Water Miscibility Differences in Coalescing Agents and the Influence on Latex Paint Properties

Coalescing agents are an inseparable component of latex paints containing polymer dispersions with a minimum film forming temperature (MFFT) higher than the temperature of application and drying of the coatings. In practice, however, in many low-MFFT paints, coalescents are also used to enhance the forming quality of the coating, especially at temperatures below room temperature. Most polymer dispersions used as binders for the production of latex paints have an MFFT of 50 °F to 77 °F (10°C to 25 °C).
Market demands mean that the expected application temperature for paints can usually start at 41 °F (5 °C). This also applies to drying, but it should be kept in mind that during drying, within several minutes or hours, the temperature may drop periodically to below 41 °F (5 °C) and remain at a critical temperature during the coating formation period. Water freezes within 32 °F to 39 °F (0 °C to 4 °C). Effective coalescing action is therefore needed not only in the region just below the film-forming temperature, but also or especially in the critical range for the initiation of freezing of the water.
It should also not be forgotten that the coalescent in the paint formulation is also present during its application at much more favorable temperatures, e.g. 77 °F (25 °C). If the procedure of selecting the coalescent was limited only to checking the MFFT and determining the effective dose for the formation of a non-fractured film, then the coalescent selected in this way may not form a proper film at low temperatures, and may also affect many coating properties when it dries at positive temperatures.
Coalescing Agent Case Studies
In case studies, six different coalescents with different properties were used, including those significantly different in their miscibility with water (Table 1).

Determination of MFFT
First, the coalescing doses needed to achieve a MFFT below 39 °F (4 °C) were determined. The test was performed in accordance with ASTM D2354 using the Rhopoint MFFT Bar 60 (Figure 1). The test was performed for a mixture of polymer dispersions with ladder-increasing doses of coalescing agents. Initial MFFT of the polymer dispersion without coalescing agents was 57 °F (13.9 °C).

The polymer dispersion used was a styrene-acrylic latex binder with a Tg of approx. 75 °F (24 °C), according to the manufacturer's TDS, and a non-volatile matter of approx. 50% by weight. The results presented as a graph of the dependence of the coalescent dose on the dispersion weight and MFFT are presented in Figure 2.

The amounts of coalescing agents added to the formulation resulted from the determination of the effective reduction of the MFFT shown in Figure 2. The doses of coalescing agents used for the preparation of paint samples were as follows:
-
PMA: 16%* (MFFT reduction to 37 °F / 3.1 °C)**
-
BDGA, TMPDMIB and WS: 3%* (MFFT reduction to 32 °F/0 °C)
-
BDG and TMPDDIB: 4%* (MFFT reduction to 32 °F/0 °C)
*(dosage on total quantity of polymer latex dispersion)
**In the case of PMA, the higher doses were not tested by obtaining the result at a very high dosage
Formulation
A latex paint formulation with PVC of approximately 33%, medium base for tinting, was prepared for the coalescing tests, as shown in Table 2.

Paint Sample Preparation
The paint samples were prepared on a laboratory scale from the previously prepared surfactant stabilized slurry 02 (formulation in Table 3), which was introduced into the polymer dispersion in the let-down stage. Slurry was prepared in such a way as to introduce the necessary amounts of biocide and defoamer into the paint.

