Superoxalloy Abrasives
Achieving Surface Quality Profitably, Safely and Sustainably
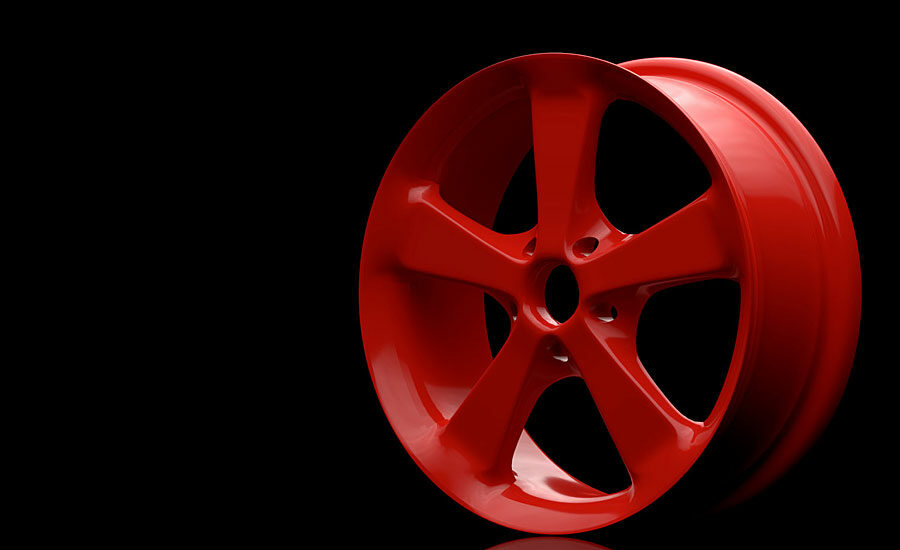
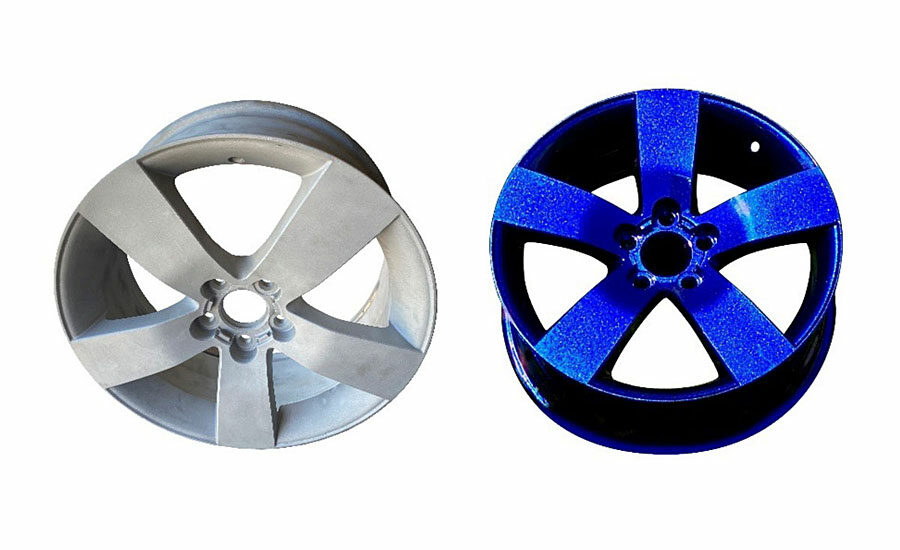


The expanding global powder coating market is forecast to reach $19.9 billion by 2027.1 Cost efficiency, health and safety, and increased focus on sustainable practices are driving changes in coating formulations and manufacturing methods that favor powder coating. In the North American automotive industry, concerns about emissions of volatile organic compounds (VOCs) are catalyzing the adoption of powder coating, and there is still room for growth.1,2
Powder coaters must consider several factors to achieve the improved economic and environmental sustainability objectives driving this upward trend. An important factor is the selection of an abrasive blasting media for surface preparation that achieves coating quality, performance and longevity without risking harm to people or the environment.
A new category of blast media, superoxalloys, is proven to help powder coaters achieve these objectives. Superoxalloy abrasives fundamentally differ from traditional blasting media in the way they are made and in how they function when delivered to a surface.
What Is a Superoxalloy?
