Alkyd Resins, Part Two

Davizro / iStock / Getty Images Plus, via Getty Images.
They say what is old is new, and for alkyds, that is the case. In last month’s column we covered a bit of history and the chemistry of alkyds. In this column we will discuss how alkyds have changed from high-VOC resins to low-solvent-containing water-based emulsions. While there is a separate area of reactive alkyds for baking or two-component systems, here, we will be discussing oxidative-cure ambient temperature systems.
I would like to thank Bruno Dario, Kip Sharp, Juliane Pereira, Fabio Rosa, and Silmar Barrios for their input on alkyd emulsification.
The original polyester/oil systems were high-viscosity systems and needed solvents to lower viscosity, and aid in application. With the need of formulations to move away from solvents and hazardous components, this led to puzzling challenges. Customers wanted low- to zero-VOC formulations along with a better global harmonization system (GHS) labeling profile. This meant that safer systems for the end users (contractor or do-it-yourself painters) were needed. Add to that the need for sustainable solutions, and alkyds are again at the forefront of technology.
Alkyds are polyesters modified with fatty acids, as can be seen in Figure 1. These polymers tend to make coatings that are easy to apply, and generate films with good adhesion and penetration into porous substrates with few defects. They are also forgiving of application conditions (temperature, humidity, substrate contamination, and condition). These are the main reasons why alkyds are so widely used for wood and metal coatings. In addition to that, they are relatively versatile, have low cost, and bring environmental advantages since part of the polymeric structure comes from renewable sources. Nevertheless, alkyds are primarily soluble in volatile organic solvents, which is not aligned with the trends for the coatings industry.

FIGURE 1 ǀ Example of an alkyd resin synthesis.
We need to be able to use it in a water-based system. There have been really four phases of alkyd chemistry development to get to the current water-based emulsions. The first was using alkyds in VOC-containing solvents, known as conventional alkyds.
In the second development/formulation phase, VOC solvents were replaced by some VOC-exempt solvents such as acetone. This was short lived as VOC-exempt solvents did not have the correct volatility. If they evaporated too fast, this led to film defects such as poor leveling, wrinkling or solvent popping. If the evaporation rate is too slow, there can be sagging, dirt pickup, or too long an open time issue. The solvency of the exempt solvents also caused re-coat issues and changed the re-coat window for the system (covered in the last issue). In the end you could not replace enough of the VOC solvents and still reach the VOC limits needed.
The next stage was the move to water-based enamels, which have become a more interesting topic of research during recent years. There was a move that switched alkyds for acrylic polymers to formulate waterborne enamels, however, for applications that require high gloss, penetration into the porous substrates, and high adhesion, these paints show poorer performance when compared to alkyd-based enamels. This is one of the reasons that has driven researchers to find alternatives to stabilize alkyds in water. There are two main options to accomplish making alkyds compatible with water:
- Alkyds with high acid values that are water-soluble after neutralization.
- Alkyd resins synthesized with stabilizing groups in the backbone, the “self-emulsifying alkyds.”
There were many issues with these approaches, such as the hydrolytic stability of the alkyds for longer periods, they still required high amounts of solvents (water-soluble glycol ethers generally), and the inclusion of stabilizing groups to the polymer’s backbone demands changes during the polymerization process and can cause loss of properties in the final film when compared to conventional alkyds.
Therefore, oil-in-water alkyd emulsions are a promising alternative since they have minimum organic solvent content, and the polymer’s backbone is like the one used in conventional solventborne alkyds, which can deliver similar properties in the final film.
Alkyd Emulsions and Colloidal Stability
Emulsions are heterogeneous systems consisting of two liquid phases that are immiscible or at least nearly immiscible. One liquid phase is dispersed as small droplets in another continuous liquid phase. Typically, the liquid phase is dispersed as small droplets that are stabilized by surfactants or emulsifiers. Not all resin emulsions are, in fact, emulsions. Many are dispersions of solids in a liquid. It gets more confusing with polymers because they behave differently above and below the glass transition temperature of the polymer. To simplify things, we will call a resin dispersed in a liquid an emulsion. Alkyds are true emulsions since the alkyd resin is a liquid, sometimes a high-viscosity liquid, but still a liquid.
The main types of emulsions are oil-in-water-emulsions (O/W) and water-in-oil emulsions (W/O). Emulsifiers that are more soluble in water generate O/W emulsions, while emulsifiers that are more soluble in the oil phase generate W/O emulsions. Figure 2 illustrates the two types of emulsions.