The slurry was introduced under the anchor mixer, and further ingredients from the formulation were added. The prepared bases of the medium were colored with a concentrated blue paste in the amount of about 2 fl oz/gal. The water used for the preparation of all samples had a conductivity <1µS/cm (measurement of the water leaving the water demineralization station). The amounts of rheological additive used in the formulation were selected by adjusting the consistency of the paints to be in the range of 90-100 KU. Consistency measurements were made in accordance with ASTM D562 using a Stormer digital viscometer.
Experimental
The aim of the experiment was to show to what extent individual coalescents affect changes in some properties of paints and coatings from the prepared paint samples and to verify whether the determined doses based on changes in MFFT for the dispersion of polymers and coalescing agents alone can be correlated with the results obtained for paints in tests in accordance with standardized methods. The paints were thoroughly mixed before the tests.
MFFT
Although the MFFT test was performed for the polymer dispersion-coalescent mixture, it was decided to carry out this test also for the prepared paints to see if any differences between the coalescents in the prepared paints were noticed. The test was performed in accordance with ASTM D2354 using the Rhopoint MFFT Bar 60 by applying paint strips with a cube applicator with gap 75 µm. Tests performed in the test range “0”: 14 °F to 46 °F (-10 °C to 8 °C).
Low-Temperature Coalescence (LTC)
The test was performed in accordance with the ASTM D7306 standard. The paint was stored within 4 hours in the refrigerator to cool it down to a low temperature, for this test 39 °F ± 4 °F (4 °C ± 2 °C). The substrate and the gap applicator were conditioned at the same temperature. The test substrates were cards with two levels of absorbency – with an absorbent (unsealed) and non-absorbent (sealed) surface.
The paint was applied with a high-gap applicator and automatic drawdown machine, in this case 400 µm gap, to increase the aggressiveness of the test (a thicker layer tolerates the test conditions worse). After storing the coatings for 18 hours at the same temperature as before, the coatings were removed, brought to 73 °F (23 °C) and assessed for cracking, gloss changes and appearance on the absorbent and non-absorbent surfaces by judging under a magnifying glass.
Blocking Properties
Coatings obtained with the gap applicator and automatic drawdown machine were conditioned for 7 days in conditions in accordance with ASTM D3924, i.e. 73 °F (23 °C) and a relative air humidity of 50% ± 5%. Then, using a guillotine, 1½-inch squares were cut, folded face to face and loaded with 1.8 psi (127 g/cm2) and placed at 115-125 °F (48-52 °C) for 30 minutes. After taking them out, they were cooled down in laboratory conditions for another 30 minutes and assessed for the ease of surface detachment and, in the case of sticking of the coatings, for the degree of sealing. The test and evaluation were performed in accordance with ASTM D4946.
Scrubbability
The scrub test was performed in accordance with ASTM D2486. The tested paints were applied to the plastic panels with a gap applicator and automatic drawdown machine, and conditioned for 7 days in a standard atmosphere at 73 °F (23 °C) and a relative air humidity of 50% ± 5 %.
Scrubbing was performed with a 454-g nylon bristle brush, which was properly prepared (soaked in water, pre-scrubbed, etc.) and an abrasive medium in accordance with ASTM D2486. Underneath the coated panel was a shim that defined where the coating failure happened.
Consistency and Settling
The consistency of the samples was assessed immediately after the faerb preparation (after adjusting the consistency to the specified value), after the night and 7 days post preparation. Consistency measurements were made in accordance with ASTM D562 using a Stormer digital viscometer.
During the paint tests, settling in the samples was observed. Settling evaluations were made with a standardized spatula according to ASTM D869.
Anti-Sag Index
Sagging was assessed according to ASTM D4400 (pre-shearing procedure with a syringe and needle for waterborne paints). The drawdown was performed in accordance with the procedure by motor-driving the Leneta ASM-4 applicator (4-24 mils gaps) at a speed of 150 mm/s.
Test Results
Below are the results of tests carried out within the scope of the project.
MFFT
All tested paints achieved coating formation assessed in accordance with the test procedure in determining the MFFT at 32 °F (0 °C). Each of the samples had a continuous coating (no cracks at 10x magnification) in the range down to approximately 26 °F (-3.0 °C). Below this range, the coatings were frozen (covered with a layer of frost). The performed test shows that all coatings are formed in a given test temperature range.
LTC
An assessment was made with a 10x magnifying glass. The rating was carried out in accordance with ASTM D7306 — cracking assessment according to the system. The total score was the addition of ratings on the absorbent (unsealed) and non-absorbent (sealed) substrates. Table 4 presents the LTC score together with comments.

Figures 3a-5b show the coatings with differences between the absorbent and the non-absorbent surfaces. All photos were taken under 10x magnification.

