Fast-Cure, High UV-Resistant, and EHS-Friendly Epoxy Coatings

ismagilov, iStock, via Getty Images
The coatings industry is constantly innovating to meet the challenges of increasingly stringent environmental regulations and demand for worker and end-user safety, while fulfilling the need to improve productivity and reduce downtime. Technology advancements have equipped the industry with epoxy systems that deliver fast cure speed and improved EHS (environment, health, and safety) profile. Two-component epoxy systems are well known for their excellent mechanical properties, chemical resistance, and adhesion to substrates. They have been widely used as protective coatings for concrete, metal, and wood surfaces. The protective coatings provide an impermeable barrier, improve aesthetics, and enhance chemical resistance to various chemicals. For these reasons, epoxy systems are frequently chosen over other technologies as a floor coating material.
Two-component epoxy systems are thermoset polymer networks formed by crosslinking epoxy resin(s) and curing agent(s) (also known as hardeners), and the properties of these systems depend on both resin and curing agent. Curing agents are typically based on amine chemistry. Commercially available epoxy resins are limited to bisphenol-A, bisphenol-F, and novolac. On the contrary, there is a wide range of curing agent options to optimize a coating system. The curing agent plays a critical role in defining the cured epoxy network, and is often designed to tailor cure speed and coating performance, thus providing a toolbox for formulators to meet performance targets and EHS requirements.
When it comes to curing agent design, fast cure to improve productivity often comes with trade offs in performance, such as durability, UV resistance, chemical resistance, and working time, and compromises EHS requirements. The cure speed of amine-epoxy systems is accelerated by using accelerators such as phenolic compounds like t-butylphenol, bisphenol A, and salicylic acid.1 Phenolic accelerators are usually not EHS friendly, and pose health and safety hazards to the workers and the environment. In addition, these accelerators often degrade the UV resistance of the coatings.
This article presents a fast-cure, high UV-resistant curing agent that addresses both performance and EHS gaps in the current commercially available systems. This new curing agent enables a rapid return to service and delivers coatings with exceptional aesthetics at ambient and low temperatures, outstanding carbmation and UV resistance, and extended working times.
Experimental
A new curing agent, Ancamine 2880, code name FC-1 in this paper,2 was developed based on a proprietary amine chemistry. Two commercially available curing agents, BM-1 and BM-2, were used as benchmark products for their known good UV resistance and cure speed. However, both have an unfavorable EHS rating. All coatings or castings were prepared with standard bisphenol A epoxy resin or diluted with a glycidyl ether of C12-14 alcohol3 at 1:1 stoichiometry. Curing agent and resin were mixed with a speed mixer for 1 minute at 3,500 rpm before testing. All the test methods in this article are listed in Table 1.
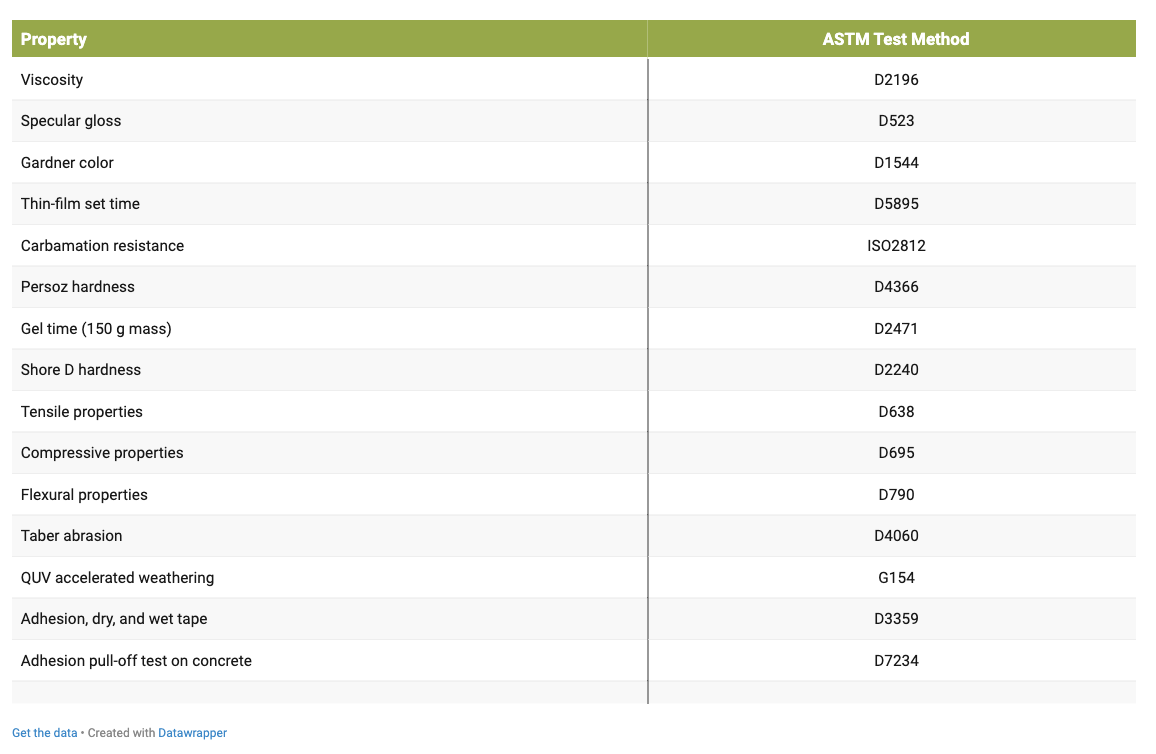
The cure speed or thin film set time (TFST) was evaluated in accordance with ASTM D5895. A coating was drawn down at 6 mil wet film thickness (WFT) on a 1 in. x 1 in. glass substrate, and placed on a Beck-Koller recorder at a specific scale of travel time under the designated environmental conditions.
