) paint film on the CFRP. Conduct artificial accelerated aging test ASTM G155 Cycle 1 for 2,100 hours. Use a colorimeter and perform adhesion testing according to ASTM D3359 to observe color change and integrity of the coating film.
- Mix acrylic polyol resin with aliphatic polyisocyanate curing agent and add different concentra-tions (0~3%) of Eversorb CP1. Apply coating films with DFT (60, 90 μm) on the CFRP. Conduct artificial accelerated aging test ASTM G155 Cycle 1 for 2,500 hours. Use a colorimeter and perform adhesion testing according to ASTM D3359 to observe the color change and integrity of the coating film.
Inspection Method
Artificial Accelerated Aging Test (ASTM G155 Cycle 1)
- Wavelength: 340 nm
- Irradiance: 0.35 W/m2/nm
- Exposure cycle: 102 min light at 63 (±2.5)°C
- Blank panel temperature: 18 min light and water spray (air temp not controlled)
- Observation of changes during accelerated aging tests using a colorimeter
Color Change Test
- Colorimeter
- Brand: Konica Minolta, Type: CM5
Adhesion Test (ASTM D3359)
- Test the adhesion of the coating film
Software and Analysis
- Software: JMP for analysis utilizing built-in analysis tools
Results and Discussion
Discussion of the UV-Aging Test without Coating CFRP
From Figure 1, it is evident that the untreated CFRP, subjected to 150 hours of artificially accelerated aging test without coating, exhibits obvious differences before and after the test, which can be easily discerned visually. Utilizing an optical colorimeter, the Delta value is measured to be 15.54, indicating a significant color change.

Discussion of Adhesion Under the UV-Aging Test with Coating CFRP
From Figure 2, it can be observed that the CFRP without clear coat showed significant improvement after undergoing a 150-hour artificial accelerated aging test, with a color change reduced to 4.29. However, according to the adhesion test (ASTM D3359) rating decreased from class 5B to class 1B.

Tips for Adhesion Test
ASTM-D3359 Class 5B: The edges of the cuts are completely smooth; none of the squares of the lattice is detached.
ASTM-D3359 Class 4B: Small flakes of the coating are detached at intersections; less than 5% of the area is affected.
ASTM-D3359 Class 3B: Small flakes of the coating are detached along edges and at intersections of cuts. The area affected is 5-15% of the lattice.
ASTM-D3359 Class 2B: The coating has flaked along the edges and on parts of the squares. The area affected is 15-35% of the lattice.
ASTM-D3359 Class 1B: The coating has flaked along the edges of cuts in large ribbons and whole squares have detached. The area affected is 35-65% of the lattice.
ASTM-D3359 Class 0B: Flaking and detachment worse than Grade 1B.
Comparison of Durability Resistance Between Eversorb CP1 and Conventional Light Stabilizers
Additives for light aging resistance in coatings commonly include ultraviolet light absorbers (UVA) or hindered amine light stabilizers (HALS) available in the market. This experiment aims to compare Eversorb CP1 with conventional light stabilizers. The assessment of light aging in this experiment will be based on color change and coating adhesion.
Color Change
The color change test results (Figure 3) of the control group and samples with added light stabilizers subjected to artificial accelerated aging (ASTM G155 Cycle 1) indicate noticeable color changes after 500 hours of accelerated durability. Both the Blank and the sample with 2% HALS exhibited significant color change. However, after 2,100 hours of accelerated durability, the sample with 2% Eversorb CP1 demonstrated the best durability performance. Compared to conventional market-available UVA dura-bility protection, Eversorb CP1 showed a 32% improvement in durability resistance. In contrast, Blank and sample with 2% HALS exhibited the poorest durability performance.