Absorbent Substrate (Unsealed)
BDG

Non-Absorbent Substrate (Sealed)
BDG

Absorbent Substrate (Unsealed)
TMPDMIB

Non-Absorbent Substrate (Sealed)
TMPDMIB

Absorbent Substrate (Unsealed)
TMPDDIB

Non-Absorbent Substrate (Sealed)
TMPDDIB
During the LTC test in the refrigerator, the temperature and humidity conditions were controlled with a temperature recorder every 1 minute. The temperature during the test was about 40 °F (approx. 4.5 °C) after stabilization (after placing the samples in the refrigerator). The relative humidity in the refrigerator during 18 hours of drying was 60% to 84%.
Blocking Properties
Figures 6-11 show the appearance of the coatings after removal from the oven and separation of the facial surfaces. Table 5 shows the rating values and interpretation of the seal.

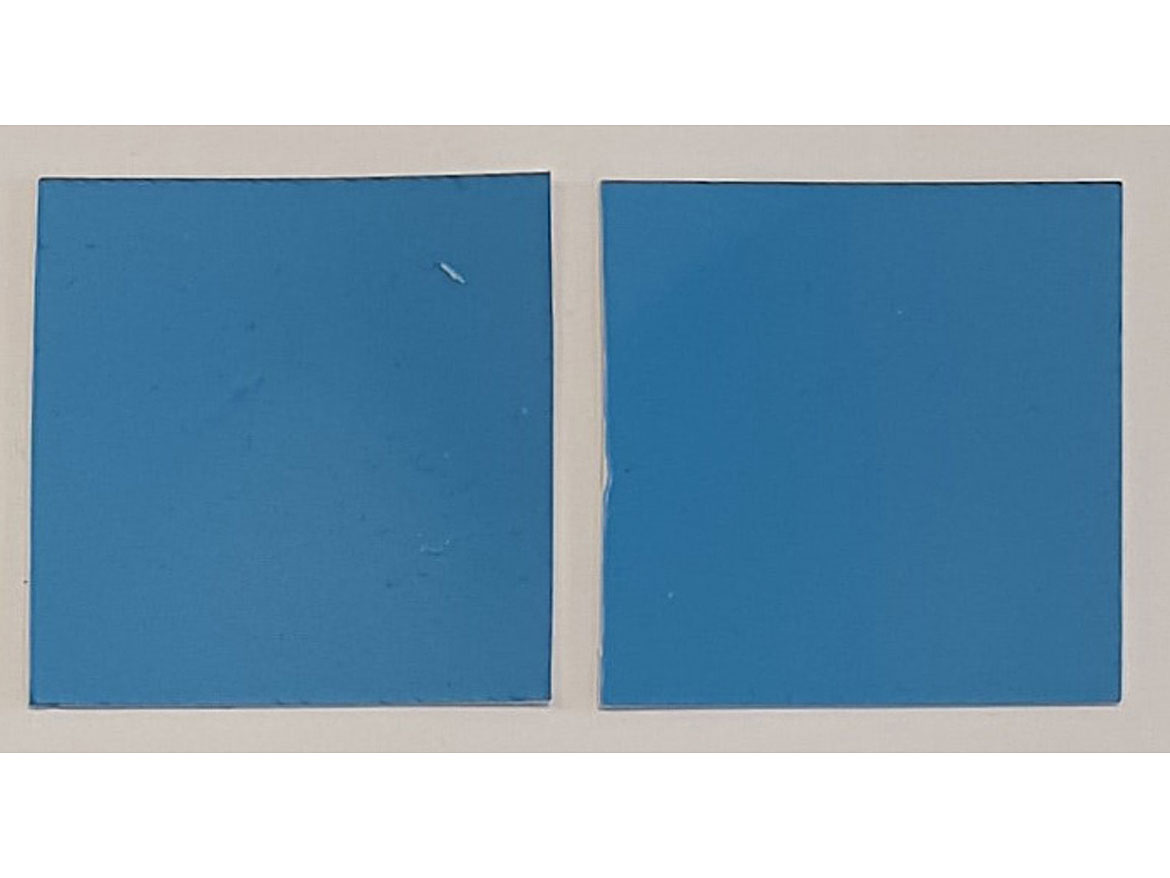





Scrubbability
The scrub test was performed on paired coatings according to the scheme: PMA and WS, BDGA and BDG, and TMPDMIB and TMPDDIB. Scrubbing was continued until breakthrough of failure as defined in the test method. Figure 12 shows pictures of coatings grouped in pairs for which a higher strength coating failure occurred.