The carbamation-resistance test was conducted on black Leneta charts according to ISO 2812 method. The coating was drawn down at 6 mil WFT and allowed to cure under the designated environmental condition and time duration. A water-saturated, 1 in. x 1 in. cotton patch was placed on the cured coating and covered with a watch glass to prevent water evaporation. The cotton patch was removed after 24 hours, and the wet coating surface was dried with a tissue. The appearance of the coating was judged on a scale of 1 to 5, with 5 being the best (showing no effect), and 1 being the worst (white surface).
The viscosity profiles were generated on a Brookfield viscometer at 23 °C using about 20 g of mixed material. Gel time of a 150 g mixture of epoxy resin and curing agent was recorded using Techne GT-3 gelation timer, as the time when the product components gelled enough to arrest the free movement of disposal plungers operated at one cycle per minute.
Persoz hardness was determined in accordance with ASTM D4366 method. The coatings were applied at 6 mil WFT on a 3 in. x 4 in. glass substrate, and allowed to cure under the designated environmental conditions and time duration. Shore D hardness was performed according to ASTM D2240, 35 g of epoxy resin and curing agent was poured in 2.75 in.-diameter circular metal lid to get a 0.4 in.-thick clear cast.
Intercoat adhesion test was established by two methods. ASTM D3359 method measures adhesion by tape (test method A – X cut tape test). The epoxy primer was coated on a steel substrate, followed by application of a topcoat onto the primer after a specified time. The coatings were cured at ambient conditions for 7 days before testing. The results were noted on a scale of 1A-5A, with 5A being best, showing no peeling or removal of coatings. The other method was ASTM 7234. A 1.5 in. thick concrete block was sand blasted to CSP 3 surface profile prior to applying 10 mil WFT of epoxy coat. The coatings were cured for 7 days under the designated environmental conditions, before performing the dolly pull-off test using a portable adhesion tester. The adhesion strength and mode of failure were documented.
Differential scanning calorimetry (DSC) was utilized to determine degree of cure. About a 5~10 mg sample of stoichiometric mixture of epoxy resin and curing agent was probed by TA instruments DSC Q20 at a heating rate of 10 °C/minute. The sample was heated in the temperature ranging from -50 °C to 250 °C at 10 °C/minute, cooled back to -50 °C and the test was repeated.
The abrasion resistance was tested per the ASTM D4060 standard test method. In this method, various epoxy curing agent systems were coated at 6 mil WFT on 4-5 steel coupons of the size of around 4 in. x 4 in. x 0.125 in., and was allowed to cure for 7 days at ambient conditions. Then a 0.25 in. diameter hole was drilled out of the center of each test specimen. The test specimens were weighed prior to abrading them. A CS-17 harsh-abrading wheel with a 2,000 g load was placed on the coatings. The specimens were then abraded with up to 500 cycles each, and they were weighed after abrasion. The average weight loss in milligrams (mg) was then calculated for all of the systems tested.
For measurement of mechanical properties in tensile, flexural, and compressive modes, stoichiometric mixture of bisphenol A resin and curing agent was casted and cured for 7 days at ambient conditions. A test for tensile properties was conducted as per ASTM D638. Mechanical properties in compressive mode were determined according to ASTM D695. The test was conducted on 1 in. cube at 0.05 in./minute cross-head test speed. The test was stopped at yield point or 0.25 in. displacement. A flexural test was performed in accordance with ASTM D790. The test is stopped when the specimen reaches 5% deflection or the specimen breaks before 5%.
