New Organic Rheology Additive Technologies

PashaIgnatov, Creatas Video+ / Getty Images Plus, via Getty Images.
Conventional first- and second-generation organic rheology additives are finely micronized powders based on blends of castor oil derivatives or fatty acid amides. They are used as thixotropic agents both in aliphatic and aromatic solventborne formulations as well as in 100%-solid formulations.
Rheologically effective structures can only be formed if sufficiently high-shear forces and temperatures are used in the dispersion process. Some of these additives require precise temperature control, as undesirable effects such as "seeding" may occur if an upper-temperature threshold is exceeded during processing. Compared to castor oil derivatives, polyamide-based additives are more suitable for a wide range of polarities. However, due to their higher melting points, polyamides require higher activation temperatures.
In the search for environmentally friendly solutions, the demand for rheological additives that can already be activated at low process temperatures is increasing. Lower energy consumption and shorter production cycle times (shorter heating and cooling phases) are of interest both ecologically and economically.
Concerning rheological stabilization of coatings, there is also a trend to move away from hazardous raw materials, with preference given to the use of bio-based and sustainable chemistries, wherever possible.
New Types of Rheology Additives
Newly developed types of organic rheology additives differ from conventional rheology additives, on the one hand, with regard to their chemical composition, and on the other hand with regard to their particle shape and size distribution. These modern rheological additives were developed on the basis of specific blends of either polyamide waxes or so-called hybrid grades (which contain selected polyolefins). In particular, LUVOTIX® VP031, one such hybrid rheology additive, contains only ingredients that are FDA compliant.
Production of these additives in a controlled micronization process results in precisely defined particle shape and size distribution. This ensures easy dispersion of the powders and reliable activation, not only in formulations of low to medium polarity, yet also in systems of higher polarity. In the case of these new additive systems, the complete formation of rheological structures is achieved in the dispersion process after a short time, even at low process temperatures and under moderate shear forces without the need for temperature control (see Figure 1).
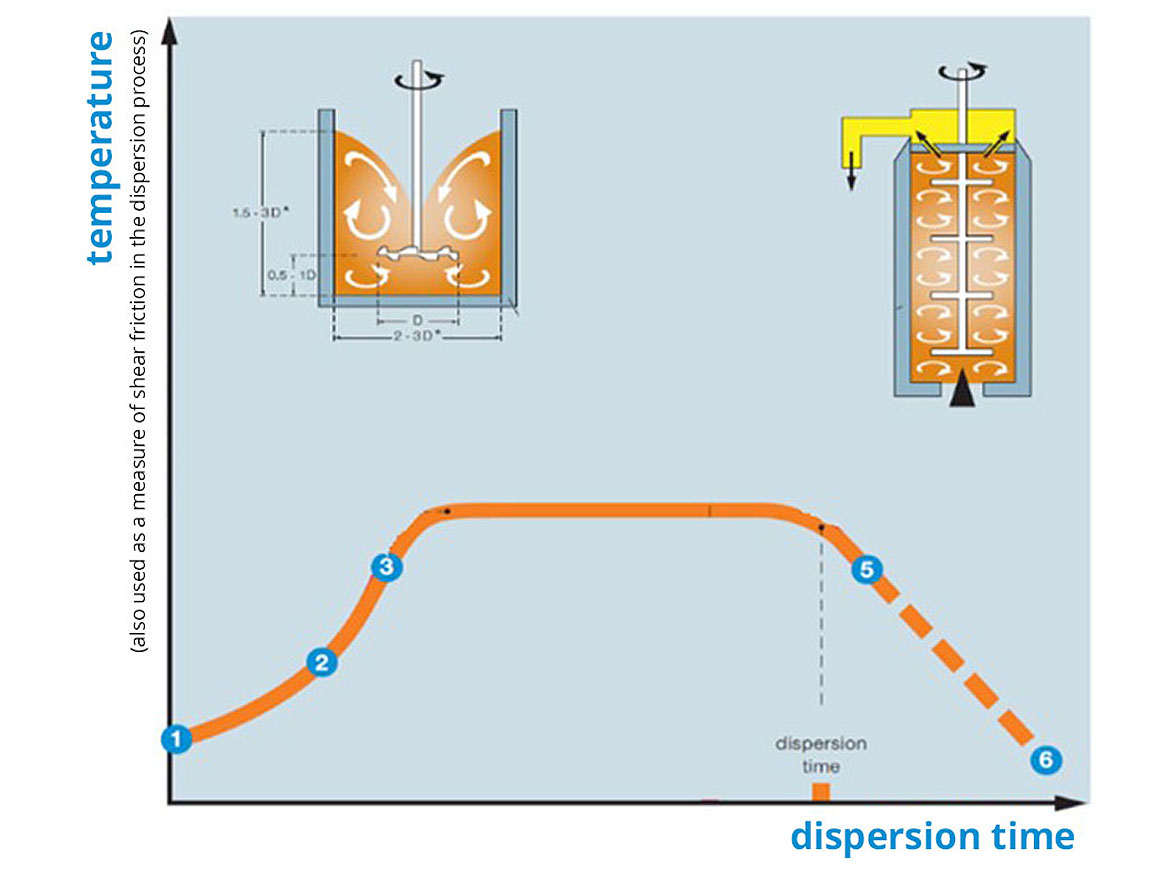
In the activated state, the additive molecules assemble fiber structures in the formulations via intermolecular forces (e.g. van-der-Waals, hydrogen bridges). The new additives discussed in this article develop structures that are stronger than those of the conventional polyamide additives. Figures 2a and 2b compare micrograph pictures of both types of additives in a solvent-free 2K epoxy test formulation (Formulation 2b, described later).
