Improving Manufacture Efficiency Through the Use of Water-Based UV-Curable Polyurethanes
May 6, 2024
Improving Manufacture Efficiency Through the Use of Water-Based UV-Curable Polyurethanes
May 6, 2024Serhii Sheremet, Creatas Video+ / Getty Images Plus, via Getty Images
High-performance UV-curable coatings have been used in the manufacture of flooring, furniture, and cabinets for many years. For most of this time, 100%-solid and solvent-based UV-curable coatings have been the dominant technology in the market. In recent years, water-based UV-curable coating technology has grown. Water-based UV-curable resins have proven to be a useful tool for manufacturers for a variety of reasons, including passing KCMA stain, chemical resistance testing, and reducing VOCs. For this technology to continue growing in this market, several drivers have been identified as key areas where improvements need to be made. These will take water-based UV-curable resins beyond simply having the “must haves” that most resins possess. They will begin adding valuable properties to the coating, bringing value to each position along the value chain from coating formulator to factory applicator to installer and, finally, to the owner.
Manufacturers, especially today, desire a coating that will do more than just pass specifications. There are also other properties that provide benefits in manufacturing, packing, and installation. One desired attribute is improvements in plant efficiency. For the water-based coating this means faster water release and faster blocking resistance. Another desired attribute is improving resin stability for capture/reuse of a coating, and management of their inventory. For the end user and installer, desired attributes are better burnish resistance and no metal marking during installation.
This article will discuss new developments in water-based UV-curable polyurethanes that offer much-improved 50 °C paint stability in clear, as well as pigmented coatings. It also discusses how these resins address the desired attributes of the coating applicator in increasing line speed through fast water release, improved block resistance, and solvent resistance off the line, which improves speed for stacking and packing operations. This will also improve off-the-line damage that sometimes occurs. This article also discusses improvements demonstrated in stain and chemical resistance important to installers and owners.
Background
The landscape of the coatings industry is ever evolving. The “must haves” of just passing the specification at a reasonable price per applied mil is simply not enough. The landscape for factory-applied coatings to cabinetry, joinery, flooring, and furniture is quickly changing. Formulators who supply coatings to the factories are being asked to make coatings safer for employees to apply, remove substances of high concern, replace VOCs with water, and even use less fossil carbon and more bio carbon. The reality is that all along the value chain, each customer is asking the coating to do more than just meet the specification.
Seeing an opportunity to create more value for the factory, our team began to investigate at the factory level the challenges these applicators were facing. After many interviews we began to hear some common themes:
- Permitting obstacles are preventing my expansion goals;
- Costs are increasing and our capital budgets are decreasing;
- Costs of both energy and personnel are increasing;
- Loss of experienced employees;
- Our corporate SG&A goals, as well as those of my customer, have to be met; and
- Overseas competition.
These themes led to value-proposition statements that began to resonate with applicators of water-based UV-curable polyurethanes, especially in the joinery and cabinetry market space such as: “manufacturers of joinery and cabinetry are seeking improvements in factory efficiency” and “manufacturers want the ability to expand production on shorter production lines with less rework damage due to the coatings with slow water-releasing properties.”
Table 1 illustrates how, for the manufacturer of coatings raw materials, improvements in certain coating attributes and physical properties lead to efficiencies that can be realized by the end user.

By designing UV-curable PUDs with certain attributes as listed in Table 1, end-use manufacturers will be able to address needs they have in improving plant efficiencies. This will allow them to be more competitive, and potentially allow them to expand current production.
Looking for a reprint of this article?
From high-res PDFs to custom plaques, order your copy today!
Experimental Results and Discussion
UV-Curable Polyurethane Dispersions History
In the 1990s, the commercial uses of anionic polyurethane dispersions containing acrylate groups attached to the polymer began to be used in industrial applications.1 Many of these applications were in packaging, inks, and wood coatings. Figure 1 shows a generic structure of a UV-curable PUD, demonstrating how these coating raw materials are designed.
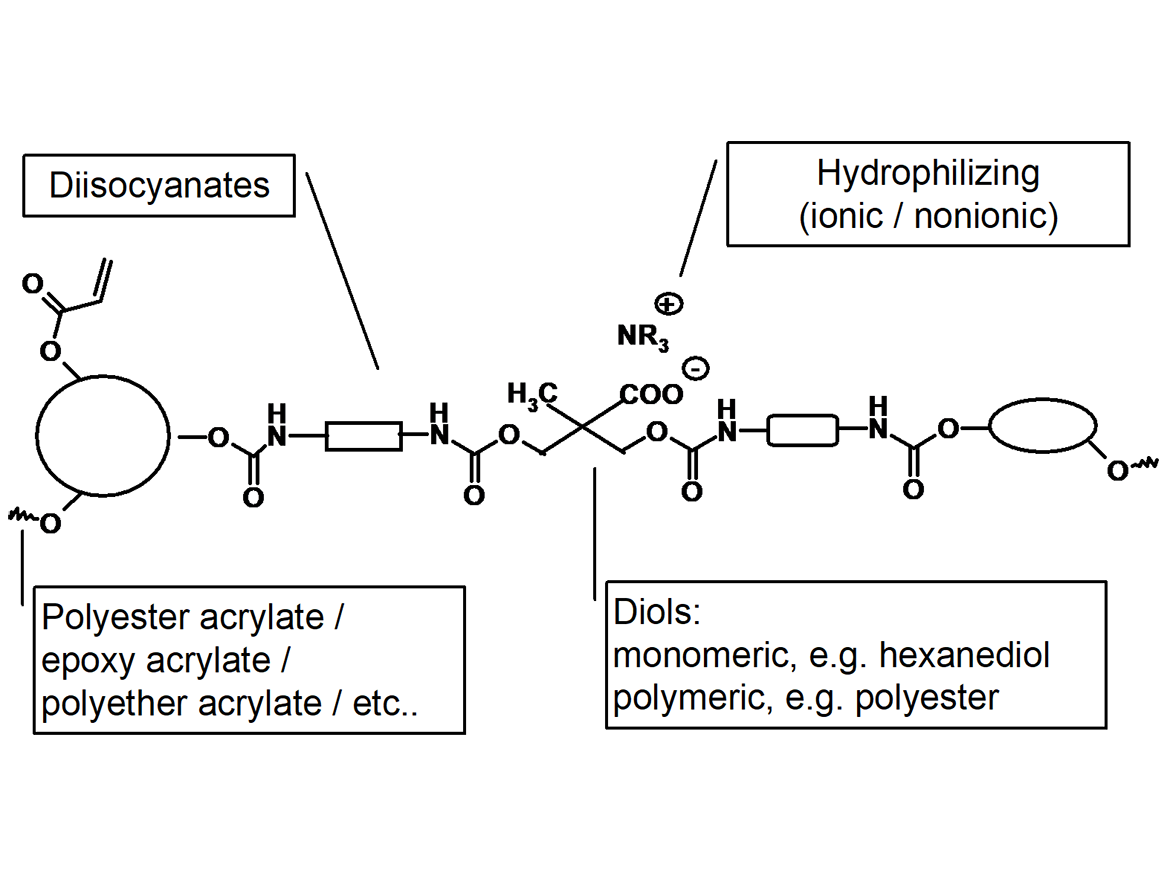
As shown in Figure 1, UV-curable polyurethane dispersions (UV-curable PUDs), are made up of the typical components used to make polyurethane dispersions. Aliphatic diisocyanates are reacted with the typical esters, diols, hydrophilization groups, and chain extenders used to make polyurethane dispersions.2 The difference is the addition of an acrylate functional ester, epoxy, or ethers incorporated into the pre-polymer step while making the dispersion. Choice of materials used as building blocks, as well as polymer architecture and processing, dictate a PUD’s performance and drying characteristics. These choices in raw materials and processing will lead to UV-curable PUDs that can be non-film forming, as well as those that are film forming.3 The film forming, or drying types, are the subject of this article.
Film forming, or drying as it is often called, will yield coalesced films that are dry to the touch before UV curing. Because applicators wish to limit airborne contamination of the coating due to particulates, as well as the need for speed in their production process, these are often dried in ovens as part of a continuous process prior to UV curing. Figure 2 shows the typical drying and curing process of a UV-curable PUD.
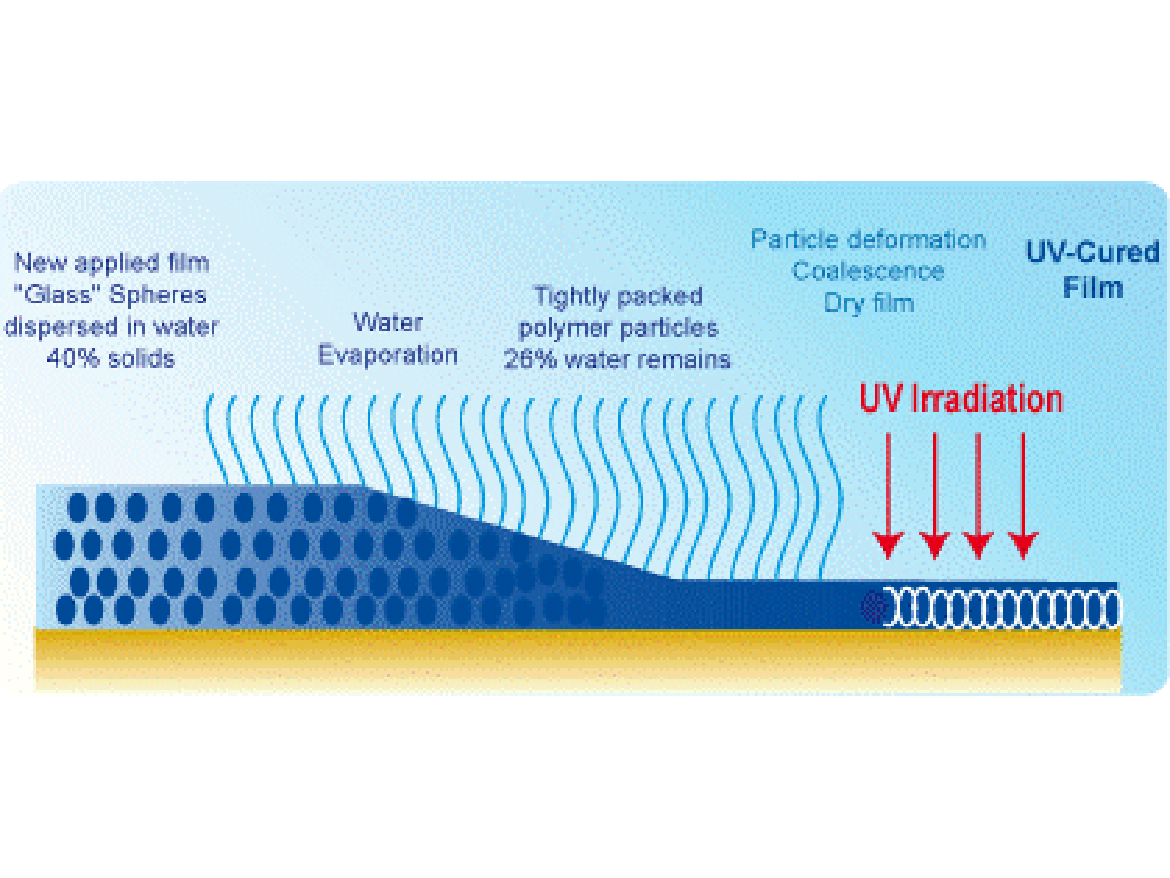
The application method used is typically spray. However, knife over roll and even flood coat have been used. Once applied, the coating will usually go through a four-step process before it is handled again.
