Using Paint to Reduce Underwater Noise for the Shipping Industry

Underwater Radiated Noise (URN) generated from shipping activity is known to have significant environmental impacts to some marine life.1 Quantifying URN from ships is an inherently difficult undertaking because vessels are equipped with many and various types of machinery that each contribute to different frequencies of noise and vibration levels.2 Many studies show that, at higher operational speeds, the main source of URN is due to cavitation of the propeller.2,3,4,5 At low speeds, the main source of URN is generally associated with machinery noise propagating into the water column. Once a ship reaches its cavitation inception speed, the URN level and pressure pulses are dominated by the cavitating propeller.2 Cavitating propellers have more complex noise spectra with considerably higher sound pressure levels than the noise spectra for non-cavitating propellers.
The overall URN level of surface ships can be associated with vessel speed and displacement up to 100 Hz for commercial vessels.3 Propeller cavitation noise is known to start at 50-150 Hz but can extend to 10,000 Hz. Low-frequency sounds are of more concern because of their transmissibility over long distances, and they often match the frequency of sounds of importance to marine mammals. Research was conducted to investigate the noise from different types of ships. Two dominant features that show predominant low-frequency noise at the low-frequency range result from propeller blade cavitation and their harmonics. For container ships and vehicle carriers there is some evidence for an increase in radiated noise with an increase in speed.3
Container ship- and tanker-generated URN is predominantly below 40 Hz, with bulk carrier noise generally being most dominant at around 100 Hz. In addition to the dominant peaks levels, broad-spectrum noise is also readily observable. Above 300 Hz, tankers produce less acoustic energy than container and bulk carriers. Fouling or damage to the propeller is unlikely to account for the major difference between ship types because the same characteristics are apparent in all ships of a given type. Vehicle carriers had the lowest source levels compared to the other ship types discussed. Noise from commercial ship traffic is a dominant component of the low-frequency noise in the deep ocean (Figure 1).3

Usually, the ship underwater noise sources are of three types: mechanical noise, propeller noise and hydrodynamic (flow) noise. Mechanical- and propeller-generated noise are the most significant in terms of overall contribution to URN. A study involving an oil tanker ship was performed, and in the range of 800-4,000 Hz the radiated sound power decreased with increasing frequency. After 4,000 Hz, the radiated sound power started to rise slowly again.1 A different study showed that any savings in noise before and after cleaning the hull are likely to be, at most, 3 to 3.5 dB for RNL (underwater radiated noise level), and 4 to 6 dB for MSL (monopole source level).6 To put this level in perspective, broadband noise emissions for the studied ship (M/V Cygnus), ranged between 177-194 dB re 1 µPa m for RNL and between 178-200 dB re 1 µPa m for MSL. Against the 177-200 dB re 1 µPa generated by the studied ship mentioned above, a male humpback whale averaging 126-158 dB re 1 μPa would be overpowered.6 The study showed that cleaning the hull and the propeller does not affect vessel noise generation.7
Table 1 shows a comparison of simulation values versus measured values in the bandwidth (dB).

Table 2 shows measurements in middle- and low-frequency ranges. It shows the noise energy emitted by the top 10 ship design contributors, which represent over 90% of the noise energy emitted on the oceans by commercial activity.3