Superoxalloy abrasives are an engineered alloy of oxide minerals created through highly controlled formulation and tempering (high heat + rapid cooling). The process creates extra-strong, non-crystalline (amorphous) particles that resist breakage under stress of high-speed mechanical impact. Superoxalloy abrasives are produced in a controlled manufacturing environment using a sustainable process and are not prone to the variations in composition and performance that often arise with mineral abrasives formed in an uncontrolled environment, i.e., slags, aluminum oxide, garnet, staurolite and others.
Abrasive particles formed in the Earth, or in virtually any other uncontrolled environment, will contain unavoidable pores and mineral solid domains that were forced together under pressure along weakly bound cleavage planes that decrease particles’ impact strength. They often contain crystalline regions on varying scales that can contain regulated forms of crystalline silicon dioxide (i.e., quartz) that cause lung fibrosis and cancer.
Superoxalloy abrasives are first formulated for health, safety and strength, and then melted, which erases pores, crystals and irregular cleavage planes in the raw material. The minerals are re-assembled in a rapid cooling and tempering process that results in a completely amorphous solid material matrix that is uniformly strong in all directions (Figure 1).

A spectrum of particle shapes in superoxalloy abrasives offers versatility. Particle shapes include rounded, sub-rounded, sub-angular and angular particles that each perform different tasks in preparing a surface. Jobs that involve multiple blasting steps can often be completed in one pass, leaving a clean, bright, ready-to-coat surface in less time and using significantly less abrasive.
The Impact Strength Factor
Impact strength, or resistance to breaking, is an enormously important but often overlooked attribute of abrasive particles. Most blasters want to know the density, hardness and sharpness of an abrasive. These have historically been used in evaluating what jobs an abrasive is capable of and what surface profile (roughness) it is likely to leave behind. Harder and sharper particles tend to be more aggressive and leave a deeper profile. Softer and rounder particles will generally be less aggressive, which may be an advantage if a smoother or more uniform surface is needed.
The strength of superoxalloy particles offers an entirely new set of benefits. For example, superoxalloy particles contain a fair fraction of rounded particles and a Moh’s hardness of around 7.5, yet regularly outperform harder and sharper abrasives like garnet, aluminum oxide and even silicon carbide. This is especially true in the most difficult applications like the removal of hardened powder coat, thick ceramics, or elastomeric coatings where auxiliary assistance from mechanical scraping, chemical treatment or thermal burn-off are often used to make abrasive blasting possible. Particle strength, not hardness, sharpness or density, enables superoxalloy particles to quickly remove these nearly impossible coatings without additional processing steps.
Abrasive blasting is essentially an energy transfer process. Blasters invest in air compressors, pressure pots, metering valves, hoses and nozzles to accelerate abrasive particles to very high speed (energy) with the objective of delivering that particle energy to do work on a surface. If a particle breaks when it impacts the surface, no matter how hard or sharp it is, much of its energy is consumed in the process of breaking. As a result, less energy is delivered to the surface where it is needed. Because fewer superoxalloy particles break on impact, they deliver virtually all of their energy to the surface. Not only does this increase blasting speed by 20-50%, but it also decreases abrasive consumption by as much as 85% because far fewer particles are needed per square foot of surface.
Superoxalloy’s impact strength allows blasters to make maximum use of available air pressure. The performance of mineral abrasives tends to level off or even decrease when the nozzle pressure is raised above a certain threshold, typically around 105-110 psi. The excessive impact forces at higher pressure cause particles to pulverize into dust, substantially decreasing their effectiveness.
With superoxalloys, the pressure at the nozzle can be raised to 120 psi or higher, and the performance of the abrasive continues to improve. The particles can withstand the impact forces, continue to bounce off the surface without breaking, and deliver the extra energy that they possess by virtue of the higher nozzle pressure.
Putting a Superoxalloy Abrasive to Work
Superoxalloy abrasives are available in multiple grades, or particle size ranges, to meet the needs of different surface preparation tasks. Coarser particles are best suited for thicker or more difficult coatings, where a deeper surface profile is preferred, or where speed and rigid production timetables are high priorities. Finer grades leave a lower profile and are more effective on thinner and more brittle coatings.
While smaller particles are more durable than the larger ones, all grades are reusable multiple times, particularly in applications like powder-coated aluminum where lower nozzle pressures are used. Powder coaters commonly reuse superoxalloy abrasives eight or more times before performance begins to degrade.