- Flash: This can be done at room or elevated temperatures for several seconds to a couple of minutes.
- Oven dry: This is where the water and co-solvents are driven out of the coating. This step is critical and usually consumes the most time in a process. This step is usually at >140 °F and lasts for up to 8 minutes. Multi-zoned drying ovens may also be utilized.
- IR lamp and air movement: Installation of IR lamps and air movement fans will accelerate the water flash even faster.
- UV cure.
- Cool: Once cured, the coating will need to cure for some amount of time to achieve blocking resistance. This step may take as long as 10 minutes before blocking resistance is achieved
Experimental
This study compared two UV-curable PUDs (WB UV), currently used in the cabinet and joinery market, to our new development, PUD # 65215A. In this study we compare Standard #1 and Standard #2 to PUD #65215A in drying, blocking, and chemical resistance. We also evaluate pH stability and viscosity stability, which can be critical when considering reuse of overspray and shelf life. Shown below in Table 2 are the physical properties of each of the resins used in this study. All three systems were formulated to similar photoinitiator level, VOCs, and solids level. All three resins were formulated with 3% co-solvent.
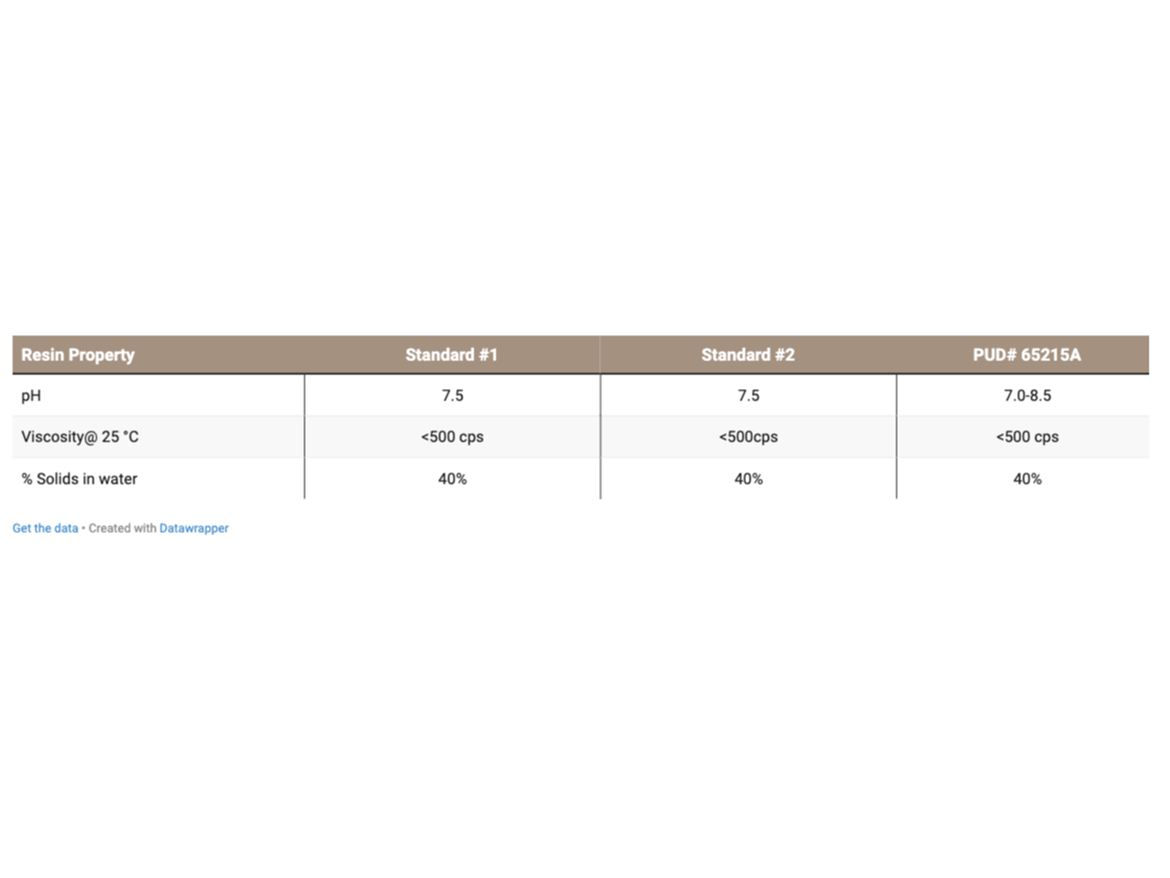
We were told in our interviews that most WB-UV coatings in the joinery and cabinetry markets dry on a production line, which takes between 5-8 minutes before UV cure. By contrast, a solvent-based UV (SB-UV) line dries in 3-5 minutes. In addition, for this market, coatings are typically applied 4-5 mils wet. A major drawback for waterborne UV-curable coatings when comparing to UV-curable solvent-based alternatives is the time it takes to flash water on a production line.4 Film defects such as white spotting will occur if water has not been properly flashed from the coating before UV cure. This can also occur if the wet film thickness is too high. These white spots are created when water becomes trapped inside the film during UV cure.5
For this study we chose a curing schedule similar to one that would be utilized on a UV-curable solvent-based line. Figure 3 shows our application, drying, curing, and packaging schedule used for our study. This drying schedule represents between a 50% to 60% improvement in overall line speed over the current market standard in joinery and cabinetry applications.

