When Product Life Exceeds Coating Life
A Major Problem with Protective Coatings
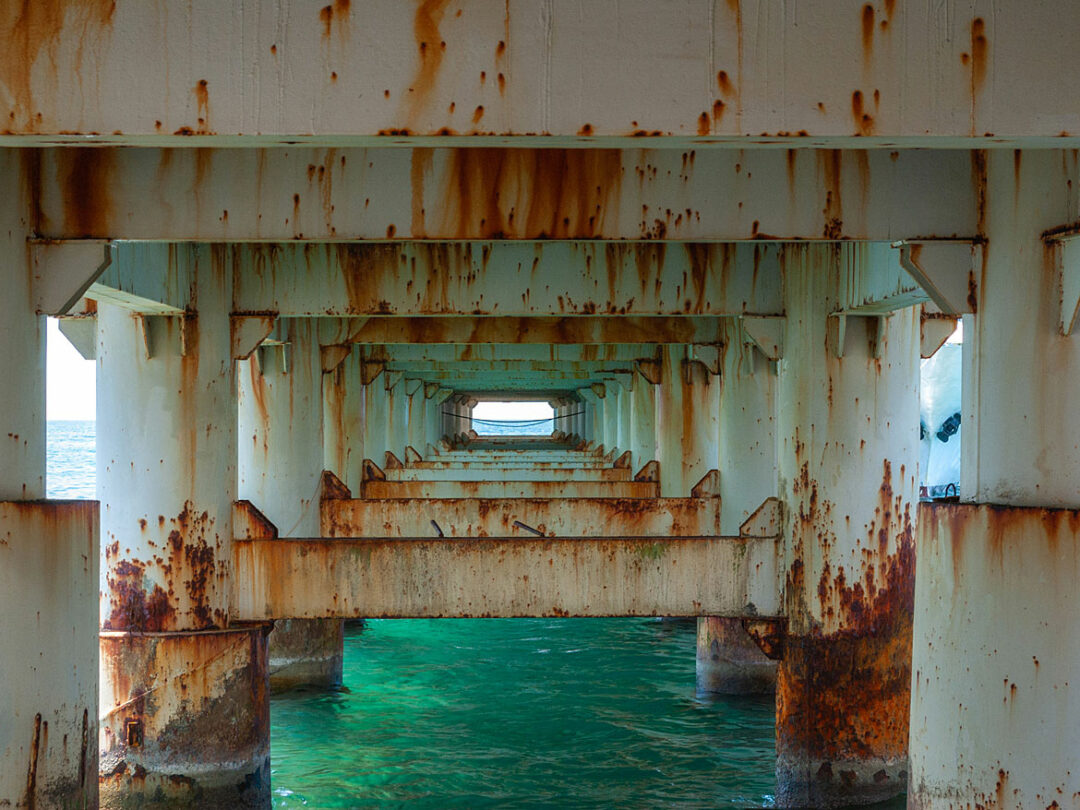
Evgeniy Kovalenko, iStock/Getty Images Plus, via Getty Images
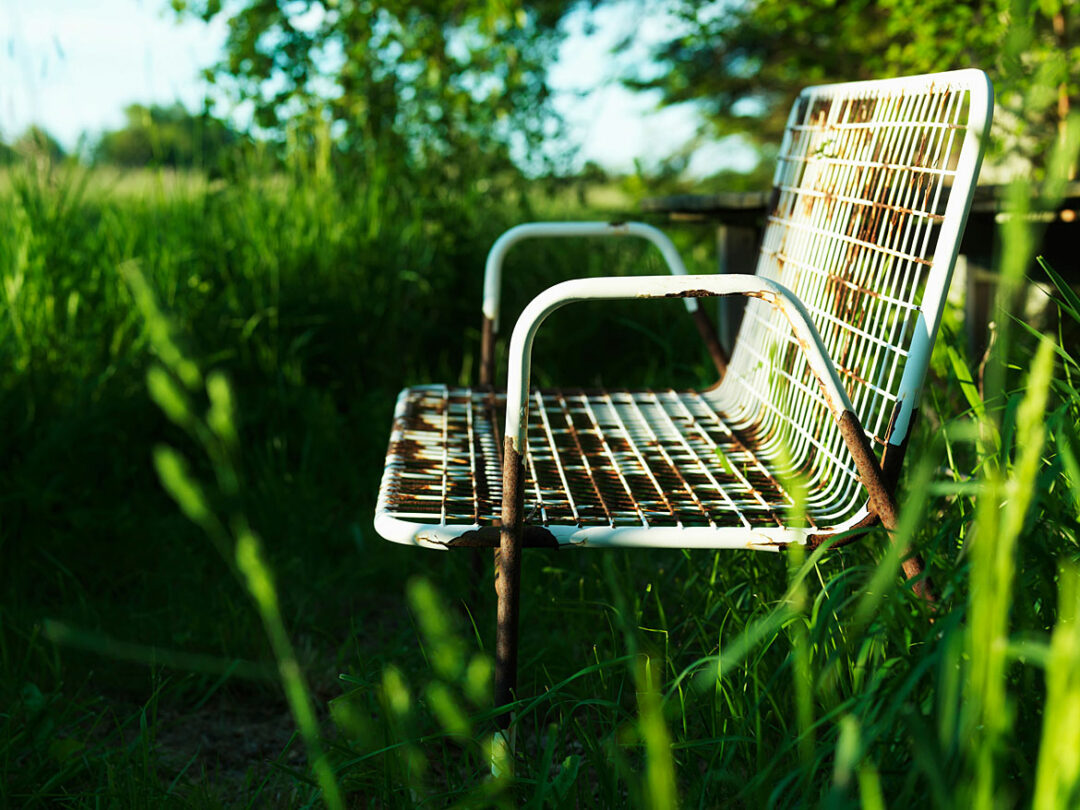
Henrik Weis, Image Source, via Getty Images