Results and Discussion
Handling Properties
The new curing agent, Ancamine 2880 (FC-1), was developed based on a proprietary amine technology without using the substance of high concern such as bisphenol A, alkylphenol, or salicylic acid. Unlike the two benchmark products, BM-1 and BM-2, with unfavorable EHS rating, FC-1 offers fast cure speed with favorable EHS rating. Table 2 summarizes the important handling and performance properties of the newly developed curing agent FC-1 and two commercially available benchmark products, BM-1 and BM-2. FC-1 offers a low neat viscosity as compared to BM-1 and BM-2. The performance was evaluated by mixing the curing agents with bisphenol A resin at 1:1 stoichiometric ratio. The low mixed viscosity of FC-1 system allows for easy handling and application. FC-1 maintains similar gel time as offered by BM-1 and BM-2 at ambient conditions.
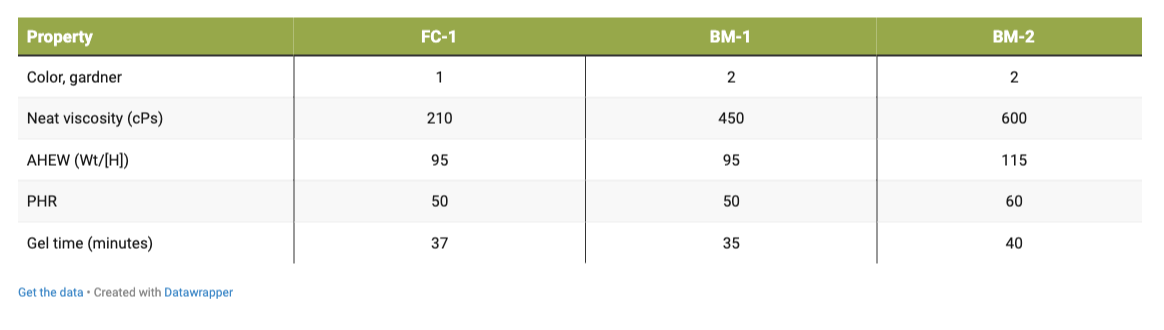
Rapid Property Development
The new curing agent provides fast cure speed and property development as evident from Table 3. FC-1 delivers fast cure speed similar to BM-1, but faster than BM-2. Rapid early mechanical property development, of thick casting, and thin coating are outcomes of fast cure speed. As seen from Table 3, FC-1 exhibits faster Shore D and Persoz hardness development as compared to BM-2.

Rapid property development is demonstrated by cure viscosity build up. Figure 1 shows the cure viscosity profiles of the curing agents at ambient condition. Fast viscosity build up often reflects on high reactivity. As shown in Figure 1, slowest viscosity build up by FC-1 offers prolonged working time while keeping the cure speed similar or faster compared to the benchmark products.

A high degree of cure is a very important feature in industrial flooring applications in terms of a coating’s performances on mechanical, chemical, and thermal resistance properties. Degree of cure is directly related to the reactivity of epoxy curing agent systems and was determined by DSC. Figure 2 displays the degree of cure of epoxy curing agent systems cured at ambient and 10 °C environments. At ambient conditions, FC-1 displayed similar reactivity compared to BM-1, but faster reactivity than BM-2. On the other hand, FC-1 provided fastest reactivity at 10 °C conditions. Additionally, FC-1 reaches almost 100% degree of cure on day 1 at ambient and on day 7 at 10 °C conditions.

Ancamine 2880 (FC-1) Offers Best Coating Appearance
One of the important performance attributes of epoxy coating systems is carbamation resistance, which is frequently related to amine blushing or blooming. The chemical component of the epoxy coating system responsible for the blushing or blooming is the amine curing agent. The hygroscopic low-molecular-weight amines migrate from the bulk of the coating to the surface and react with atmospheric carbon dioxide and moisture to form an ammonium carbamate. The outcome of the above undesirable side reactions is that some amine is consumed, which results in compromised stoichiometry in the epoxy-amine reaction. Ultimately, the under-cure epoxy coating appears as greasy, tacky, hazy, reduced gloss, with white salt on the surface. And most importantly, carbamation leads to poor intercoat adhesion. The result of carbamation resistance of FC-1, BM-1, and BM-2 is summarized in Table 4, and the photographs are shown in Figure 3, as well. The results shown in the table are with relative rating scales of 1 to 5, with 5 being the best, showing no signs of carbamation. FC-1 exhibits excellent coating appearance and outstanding carbamation resistance with a rating of 5 even after only 1 day at 10 °C. At a lower temperature, reactivity of epoxy and amine decreases. During this period, reaction of amine with carbon dioxide and moisture can be favored over that with epoxy, which results in carbamation. The new curing agent FC-1, designed by a proprietary chemistry, shows outstanding carbamation resistance at 10 °C compared to benchmark products.