Below are the application and curing conditions we used for our study:
- Spray application over maple veneer with a black basecoat.
- 30-second room temperature flash.
- 140 °F drying oven for 2.5 minutes (convection oven).
- UV cure – intensity about 800 mJ/cm2.
- Clear coatings were cured using a Hg lamp.
- Pigmented coatings were cured using a combination Hg/Ga lamp.
- 1-minute cool down before stacking.
For our study we also sprayed three different wet film thicknesses to see if other advantages such as fewer coats would also be realized. 4 mils wet is the typical for WB UV. For this study we also included 6 and 8 mils wet coating applications.
Curing Results
Standard #1, a high-gloss clear coating, results are shown in Figure 4. The WB UV clear coating was applied to medium-dense fiberboard (MDF) previously coated with a black basecoat and cured according to the schedule shown in Figure 3. At 4 mils wet the coating passes. However, at 6 and 8 mils wet application the coating cracked, and 8 mils was easily removed due to poor water release before UV curing.
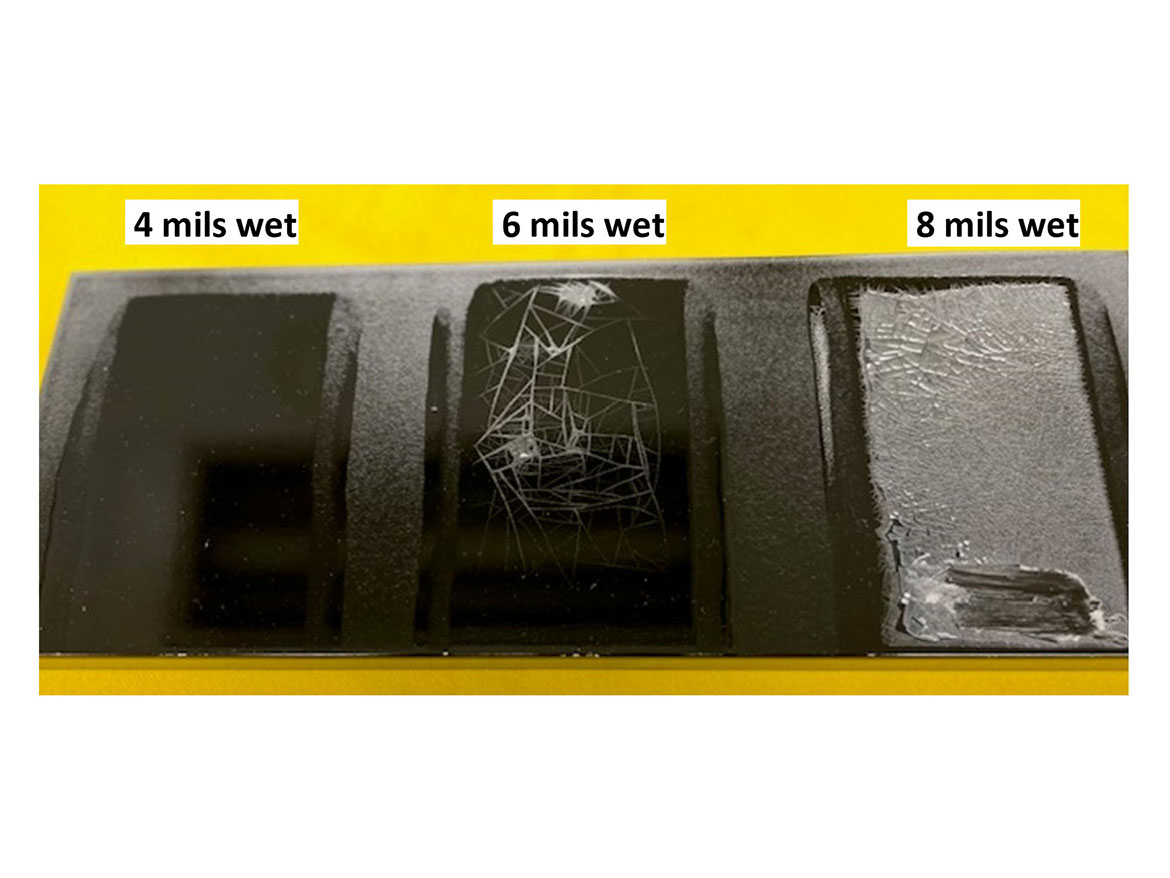
A similar result is also seen in Standard #2, shown in Figure 5.

Shown in Figure 6, using the same curing schedule as in Figure 3, PUD #65215A demonstrated tremendous improvement in water release/drying. At 8 mils wet film thickness, slight cracking was observed on the lower edge of the sample.