Effects of Noise Pollution on Marine Mammals
Invisible to the human eye, ocean noise pollution is one of the deadliest threats to marine animals. The effects on whales and dolphins, and fish in general, can result in the degradation of their hearing for communicating, sensing danger, finding a partner and hunting prey, or even affecting the schooling structure of fish.
Alternative Methods for URN Reduction
The following list shows possible methods for reducing underwater radiated noise.
- Painting the propeller, except for the trailing edge, potentially decreases cavitation effects.
- Increasing cavitation inception speed through improved propeller design.
- Reducing overall cavitation noise through improved propeller design.
- Improving machinery mounting systems, focusing on main engines, diesel generator sets and gearboxes (while not forgetting other machinery and flanking paths). This could go all the way to fully rafted and enclosed machinery.
- Improved machinery design and selection during build (lower vibration machinery).
- Increase structural damping (addition of tiles of some sort). Note that anechoic tiles have nothing (well almost nothing) to do with radiated noise.
- Changes in ship operation (slower acceleration, slower turning, reduced speeds in some areas).
Modern Solutions Involving Coatings
There are two types of acoustic coatings that are efficient technological solutions to noise reduction: decoupling coatings and anechoic coatings. Normally, both consist of relatively thick viscoelastic layers with some voids and other inclusions in the matrix. The role of decoupling coatings is to reduce the transmission of hull vibrations to the water, and the role of anechoic coatings is to reduce acoustic reflection from the hull by absorbing incoming sound waves.4 Figure 2 is a schematic of a possible solution that includes full hull protection, including an anticorrosive primer system, a noise reduction primer and a foul release, environmentally friendly coating. The solution will potentially provide full environmental protection and superior hull protection for ship owners.

Lab Data – Coating Solutions for Noise Reduction
Noise reduction coatings are a new concept for the shipping industry. They consist of a hard polymeric layer with functional pigments that have the capacity to “dump” noise, or absorb and reflect acoustic energy. Figures 3 and 4 illustrates the potential reduction in (dB) at low frequencies (<1,000 Hz), where it is possible to reduce ~3db of noise per 100 µm of paint applied to the painted hull. The coating was compared with sandblasted metal (3 mm thick) and other commercial coatings.


As the static sound measurements of the disclosed compositions, the experimental sound encapsulation setup had been designed and assembled by our laboratory, as depicted in Figure 5 below.

To isolate the measurements from the environmental noise, the sound irradiation and recordings were performed inside the Styrofoam double chamber. Styrofoam performed the sound deadening function, and the smaller inner chamber hosted both the sound measuring device (software – audacity, hardware – amplifier, low frequency microphone) and the lab speaker that emitted frequencies from 100 Hz to 10 KHz. The data was than collected using the acoustic signal of the painted cold rolled steel, subtracting the interference of the cold rolled steel on air, leaving only the acoustic signal referencing to the paint portion. The gain and distance of the microphone and speaker were kept constant for repeatability purposes, with triplicates of each sample being tested.
Field Data – Coating Solutions for Noise Reduction
In terms of marine paints and coatings, we have focused on three ways to reduce underwater noise:
-
Use a propeller paint to increase the cavitation inception speed. The painted propeller also significantly reduces the surface defects from cavitation and reduces the surface friction resistance of the blades passing thought the water (Figure 6).
-
Use a “noise-reduction primer” to decrease the noise transmission from engine, gear box and machinery from inside of the vessels (Figure 7).
-
Create low surface friction with the ocean water to reduce the hydrodynamic noise created by the skin friction layer between the hull and the ocean water (Figure 8).
Hull Data Collection
The vessel’s hull was split into four zones as follows: Port Side Bow, Port Side Stern, Starboard Side Bow and Starboard Side Stern. The prior application data refers to the measurements collected during the first boat inspection done last year at McGraths cove in Nova Scotia.
The results show a reduction of approximately 71% on the average hull wet coefficient of friction after applying the new hard foul release coating, XGIT-Fuel (Figure 9).