Adhesion Test
The results of ASTM G155 Cycle 1, the artificially accelerated aging test (Figure 4), indicate that at the initial 0-hour test, the adhesion test of all groups was 5B, indicating that none of the additives affected the initial adhesion. After 500 hours of accelerated durability, the adhesion test decreased from 5B to 0B in the Blank and the with addition 2% HALS, while the adhesion test for samples with added Eversorb CP1 and conventional market-available UVA were kept at 5B. As the accelerated durability time reached 1,700 hours, the adhesion test for samples with addition 2% Eversorb CP1 still maintained at 5B, whereas the adhesion test for conventional market-available UVA decreased from 5B to 0B. Con-tinuing the accelerated durability to 2,100 hours, the adhesion test for samples with an addition 2% Eversorb CP1 exhibited good performance with a rating of 3B.
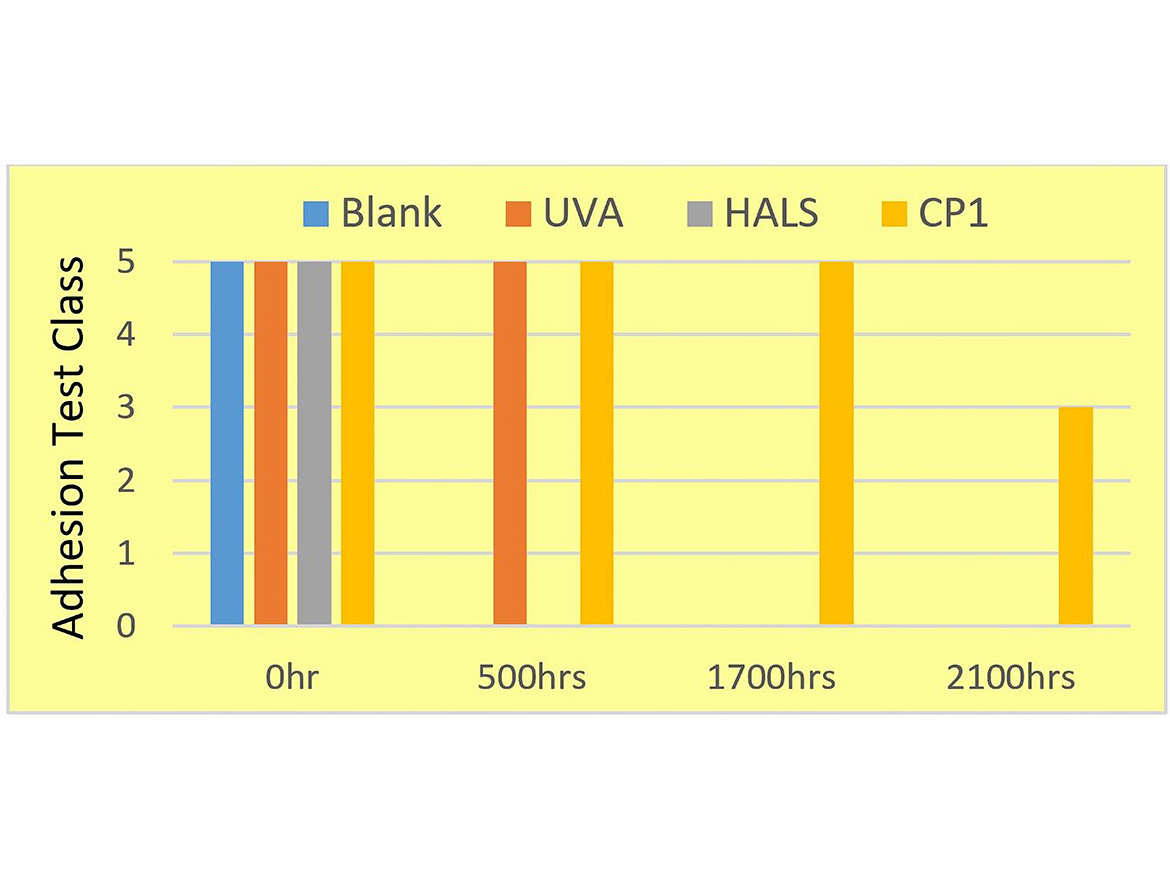
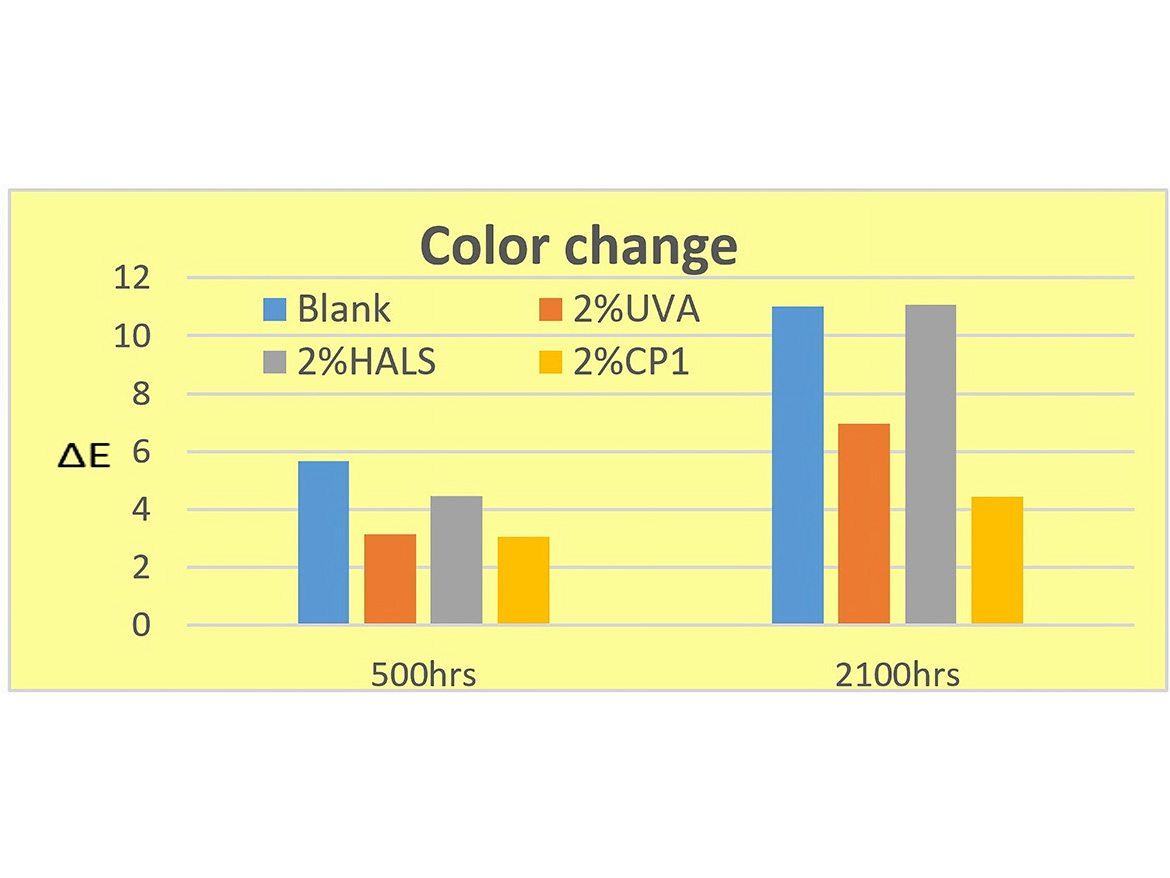
Discussion of the Impact of Different Addition Levels and Coating DFT of the Novel Composite Light Stabilizer on Durability Protection
This experiment employed DOE methodology to design test parameters and analyze their results, with a specific emphasis on utilizing Screening Design to assess the influence of the novel composite light stabilizer Eversorb CP1 and various DFT on durability performance, including color change and adhe-sion test results. The DOE is illustrated in Table 3. The parameter estimation table and Analysis of Var-iance (ANOVA) table based on the experimental data from Table 2 are presented below in Table 4 and Table 5, respectively.