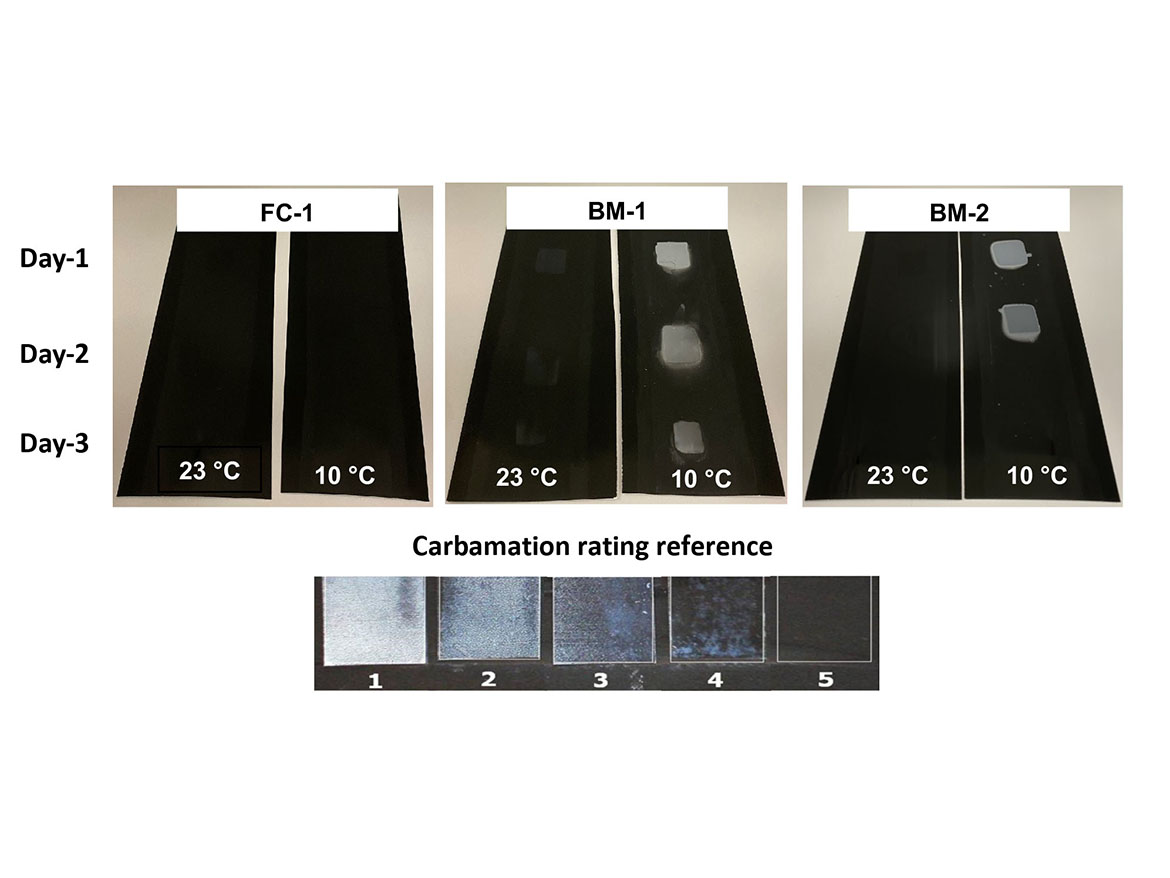
Effect of Humidity on Coating Performance
Two major factors that may impact a coating’s performance are humidity and temperature. At high relative humidity (RH) and low temperature, moisture in the air condenses on the coating surface, and the amine on surface reacts with carbon dioxide and moisture to form carbamate. Low temperature slows down the amine-epoxy reaction and increases the carbamate side reaction. High humidity and low temperature negatively affect the cure performance and coating appearance. Table 5 provides a summary of cure speed, carbamation resistance, and water spotting resistance of epoxy coatings cured with FC-1 at 23 °C, 50% RH and at 10 °C with varying RH. The 6.5-hour cure speed at 23 °C/50% RH was lengthened to 14 hours due to reduced epoxy-amine reactivity at 10 °C/60% RH. The cure speed at 10 °C was not affected by varying the RH ranging from 60% to 85%. The coating retained excellent carbamation resistance and water-spotting resistance across the temperature and humidity ranges under consideration.