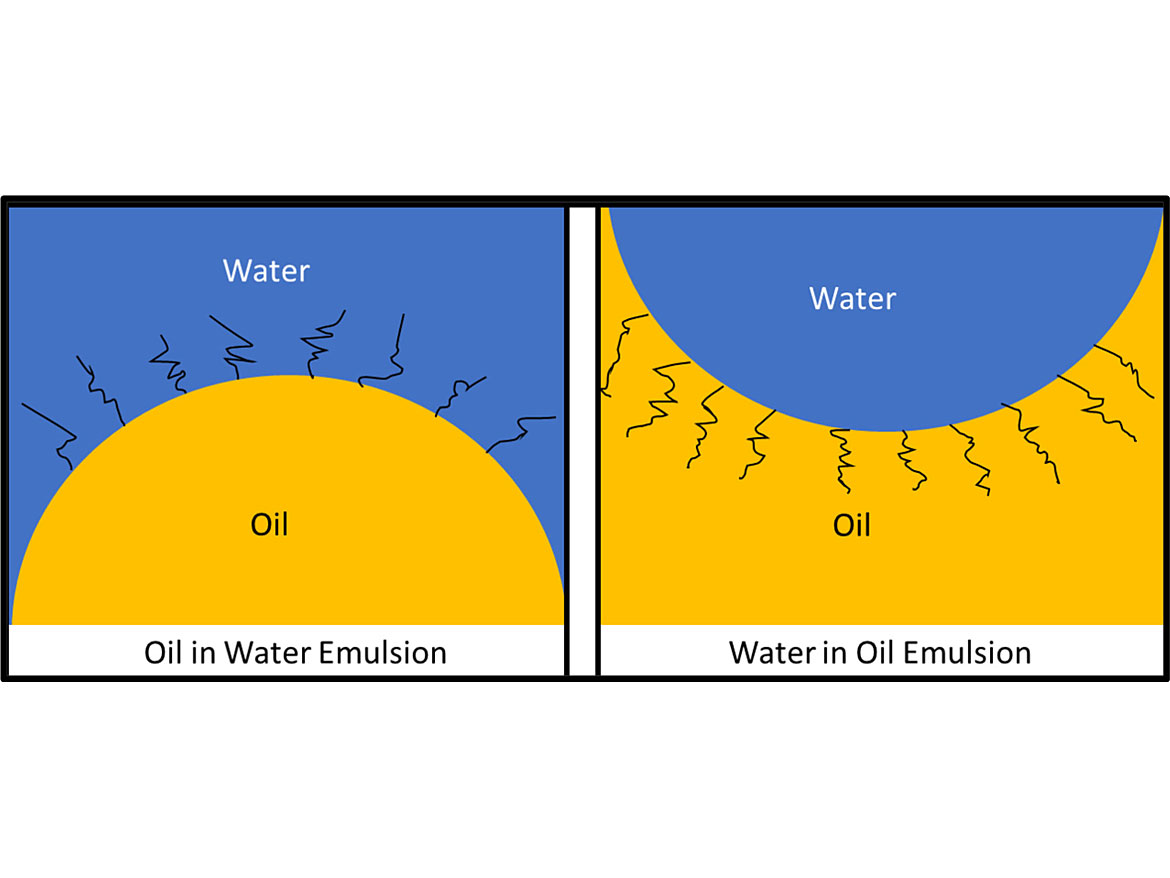
The best way to tell if an emulsion is oil-in-water or water-in-oil is to disperse a drop of the emulsion in what you think is the continuous phase. If you suspect it is an oil-in-water, then add a drop to water to determine if the continuous phase is water. If it blends in well it is an oil-in-water emulsion. While you can always test it in a non-aqueous media, not all non-aqueous media are compatible, and you can get a false negative result. So, test it in water, and through the process of elimination determine if it is water-in-oil.
When considering alkyd emulsions, there are two main types:
- Water-in-alkyd emulsion: Water is dispersed in the alkyd resin diluted in mineral spirits or similar solvent, which is the continuous phase. This emulsion is prepared through direct emulsification using a surfactant or polysaccharide to stabilize the water droplets. This is done to replace some solvent with water to lower solvent cost. Depending on how VOCs are calculated the water may not lower the VOC of the resin or coating.
- Alkyd-in-water emulsion: Here the alkyd resin is the dispersed phase and is stabilized by surfactants (also known as emulsifiers) that are soluble in water, which is the continuous phase. It is normally prepared by the phase inversion process.
The phase inversion process uses surfactants. Anionic surfactants play an important role in controlling particle size through the electrostatic repulsion method, which is critical in oil in water emulsions. Non-ionic surfactants are also needed and are crucial for freeze-thaw resistance as well as providing steric repulsion. You need both classes to reduce the interfacial surface tension between the incompatible liquids during the emulsification process, as well as helping stabilize the oil in water emulsions. The flip from water-in-oil to oil-in-water (also known as the inversion) happens when you get greater than the sphere close packing limit and there is no way to pack the water spheres and still have oil surrounding them. One thing to be aware of is that the viscosity at the inversion point can be very high and will break quickly once more water is added.
In the case of the alkyd-in-water emulsion, water is slowly added to the alkyd with surfactant already present along with a neutralizer for the alkyd under mechanical agitation. As the amount of water increases, you get to the critical point where there is not enough oil to surround the water drops and then the inversion happens. Water is continually added to move from the critical point to form a stable alkyd in water emulsion.
The surfactant choice and level of use, as well as water addition rate, will greatly affect how easily the inversion process is. In some cases, a gel or paste is formed and adding extra water will just cause water to remain around the agitator and not break up the gel/paste. The worst case is when the surfactant package does not allow a stable inversion and you have two different layers of immiscible liquids in the tank. The surfactant is critical in making a stable alkyd emulsion.
We will continue this next month when we cover the emulsification process and show some data on generating stable emulsions.
All information contained herein is provided "as is" without any warranties, express or implied, and under no circumstances shall the author or Indorama be liable for any damages of any nature whatsoever resulting from the use or reliance upon such information. Nothing contained in this publication should be construed as a license under any intellectual property right of any entity, or as a suggestion, recommendation, or authorization to take any action that would infringe any patent. The term "Indorama" is used herein for convenience only, and refers to Indorama Ventures Oxides LLC, its direct and indirect affiliates, and their employees, officers, and directors.
Looking for a reprint of this article?
From high-res PDFs to custom plaques, order your copy today!