Because superoxalloy abrasives are manufactured in a controlled process, all of the grades deliver a consistently clean and bright finish. They are effective in both wet (vapor) and dry blasting processes.
Detailing Surfaces to Improve Coating Adhesion
Metal coatings are formulated to uniformly cover and bond with the substrate metal. Coating specification sheets set forth requirements for preparing the surface to be coated, which include the desired profile depth and surface cleanliness. It is here that the impact strength of superoxalloys emerges again.
Particles crushed on impact with a surface tend to smear into the surface profile, much like mud sticking to a wall. These embedded residues prevent coatings from bonding to the metal as they were formulated to do, which can result in poor adhesion, telegraphing or delamination of the coating (Figure 2). Superoxalloy particles bounce off the surface, leaving ultra-clean metal for maximum coating adhesion without the need for subsequent chemical cleaning. In a comparative study conducted by a global petrochemical company, superoxalloys were the only abrasives that left zero detectable embedded residues after blasting. Powder coaters routinely report superoxalloys require reduced surface preparation time and deliver improved coating appearance, adhesion and overall performance.

In one application, silicon carbide abrasive was being used to remove a carbonized coating from the tip and base of a tungsten carbide asphalt milling and removal bit. The process involved blasting the tips and bases for 30-60 minutes, flux cleaning to remove residues from the surfaces to be braze-bonded, and then braze bonding the tip to the base to form the part. The brazed bond would often fail a strength test at about 5,000 psi of pressure in a test press when 8,000 psi was the minimum requirement.
When the process was tested using superoxalloy in place of silicon carbide, the blasting time was reduced to 10 minutes, and flux cleaning before brazing was not necessary. In the test press, the tungsten carbide tip cracked at 18,000 psi with the brazed bond still intact. Superoxalloys reduced blasting time by 67%, eliminated a cleaning step, and increased the strength of the milling bits by 125% compared with one of the hardest, sharpest and most expensive abrasives available.
Addressing Particle Embedment and Rust Bloom
While a pristine and profiled surface is important, it is just as important that the surface remain clean between surface preparation and application of the first coating layer. The rapid onset of rust bloom on a prepared surface before coating, particularly in humid environments, presents cost and scheduling challenges. Rust bloom is a common cause of poor coating adhesion and premature coating failure. Many applications require corrosion inhibitors or dehumidifiers to afford enough transition time between blasting and application of the first coating layer without having to re-blast the surface.
Rust bloom forms quickly when water-soluble salts or iron residues are left on a steel surface after abrasive blasting. These residues accelerate the electrochemical reactions in which iron in the steel is oxidized to form iron oxide on the surface. Without these residues, the bare metal would corrode at a naturally slow rate, allowing ample time between surface preparation and coating before the corrosion layer develops.
Embedded abrasive material from crushed particles often contains the soluble salts or iron needed to initiate and accelerate corrosion. The impact strength of superoxalloy particles prevents embedment and leaves an ultra-clean surface free of corrosion-promoting residues. The surface stays clean and free of rust bloom for as long as weeks, even in the most humid environments or rainy weather.
A shipyard blaster recently blasted a section of a ship with superoxalloy abrasives, after which it remained unprotected for two weeks in a marine environment. The blasted surface held the required SSPC-SP6 finish throughout the two-week period (Figure 3). No corrosion inhibitors were used, and reblasting was not required before finishing the blast job and applying a new coating. Delaying and preventing rust bloom saves costs, but just as importantly eases scheduling complications and accelerates job completion, which increase revenues for a blast and paint operation over time.

Calculating Blasting Media Economics, Efficiency
The impact strength of superoxalloy abrasives offers clear benefits compared with traditional abrasives: 1) up to 50% faster blasting speed; 2) as much as 85% lower abrasive consumption; 3) a cleaner, more uniform surface finish; and 4) better coating quality and performance. The value of these advantages for the blast and paint operation, and the asset owner becomes clearer when examined through the lens of economics.
When abrasive blasting is faster, the time-based costs of surface preparation are lower, including labor, compressor fuel and equipment rental costs. The contractor can either make a larger margin on jobs at its current bid price or bid a tighter project schedule with lower overall cost. Faster blasting also increases revenue because more jobs can be completed, more square feet prepared and coated, over time. From the asset owner’s perspective, the asset is put into service sooner, increasing return on the asset.