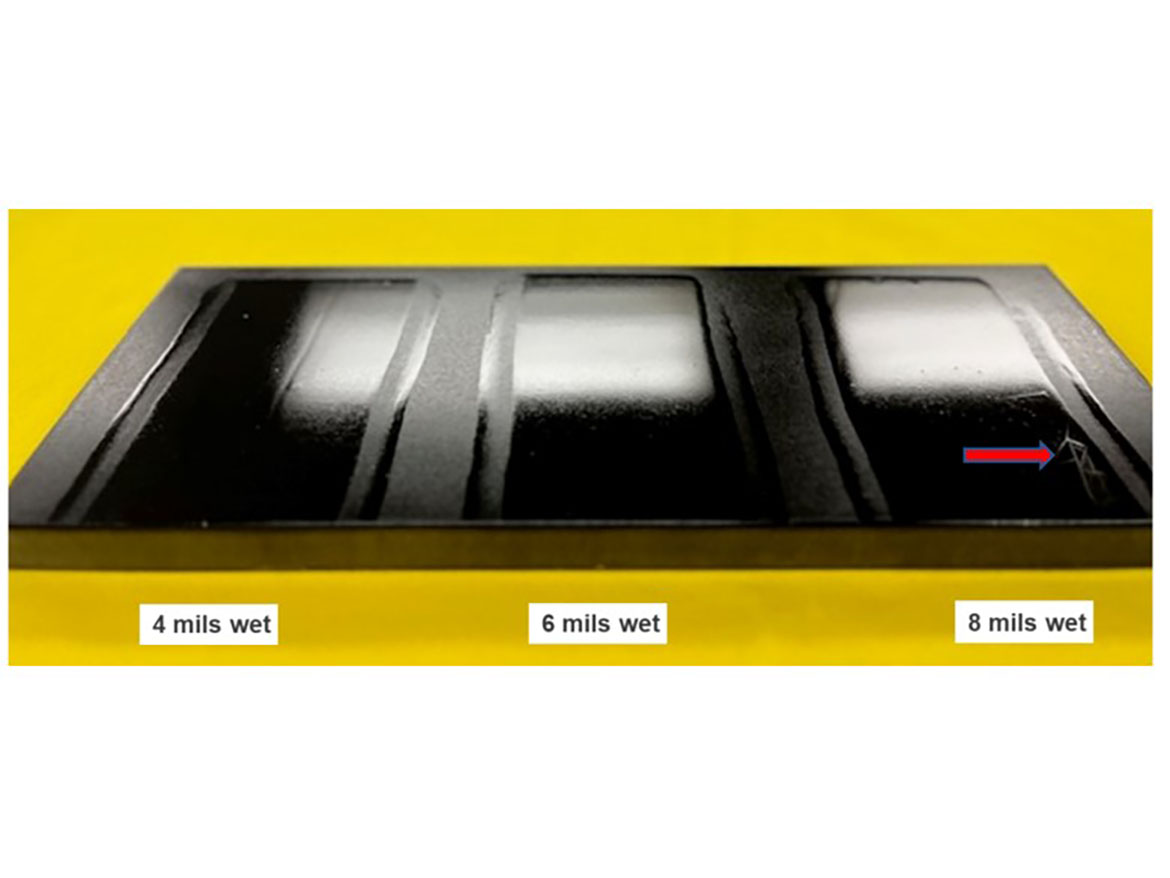
Additional testing of PUD# 65215A in a low-gloss clear coating and pigmented coating over the same MDF with a black basecoat was evaluated to evaluate water-release characteristics in other typical coating formulations. As shown in Figure 7, the low-gloss formulation at 5 and 7 mils wet application released the water and formed a good film. However, at 10 mils wet, it was too thick to release the water under the drying and curing schedule in Figure 3.

In a white pigmented formula, PUD #65215A performed well in the same drying and curing schedule described in Figure 3, except when applied at 8 wet mils. As shown in Figure 8, the film cracks at 8 mils due to poor water release. Overall in clear, low-gloss, and pigmented formulations, PUD# 65215A performed well in film formations and drying when applied up to 7 mils wet and cured at the accelerated drying and curing schedule described in Figure 3.
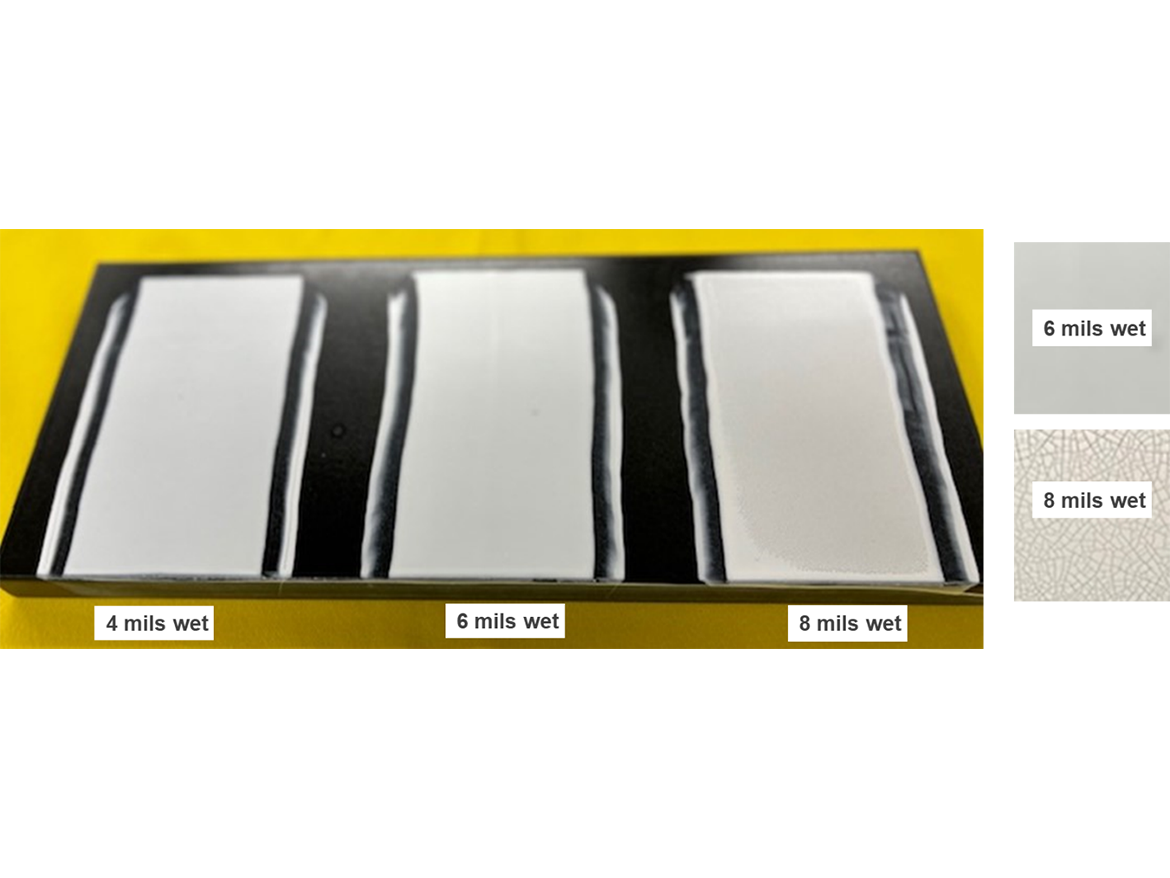
Blocking Results
Blocking resistance is a coating’s ability to not stick to another coated article when stacked. In manufacturing this is often a bottleneck if it takes time for a cured coating to achieve block resistance. For this study, pigmented formulations of Standard #1 and PUD #65215A were applied to glass at 5 wet mils using a drawdown bar. These were each cured according to the curing schedule in Figure 3. Two coated glass panels were cured at the same time – 4 minutes after cure the panels were clamped together, as shown in Figure 9. They remained clamped together at room temperature for 24 hours. If the panels were easily separated without imprint or damage to the coated panels then the test was considered a pass.