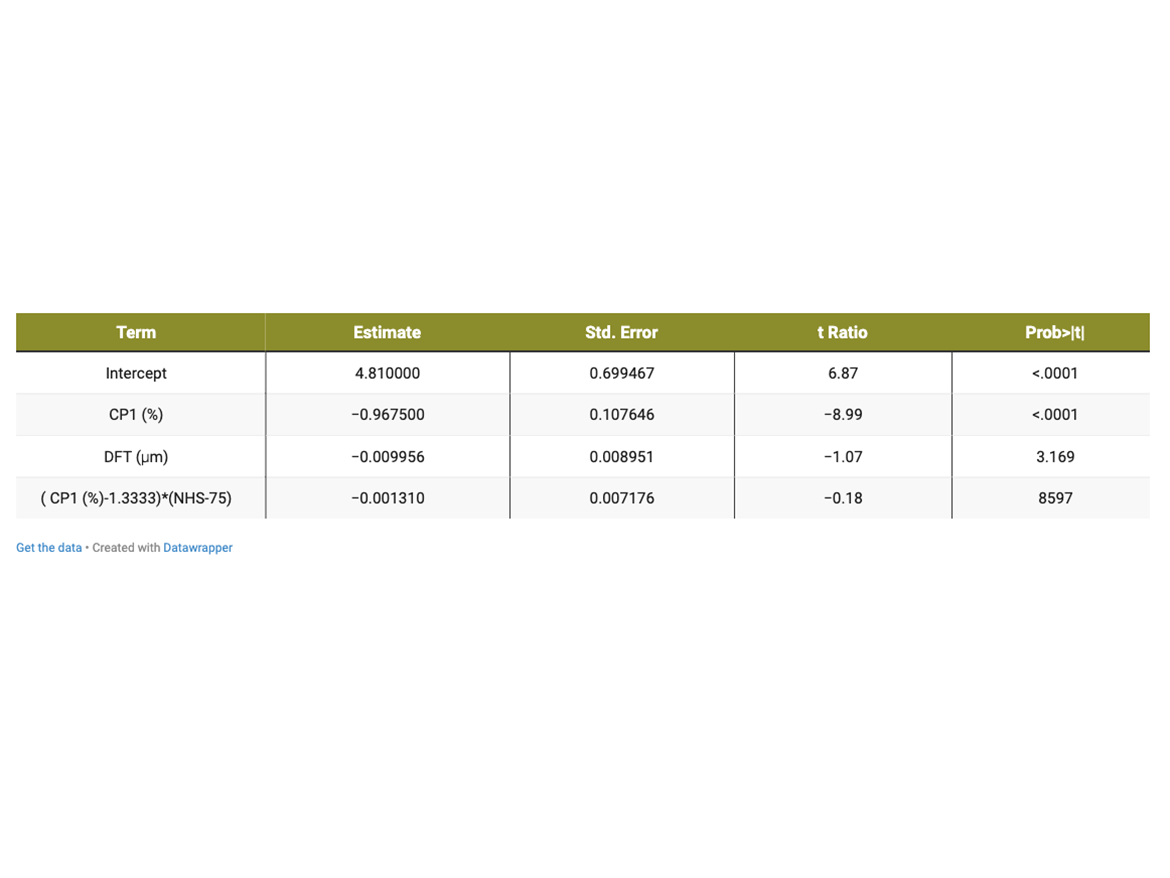

Analysis of the Impact of Composite Light Stabilizer Eversorb CP1 and DFT on Coating Color Change
The results of artificial accelerated aging for 2,500 hours indicate that the new composite light stabilizer has a high effectiveness in reducing coating color change, accounting for 88.7% of the variance, while the affect of coating film thickness (DFT) is 0.16%, as shown in Table 5. This suggests that adding the new composite light stabilizer has important effect on mitigating the color change of the coating under artificial accelerated aging.