Needing less abrasive to complete a job decreases the costs associated with the quantity of abrasive used, including the costs of the abrasive itself, cleanup and disposal.
Cleaner finished surfaces and better coating quality can prevent unnecessary delays and rework. The benefits of higher coating quality and performance are even stronger for the asset owner, particularly for large assets, because the time between maintenance outages is extended, keeping assets in service.
Supporting a Safe, Sustainable Operation
The past five years have brought major changes in the safety regulations for blasting operations. The Occupational Safety and Health Administration (OSHA) decreased the permissible exposure limits (PEL) for crystalline silica and beryllium by a factor of 10. Long-term exposure to inhalable dust containing beryllium and crystalline silica is known to cause lung diseases and cancer. Abrasive materials must also satisfy regulatory limits on leachable heavy metals for handling and disposal.
Superoxalloy abrasives are formulated for health and safety in addition to material strength and performance, and are manufactured in a way that precludes crystal formation in the material. Virtually all other mineral abrasives are either mined (garnet, aluminum oxide, staurolite) or formed in an unformulated and uncontrolled environment (slags). Whether these abrasives contain hazardous constituents like crystalline silica or beryllium is a matter of source or location, which varies even within a particular abrasive class.
Exposure to respirable toxins is essentially the mathematical product of total dust concentration in the air times the level of a toxic substance in the abrasive material, averaged over an eight-hour work shift. Superoxalloy abrasives reduce the risk of exposure to beryllium and crystalline silica by decreasing both mathematical factors.
Impact strength allows superoxalloy particles to bounce off of a surface rather than pulverize into dust. Users of superoxalloy regularly comment on enhanced visibility during blasting, especially in enclosed spaces (Figure 4).

Formulation, melting and rapid cooling in the production of superoxalloy abrasives take care of the second part of the mathematical product for exposure, which is the level of the toxic substance in the abrasive to begin with. Superoxalloy abrasives contain no beryllium and are processed into a completely amorphous material matrix free of crystals in any form. Crystalline silica and beryllium have never been detected in samples of superoxalloy abrasives analyzed by certified third-party laboratories.
Considering heavy metals and disposal, only barium, vanadium and zinc are barely detectable in leachate analyses at levels that are more than 50 times below EPA limits for total threshold limit concentration (TTLC) and soluble threshold limit concentration (STLC). Superoxalloys are also CARB certified, SSPC-AB 1 certified, and compliant with the Clean Water Act (40 CFR 122.21 and 40 CFR122.42).
Superoxalloy abrasives can contribute to environmentally sensitive projects. A developer seeking LEED certification for a building renovation switched from coal slag to superoxalloy to clean and restore surfaces. The switch helped the developer finish abrasive cleaning ahead of schedule and reduced abrasive usage and disposal more than 50%. The reductions in dust, abrasive use and waste generation earned seven points toward LEED certification.
Conclusion
Surface preparation directly influences the success or failure of wet and dry applied coatings. The easiest way to repair coating problems is to prevent them.3 As the reliance on powder coating in the automotive and other manufacturing industries expands to address concerns about performance, emissions and safety, there is sure to be increased focus on the efficiency and effectiveness of the overall process, including surface preparation.
Superoxalloy abrasives have proven especially effective in powder coating. Manufactured for safety and impact strength in a controlled process, superoxalloy abrasives are more productive and leave ultra-clean, uniformly profiled surfaces, free of embedded residues and rust bloom. They carry virtually zero risk of harm to people or the environment. All of this creates value for blasters, paint operators and asset owners.
References
1 Powder Coatings Market Size Worth $19.9 billion by 2027.
Grand View Research industry report. February 2020. (https://www.grandviewresearch.com/press-release/global-powder-coatings-market).
2 Lovano, S. Automotive Applications for Powder cCoating, Metal Finishing, Volume 94, Issue 9, (1996) Pages 20-24. https://doi.org/10.1016/0026-0576(96)82097-6.
3 Schoff, C. Automotive Coatings: Application Defects,
American Coatings Association. https://www.paint.org/coatingstech-magazine/articles/automotive-coatings-application-defects/.
Looking for a reprint of this article?
From high-res PDFs to custom plaques, order your copy today!