Intercoat Adhesion and Over-Coatability
High-performing floorings have multi-layer systems depending on the target end use. Flooring with two-coat systems is preferred in terms of economics, where mechanical properties are not so important. On the other hand, a mid-coat is required to maintain concrete integrity for protection against mechanical wear and tear, in industrial floors for example. Generally, a topcoat is applied to improve protection to the underlying epoxy mid-coat. Intercoat adhesion between a primer and a topcoat, a primer and a mid-coat, and mid-coat and topcoat is an important parameter for a successful high-performance multi-stage floor installation. For a fast return-to-service multi-stage flooring system such as one-day flooring, each stage is required to cure within a short period of time, especially for primer. Typically it is a requirement for a primer to cure within 8 hours even at low temperature, so the topcoat can be applied by the same crew and same shift.
The intercoat adhesion test was carried out on concrete and steel substrates. When FC-1 was used as a topcoat, a fast-cure epoxy was used as primer on both concrete and steel substrate. And when FC-1 was used as a primer on steel substrate, a highly UV-resistant and fast-cure aliphatic polyurea was used as topcoat to provide extra UV stability.
The standard test method for intercoat adhesion on concrete is the pull-off test based on ASTM D7234. The concrete blocks used in this study had a surface profile of CSP 2 or 3. For tests with damp concrete, the concrete block was submerged in water for 24 hours, and then removed from water before coating. The fast-cure epoxy primer4 was coated at 6-mil WFT on dry and damp concrete, and cured at ambient and 10 °C environment. The 10 mil FC-1 topcoat was applied 4 hours after the primer was coated at ambient condition and after 8 hours at 10 °C. The test results in Table 6 demonstrate the excellent intercoat adhesion between a fast-cure epoxy primer and FC-1 topcoat on both dry and damp concrete. At ambient temperature, an FC-1 system can be top coated within 4 hours, and only 8 hours at 10 °C onto the fast-cure primer to achieve a one-day flooring system with excellent intercoat adhesion. Figure 4 shows the cohesive failure of concrete for both primer only and with a topcoat.

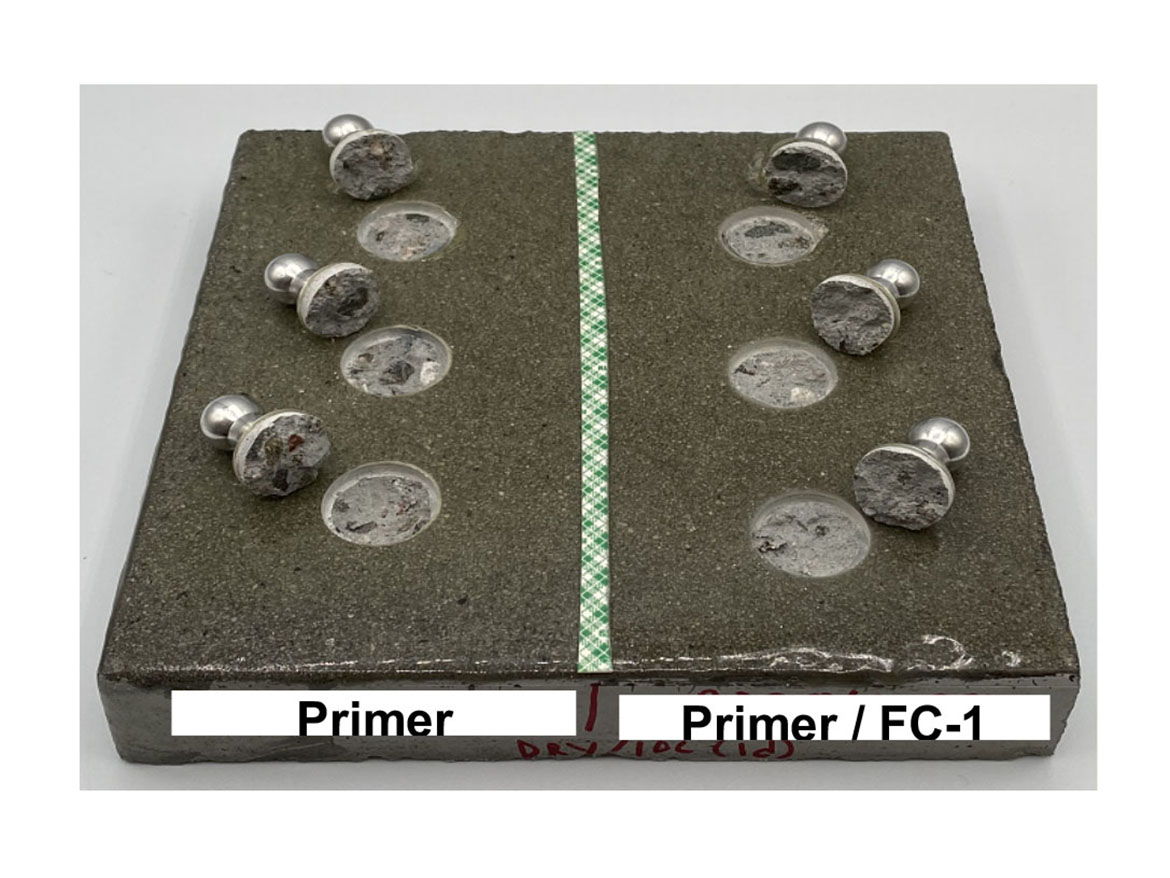
The intercoat adhesion was also evaluated on steel substrate according to ASTM D3359. The X-cut and crosscut results were recorded as a relative scale of 1A-5A, with 5A being best, no visible peeling or removal of coatings. Two sets of experiments were conducted using two different coating systems. The first set of the two-coat system is the same as on concrete substrate, the fast-cure epoxy primer was coated at 6-mil WFT on steel substrate, and after 4 hours the FC-1 topcoat was applied at 10 mil WFT. In the second set of experiments, the FC-1 was used as primer and coated at 6 mil WFT on steel substrate, and after 6 hours a commercially available aliphatic polyurea5 topcoat was applied at 10 mil WFT. Both systems were cured at controlled ambient condition for 7 days. The test results are shown in Table 6. The results of the first set experiment collaborate with the data on concrete substrate where FC-1 showed excellent adhesion to the epoxy primer. Similarly, when used as primer on steel panel, FC-1 demonstrates excellent adhesion to polyurea topcoat. The fast cure and outstanding intercoat adhesion of FC-1 offers a solution for fast return to service where multiple layers can be applied within 24 hours.