The photos were taken at the end of the test for coatings with higher scrub resistance, and the values obtained for each coating in accordance with the test method are shown in Table 6.

Consistency and Settling
The consistency measurement results are shown in Table 7.

During the tests of the described parameters, the paint samples were observed for the presence of sediment in the samples. They were not subjected to accelerated tests, but the behavior was observed under laboratory conditions. As a result of these observations, it was noticed that in the BDG and BDGA samples, sediment appeared several days after preparation. Settling took more and more form over the course of several weeks. The scores are shown in Table 8, and a visual result is shown in Figure 13.
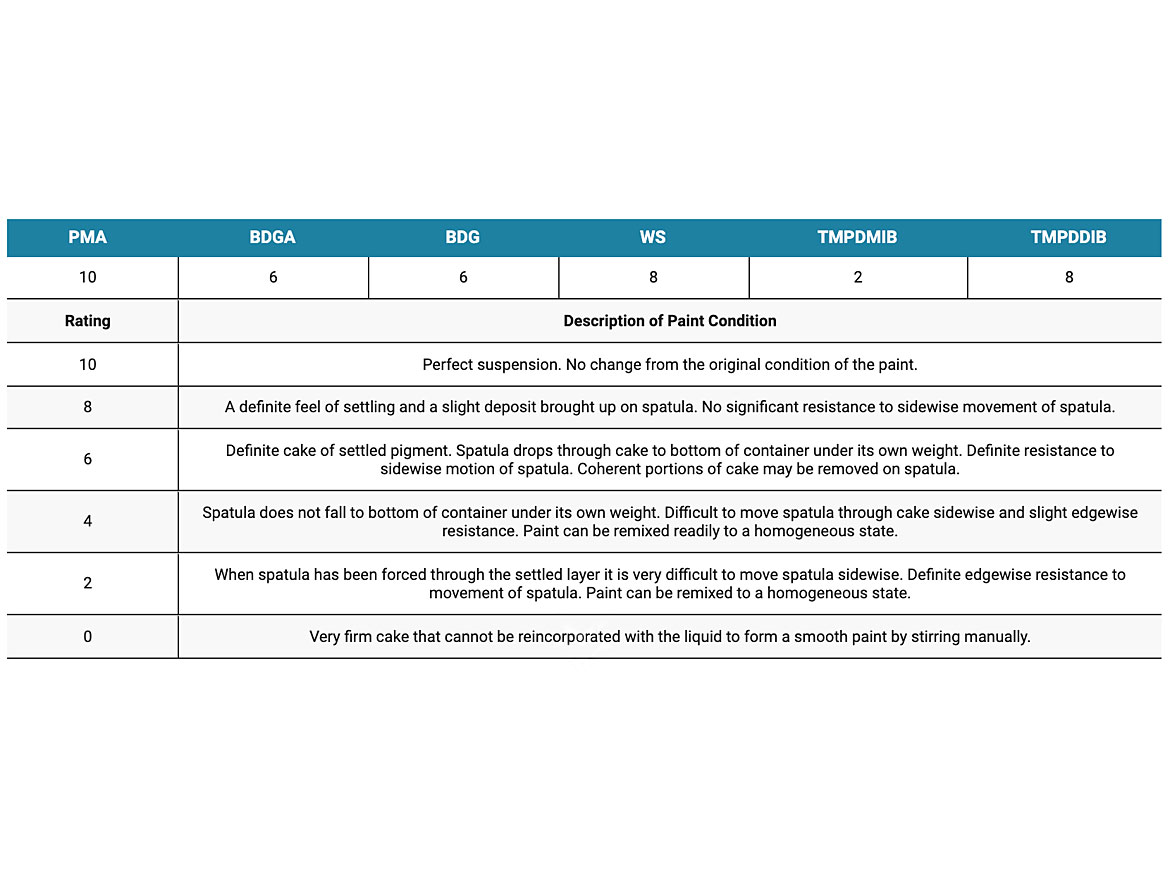

