A Perfect Match: High Performance and Potential for Cost Optimization

Over the last few years, topics around health and environmental challenges, and sustainability have gained further attention, especially amongst the younger generation. This megatrend is seen across all industries globally, but is particularly visible for the automotive, chemical and manufacturing industries. Numerous new and revised regulations have been introduced to the chemical industry in different regions in the last two years, including a number of revised regulations and reclassifications of chemical substances such as volatile organic compounds (VOCs), formaldehyde, acetaldehyde, titanium dioxide (TiO2) and several isothiazolinone limitations.
With this trend in mind, Synthomer has developed a novel styrene acrylic binder with excellent water resistance, scrub resistance and hiding power, and that potentially enables the paint and coatings industry to optimize binder and pigment dosage, resulting in paint property, carbon footprint and cost improvements. Formulations based on this new binder can also meet the 2018 criteria for the RAL UZ 102 label (Blue Angel) in the category “Low Emission Interior Wall Paints.” In this article we detail our internal studies that enable the aforementioned savings by showing test results of paint formulations with a high pigment volume concentration (PVC) and within the gloss range of matte (<10 GU 85°) and dead matte (<5 GU 85°), which are popular in the central European market, particularly the DACH region. We will also elaborate on results from formulations for mid-sheen gloss >10 GU 85° wall paint, often encountered in other international markets. A market-standard styrene acrylic polymer was used as benchmark in this study.
Lower Binder Dosage: A Gain in Formulation Cost, No Compromise in Performance
Paint formulations developed in our laboratory with the new styrene acrylic polymer (Table1) have shown an excellent wet scrub resistance and opacity, fulfilling class 1 – EN 13300. We then further investigated the possibility to optimize the paint formulations towards lower binder content while still meeting the requirements of the class 1 – EN 13300.

A series of paint samples was compounded with the binder content reduced in increments of 1% from 17% to 7%. Pigment and fillers were adjusted accordingly to ensure all paint samples had the same solid content, and all paint samples went through the full application test cycle including both liquid and dry film properties. Test results showed that with the new polymer, paint formulations with 8% binder content (reduced from 17%) can still meet the EN13300 class 1 wet scrub resistance and opacity requirements (Figure 1). Consequently, PVC of the paint formulation increased from 67% to 81%. At 7% binder content, the Revacryl Ultragreen™ performed better than the benchmark, albeit both only met EN13300 class 2 wet scrub resistance (Table 2).


All paint samples were subjected to a stability test at room temperature (RT) and at 40 °C for four weeks, and no instability was observed throughout the test period.
Lower TiO2 Content for Lower Cost and Leaner Carbon Footprint
The high refractive index (n20D = 2.609) of TiO2 is a major contributing factor to the hiding power of a wall paint formulation. However, TiO2 represents a costly ingredient and may represent up to 25% to 30% of raw material costs in a class 1 – EN 13300 formulation. Furthermore, the high amount of energy for TiO2 production (5.3 t CO2 per ton TiO21) contributes substantially to the carbon footprint of the total paint formulation. Also, TiO2 has been reclassified by the European Commission to H351 carcinogen 2, suspected of causing cancer through inhalation in powder mixture, and the updated classification will be implemented on the 1st of October 2021.2 Therefore, the industry is constantly looking for opportunity to reduce TiO2 content in a formulation without significantly affecting its performance, especially in paint opacity.
Similar to the binder content optimization study, a series of paint samples was compounded with different TiO2 content starting from 20% and reduced in increments of 1%, while binder content remained constant at 8%. Solid content of paint samples was controlled by adjusting the fillers such as clay and calcium carbonate accordingly (Table 3), and the paint samples were subjected to selective application tests, namely opacity, wet scrub resistance and storage stability.

Results indicate that a 10-11% reduction of TiO2 (from 20% to 17.8%) is viable while keeping the paint contrast ratio above 99.5%. Wet scrub resistance of the paint was not affected, therefore the optimized formulation still meets the EN13300 class 1 requirements. Paint samples remain stable after 4 weeks at both room temperature and 40 °C (Table 4).

With the optimized paint formulation where both binder and TiO2 content are reduced, we estimate a potential saving of 14% in formulation cost and an improved carbon footprint by 12% (117 kg/t) based on theoretical calculation.
Robust Polymer Design to Fit a Broad Range of Formulations
To further validate the performance of the newly developed styrene acrylic polymer, additional laboratory studies were carried out in three mid-sheen paint formulations that are commonly seen in many international markets (Tables 5-7).



Using the same methodology as before, three in-house formulations were selected and a binder content optimization study was carried out (Figure 2). A reduction of 7-12% in binder content was achieved while maintaining similar paint properties.