Abrasion Resistance
The abrasion resistance was tested per the ASTM D4060 standard test method. The curing agents mixed with different epoxy resins, were coated at 6 mil WFT on steel substrates and cured for 7 days at ambient conditions. The abrasion test was conducted using the CS-17 harsh-abrading wheel with a 2,000 g load for 500 cycles. The average weight loss in milligrams given in Table 7 illustrates excellent abrasion resistance of FC-1 in all the resin systems tested. This makes FC-1 an ideal candidate for flooring to withstand wear and tear in high-traffic areas.

*Resin 1: Bisphenol A epoxy (EEW = 190)
**Resin 2: 90% Bisphenol A epoxy – 10% Epodil 748
***Resin 3: 50% Bisphenol A epoxy – 50% Novolac epoxy
Mechanical Properties
Mechanical characteristics of a through-cure epoxy is critical in flooring applications to prevent structural disintegrations. The tests in tensile, compression, and flexural modes were evaluated to ensure that the cured epoxy material maintains its high mechanical properties. The details of sample preparation and test method are described in the experimental section. Table 8 presents a summary of mechanical properties of curing agents FC-1, BM-1, and BM-2 cured with standard bisphenol A epoxy resin. The test data show that epoxy material cured with FC-1 maintains high mechanical characteristics by providing high load-bearing capability, stiffness, resistance to deformation, and resistance to cracking.

Chemical Resistance
Two-component epoxy coatings protect the underlying substrates from chemical attack by creating a highly crosslinked impermeable barrier layer between the substrate and environment. A chemical resistance study was conducted as per ASTM D1308. Curing agent and epoxy were blended and coated on 4 in. x 12 in. steel panels at 6 mil WFT, and cured for 7 days at ambient conditions. Cotton patches of different class of chemicals were placed on 7-day-cured films and covered with a watch glass. Patches were removed after 24 hours of exposure, followed by a pat dry with paper towel. The coatings were visually inspected and evaluated. The results were recorded as the film appearance on a relative scale of 1-5, with 5 being excellent, no swelling or color change. A summary of the test results is given in Table 9. FC-1 provides good-to-excellent resistance to most of the selected chemicals of different classes, such as organic solvent, alkali, inorganic, and inorganic acid. Good chemical resistance is a requirement for flooring application to withstand daily cleaning chemicals and accidental spillage or leakage of chemicals in industrial settings. The good appearance, high aesthetics, and good chemical resistance properties of FC-1 make it an ideal candidate, not only for institutional and decorative flooring, but also for industrial and commercial flooring such as factories and commercial kitchens.

5: Excellent, 4: Good, 3: Fair, 2: Poor, 1: Not recommended
Cured with standard bisphenol A resin (EEW 190) diluted with 10% Epodil 748.