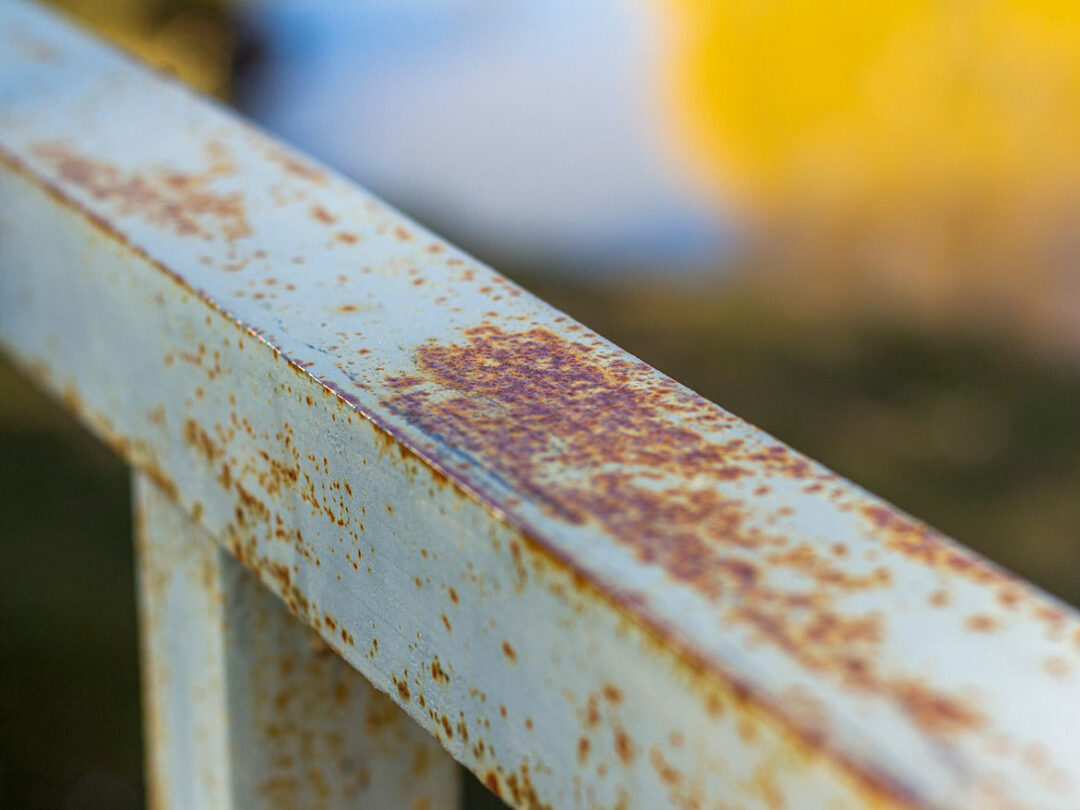
Nikolaeva Elena, iStock/Getty Images Plus, via Getty Images
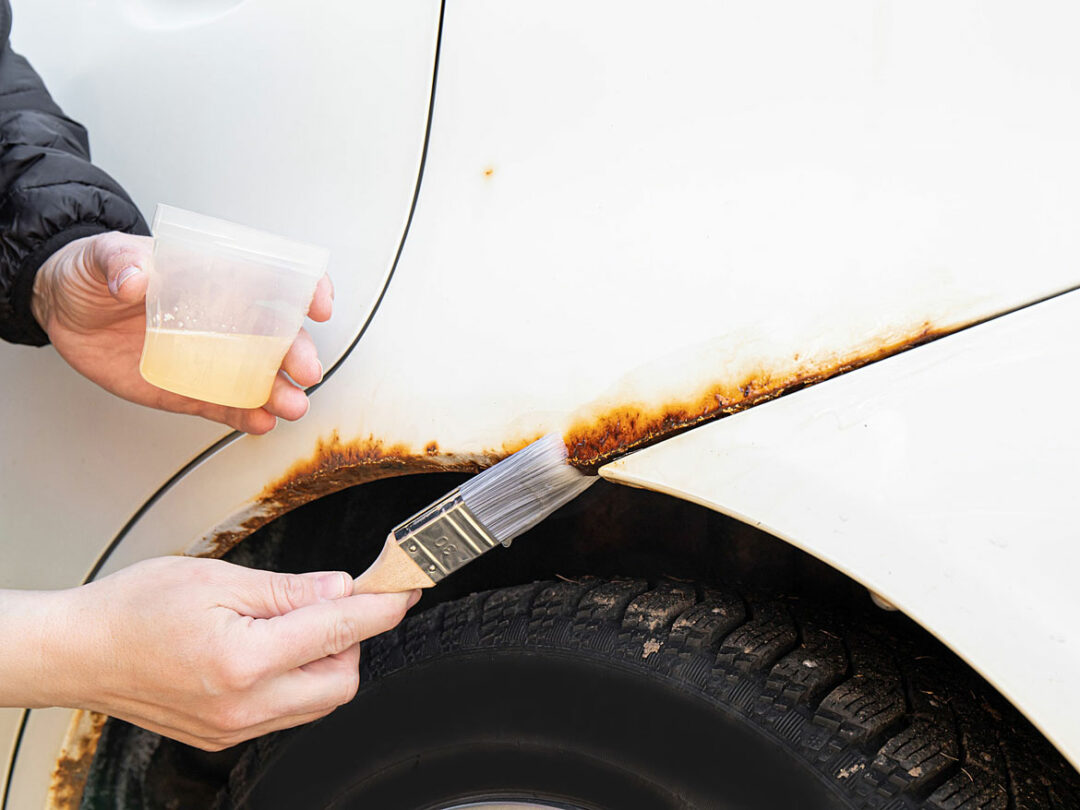
Helin Loik-Tomson, iStock/Getty Images Plus, via Getty Images




Published reports place the total cost of corrosion in the United States at $552 billion. Direct costs account for 50%, or $276 billion, which include corrosion-related repairs or replacements. Indirect costs account for the other 50%, and include loss of production, environmental damage, transportation disruptions, injuries, and fatalities.