Figure 10 illustrates the improved blocking resistance of PUD# 65215A. Although both Standard #1 and PUD #65215A achieved full cure in the previous test, only PUD #65215A demonstrated enough water release and cure to achieve blocking resistance.

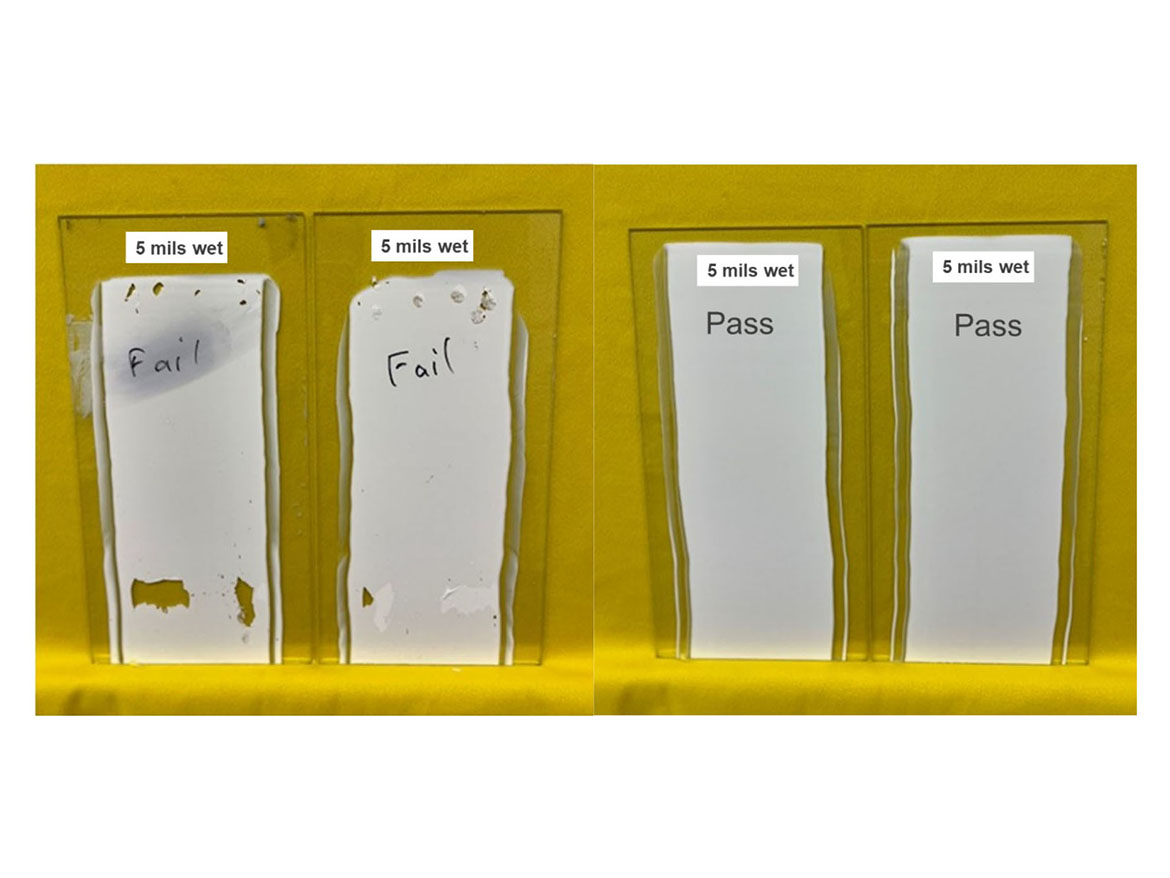
Acrylic Blending Results
Coating manufacturers often blend WB UV-curable resins with acrylics to lower cost. For our study we also looked at blending PUD#65215A with NeoCryl® XK-12, a water-based acrylic, often used as a blending partner for UV-curable water-based PUDs in the joinery and cabinetry market. For this market, KCMA stain testing is considered the standard. Depending on the end-use application, some chemicals will become more important than others for the manufacturer of the coated article. A rating of 5 is the best and a rating of 1 is the worst.