UV Resistance
Epoxy coatings provide excellent chemical resistance, strong mechanical properties, and good adhesion to a variety of substrates. However, epoxy coatings degrade when exposed to UV light in outdoor conditions, resulting in discoloration, reduced gloss, chalking, and delamination. One of the biggest challenges in the coatings industry is to formulate epoxy coating with high UV resistance for outdoor applications. In the present study, photostability was studied in accordance with ASTM D4587. 6 mil of curing agent epoxy coating was applied on pre-coated white polyurethane steel panels and allowed to cure for 7 days at ambient conditions. The cured epoxy panels were exposed to UV irradiation in the accelerated weathering QUV machine equipped with fluorescent ultraviolet lamp apparatus (340 nm bulbs, 0.89 W/m2, nm irradiance at 50 °C) operated in accordance with ASTM G154 for 1,000 hours without condensation. The data for δE, yellowness index (YI), and gloss retention were collected before and after exposure to UV irradiation on a regular interval. Figure 9 describes the UV resistance of epoxy coating cured with FC-1 and the benchmarked products BM-1 and BM-2. The benchmarked products are known for their good UV resistance in epoxy coatings. FC-1 exhibits good UV resistance similar to BM-2, and better than BM-1. The UV resistance can be further improved by using hydrogenated epoxy resin in place of standard bisphenol A resin, which will be described in the following section of this paper.
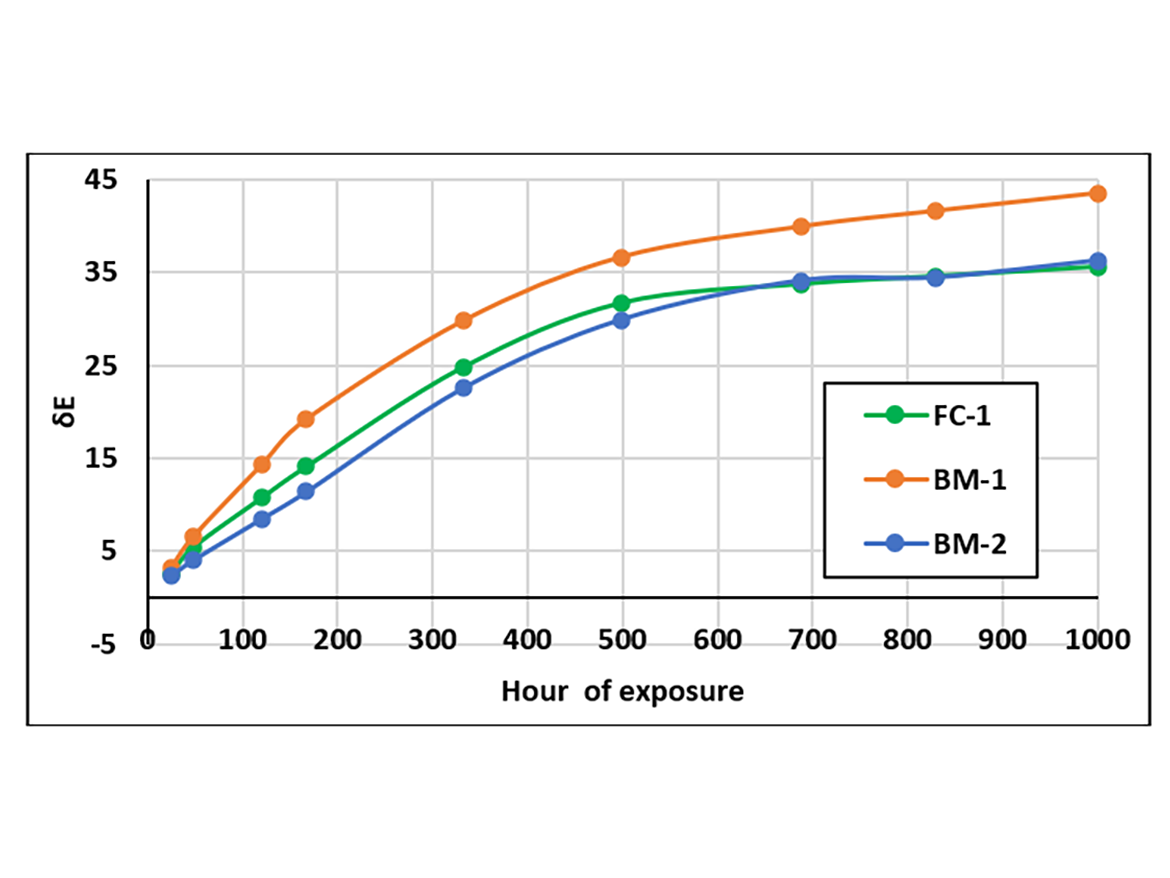
Performance Evaluation of Ancamine 2880 (FC-1) with Hydrogenated Epoxy Resins
The major cause of yellowing in bisphenol epoxy resin system is the oxidation of the aromatic ring. There are different chemical approaches to mitigate such chemical structure degradation, for example using silicon-based epoxy hybrids,6 doping standard epoxy system with UV-resistant additives, and hydrogenation of bisphenol epoxy resins.7,8 Of these solutions, the hydrogenation of bisphenol epoxy offers the best techno-economic viability. Hydrogenated bisphenol A epoxy resin does not contain double bonds in the molecule, and has the advantages of good weather resistance for outdoor use, excellent electrical properties, low viscosity, and good processability. Compared to bisphenol A, hydrogenated bisphenol A improves the UV-resistance performance to maintain color stability, thus prolonging the service life.