Anti-Sag Index
Sagging results are presented in Figure 14 with the anti-sag index score for individual samples in the range of 4 mils to 24 mils.

Discussion of Test Results
The test results are discussed and interpreted below.
MFFT
The established doses of coalescents ensured the film formation of the mixture polymer dispersion plus coalescent at 32 °F (0 °C) for the tested coalescents, with the exception of PMA, whose very high dose (16% per polymer dispersion) allowed to form a film at 37 °F (3.1 °C). Testing according to ASTM D2354 method confirmed film formation of paints prepared with individual coalescing agents in the range from 14 °F to 46 °F (-10 °C to 8 °C) according to the same ASTM D2354 test procedure.
LTC
The test that verifies the formation of coatings under low-temperature conditions that can occur in real life, and for this purpose coalescents are added, is the LTC test. As shown by the results of the low-temperature tests, the BDG coalescent did not form a coating on an absorbent (unsealed) substrate. Coalescents TMPDMIB and TMPDDIB did not form coatings on both types of substrate (absorbent and non-absorbent).
Consider as the first case the two coalescents TMPDDMIB and TMPDDIB. The selected doses based on the MFFT test were set at a dosing level of 3% per polymer dispersion and ensured continuous film formation at 32 °F (0 °C) under MFFT test conditions. It should be emphasized that the MFFT test carried out in accordance with the standard evaluation method differs from the LTC test performed on substrates of different absorbency and under significantly different air humidity conditions above the coating. The example of these two coalescents shows that although the 3% dose was determined from the MFFT test, this amount is not sufficient to form a coating as low as 39 °F (4 °F). Tests performed in addition to the above-mentioned examples with a dose of 4% allowed to obtain satisfactory results and formation of coatings during the LTC test. The example of these two coalescents shows that the selection of coalescents should be made with great caution only on the basis of determining their doses on the basis of the MFFT test, and that the selection should be carried out in many ways, for different doses of coalescents, different temperatures and with the use of different test methods, of which LTC is one of the most important.
The example of the BDG shows something completely different. Coalescent BDG did not form a coating on an absorbent substrate (not sealed) at the reduced temperature. The coating on a sealed, non-absorbent substrate is continuous and does not show cracks. It should be remembered that during the formation of the coating and its drying, all volatile components (water, coalescents, other volatile components of additives, etc.) evaporate from it. This evaporation into the environment takes place in an obvious way, however, one should not forget about the absorption of water and other ingredients, including coalescents, into the substrate.
Architectural paints are usually applied to highly absorbent substrates. Even with the use of primers or sealants, this absorbency is still present. If the coalescent does not mix with water (it forms droplets in it), it does not evaporate into the atmosphere with water, but it is also not absorbed with water into the substrate. After the coating has discharged water, the coalescent with low or virtually no miscibility with water will continue to participate in the formation of the coating and will not "run out" due to its partial release to the substrate. In the case of coalescents, which show a very high miscibility with water, and the BDG shows such miscibility (995 g/L), we can see on the example of the LTC test.
Water, together with the coalescing agent, is returned to the substrate in the form of a mixture, and part of the coalescent is lost without taking part in the formation of the coating (Figure 15). At low temperatures, this phenomenon is further exacerbated by extended drying times, higher air humidity, and reduced mobility of water particles and polymer dispersion during coating formation.