The total cost of corrosion is placed at 6.2% of the Gross Domestic Product (GDP). The $552 billion is based on the 1997 GDP of $8.76 trillion. In 2010, the GDP was $14.7 trillion. 6% of $14.7 trillion equals $882 billion. This represents a 60% increase since 1997.
The economic failure in 2008 from the housing market produced a dramatic reduction in GDP growth. However, corrosion is not affected by negative changes in the GDP. Corrosion activity increases when the economy slows. Companies are less likely to budget funds for corrosion repairs when profits are significantly reduced. For this reason, the cost of corrosion is predicted to be higher than the stated $882 billion.
Planned maintenance extends coating life but its use is limited. This is due to the high cost, and complexity of the inspection and evaluation process of in-place coatings in need of repair, and the majority of the current coating formulations are not designed for extended maintenance support.
This article introduces the concept of Lifetime Coating Systems (LCS). LCS is a strategically engineered maintenance program designed to match coating life with asset life for products and structures with a design life of 25-100 years, or more. LCS uses a combination of modern maintenance principles: preventive, predictive, and reliability-centered maintenance (RCM) versus customary reactive maintenance.
Maintenance Classifications Defined
Reactive Maintenance
Assets are allowed to operate to failure before repairs are planned. The majority of maintenance recoating is performed using reactive maintenance.
Preventive Maintenance
Repairs or replacements are scheduled on a pre-determined time schedule. Work is based on manufacturers’ recommendations, operational histories, and performance estimates. A small percentage of recoating repairs are performed by preventive maintenance guidelines.
Predictive Maintenance
Repairs are based on current asset condition. Predictive maintenance relies on precise evaluation of component parts using specialized inspection devices and highly trained workers. Predictive maintenance plans can virtually eliminate unplanned breakdowns but inspection equipment can be expensive. Currently, no recoating operations are performed using predictive maintenance.
Reliability-Centered Maintenance (RCM) with Root-Cause Analysis
RCM considers the optimum maintenance strategy for an asset in its operating environment and is based on regular inspections to determine when an asset has reached a predetermined unacceptable level of performance. At this time, repairs or replacements are performed to prevent a more costly failure. Maintenance personnel then use root-cause analysis to identify excessive wear points and make changes to future maintenance operations through design changes or part modifications. No recoat repairs use RCM concepts currently.
A comparison of savings based on part or system replacements resulting from excessive corrosion damage:
- Reactive 0%;
- Preventive 25-35%;
- Predictive 45-55%;
- RCM and root-cause analysis 60-80%.
LCS — Component Parts
Surface Preparation
Surface preparation is the foundation for coating performance. LCS recommends the use of improved surface preparation standards to further clean and condition the metal substrate to reduce under-film corrosion activity. This will reduce premature coating failure due to corrosion activity at the metal/coating interface and provide a sound foundation for recoating operations later.
Permanent Primer Coats/Expendable Finish Coats
LCS is based on the application of permanent-foundation primer coats over-coated with expendable finish coats, whereas traditional maintenance focuses on the repair or replacement of the complete system. In principle, the bare metal substrate will never be entirely exposed to the environment after the initial application. The majority of coating damage produced by sunlight, weathering, abrasion, chemical, or biological attack will be absorbed by the finish coat, which can be repaired or replaced as needed.
Quality Control
One or more separate coats of the LCS system are formulated by black-light-activated fluorescence. Safe and simple black-light monitoring allows workers to easily locate areas of premature coating failure long before complete system failure occurs and irreversible corrosion damage begins. Black-light illumination produces an enhanced visual signature (EVS) that allows “real time” identification of coating defects even in low-light conditions or during production painting operations. Black-light non-destructive testing is the only quality control process that can match the speed of modern spray-painting operations where thousands of square feet are coated in a single shift. Black-light inspections can be performed as fast as a worker can move the black light, and as fast as the human eye can follow.
LCS — Maintenance Cleaning
Keeping the painting surface clean is an additional way to extend coating life. Today, waste products from industrial activity including carbon dioxide and chemical by-products including chlorides, sulfates, nitrates, and other forms of soluble salts can have a damaging effect on protective coatings even in low concentrations.