As shown in Table 3, PUD #65215A performs exceptionally well in KCMA stain testing as a high-gloss clear, low-gloss clear, and as a pigmented coating. Even when blended 1:1 with an acrylic, the KCMA stain testing is not drastically affected. Even in staining with agents such as mustard, the coating recovered to an acceptable level after 24 hours.

In addition to KCMA stain testing, manufacturers will also test for cure immediately after UV curing off the line. Often the effects of acrylic blending will be noticed immediately off the curing line in this test. The expectation is to not to have coating breakthrough after 20 isopropyl alcohol double rubs (20 IPA dr). Samples are tested 1 minute after UV cure. In our testing we saw that a 1:1 blend of PUD# 65215A with an acrylic did not pass this test. However, we did see that PUD #65215A could be blended with 25% NeoCryl XK-12 acrylic and still pass the 20 IPA dr test (NeoCryl is a registered trademark of the Covestro group).
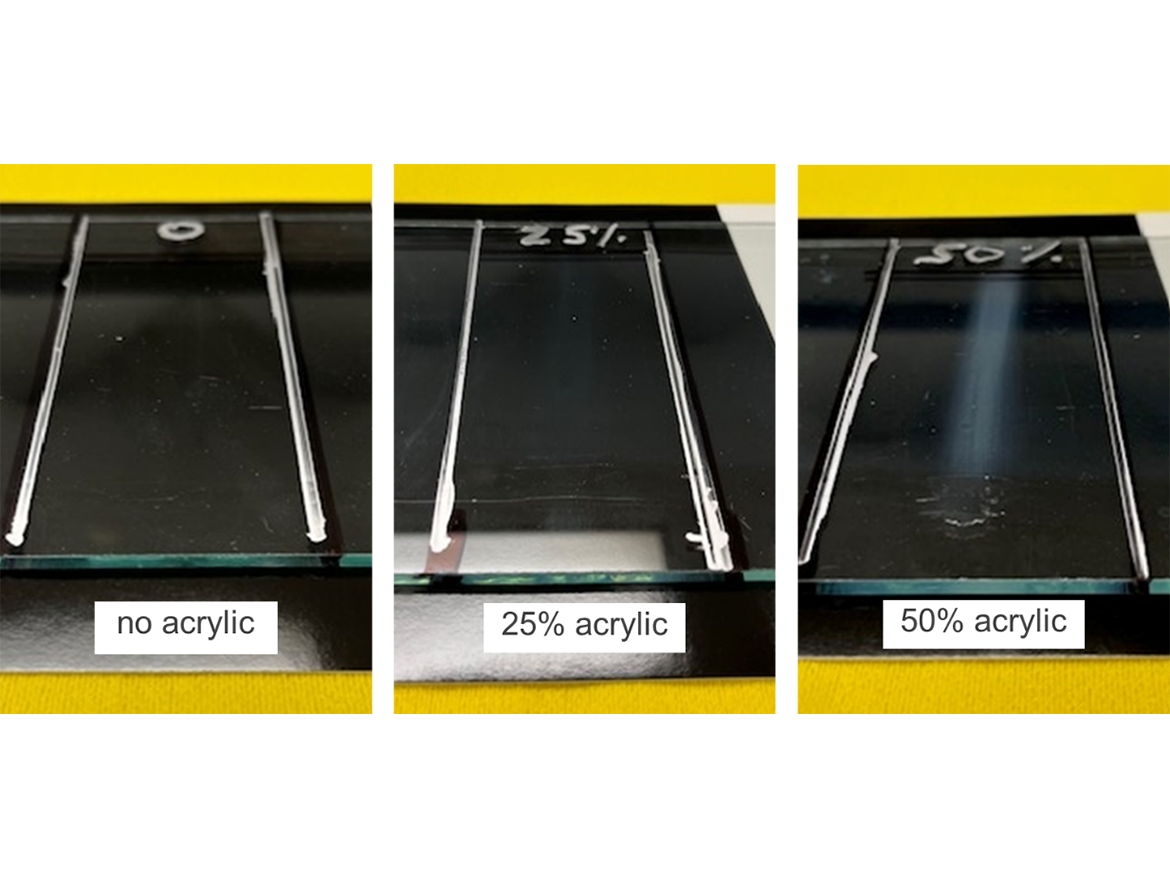
Resin Stability
The stability of PUD #65215A was also tested. A formulation is considered shelf stable if after 4 weeks at 40 °C, the pH does not drop below 7 and the viscosity remains stable when compared to the initial. For our testing we decided to subject the samples to the harsher conditions of up to 6 weeks at 50 °C. At these conditions the Standard #1 and #2 were not stable.
For our testing we looked at the high-gloss clear, low-gloss clear, as well as the low-gloss pigmented formulations used in this study. As shown in Figure 12, the pH stability of all three formulations remained stable and above the 7.0 pH threshold. Figure 13 illustrates the minimal viscosity change after 6 weeks at 50 °C.


Another test demonstrating stability performance of PUD #65215A was to again test the KCMA stain resistance of a coating formulation that has been aged for 6 weeks at 50 °C, and comparing that to its initial KCMA stain resistance. Coatings that do not exhibit good stability will see drops in staining performance. As shown in Figure 14, PUD# 65215A maintained the same level of performance as it did in the initial chemical/stain resistance testing of the pigmented coating shown in Table 3.