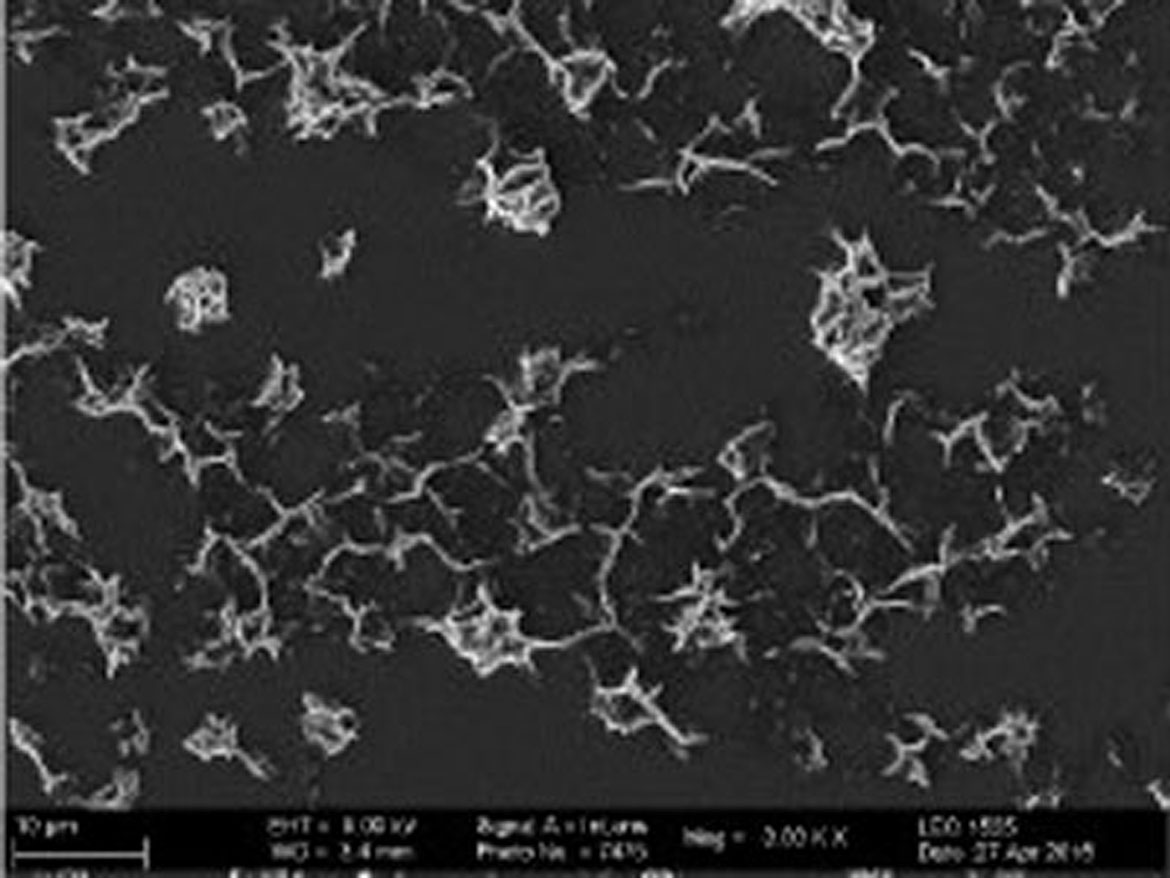
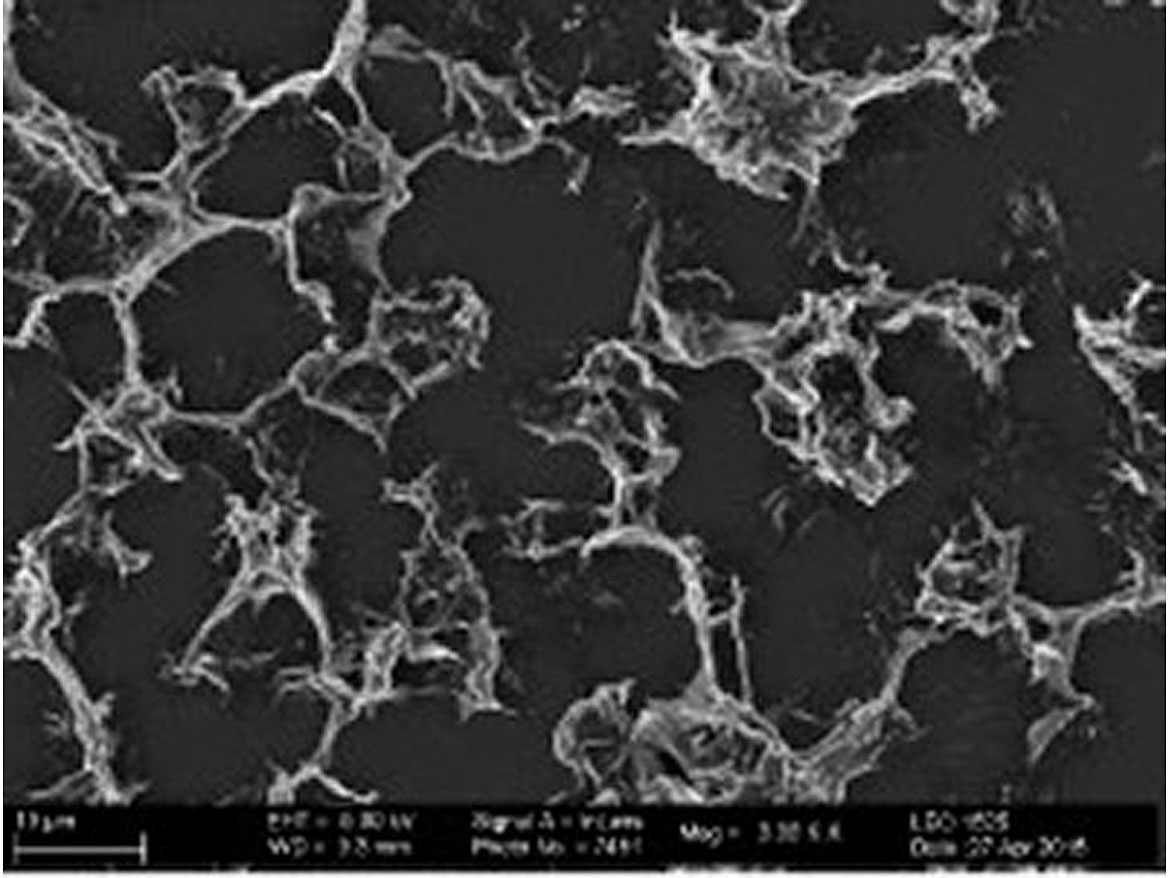
The new organic rheology additives were compared to several commercially available polyamides in various solventborne and solvent-free test formulations. Activation conditions such as time, shear intensity, and process temperature were varied in order to investigate the differences between the various rheology additives.
Samples were prepared in a laboratory dissolver. All rheological tests were performed at 23 °C using a controlled-stress rheometer (Anton Paar, MCR 301), 24 hours after sample preparation. Sag resistance was tested with an antisag meter. Properties of the dried films, such as gloss and pendulum hardness, were also tested and compared.
Test Formulation 1: Two-Component Polyester Formulation
Test formulation 1 (Table 1) is an air-drying, high-gloss, two-component (2K) white topcoat, based on Synthoester 1165 (Synthopol). The resin is a hydroxy-functional, weakly branched saturated polyester, supplied as a liquid 65% in a 1:1 mixture of MPA/xylene. Desmodur N75 (Covestro), an aliphatic polyisocyanate based on hexamethylene diisocyanate (HDI), supplied at 75% in a 1:1 mixture of MPA/xylene was used as hardener. Three rheology additives were tested, a classic commercial polyamide, new polyamide additive “AB”, and new hybrid additive “VP031”.

