How Can Digital Transformation Help Reduce Unplanned Downtime?
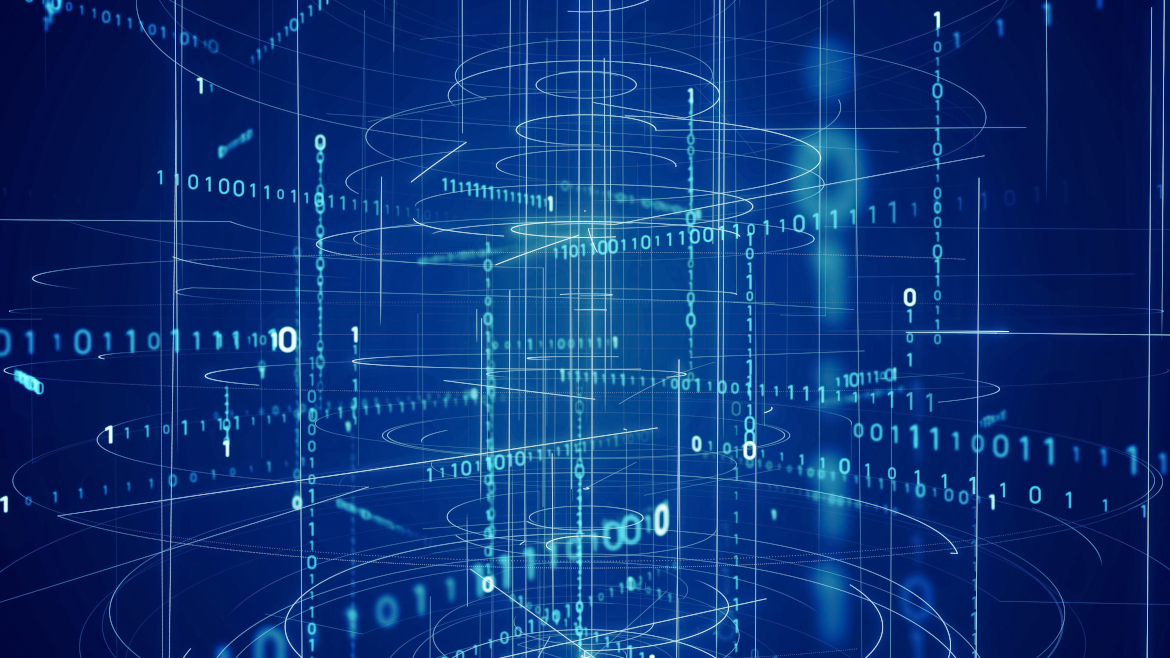
Unplanned downtime causes significant losses to a company. With an estimated price tag of $50 billion annually, there is a serious effort that, rightfully, goes into preventing unscheduled failures.
Upcoming technologies offer tools and capabilities that enable more effective strategies to reduce unplanned breakdowns. However, more advanced processes call for equally progressive requirements. Digital transformation can open the gates to unprecedented reductions in unplanned downtime.
Maximize Data through Digitalization and Integration
The cornerstone of today’s digitally driven innovations is quality data. Information is everywhere, but before it can provide any real value, it first needs to be in a form that enables analysis.
Digitalization involves varying levels of effort to achieve proper standards. Transforming data can involve a combination of structured and unstructured sources, contributing large volumes of information across multiple channels.
A forward-looking way to sustain digitalization is to think about methods of collecting data seamlessly. These are often readily available in technologically mature companies with the data-gathering infrastructure in place. Computerized systems, for example, are effective at taking snapshots that serve as data points for analysis.
Regardless of whether a company is just embarking on digital transformation or has been gaining experience for years, bringing data into one place is always a relevant activity. Integrating data sources provides a complete picture; one that can draw more meaningful interpretations. Companies can explore opportunities to share data in an interconnected world.
Collaboration prospects using an integrated data source span both internal and external functions. Within the same company, departments can break down silos to eliminate inefficiencies when adapting to immediate business needs. Working with external stakeholders, such as trusted suppliers, can improve supply chain lead times and overall costs for keeping production lines running.