Hull Surface Roughness
The vessel’s hull was split into four zones as follows: Port Side Bow, Port Side Stern, Starboard Side Bow and Starboard Side Stern. Each hull zone area was fully cleaned of fouling in order to accurately capture the surface profile and obtain the roughness measurement data prior to surface preparation and coating application. Ten averages of nine measurements were taken prior application for this study, and another 10 averages of nine measurements each were taken post application of the coating. Each of the 90 measurements of each zone represents the total peak to valley height value “Rt” of the surface profile. The prior application data were taken from the previous boat inspection due to the dirty condition of the boat. The results show that there was a reduction of approximately 30% on the average hull surface roughness (µm), which should contribute to the reduction in hydrodynamic noise (Figure 10).
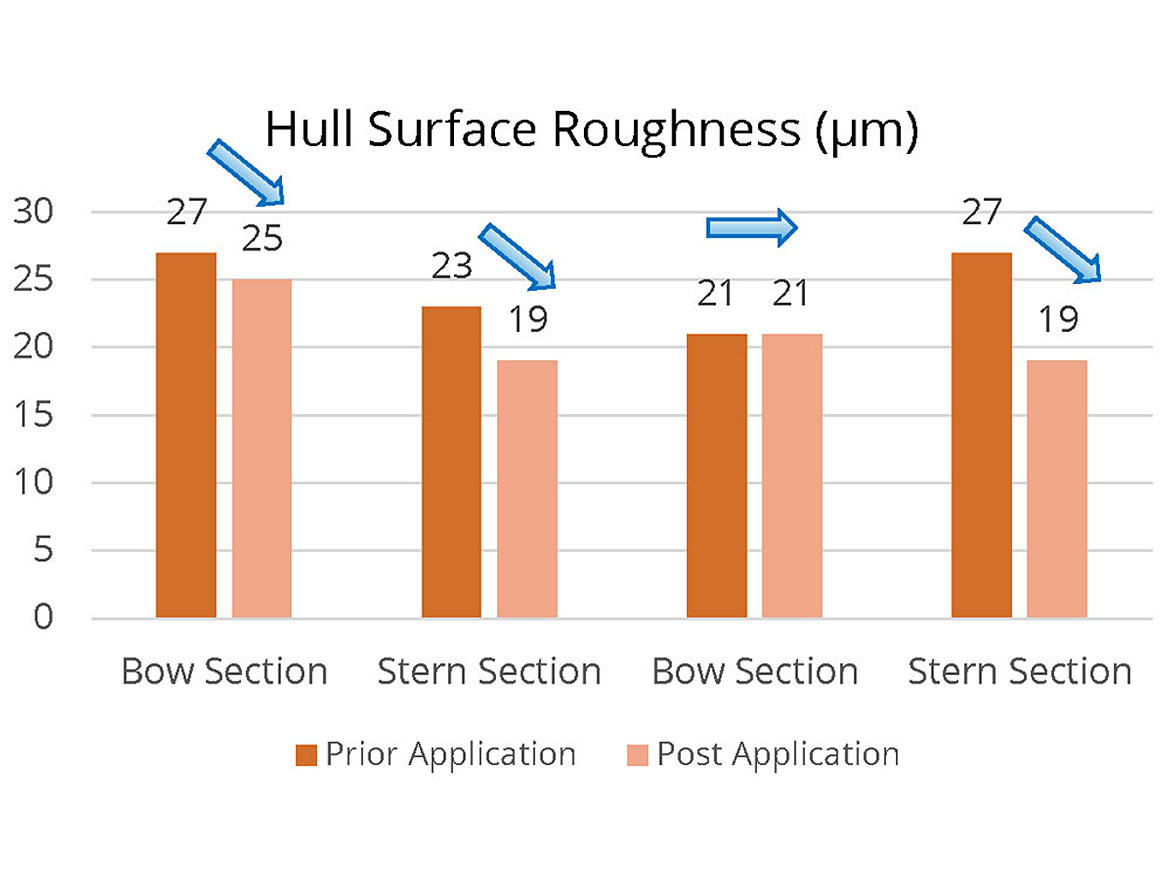
Propeller Data Collection
Figure 11 and Table 3 show surface properties before and after XGIT-Prop coating application.


Underwater Noise Field Measurements
The dynamic URN measurements include the contributions of machinery, flow and propeller-generated noise. Figure 12 shows the URN results obtained for all currently trialed boats in terms of minimum (~4 knots) and near maximum speed (~8 knots) conditions. The results are averaged for reciprocal runs to minimize the influence of wind and current. As with the static measurements, the low-speed run results are similar for all boats with the noise levels within a range of 10 dB at any given frequency.