Considerably stronger rheological structures were obtained in the 2K polyester formulation at an activation temperature of 55 °C when using VP031 and AB in comparison to the conventional polyamide wax additive. This can be seen from the viscosity curves and in oscillatory tests (amplitude sweep, see Figure 3).
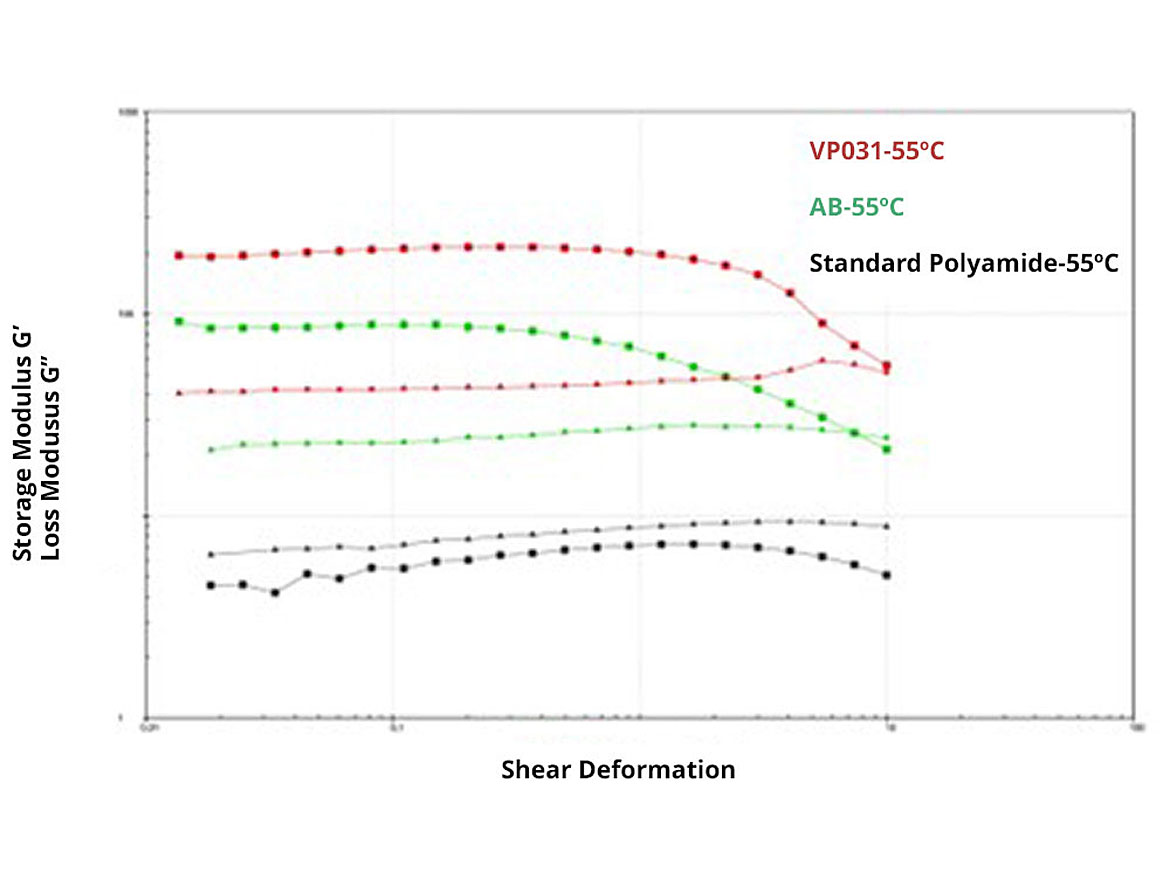
High plateau values of storage modulus G’ and loss modulus G’’ in the linear-viscoelastic range and G’>G’’ are typical for a strong viscoelastic gel structure in the formulations with VP031 and AB, respectively. On the other hand, the formulation containing the standard polyamide shows liquid-like behavior.
The stronger the network structure in the formulation, the higher its sag resistance. With VP031, gloss and pendulum hardness are only slightly lower compared to the standard polyamide additive, whereas with AB, gloss and pendulum hardness are significantly reduced (Table 2). Thus, in this test formulation, additive AB was a less-suitable additive.