Looking into the Future with Predictive Analytics
The next step to maximizing a digitally capable facility is drawing out actionable insights from this wealth of data. Streamlining maintenance practices realizes both practical and effective benefits, and predictive analytics can help companies prevent incidents before they happen.
Industry 4.0 enables a factory to incorporate large data sets with artificial intelligence and machine learning. The result is an informed decision process stemming from a combination of historical and real-time data. The data that goes into a predictive approach bridges the gap between human intervention and machine performance.
Sensors for monitoring equipment conditions tell a lot about the state of a machine. Instead of performing too much or too little servicing, a more objective process becomes available to prioritize maintenance efforts.
For instance, a manufacturing plant that relies on precise formulations may use a predictive approach to flag inconsistencies in the end product, occurring as a consequence of faulty equipment. An industry working with paint and coatings can use machine learning models that automatically identify faults in the final product within a tolerable threshold. Mixing processes and curing schedules for coating procedures can also use artificial intelligence to find the most efficient routes around a system.
In such cases, a condition-based monitoring system, alongside an advanced algorithm, can simplify the identification of root cause analyses and defect detection.
The other piece of the puzzle is keeping track of remediating actions and factoring them into the bigger picture. While condition-monitoring devices are relentless in reporting data, the data still requires the constructive judgment of human intervention. An adaptable system allows inputs from completed corrective work and inspection observations to be included in a more comprehensive analysis.
Digital Work Management
In relation to the human component of a typical plant, digital transformation eases the communication between teams and machines. Aside from the brains behind predictive analytics, another practical solution associated with digitalization is a simplified work management process.
Ultimately, any company that deals with pieces of equipment and machinery will require maintenance work. Completing a work order is often a tedious process; maximizing the capabilities of an interconnected digital system reduces the number of tasks that do not add any real value to the process. Workflow digitization enables seamless communication between workers, equipment, and a centralized system. The steps that comprise an entire work order, from identification to execution, provide opportunities for automation using linked devices.
Modern software, such as a computerized maintenance management system (CMMS), provides mobile options that bring the application onto the shop floor. Workers can input their actions as they move around the facility; including inspection findings, servicing requirements, and other general updates.
Digitizing the work management process creates a seamless route to raise work demands and trigger the material sourcing required for a job. Scheduling and planning activities become more efficient with an overall view of work requests alongside resource capacity. Additionally, maintenance teams can also track the progress of work schedules to improve productivity, safety, and cost efficiency.
Scalability and Continuous Improvement
Truly reaping the benefits of digital transformation requires the capacity to include a sizable portion of the manufacturing facility. Depending on the size of the operation, multiple components will contribute to data collection, generating recommendations for preventing a breakdown. Because digital transformation is a continual effort, scalability is an important consideration throughout the journey.
As a start, companies might aim to digitize and integrate data within an entire facility. With enough experience and the proper infrastructure, the same workflow can expand into more locations and throughout the enterprise.
As companies scale their operations, conscious performance evaluation will bring out the best practices. Continuous-improvement cycles, that document room for improvement from each process, will inevitably accumulate to a sizable and measurable increase in productivity. For instance, moving toward more advanced tools that can measure equipment condition using non-disruptive techniques allows companies to reduce non-essential stoppages. Thinking about scalability, along with continuous improvement, broadens the application of strategies that minimize downtime.
Real-world success stories of digital transformation show a lot of promise in improving production time, while mitigating the cost of equipment downtime. A case study spanning 26 months shows the progression from whiteboards and spreadsheets to integrated mobile systems. The transformation led to a 350-hour reduction in downtime, saving upwards of a million dollars in cost mitigation.
Conclusion
Transitioning into a more digitally capable approach takes advantage of some recently unprecedented technology. This technology improves long-standing manufacturing practices, digitizing plant data into a form that enables advanced analytics, and opening a world of data-driven insights. As a result, unplanned downtime is no longer an uncontrollable consequence but a manageable outcome.
Looking for a reprint of this article?
From high-res PDFs to custom plaques, order your copy today!