In lowered temperature, the drying process usually takes place with a faster discharge of water to the substrate than evaporation to the environment, which has increased humidity. Such conditions are even more favorable for the unfavorable absorption of the water-coalescent mixture into the substrate.
Blocking Properties
Blocking properties are very important when painting surfaces that will be in contact with each other. It is very important that they do not show sticky properties and that there is no risk of sticking, for example, of the door to the frame. The timing of getting anti-blocking properties is also important.
The blocking tests performed show that the coalescent used can significantly affect the anti-blocking properties. The coalescents PMA, BDGA and WS allowed the coatings to separate from each other, but they still showed tack. The BDG, TMPDMIB and TMPDDIB coalescents in the tested formulation showed sealing of the coatings, the smallest of which was shown by the TMPDDIB sample.
None of the samples obtained a satisfactory result, because the polymer dispersion used in the formulation did not show very high hardness and blocking resistance. The Tg of the polymer dispersion is approx. 75 °F (24 °C), and the formulation itself was not to be dedicated to applications, for example, in window or door joinery. The tests were aimed at showing that despite the average blocking resistance of the polymer dispersion and the starting formulation, each coalescent used in the tests had a different effect on the change of the result.
Scrubbability
The tested formulation based on the polymer dispersion used and relatively low PVC did not show stunning results of scrub resistance (all results below 1,000 cycles). However, there are differences between the results that allow for the interpretation of the influence of coalescing agents on the obtained wet scrub resistance.
The paint with the BDG coalescent had the highest scrub resistance result (610 cycles to failure). About 78% of this scrub resistance is in BDGA paint. On the other hand, paints based on alcohol esters, TMPDDIB scored 500 cycles to failure, and TMPDMIB achieved 92% of this result. PMA-based paint scored 280 cycles to failure, which is 58% of the WS-based paint score (480 cycles to failure).
The percentage ratio of the lowest score (PMA based paint) to the highest score (BDG ink sample) was almost 46%. These results show a significant influence of coalescing agents on the wet scrub resistance of coatings, as they are responsible for the quality of the formed coatings.
Consistency and Settling
During preparation, all paints had consistency adjusted to obtain the expected value of 90-110 KU. Due to the presence of HEUR thickeners in the formulation (both added to the prepared paint and pigments and fillers present in slurry), the dependence of viscosity on coalescing agents is high. Polyurethane thickeners (HEUR) show various effectiveness and sometimes instability depending on the polarity of the cosolvent, the role of which in this case is also played by the coalescents used in the tests.
All the coalescents used allowed to obtain the consistency in the expected range, except for the consistency with the WS coalescing agent, which was difficult to control. Its complete dissimilarity in terms of physicochemical properties, perhaps the enhancement of associative thickening, caused the paint consistency to increase slightly above the desired level of 110 KU after a night.
In the case of sludge evaluation, there is also a tendency to settling of pigments and fillers depending on the coalescent used.
Anti-Sag Index
The synergistic effect as a cosolvent, especially as solvents of different polarity, can be seen in the sagging tests. The varied results obviously come to some extent from the adjusted consistency of the samples and cannot be directly compared due to the different amounts of thickeners in the formulations to obtain the desired consistency, however, there are clearly differences in the tendency to maintain non-sagging depending on the type present in the formulation coalescent.
Summary
The conducted range of case studies with six different coalescents with completely different physicochemical properties, of which the key was different miscibility with water, showed that the selection of an appropriate coalescent for applications in latex paints must be supported by appropriate, extensive laboratory tests. On the basis of the conducted research, it was not possible to clearly state which coalescent is better and which is worse. Depending on the tested parameter, different results were obtained, which can then be used as a selection key. For this purpose, it is necessary to define the parameters that have priority for a given application, e.g. blocking resistance to scrubbing. The conducted tests have shown that depending on the type of coalescing agent, it may not be sufficient to rely only on the MFFT curve to select the appropriate dose used in the formula. It is very important to extend the tests with an additional LTC test, which should always follow the MFFT curve verifying the results in conditions of low temperature and increased humidity.
For more information, e-mail artur.palasz@spektrochem.pl.
Looking for a reprint of this article?
From high-res PDFs to custom plaques, order your copy today!