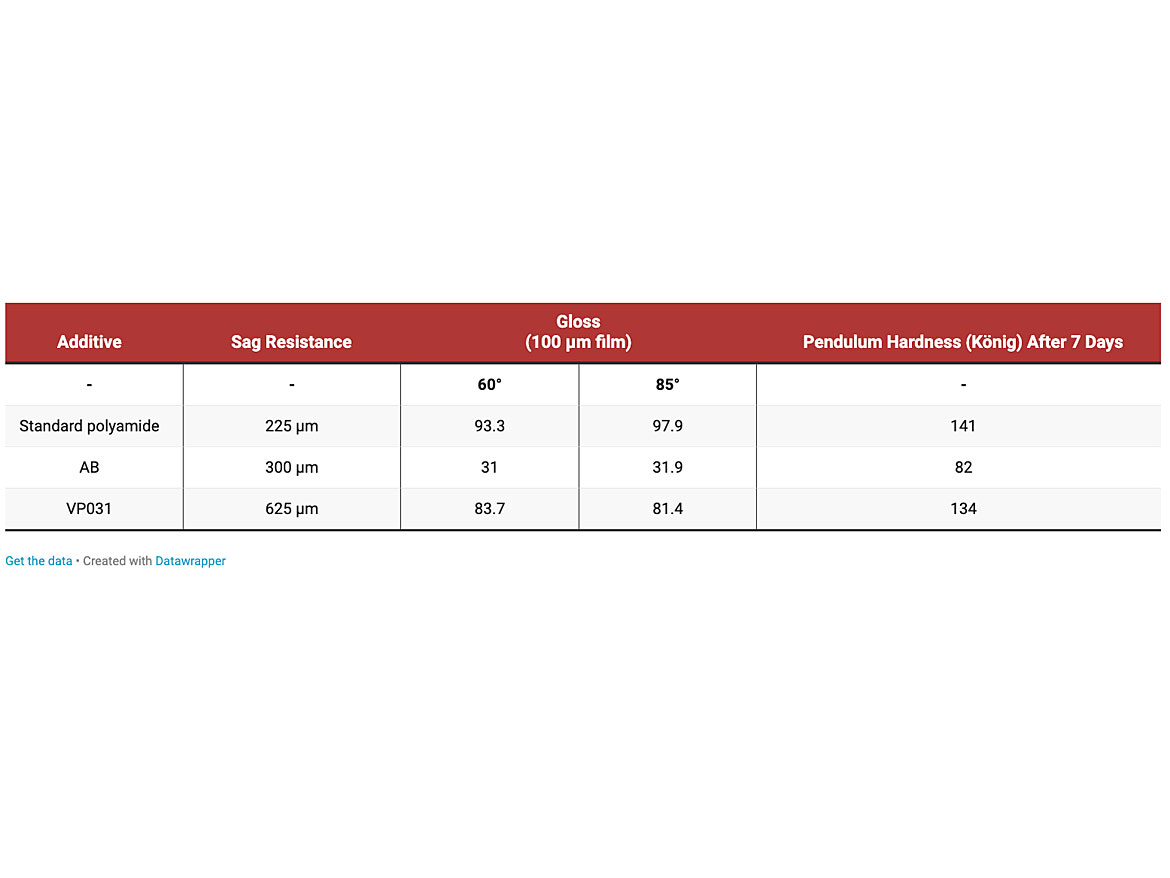
Test Formulation 2a: 2K Epoxy Formulation, Solventborne
The second test formulation (Table 3) is an anticorrosive primer based on epoxy resin. The epoxy resin is a low-viscosity BPA/F resin with a monofunctional reactive diluent, used in combination with a polyamidoamine curing agent.
In this formulation it is especially important to achieve a good sag resistance after spraying. Wet film thickness of at least 750 µm is required. Here, again, three rheology additives were tested, a classic commercial polyamide, new polyamide additive “AB” and new hybrid additive “VP031.”