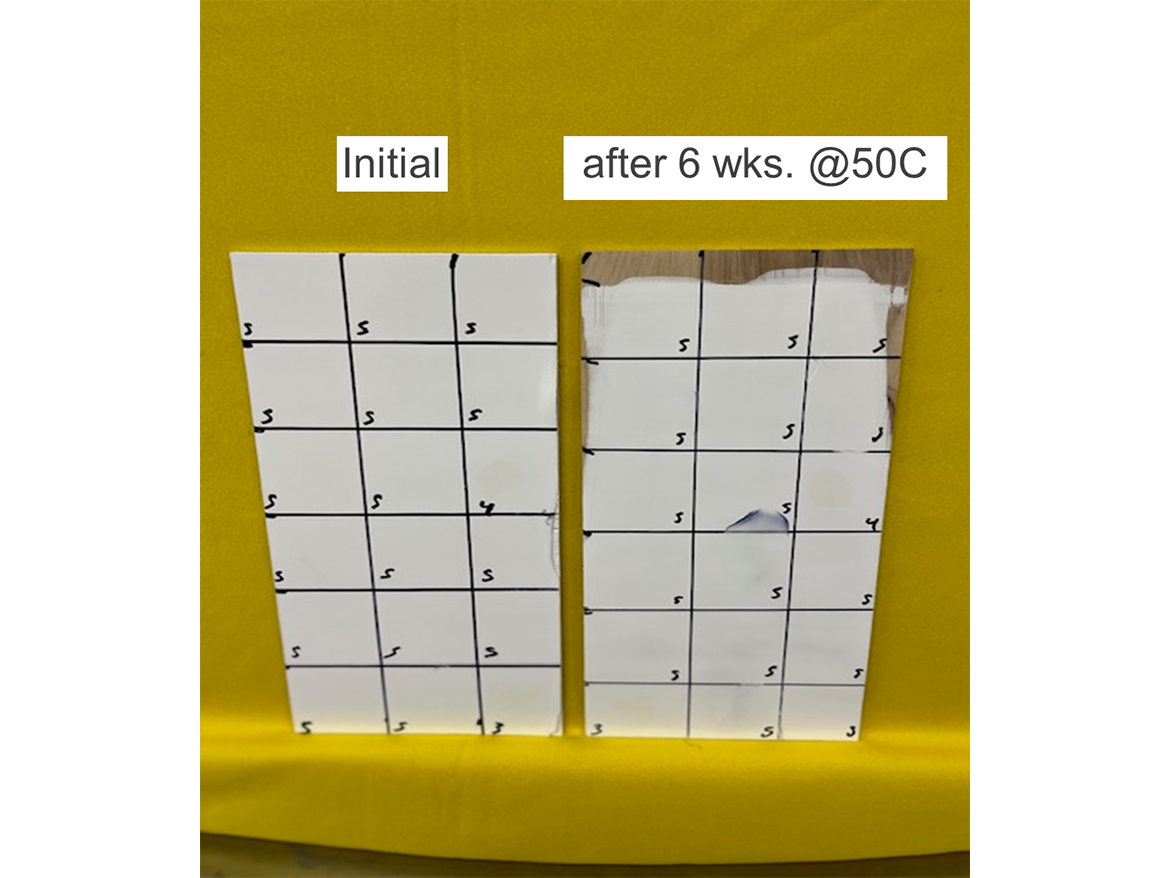
Conclusions
For applicators of UV-curable water-based coatings, PUD #65215A will enable them to meet the current performance standards in the joinery, wood and cabinet markets, and in addition, will enable the coating process to see line speed improvements to greater than 50-60% over current standard UV-curable water-based coatings. For the applicator this may mean:
- Faster production;
- Increased film thickness reduces the need for additional coats;
- Shorter drying lines;
- Energy saving due to reduced drying needs;
- Less scrap because of fast blocking resistance;
- Reduced coating waste due to resin stability.
With VOCs less than 100 g/L, manufacturers are also more able to meet their VOC targets. For manufacturers who may be having expansion worries because of permit issues, the fast-water-release PUD #65215A will enable them to more easily meet their regulatory obligations without performance sacrifices.
In the beginning of this article we cited from our interviews that applicators of solvent-based UV-curable materials would typically dry and cure coatings in a process that took between 3-5 minutes. We have demonstrated in this study that according to the process shown in Figure 3, PUD #65215A will cure up to 7 mils wet film thicknesses in 4 minutes with an oven temperature of 140 °C. This is well within the window of most solvent-based UV-curable coatings. PUD #65215A could potentially enable current applicators of the solvent-based UV-curable materials to switch to a water-based UV-curable material with little change to their coating line.
For manufacturers considering production expansion, coatings based on PUD #65215A will enable them to:
- Save money through the use of a shorter water-based coating line;
- Have a smaller coating line footprint in the facility;
- Have a reduced impact on current VOC permit;
- Realize energy savings due to reduced drying needs.
In conclusion, PUD #65215A will help to improve the manufacture efficiency of UV-curable coatings lines through high-physical-property performance and fast water releasing characteristics of the resin when dried at 140 °C.
References
1 Meier-Westhues; Danielmeier; Kruppa; Squiller. Polyurethane Coatings Adhesives and Sealants. Vincentz Network 2019, 2nd Revised Edition, 151.
2 EP-B 753 351 Bayer MaterialScience AG.
3 Meier-Westhues; Danielmeier; Kruppa; Squiller. Polyurethane Coatings Adhesives and Sealants. Vincentz Network 2019, 2nd Revised Edition, 131.
4 Wade, R. Wood Furniture Coatings Market and Technology Options. Bayer Material Science, BIFMA Conference, 2010.
5 Van Iseghem, L.C. Wood Finishing with UV-Curable Coatings. RadTech Report, May/June 2006 Issue, 35.
This paper was presented at the 2024 Waterborne Symposium in New Orleans.