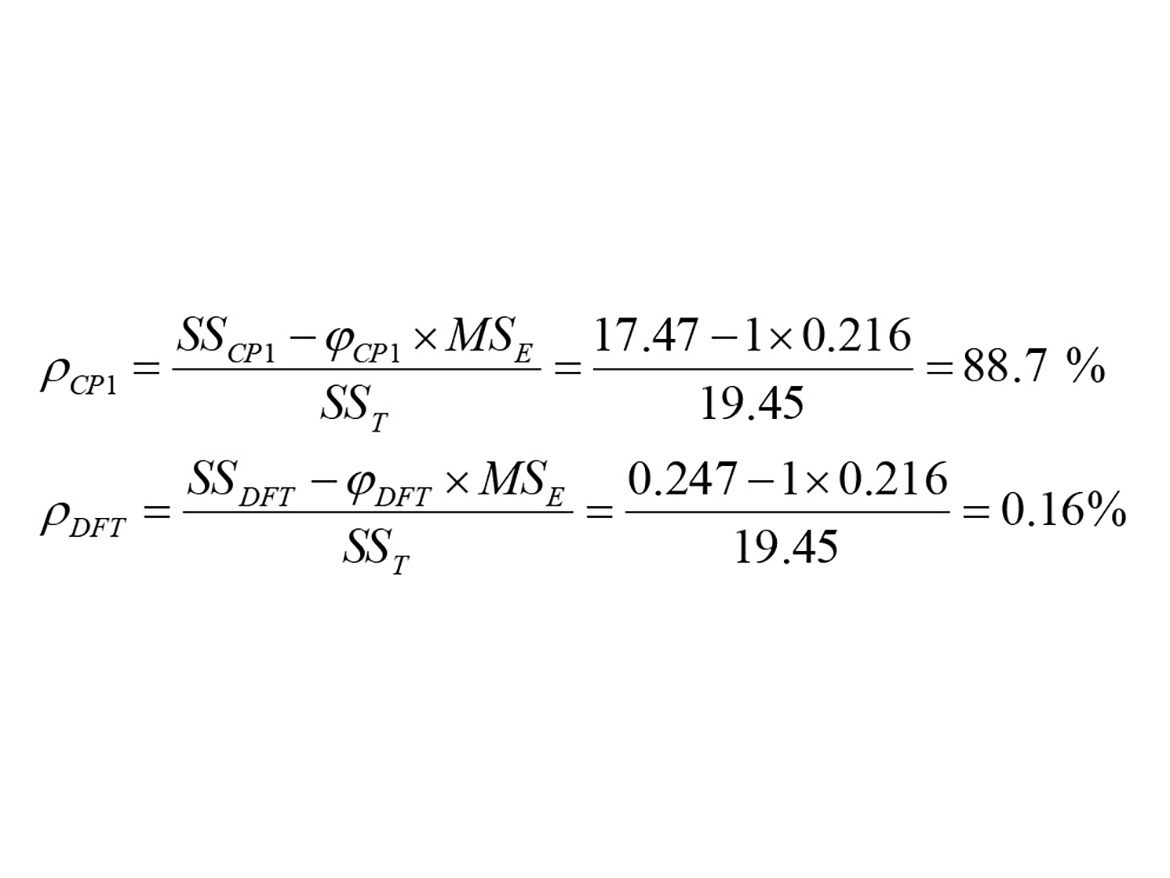
Analysis of the Impact of the New Composite Light Stabilizer and DFT on Coating Adhesion
After 2,500 hours of artificial accelerated aging, the results indicate that the novel composite light stabi-lizer Eversorb CP1 has a significant impact on reducing coating adhesion loss, accounting for 56.6% of the variance, while the effect of coating DFT is 1.4%, as shown in Table 6. This suggests that adding the novel composite light stabilizer Eversorb CP1 has a notable effect on mitigating coating adhesion loss.