LCS recommends regular cleaning of corrosion-prone surfaces to remove visible dirt and grime, and non-visible contaminants, as well. For non-visible contaminants produced by atmospheric pollution and industrial activity, LCS recommends the use of amine-based detergents designed to solubilize salts for easy removal.
“Smart-Dirt” Cleaning
A major problem with industrial cleaning is the inability of workers to visually determine when a surface is truly clean. Smart dirt is a quality assurance process that uses special cleaning materials containing a fluorescent tracer. This improves the effectiveness of parts cleaning by reassuring complete coverage and saturation of a target surface by black-light verification. Cleaning performance is ensured by total lack of visible florescence. The purpose is to extend coating life by preventing the build-up of soils and industrial wastes.
Low-Pressure/Low-Impact (LPLM) Abrasive Cleaning
LPLM cleaning uses a combination of hard, dense minerals to remove aged or damaged coatings while leaving sound coatings intact. LPLM media can be recycled several times for additional savings including abrasive delivery and disposal costs. The purpose is to reduce energy and material waste by selective, abrasive-blast cleaning.
Thin Film Recoating
Thin film recoating when used in combination with low-pressure/low-impact abrasive cleaning maintains specified mil thickness, protects the integrity of the original application, and minimizes waste and environmental pollution. The purpose is to reduce costs by eliminating the need to over apply the coating to insure coverage.
Nanocoatings
A new generation of micro-thin exterior clear coats has been developed to improve the appearance and increase the durability of factory-applied coatings. These coatings are based on the nanoscience or the creation, organization of materials, devices, or systems at the nanolevel (one billionth of a meter).
Permanon
One new nanocoating from Germany, Permanon, uses silicium as its pigment base. Silicium is a component of glass and is the same material used to produce modern computer chips. Silicium, also known as silicon, is the second-most-abundant element on earth, after oxygen. Silicon is a metalloid, meaning it has properties of both metal and nonmetals but, should not be confused with silicone, which is a man-made sealant.The application of Permanon over factory-applied coatings produces properties similar to hardened glass. The surface is chemically inert, dirt and dust will not bond to treated surfaces, and are protected against water, acid rain, and other types of chemical pollution. Permanon produces a hydrophobic surface that repels moisture. Waterproofing a coated surface eliminates moisture from being absorbed into the coating and migrating to the underlying metal substrate. This aids in protecting the asset from coating failure and irreversible corrosion damage.
Surface modification at the microscopic level with silicium nanoparticles produces a coating that is smoother, easier to clean, and stays clean longer.
Permanon provides workers with a simple way to monitor performance by ASTM F-2202 water break testing. When water is sprayed on a surface, the formation of large droplets indicates that water-repelling properties have been created. The size and shape of the droplets indicate the level of water-proofing. This can be measured by contact angle.
Contact-Angle Measurement
Contact angle is measured by a straight line that begins at the base of the droplet and travels in a straight line along the outer surface to the break-off point. The higher the degree of incline of the water droplet; the higher the surface’s resistance to moisture.
LCS — Time Management
Corrosion develops over time. The shorter the time intervals between coating maintenance, the less likely corrosion will have to reach serious levels. Steel structures and manufactured products have a number of irregular surfaces, each with an individual rate for coating failure. LCS is designed to make maintenance manageable by performing simple repairs at the early stages of coating failure rather than waiting until corrosion reaches serious levels requiring a major investment in labor and resources. A large percentage of LCS operations involve cleaning, inspecting, and system evaluating in place of traditional recoating, resulting in higher productivity and waste reduction.
Estimates show that one hour of LCS maintenance can replace up to 50 hours of crisis painting involving the complete removal of aged, damaged coatings followed by total re-application. Smart dirt cleaning, followed by thin-film recoating protects the integrity of the original application, extending coating life. Thin-film recoating performed at the early stages of deterioration reduces the volume of recoating materials for life-service corrosion protection. An 80% reduction in material waste can be expected with LCS-maintenance programs. LCS is designed to reduce the amount of energy, labor, and materials required for complete life-corrosion protection.