Three hydrogenated bisphenol A epoxies (HE-1, HE-2 and HE-3)9 were selected for performance evaluation with the curing agent FC-1. The handling and performance properties of the three resins with FC-1 curing agent are summarized in Table 10. FC-1 in combination with HE-2 resin provides the fastest cure speed with long working time, and offers a walkable floor in one day, even at 10 °C.

The study of chemical resistance was performed in the same manner as mentioned in the previous section, and the results are shown in Table 11. FC-1 curing agent in combination with HE-2 hydrogenated resin exhibits better resistance to a different class of chemicals compared to HE-2 and HE-3 resins.

A UV-resistance study of the coatings, prepared by mixing FC-1 with bisphenol A epoxy (BPA) and the three hydrogenated epoxy resins, was conducted by following the same procedure as described in the previous section. The bisphenol A resin was included to compare its UV stability with hydrogenated bisphenol A resin. The color retention and yellowness index (YI) are shown in Figure 6A and 6B, respectively. FC-1 curing agent in combination with HE-1 hydrogenated resin delivered the best UV resistance compared to HE-2 and HE-3 resins. All three hydrogenated resins outperformed the BPA resin as expected. It is also notable that the HE-1 resin exhibited greater than two-times-better UV resistance, as can be concluded from color retention and yellowness index values after 1,000 hours of exposure.

Conclusions
Fast return to service and productivity improvement are key market trends for the coatings industry that drive new product innovation. This requires fast cure speed of coatings without sacrificing performance and EHS requirements. Two-component epoxy systems have a proven track record in coatings application owing to good adhesion to various substrates, and excellent chemical resistance and mechanical properties. To achieve fast cure speed, epoxy systems are often accelerated with phenolic compounds to improve cure speed, however these compounds are typically not EHS-friendly due to their health hazard rating and/or degrade the UV resistance.
Fast-curing agent Ancamine 2880 (FC-1) was developed to close the performance gaps and improve the EHS profile. This new curing agent delivers fast cure speed with good working time. The resulting coatings exhibit exceptional aesthetics at ambient and low temperatures, and good abrasion, UV, and chemical resistance. In a multiple-coat system, FC-1 demonstrates excellent intercoat adhesion with epoxy primer and with aliphatic-polyurea topcoat. The fast cure speed in combination with superior coating appearance and excellent mechanical properties renders FC-1 an ideal candidate for one-day flooring solution where both primer and topcoat can be applied on the same day and are ready for service within 24 hours. Furthermore, when cured with hydrogenated resin, the coating maintains rapid cure speed and excellent UV resistance, achieving results not attainable with current available systems. This opens the possibility for using FC-1 epoxy system for outdoor application where high UV durability is a requirement for long service life.
References
1 Lee, H.; Neville, K. Handbook of Epoxy Resins, McGraw-Hill, Inc., New York, 1967, 5-1 to 5-18.
2 FC-1: Ancamine 2880, Evonik Corporation.
3 Epodil® 748 Reactive Diluent, Evonik Corporation.
4 Fast epoxy primer: Ancamine 2850, Evonik Corporation.
5 Aliphatic polyurea topcoat: Amicure IC20 with standard HDI trimer.
6 Chruściel, J. J.; Leśniak, E. Modification of epoxy resins with functional silanes, polysiloxanes, silsesquioxanes, silica and silicates. Prog. Polym. Sci. 2015, 41, 67,
7 Murai, K.; Nishi, M.; Honda, M. Alicylic epoxy compounds and their preparation process, alicylic epoxy resin composition, and encapsulant for light-emitting diode. U.S. Patent 6,756,453B2, 2004.
8 van Laar, F.; Becker, M. Heterogeneous ruthenium catalyst and method for hydrogenating a carboxylic aromatic group, in particular for producing core hydrogenated bisglycidyl ether bisphenols A and F. U.S. Patent 2008/0200703A1, 2008.
9 HE-1, HE-2, and HE-3 are Epalloy 5000, 5001 and 5200 respectively.
This paper was presented at the 2024 Waterborne Symposium in New Orleans, LA.
Looking for a reprint of this article?
From high-res PDFs to custom plaques, order your copy today!