Comprehensive Analysis of the Main Effects with the Novel Composite Light Stabilizer, DFT (μm) on Coating Color Change and Adhesion Test
From the results depicted in Figure 5, it is obvious that adding different percentages of the novel com-posite light stabilizer CP1 to the coating leads to larger slopes in both color change and adhesion test. This indicates that the addition of CP1 can effectively improve these properties compared to new light stabilizer (NLS) dosages. On the other hand, different DFT exhibit flatter slopes and lower magnitudes, suggesting limited improvement in color change and Adhesion rating with varying film thickness. Figure 5 further utilizes response surfaces to represent these findings.
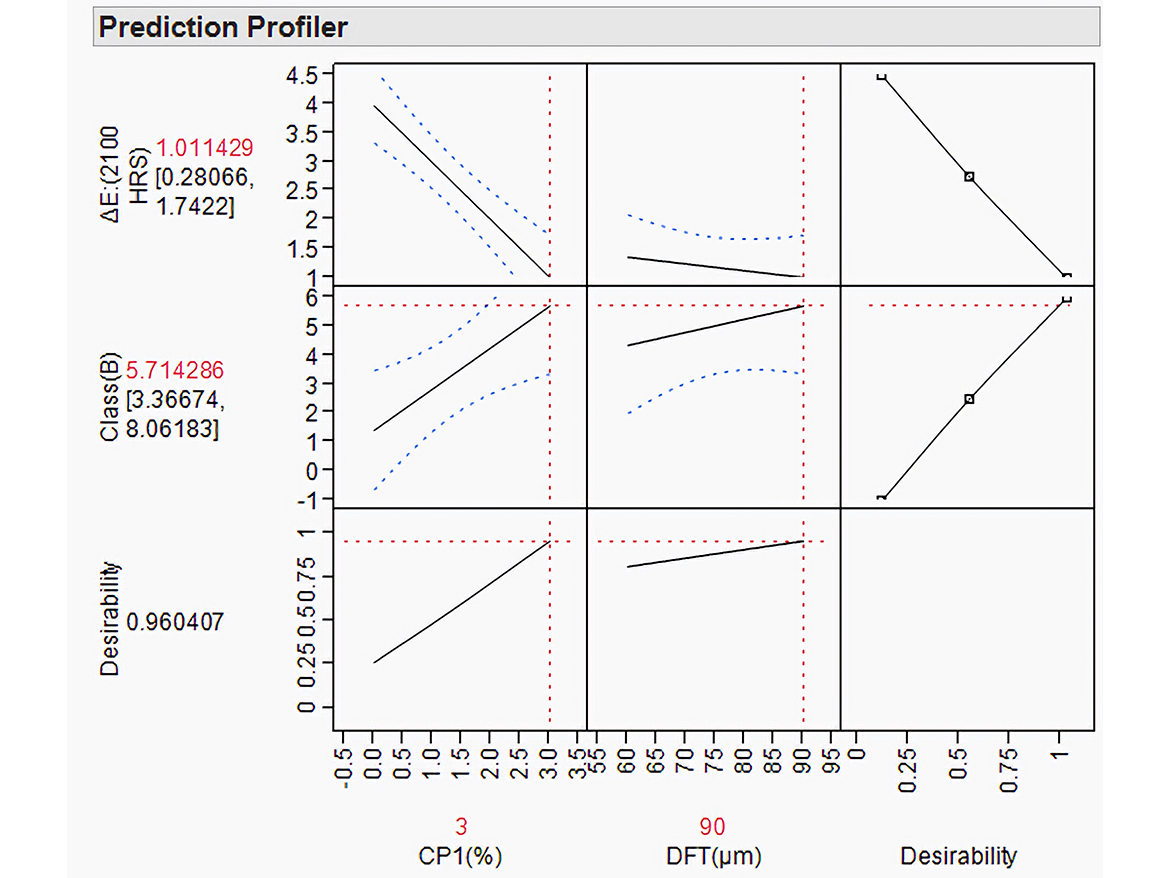
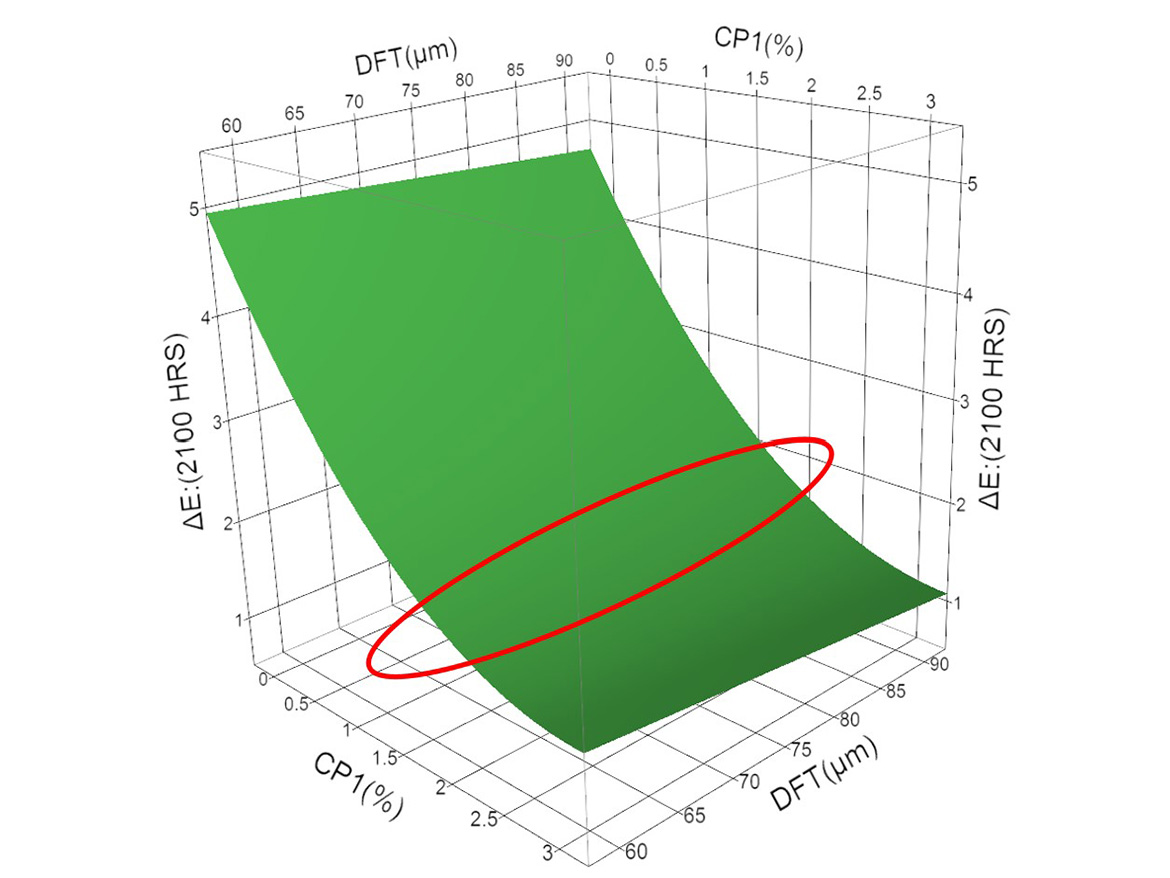
Using the data from Table 2, we further generated Figure 7 to present a response surface plot. The X-axis represents the percentage of Eversorb CP1, the Z-axis represents DFT (μm), and the Y-axis represents the variation in coating adhesion (Class). The red region indicates the optimal solution for mitigating the effects of coating color change and enhancing adhesion.