The targeted gloss unit was achieved across all three paint formulations, despite lower binder content and higher PVC. All three samples showed excellent wet scrub resistance, meeting the EN13300 class 1 requirement, while opacity was between class 1 and class 2 depending on formulation, the type and amount of extenders used.
Blocking resistance of the paints was tested according to an internal method where each paint was applied at 150 µm wet thickness, dried for 24 hrs at room temperature and subsequently tested at room temperature for 30 min with a 1-kg weight using a blocking tester (R&H ECA 7038-6). Results in Table 8 show that all samples reach acceptable blocking resistance, with a force value ranging from 0.5-0.8 N/cm2.
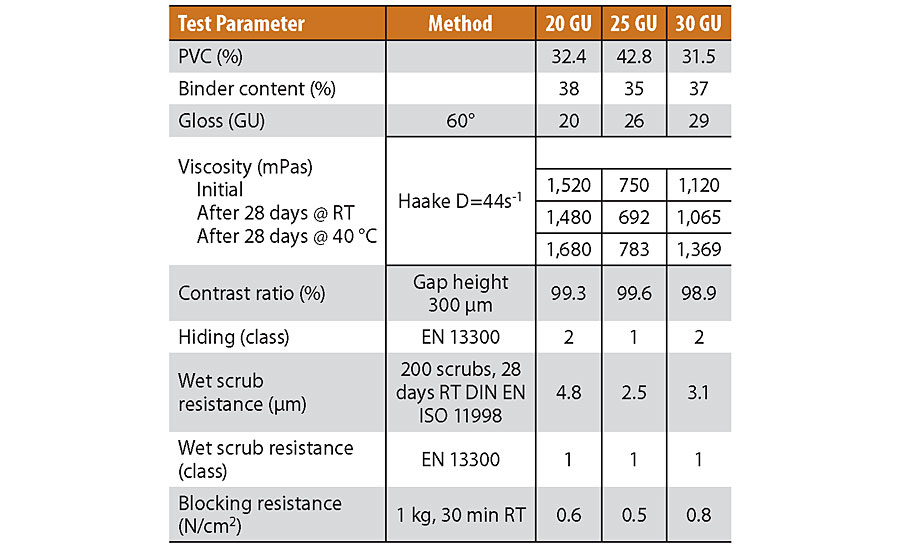
The paint stability tested after 4 weeks at room temperature and 4 weeks at 40 °C storage, measured with a Haake-Rheometer at shear-rate D = 44 s-1 showed a good storage stability with only slight viscosity increase.
Passing the VOC Requirements for RAL UZ 102 Labelling
With an optimized post-activation process, residual monomers of the new styrene acrylic polymer were reduced and the formaldehyde content (according to VdL-RL 03) is below detection limit. The total VOC content can be further reduced by steam-stripping on demand. However, based on the optimized formulation used in this study, the requirements for environmental labels e.g. RAL UZ 102 (VOC <700 ppm) can be achieved.
A Next-Generation Polymer Dispersion for a More Sustainable Future
The findings and results presented in this study confirm that the newly developed styrene acrylic polymer does show a significant improvement in wet scrub resistance over the current benchmark. This indicates that wall paints made using this polymer can have better durability and will last longer. Thanks to its excellent pigment binding capability, the polymer enables paint formulators to optimize their existing formulations to potentially reduce both the binder and TiO2 content while still meeting the stringent EN13300 class 1 standard, delivering a more sustainable solution to consumers.
The new polymer was tested in a broad range of formulations at different PVC and gloss. In all tested formulations, the polymer exhibited a consistent performance in the key parameters including wet scrub resistance, opacity and storage stability at both room temperature and 40 °C. The robustness of a polymer remains crucial in complexity reduction for procurement and raw material inventory management.
A few considerations were taken into account during the development of the product to limit the use of any known hazardous substance. The polymer is therefore free from alkylphenol ethoxylate (APEO) surfactant, formaldehyde and ammonia. Optimization in polymerization and post-activation helped to reduce the residual monomers, hence also lowering the total VOC of the product, allowing formulators to design a paint formulation that can meet even the demanding requirement of Blue Angel eco-label for low emission wall paints.
Results at a Glance
- The new novel styrene acrylic polymer is suited for a broad range of formulations that meet the EN 13300 – class 1 requirements.
- The polymer enables potential binder and TiO2 content optimization up to 8% to 11% respectively. This enables cost-saving potentials of 14%, as well as a leaner carbon footprint.
- The binder offers an excellent water resistance, wet scrub resistance and pigment stabilisation capability.
References
1 TDMA-Info (December 2013): The Carbon Footprint of Titanium Dioxide Pigment
2 https://echa.europa.eu/de/brief-profile/-/briefprofile/100.033.327
This article was originally published in the European Coatings Journal, 10/11, 2020.
Looking for a reprint of this article?
From high-res PDFs to custom plaques, order your copy today!