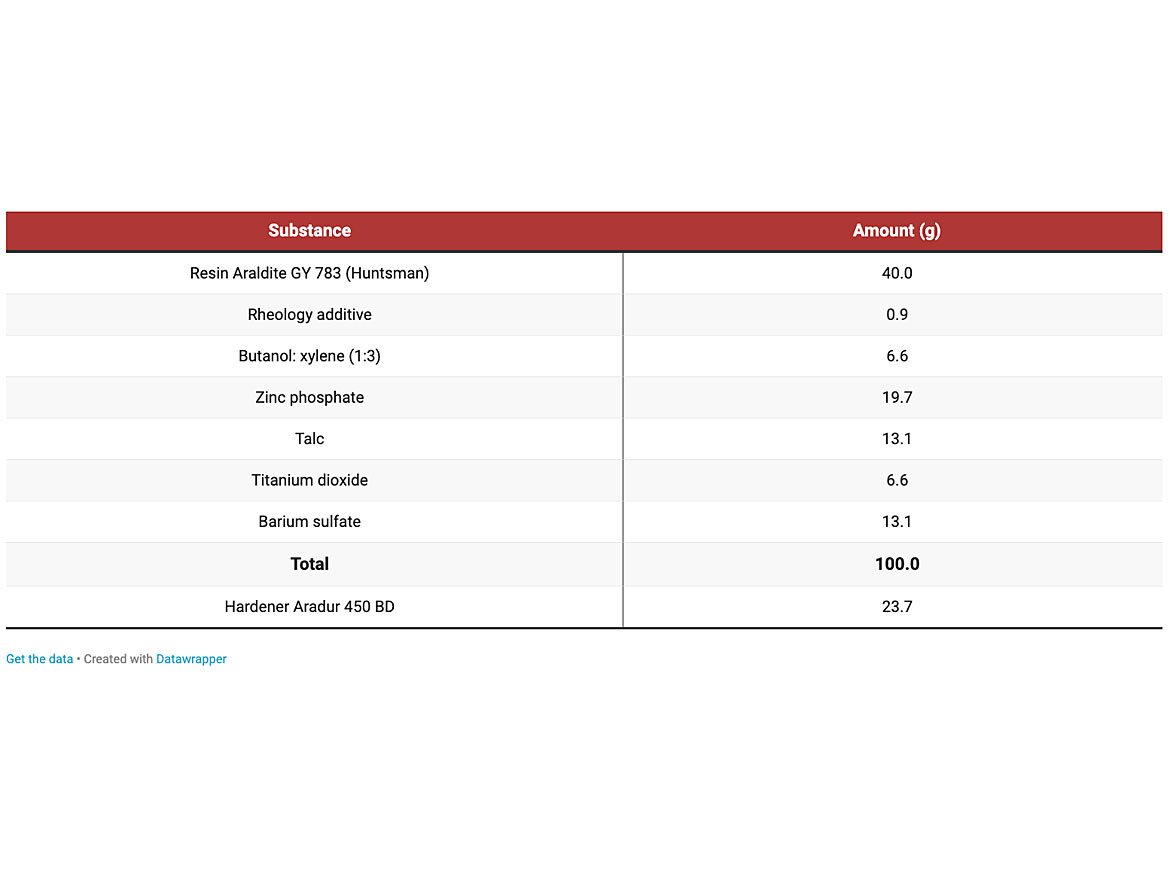
In this test formulation, both VP031 and AB were already fully activated at 45 °C, while this is not the case with the classic polyamide additive, which requires higher activation temperatures. While the viscosity curves of VP031 and AB are very similar (Figure 4a), differences are more clearly shown in the amplitude sweep (Figure 4b) where the strongest viscoelastic network structure is seen in the formulation with VP031.
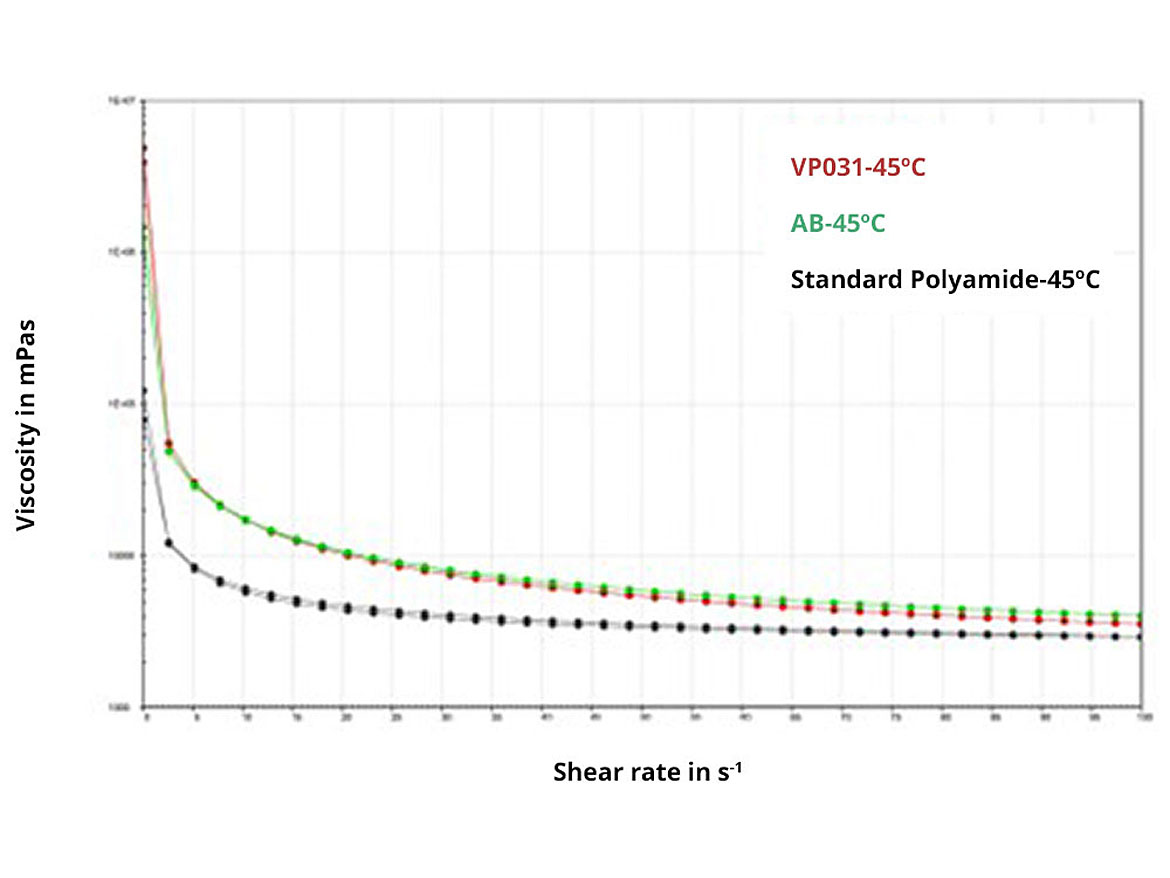

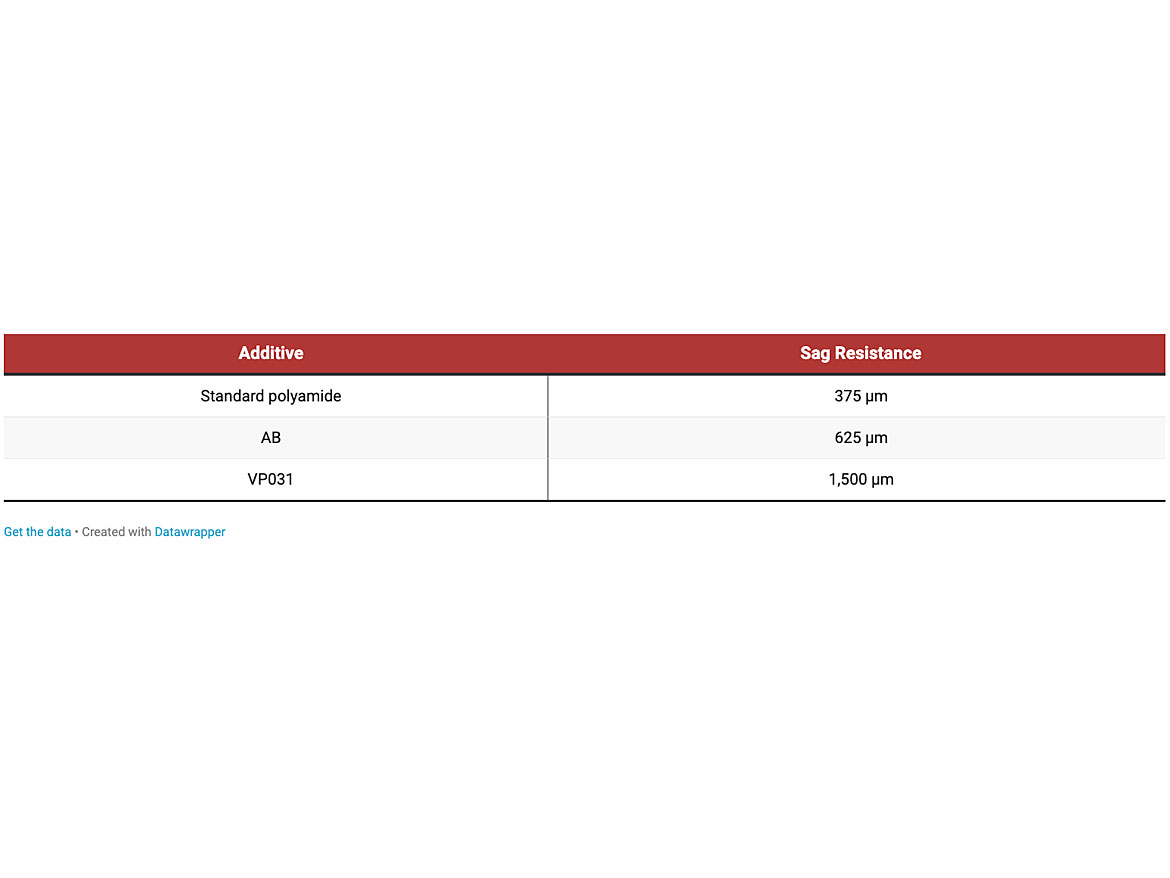
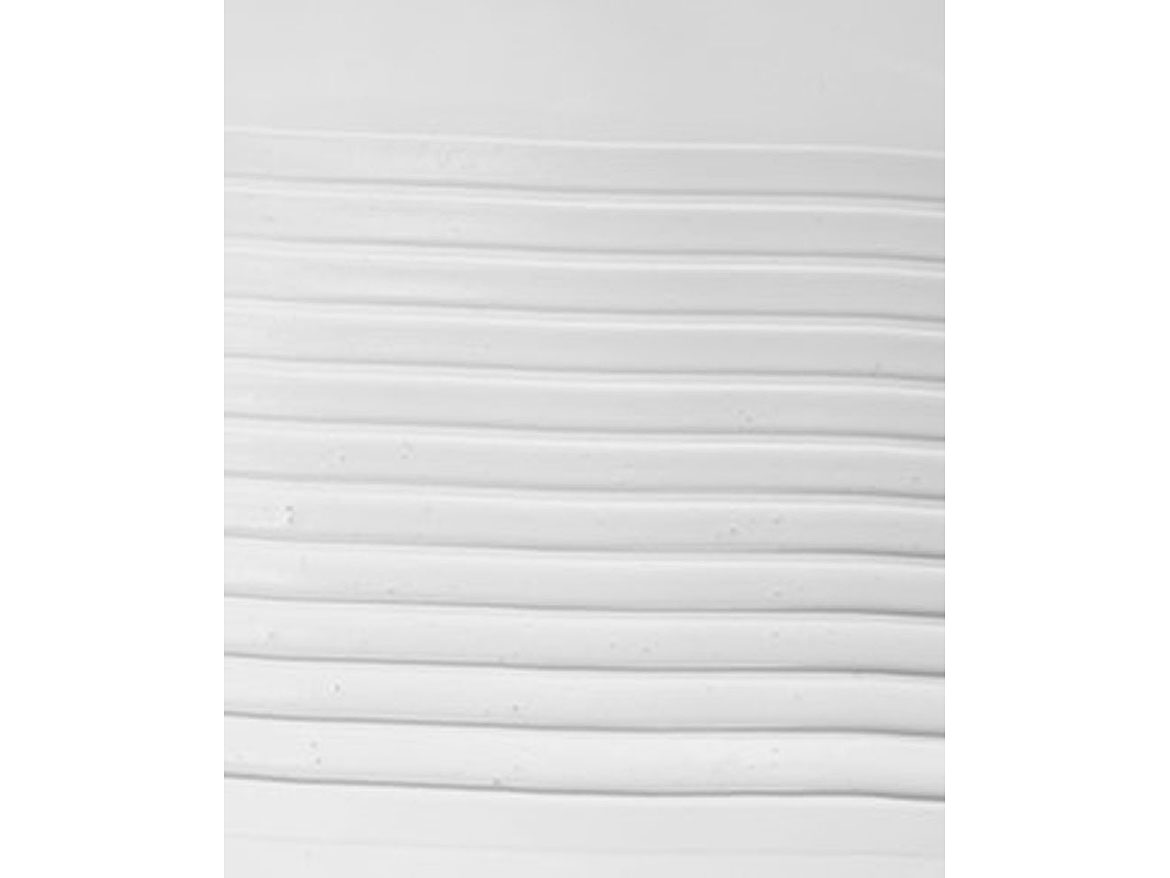

Test Formulation 2b: 2K Epoxy Formulation, Solvent-Free
In a solvent-free 2K epoxy primer formulation, the performance of the new rheology additives was also superior to that of conventional polyamide additives, as they show stronger structures and higher viscosities.
Application results from Test Formulation 2b are shown in Table 5 below. These results demonstrate that no significant influence on the pendulum hardness is caused by the rheology additives. A slight gloss reduction is observed with VP031, which might be caused by poorer surface leveling as viscosity of the sample is significantly higher.


Summary and Conclusions
Newly developed types of organic rheology additives are available for solvent-based and solvent-free coating formulations. These additives outperform the current standard type additives by showing good dispersibility and ease of activation, even at low process temperatures. The performance of this new class of additives is comparable or superior to that of polyamide-based additives. In addition, the hybrid-type additive LUVOTIX VP031 is FDA compliant.
Looking for a reprint of this article?
From high-res PDFs to custom plaques, order your copy today!