Conclusion
The durability performance of coated carbon fiber substrates is improved compared to non-coating carbon fiber composite. However, after undergoing a 150-hour artificial accelerated aging durability test, the adhesion rating of the coated carbon fiber substrate decreased from 5B to 1B.
In our study, the novel composite light stabilizer Eversorb CP1 was compared with HALS, UVAs, and an untreated blank group. The untreated blank group and the group treated with HALS exhibited poor durability performance after undergoing a 500-hour artificial accelerated aging test, showing significant color changes and a decrease in adhesion rating from 5B to 0B.
The addition of 2% Eversorb CP1 provided effective protection, as evidenced by minimal color variation and maintenance of a 5B cross-cut adhesion rating after a 1,700-hour durability test. Conversely, adhesion rating of the group treated with UVAs decreased from 5B to 0B after the same duration of durability. After 2,100 hours of artificial accelerated aging, the group treated with 2% Eversorb CP1 continued to exhibit effective protection, with minimal color variation and an adhesion rating of 3B.
Using a Design of Experiments (DOE) approach, we conducted artificial accelerated aging for 2,500 hours to investigate the effects of the addition level of the novel composite light stabilizer Eversorb CP1 and coating thickness. Regarding the color change durability test results, the impact of Eversorb CP1 was found to be 88.7%, while the effect of coating thickness (DFT) was 0.16%. As for the adhesion results, the impact of Eversorb CP1 was 56.6%, while the effect of coating thickness (DFT) was 1.4%.
In addressing durability issues with carbon fiber composites, the addition of the novel composite light stabilizer Eversorb CP1 provides the optimal solution for durability resistance.
References
1 柯澤豪.梁恆嘉. 碳纖維的故事[J] .科學發展, 2012,470(2).
2 冯帆.汽车轻量化的碳纤维复合材料应用分析[J]. 合成材料老化与应用[J],2022 ,51(1): 123-125.
3 蕭亞漩, 劉致中. 亞洲地區碳纖複材之應用市場及技術發展趨勢與方向[J]. SEP 2021 工程 • 94 卷 03 期.
4 富士経済.炭素繊維複合材料(CFRP/CFRTP)関連技術・用途市場の展望 2018[J].
5 富士経済.炭素繊維複合材料(CFRP/CFRTP)関連技術・用途市場の展望[J]. 2020 発刊日2020/02/14 111910820.
6 Yang, Y.; Sung, Y.; Chein, C.; Huang, Y. Novel light stabilizers for waterborne UV-curable coatings. Polymers Paint Colour Journal, 2013, 203(4583):13-15.
7 Yang, Y.; Ming-Hua, L.; Yu-Shu, S.; Yin-Ting, L.; Shian-Fang, C.; Chin-Hsien, C.; Huang, Y. Light stabilizers make the UV protection of waterborne UV-curable coatings easier. Coatings World, 2014, 19(6): 38-40.
8 Yang, Y.; Ming-Hua, L.; Yu-Shu, S.; Yin-Ting, L.; Shian-Fang, C.; Chin-Hsien, C.; Huang, Y. Less yellowing in uv coat. European Coating Journal, 2017(4): 136-140.
9 Huang, Y.; Yang, Y. Light stabilizers for clear coatings. Polymers Paint Color Journal, 2010, 200(4544):38.
10 Yang, Y. Sung, Y.; Chein, C.; Huang, Y. Light stabilizers for environmental friendly coatings. Polymers Paint Color Journal, 2012, 202(4571):16-18.
11 Yang, Y.; Lee, S.; Huang, Y. Light stabilizers make the UV protection of environmental friendly coatings easier. Coatings World, 2012, 17(4):83-85.
For more information, click here.