LCS — Reliability and True Sustainability
The responsibility for extended corrosion prevention is divided between the corrosion engineer, the coating manufacturer, the applicator, and the asset owner. Each has an important role in the LCS-maintenance program.
- Engineer — studies the application and develops the appropriate LCS specification.
- Coating manufacturer — formulates the coating to meet the engineer’s guidelines.
- Applicator — applies new coating to meet LCS performance specifications.
- Owner — develops asset inventories, scheduling, and records all painting work.
LCS provides the opportunity for the private sector to be included in the corrosion-prevention equation. Safe and simple black-light inspections allow in-house personnel to monitor coating performance and thin-film repair allows effective corrosion prevention before irreversible corrosion damage begins. Only a small work force is necessary since failure locations are rare and random in a given time period.
LCS significantly reduces catastrophic coating failure and the need for crisis painting operations. Catastrophic coating failure may become an unacceptable economic event due the future certainty of rising energy costs.LCS is designed to ensure future generations inherit a corrosion prevention strategy that is self-sustaining and operational versus traditional coatings which will eventually fail and require serious repairs or eventual replacement.
LCS — Evolution
Beginning in the late 1800s, five major events changed the economic structure of the United States.
- The discovery of the Bessemer process for steel production.
- The use of electricity and the invention of the electric light bulb.
- The development of the internal combustion engine and personal automobile.
- The development of assembly line production by Ford Motor Company.
- The change to oil from coal and wood as the nation’s primary energy source.
The coating industry has evolved over the last 100 years to meet American industries’ demand for increased production to support the dynamic growth of the U.S. economy. During the twentieth century, a sizable amount of waste was acceptable, and sometimes necessary, as long as high production levels were maintained. This was a direct result of cheap oil, abundant natural resources, and the growing efficiency of U.S. manufacturing and construction.
LCS — Job Creation Potential
Today, the cost of corrosion in the United States exceeds $1 trillion dollars based on current GDP. Corrosion causes unplanned repairs, downtime, and early replacement costs on high-value assets. A simple way to reduce ownership costs is to use coatings that last longer. Pro-active maintenance is a proven way to extend coating life but has been limited due to high labor costs for recoating repairs.
The National Association of Corrosion Engineers (NACE) estimates 25-30% of all corrosion-related damage can be eliminated with improved painting practices estimated at $250-300 billion. A proven maintenance program designed to prevent the conditions that cause corrosion rather than dealing with its effects, have the potential in creating thousands of high-paying jobs for American workers. This would be based on a simple economic principal, “replace economic waste with pro-active work”.
Note: The passage of the corrosion-prevention tax credit bill (HR 4913) would provide a tremendous incentive for companies to adapt maintenance painting programs.
LCS — Program Advantages
- Increase service life for manufactured products and steel structures
- New jobs for U.S. workers trained in LCS-maintenance programs
- Energy savings for corrosion prevention by protective coatings
- Improve asset performance and operational readiness
- Worker safety and morale
- Remanufacturing and recycling potential
- Trade balance, U.S.-made products that last longer reduce foreign imports
- Reduce
- Material waste
- Disposal costs
- VOCs, HAPs, and other forms of environmental pollution
- Corrosion-related repairs downtime
- Early replacement costs
- Lean engineering — need to over-design structures to resist corrosion
Conclusion
A return to planned maintenance is an economic certainty due to the rising global population and energy costs. Today, there is a critical need for coatings that last longer. Billions of dollars are lost each year due to the limited service life for high-value durable goods, equipment, and steel structures. As energy costs rise, asset prices will as rise as well, consisting of manufacturing costs, transportation, operating expenses, and outdated maintenance practices. To offset rising energy costs, the development of a new generation of strategically engineered maintenance programs for paints and coatings are needed for product life maximization.
The argument for planned maintenance is simple, it takes far less resources to repair a coating than it does to repair or replace the surface it is designed to protect.
Looking for a reprint of this article?
From high-res PDFs to custom plaques, order your copy today!