Comparing the low-speed to the high-speed runs, there is a marked increase (~15 dB) in the noise level starting at approximately 100 Hz for all boats. Below 60 Hz the change in sound level between low-speed and high-speed tests is minimal. Comparing the dynamic results to the static measurements below 60 Hz shows that there is only a slight increase in noise levels in this frequency range, which suggests the noise levels below 60 Hz are dominated by the engine. The broadband increase in the noise levels at the upper frequencies is typical of propeller- and flow-related noise. (The first order engine running frequency is 12-15 Hz at 4 knots for most of these engines/boats, and 30-40 Hz at 8 knots, keeping in mind that half orders are typically present for four-stroke engines, which would be the case for all boats with the exception of one of the studied vessels. With four blade propeller and 3:1 gearbox, blade passing frequencies are approximately 16-20 and 40-53 Hz at 4 and 8 knots respectively).
On average, the vessels showed the bellow noise signature when measured in three stages: 1) heavy fouled and with cavitation propellers; 2) with clean hulls; and 3) after being retrofitted with the XGIT-Product line. A large reduction of the sound level was observed when the hull was cleaned, and a further reduction of URN was observed when the coatings were applied.
Conclusions
A noise hygiene plan is generally not a single point address into any one area, but an overall attention to all areas, as detailed in this article. The cumulative effects can become quite significant. To reduce the noise impact of ships, a series of technologies must be adapted including:
- Avoid cavitation inception speed.
- Constantly keep the hull and propeller clean and without surface defects.
- Use noise-absorbing mounts on ship vibration sources (engines, motors and other machines).
- Use noise insulation coatings on the hull of the vessel to reduce noise and vibrations.
Additional conclusions from this study include:
- Noise-damping hull coatings can be easily applied with minimal interference in traditional methods of vessel retrofit.
- Propeller cavitation has a significant impact on URN emissions and can be closed monitored to prevent and reduce emissions.
- Several modifications on the vessels can have a cumulative effect on shipping noise reduction.
- Of final note, addressing noise pollution creates an instantaneous remedy to the problem which cannot be said of many forms of pollution reduction measures.
Acknowledgements
This project was supported by Transport Canada’s Innovation Centre (TC-IC).
Jim Covill and Ken Mackay (Lloyds Register – Canada office) for their data collection of Underwater radiated noise presented on Figure 12.
References
1 De Paepe, A.E. et al., IMO - Ship Underwater Radiated Noise Technical Report and Matrix, 2019. doi: 10.1017/CBO9781107415324.004.
2 Turkmen, S.; Aktas, B.; Atlar, M.; Sasaki, N.; Sampson, R.; Shi, W. On-Board Measurement Techniques to Quantify Underwater Radiated Noise Level, Ocean Eng., vol. 130, no. December 2015, pp. 166-175, 2017, doi: 10.1016/j.oceaneng.2016.11.070.
3 Mckenna, M.F.; Ross, D.; Wiggins, S.M.; Hildebrand, J.A. Underwater Radiated Noise From Modern Commercial Ships,” Cit. J. Acoust. Soc. Am., vol. 131, p. 92, 2012, doi: 10.1121/1.3664100.
4 Jalkanen, J.P. et al., Modelling of Ships as a Source of Underwater Noise, Ocean Sci, vol. 14, pp. 1373-1383, 2018, doi: 10.5194/os-14-1373-2018.
5 Noise Emitted from Ships: Impact Inside and Outside the Vessels | Elsevier Enhanced Reader. https://reader.elsevier.com/reader/sd/pii/S1877042812028005?token=1673AC7E190256D17BA01FE34658AA5637A324D3109C3DA0BA42A1E2B551BF1EE557F2EEEDAB3EBF7F74D3E8466BB505 (accessed May 15, 2020).
6 Chen, J.; Pack, A.A.; Au, W.W.; Stimpert, A.K. Measurements of Humpback Whale Song Sound Levels Received By a Calf in Association with a Singer. J Acoust Soc Am. 2016 Nov;140(5):4010. doi: 10.1121/1.4967444. PMID: 27908071.
7 Centre, I.; Canada, T. M/V Cygnus Underwater Radiated Noise Level Measurements in Conception Bay, NL, no. November, 2018.
Looking for a reprint of this article?
From high-res PDFs to custom plaques, order your copy today!